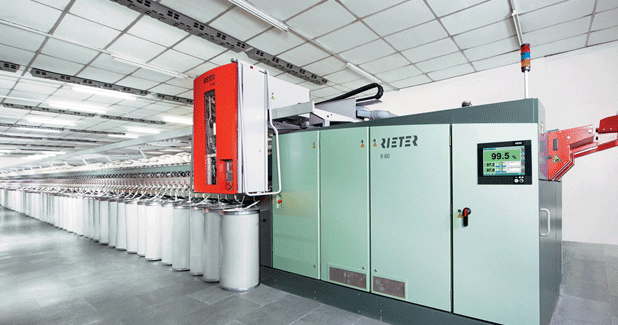
The economic benefits of Rieter rotor system
This technical article from the series ¨Higher profitability with Rieter complete systems¨ deals with automatic rotor spinning. The US market, resurgent in recent years, was selected as the location for the economic analysis, which also examines the issue of flexibility in detail.
This technical article from the series ¨Higher profitability with Rieter complete systems¨ deals with automatic rotor spinning. The US market, resurgent in recent years, was selected as the location for the economic analysis, which also examines the issue of flexibility in detail. The Rieter complete system shows economic benefits compared to a mixed system of different machine suppliers.
The strength of Rieter rotor spinning can be found in its high productivity and, at the same time, its great flexibility with regard to raw material and yarn structure. In particular, shorter fibres and waste, such as noils, can be easily processed with this technology. The preparatory process from bale to sliver can also be designed to be flexible and adapted to the end product. As a system supplier, Rieter can satisfy any requirement (Figure 1).
Raw material savings in Rieter´s flexible preparatory process
The rotor spinning mill used in this comparison produces a wide range of yarn from various grades of cotton. A low quality cotton mixed with noil is used for coarse yarns (Ne 12, 14, 16 and 18). For finer weaving yarn Ne 30, a slightly longer cotton is used and the addition of waste is omitted in order to achieve the required high strength. Accordingly, the blowroom |has two mixers and fine cleaners in order to process the two ranges separately. The VARIOset blowroom adjusts perfectly to both mixtures. It provides efficient cleaning with the lowest possible waste of good fibres.
The carding section consists of seven high-performance C70 cards, which are equipped with the Q-package in the pre- and post-carding zones. VARIOset in the blowroom and Q-package in the carding section ensure optimal utilisation of raw materials in the preparatory process. In our case study, this is reflected in a reduction in waste of 0.5 per cent compared to the preparatory machines of the mixed system.
Shorter processes and optimal sliver preparation
Two different carding models are used for the sliver formation process. The direct process was chosen for the coarser count yarns, so that three high-performance C70 cards are equipped with the RSB draw frame module. This module is a completely regulated draw frame with tongue scanning disc and groove scanning disc to ascertain sliver regularity in the infeed and fully-fledged 4-over-3 drafting system.
The regulated sliver has excellent evenness and long-term consistency. All quality parameters are constantly monitored by the RQM sensor and displayed on the machine panel. Even at the critical moment of the can change, the RSB module ? like no other draw frame module ? maintains the sliver count reliably constant. A prerequisite for a successful direct process in rotor spinning. For finer yarn counts, the classical process with only one draw frame passage was selected. The four C70 cards used for this purpose are equipped with the CBA changer for 1000 mm cans. The final preparatory step is performed on the RSB-D 45 autoleveller draw frames, which produce slivers of the highest quality. The newly designed suction device on the RSB-D 45 provides additional dust removal of the material and also saves up to 5000 kWh of electricity per year.
Flexibility and high production on the R 60
A total of six R 60 rotor spinning machines each with 600 spinning units are used in the system (Figure 2). Two of the machines have independent sides so that four different yarn counts can be produced in parallel. This flexibility allows the customer to respond quickly to market needs. In this case study, these two R 60 machines are spinning the yarn counts Ne 12, 14, 16 and 18 and process a blend of cotton and noil.
Separating the batches on the two package conveyor belts of the R 60 ensures that the yarns are not mixed-up by the operato