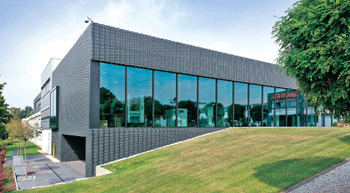
The turbo for the winding mill
The Autoconer is the firm favourite for the most efficient winding process giving the best technological value in denim production. Competition is tough in the growing market for denim. To stay ahead of rival companies successfully in this fiercely contested market, optimally configured machines offering maximum productivity are a must.
The Autoconer is the firm favourite for the most efficient winding process giving the best technological value in denim production.
Competition is tough in the growing market for denim. To stay ahead of rival companies successfully in this fiercely contested market, optimally configured machines offering maximum productivity are a must. The Autoconer is the firm favourite for the most efficient winding process giving the best technological value in denim production. In an extremely large-scale comparative study, the Schlafhorst Technology Center worked out the maximum productivity potential of PreciFX and Speedster FX, thus successfully demonstrating their superiority. More than a tonne of denim yarn was processed under real conditions. The results exceeded all expectations: the winding speed was increased by 25 per cent compared with rival machines with drum winding systems that were included in the study, while the package weight was augmented by 17 per cent.
Fierce competition in the growing denim market
Two years ago, the production of denim wovens broke through the magic barrier of 7 billion yards per annum. Global annual sales of denim jeans are estimated at over $66 billion. Whether as standard or premium applications, as ´classic´ cotton grades or increasingly as a blend of cotton with an elastane core giving more comfortable wear attributes, denim garments are still in growing demand. For years Schlafhorst has been the preferred supplier for many large and small manufacturers of denim yarns worldwide. For Schlafhorst customers, increasing their competitiveness through greater productivity, optimised process sequences and reduced machine downtimes in downstream processing are key factors in prevailing in this demanding mass market.
1 tonne of yarn wound
The Schlafhorst textile technologists had more than a tonne of denim yarn on bobbins at their disposal in this practical study. The yarn in question was a single weaving yarn of 100 per cent cotton for warp and weft with a count of Ne 7. The task on the one hand was to fully utilise the productivity potential of the Autoconer X5 in combination with PreciFX and Speedster FX without diminishing the yarn quality. On the other hand, focusing on maximum efficiency in the downstream process, a package design was developed that guarantees improved unwinding behaviour in downstream processing on the warping creel and in the weaving mill. The practical values obtained on a rival machine with conventional drum winding, the capacity of which had already been fully utilised in a customer´s mill through maximum optimisation, were used for comparison purposes.
Winding speed increased by 300 m/min
Thanks to an optimal configuration of reduced yarn tension and a variably adjusted number of turns, the Schlafhorst experts attained a winding speed of 1,500 m/min. This is 300 m/min or 25 per cent more than on the competitor´s drum winding machine, which was already operating at the technological limit of 1,200 m/min for this yarn. In addition to the increased winding speed, the Schlafhorst technologists also recorded fewer yarn breaks, because Speedster FX reduces the yarn tension especially in the critical final third of the bobbin, thereby considerably reducing the number of tension breaks. In consequence, fewer machine stoppages and higher winding speeds lead to a huge boost in productivity in the winding mill.
Better yarn quality compared with the rival machine
In spite of the much higher winding speed, the quality of the yarns wound on the Autoconer X5 was better compared with the yarns from the rival machine. Decisive contributory factors to this are the 30 per cent lower yarn tension and the gentle yarn detachment f