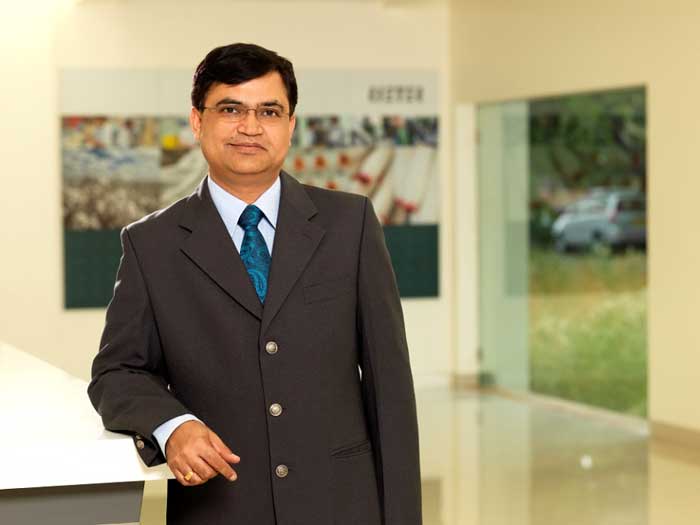
The government’s focus into the MMF sector will create many opportunities
Rieter is the world’s leading supplier of systems for manufacturing yarn from staple fibres in spinning mills. Based in Winterthur (Switzerland), the company develops and manufactures machinery, systems and components used to convert natural and man-made fibres and their blends into yarns in the most cost-efficient manner. Cutting-edge spinning technology from Rieter contributes to sustainability in the textile value chain by minimizing the use of resources. In an interview with Divya Shetty, Prasanta Kumar Deka, Country Managing Director, Rieter India, emphasises how the industry can address the challenges it is facing currently.
How was Rieter’s performance in the financial year 2023?
The Rieter Group recorded solid sales in the financial year 2023 despite a challenging market environment. According to first unaudited figures, sales were CHF 1 418.6 million and order intake was CHF 541.8 million with an order backlog of around CHF 650 million as of December 31, 2023. While Rieter recorded higher demand in the second half of 2023, project commitments have not yet been able to materialise. Rieter is operating in a challenging market environment due to the economic and geopolitical conditions as well as the continuing weak demand. The Rieter Group will provide more details when the full-year results will be published on March 13, 2024.
Amid the global uncertainty, how can India boost its exports?
In the post-Covid era, global brands are seeking sustainable sourcing destinations that enable them to meet the requirements of their diverse product offerings while also providing acceptable quality standards. India’s capabilities across the entire textile value chain position the country ideally to meet these demands and become a global textile powerhouse.
The textile industry needs to adopt agile work processes so it can react quickly to -art technologies for processing mechanically recycled fibres into high-quality yarns. Many Rieter customers, especially in India, count on our recycling systems so they can benefit from the industry’s sustainability trend. fast-changing situations. Manufacturers should upgrade their equipment with the latest automation and digitisation technology. This will enable them to connect the dots across the complete manufacturing process and make faster, smarter decisions that strengthen their competitiveness. It is vital that we help brands minimise the environmental impacts of their products and support them in delivering on their sustainability claims.
What are the challenges before the Indian Textile & Apparel manufacturers as they aim to expand their exports globally?
The government’s “Make in India” initiative places greater responsibility on textile companies to excel in scalability, innovation, and quality. This means manufacturers need to put the focus where they can have a real impact. The Indian textile industry has traditionally had a penchant for cotton textiles. However, the cotton industry’s recent price volatility has squeezed margins despite improved sales. This means that manufacturers need to look at options like incorporating man-made fibres into their processes so they can diversify their portfolio. Moreover, additional steps are underway to strengthen the downstream segment and increase the share of value-added textiles in India’s export basket.
We applaud the Indian government’s initiatives like the PM Mega Integrated Textile Region (PM-MITRA) and production-linked incentive (PLI) schemes that will serve as powerful growth platforms for the industry. They will pave the way for the industry to adopt the latest technology and improve costs thanks to synergies in logistics. These initiatives will also reduce the trade barriers that many face due to differing tariffs in major consumer markets while at the same time leveling the playing field for domestic producers.
How is the textile machinery industry performing?
The textile machinery industry’s performance is under pressure due to weak demand, inflation, and a challenging geopolitical environment.
The subdued demand in key export markets have forced major textile producers to limit their capacity utilisation, which puts more pressure on operational costs. The restrained investments amongst these companies and their cautious approach to new projects are key challenges the industry faces.
However, the industry’s attractive growth potential paired with promising government initiatives are sure to pave the way for recovery in the coming months. Rieter India is ready to support the country’s growth with innovative solutions in spinning technology.
How do you foresee the expansion of spinning sector in India?
The spinning sector in India has many opportunities thanks to its cost competitiveness in manufacturing and the wide availability of cotton. The recent government push into the man-made fibre (MMF) sector will also create many opportunities for MMF staple yarns, including blends. The increasing awareness around sustainability and the demand for recycled products by end users will also usher in a new area of opportunities for all segments across the textile value chain, including spinning.
To what extent is the topic of sustainability in the textile industry reflected in your corporate strategy?Rieter has been committed to sustainability in relation to Environment, Social and Governance (ESG) for many years. ESG is an integral part of Rieter’s corporate strategy. Our technologies minimise resource consumption in the spinning process while setting standards for economic efficiency and sustainability in the textile value chain. We develop state-of-the Rieter also supports customers in the development of new yarns from fibres produced or recycled in a chemically sustainable manner.
We are moreover working to reduce the environmental footprint of Rieter across all our plants and are cooperating with suppliers along our value chain. I am particularly proud of the solar plant at our Wing manufacturing site, which was installed in 2019, and has an annual capacity of 2 500 MWh.