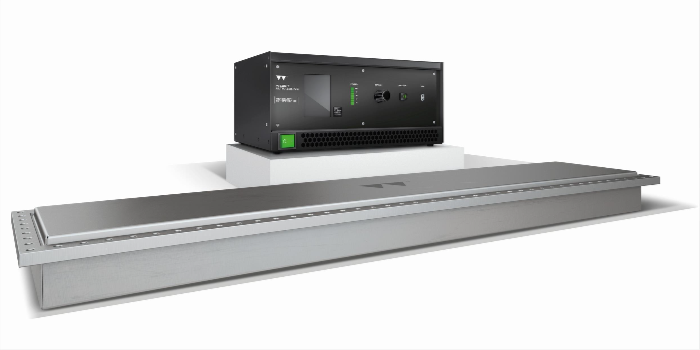
Ultrasound technology for antimicrobial finish
In light of the coronavirus pandemic and the increasing number of hospital infections around the world involving multidrug-resistant pathogens, antimicrobial textiles are coming back into focus.
An innovative,
ultrasound-based finishing technology developed by Sonovia, Brückner Textile
Technologies, and Weber Ultrasonics now offers some crucial advantages: because
the impregnation meets industrial requirements for wash resistance, it remains
effective for a long period of time –
even against coronaviruses. Furthermore, the new “sono-finishing”
process minimizes the environmental impact associated with conventional textile
finishing.
Antimicrobial
textiles are nothing new. But because the majority of impregnations that
protect against bacteria, viruses, and fungi use chemical binding agents that
only deliver limited wash resistance, the protective effect only lasts a
certain amount of time. Additionally, the chemicals and substances used can be
harmful to the environment. This may not only impact the environment; it can
also result in pollutant residues on finished products. “To ensure
antimicrobial textiles like those used in clothing for medical workers,
hospital linen/laundry, and oronasal masks significantly reduce the risk of
infection, the impregnation must be able to withstand frequent laundering at
the high temperatures required in the medical sector. They cannot lose efficacy
over the course of their normal useful life,” says Liat Goldhammer, chief technical officer at Sonovia Ltd, setting
out a key requirement. Furthermore,
textile finishing must meet today’s high economic and ecological standards.
Sonochemical
process offers solution for all types of textiles in 2017; the Israeli startup
began industrialising a patented sono-finishing process developed at Bar-Ilan
University in Israel. The one-step, sonochemical finishing process is suitable
for all types of textiles – whether they’re made from natural fibres like
cotton, linen, and silk, synthetic materials, or a blend of both. The procedure
uses zinc-oxide nanoparticles as an active medium and is based on the physical
phenomenon of acoustic cavitation: when exposed to ultrasound, small bubbles
continuously form in the solution mixed with the nanoparticles, which then
expand and collapse within split seconds. This creates high-energy
microstreaming patterns, which move at around 500 meters per second. These
carry the particles with them and embed them firmly in the textiles. “This
is a distinctive feature of our technology versus conventional textile
finishing processes that use chemical binding agents,” explains Liat
Goldhammer. “With sono-finishing technology, the particles are
mechanically embedded, so the antimicrobial properties remain in place for a
long time.” What’s more, no polluting binding agents are required in the
process, and the use of chemicals can be reduced by up to 50 percent.
The
formation of cavitation bubbles via ultrasound is crucial to ensure the reliable
application of the antimicrobial zinc-oxide particles. Standard ultrasonic
systems cannot be used for this.
Strong partners for industrialisation
To
transfer the technology from the university laboratory to large-scale industrial
production, Sonovia partnered with Brückner Textile Technologies, a manufacturer of textile finishing systems
and process technology developer, as
well as Weber Ultrasonics, an international manufacturer of ultrasound technology components – both world
leaders in their respective industries.
“Both companies were impressed by the technology’s potential and entered
into partnerships with us. This cannot be taken for granted with such
established firms – after all, collaboration with a startup always comes with
certain risks,” comments Liat Goldhammer.
While
the R&D department at Weber Ultrasonics came up with a made-to measure
ultrasonic concept, Brückner developed and built a corresponding application
unit that can also be integrated into a wider, continuous finishing process. The first system prototype for the
sonochemical process has been in use at Brückner’s technology center since
early 2019.
Technological, environmental, and cost
advantages
In
addition to ensuring maximum process reliability, key aspects included meeting
the modern textile industry’s high standards in terms of productivity, reliability, sustainability, ease of
maintenance, and cost effectiveness.
Compared
to conventional textile equipment, the new procedure not only offers the
benefits of more long-lasting antimicrobial properties and being more
environmentally friendly; it also allows for cost savings. “Although development
is not yet complete, initial, conservative calculations suggest potential
savings of around 10 percent from the reduction of chemicals used,” comments Liat Goldhammer.
The
new application unit, which is similar to a padding mangle, can easily be integrated
into existing plants and lines. It can be used for finishing both woven and
knitted fabrics, as well as nonwovens and carpeting.
Proven
wash resistance and efficacy – even against coronaviruses To prove the lasting
and reliable antimicrobial efficacy of sonochemical textile finishing, Sonovia
conducted testing together with renowned international textile research and
certification institutes. The tests confirmed that the finished fabrics still
retained their full antimicrobial properties after multiple wash cycles at high temperatures.
Sonovia
now manufactures and sells antimicrobial oronasal masks made out of textiles
that use this technology. Tests carried out in summer 2020 revealed more than
99 percent efficacy against SARS-CoV-2. Additionally, the mask filters 95
percent of 3 microns particles, the particle size which has been identified by the WHO as relevant to the
spread of COVID-19.
The
new technology’s proven, lasting protective effects, in addition to the user-friendly and sustainable process, make
it an optimal solution for finishing
clothing for medical and care workers and laundry/linen in hospitals, senior homes, and hotels, as well as many
other areas where hygiene and infection
control are critical. The fashion and sportswear industries, as well as the
automotive sector and railroad car fitters are also interested in
sonochemically finished textiles. Relevant tests are set to be carried out at Brückner
Textile Technologies’ technology center starting in the second quarter of
2021.