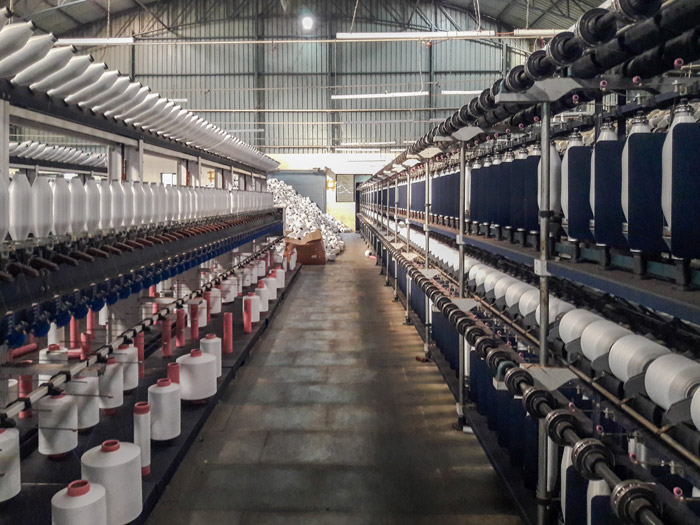
Yarn realisation in spinning: Some case studies in Ethiopian mills
A high yarn realisation is a factor of great importance in the production economics of a spinning mill, says Wondwossen Mamuye
The growing global competition forces the cotton spinning mills to produce yarns in constant quality at internationally competitive prices. The cotton textile industry contributes a significant position in the economy of globe as well as in Ethiopia. When comparing the cost structures in different locations it can be clearly seen under consideration of all the regional dissimilarities that the raw material price now as before represents the dominating factor in yarn manufacturing costs. This means that the key to survival in the international market is to best possibly utilise the raw material, despite all influences of labour costs and capital costs.
Introduction
Yarn realisation denotes the percentage of yarn produced from a given weight of bale material. The rest is the waste which has much less worth compared to fresh fibres or yarn. For a successful waste control in spinning mill establishment of norms for waste is a pre-requisite. Yarn realisation is largely governed by the level of trash in cotton, expected yarn quality and types of machinery. A high yarn realisation is a factor of great importance in the production economics of a spinning mill. One percent reduction in yarn realisation would cause almost the same economic impact on the mill’s profit as 1 per cent increase in the raw material (lint) cost would make. This is because resale value of waste is much less than the actual price of cotton till it reaches yarn stage. Yarn Realisation is the percentage of yarn output produced from the given cotton input and largely depends on the waste taken out in the blow room (trash content of the mixing), the waste in cards, the type of cards, the trash in the lap and the waste in combers (nature of fibre length distribution).
The control of raw material cost which constitutes 40 per cent to 70 per cent depending on its count mainly influenced by yarn realisation. The yarn realisation normally ranges from 85 per cent to 90 per cent for carded cotton yarn and from 67 per cent to 75 per cent for combed cotton yarn, depending on the trash percentage in cotton and quantity of waste extracted during fibre to yarn conversion In buying cotton or raw material, the price includes the non-lint material and has to be considered in valuing the material. Operating machines produce waste products i.e. useable and non-useable waste. Factors that influence raw material cost per kilogram of yarn produced are yarn realisation, invisible loss, raw material (lint) cost and waste selling price have to be controlled for a spinning mill to have a maximum possible profit. Spinning factories in Ethiopia have limitations on their production capacity utilisation and productivity (as shown Table 1), waste control/management and yarn realisation to produce yarns in constant quality being competitive in the international market.
Statement of the problem
Improved utilisation of raw material is the most important factor to assess the technical performance and profitability of spinning mills. A one percent improvement in yarn realisation has a significant economic impact on mill’s profit. It denotes the percentage of yarn produced from a given weight of bale material. Establishment of norms for wastes is a pre-requisite for a successful waste control in a mill. Yarn realisation is largely governed by the level of trash in cotton, bale management, amount of flat and licker in waste to be removed, length and maturity of the fibre, expected yarn quality and type of machinery and other parameters.
Then, by considering the above yarn realisation governing factor it is important to assess, address and solve the problem related to yarn realisation and waste control of the Kombolcha Textile Share Company, Adama Development PLC, MNS manufacturing PLC and Edget yarn and sewing thread Share Company spinning mills to attain proper utilisation of raw material. Almost all mills which are located in Ethiopia are not able to accurately calculate yarn realisation despite all the effects. Spinning factories in national level have limitations on their waste control/management and yarn realisation which affect the production cost of yarn produced inhibiting them from being competitive in the international market.
In relation to the above problems, Textile and Apparel Industries Research and Development Centre work in close collaboration with governmental organisation and non-governmental organisation GIZ (Deutsche Gesellschaft für Internationale Zusammenarbeit) to know the real practical work experience of the above spinning mill on yarn realisation and waste control (management). This study shows the importance of yarn realisation and waste control on local spinning mill on economic impact and profit.
⦁ Materials and methodology
3.1 Materials
In all factories cotton and regenerated polyester (Kombolcha Textile Share Company only) fibres were used to produce yarn. The cotton is produced in Ethiopia from different parts of the country.
3.2 Methodology
Yarn realisation can be of two types: expected yarn realisation and estimated yarn realisation. For the calculation of yarn realisation only non-usable wastes (blow room waste, card waste, comber noil, yarn waste, sweep waste, gutter / filter waste, invisible loss) are taken into consideration and if a mill does not reuse the usable wastes in the same mixing, the corresponding usable wastes must be deducted. Expected yarn realisation is calculated on the basis of the waste norms set to each section of the mill. The estimation of yarn realisation has to be done accurately by maintaining proper recording of bale weights or cotton consumption, wastes and yarn produced by making inventory on monthly basis. Data required for yarn realisation estimation (one month) mixing-wise data on cotton consumption, yarn production and process wastes (blow room waste, card waste, gutter/filter waste, comber noils, hard waste and sweep waste).
The actual waste collected should be compared with the norms and causes for deviation should be thoroughly investigated daily. Formula for estimating the expected yarn realisation given by SITRA is as follows.
Yarn Realisation YR ( per cent) = (100 – (Wbr + Wk + Wh + Ws +Wg) –I) for carded counts
= (100 – (Wbr + Wk + Wc + Wh + Ws +Wg) –I) for combed counts
Where; Wbr = Blow room waste per cent, Wk = Card waste per cent, Wc = Comber noil per cent, Wh = Yarn waste per cent, Ws = Sweep waste per cent, Wg = Gutter/Filter waste per cent, I = Invisible loss per cent
The approach and methodology followed during this raw materials utilisation study are training and common awareness on importance and methods of yarn realisation and waste control management system were delivered for every concerned employee and managerial level, gathering the real practical existing yarn realisation data, calculation method and waste control system through primary and secondary data, performance improvement team and inventory committee formed, opening and closing stock inventory carried out, each working day shift based data for one month (raw material, production and waste in type) as per the format provided was collected, process parameter diagnosis and appropriate measures were taken accordingly, waste investigation done against to SITRA standard and action taken where on abnormality noted, tests were conducted on blow room wastes and card wastes (using Uster High Volume Instrument HVI 1000 and trash analyser) and calculate yarn realisation after various optimisation performed using in one month recorded data. The formula that use to estimation of yarn realisation are:
Net cotton consumption (A) = Quantity of cotton issued + (Opening stock of in-process material – Closing stock of in-process material) + (Quantity of usable waste used – Quantity of usable waste produced)
Net yarn production (B) = Packed yarn production + (Closing stock of yarn – Opening stock of yarn) + (Sample yarn packed – Reopened quantity of packed yarn)
Total Process waste (C) = Sum of all Quantity of process waste generated
Yarn realisation ( per cent) = B/A *100
Invisible loss ( per cent) = (A – (B+C))/A *100
Invisible loss is a part in the estimation of yarn realisation. Invisible loss in a spinning mill arises mainly due to higher liberation of short fibres and fluff, error in weighment of cotton bale, yarn and waste, wrong method of estimating process stock, higher differences in moisture regain between incoming cotton and outgoing yarn and etc.
The action taken to overcome the problem of waste management and improve yarn realisation are common awareness delivered on importance of waste segregation on type, training were given on non-usable and usable waste type, comparing with norms and action was taken on abnormally recorded waste, arrangement and amount of usable waste on lay down performed, adjustment on relative humidity and temperature, setting in blow room and carding machines done to reduce waste, increase quality and quantity of yarn product on those mentioned blow on the Table 1.1 locally located spinning mill.
4.0 Results and discussion
The deflector blade and grid bars are adjustable to vary the angle and open space allowing more, or less trash to be removed. With an increase in the grid bar opening, there is an increase in the amount of good fibre that goes into the waste with the trash. Good fibre in the waste is normally kept to a minimal amount. Wider grid bar spacing and higher deflector blade angle setting gives more waste and higher lint loss per cent. Hence the setting has to be optimised. In the case of Kombolcha Textile Share Company study waste investigation done against to SITRA standard and action taken where on abnormality noted through conducting tests on blow room wastes and card wastes.
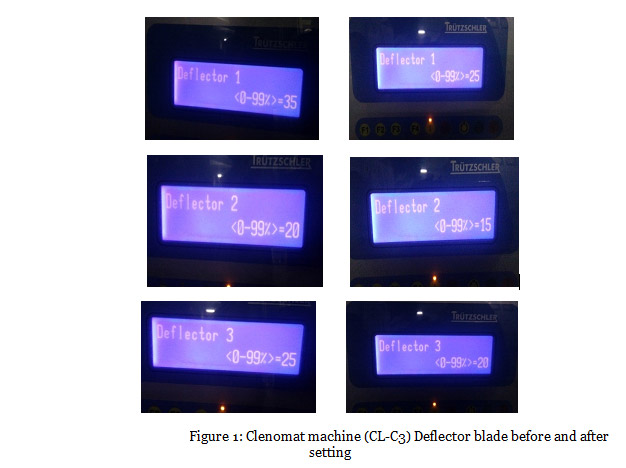
The lay down mixing mass average trash was found to be around 5.22 per cent and the expected blow room waste is thus 5.22 per cent (the same as trash per cent in the mix) and it would reach up to 6.53 per cent but the actual existing waste in the blow room is 7.45 per cent out of the standard. To reduce the waste within the standard clenomat machine of (CL-C3) the three-deflector blade angle setting changed from 35, 20, 25 to 25, 15, 20 (Figure 1) in rig spinning line and 14, 12, 10 to 10, 8, 6 in open end line. The grid bars setting also changed in both ring spinning line and open-end line from 3.6, 3.5 to 3.6, 2.4 and 3.1, 3 to 2, 2 (Figure 1.1) respectively.
The amount of waste using trash analyser after setting changes was found to be 5.93 per cent and not bad as compared to same as trash in the mix (5.22 per cent). Lint loss shall not be above 40 per cent if the trash is high and it shall not be more than 50 per cent for good raw material internationally. But the lint loss found 70.85 per cent before setting of deflector blade and grid bar and after the setting the amount of lint lose 56.40 per cent which is still high.
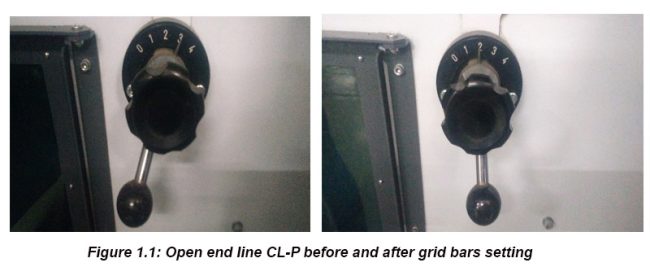
The other setting done in this study is changing the flat speed (TC-3) on the carding machine from 360mm/min to 340mm/min and the amount of waste reduced from 4.04 to 3.60 per cent in open end spinning line. Flat setting and flat waste play a vital role in quality of carding sliver. The speed of the flat has directly related to the amount of waste removed in the form of flat strips, i.e. the higher the flat speed heavier is the flat strips. To Calculating yarn realisation net cotton consumption, net yarn production and total process waste are required. So, during the study in Kombolcha Textile Share Company the net cotton consumption (A) is 137642.55 kg, net yarn production (B) 119493.23 kg and total process waste produced (C) is 20283.30 kg.
Yarn realisation =
= 86.81 per cent
Invisible lose = *100
= -1.55 per cent (indicates gain of 1.55 per cent materials)
The raw material price represents the dominating factor in yarn manufacturing costs. This means that the key to survival in the international market is to best possibly utilise the raw material, despite all influences of labour costs and capital costs. One per cent reduction in yarn realisation would cause almost the same economic impact on the mill’s profit as one percent increase in the raw material cost would make. On the other hand one percent improvement in yarn realisation would cause one percent reduction in the raw material cost. As shown in the below Table 1.1 each of the four spinning mill improved their own different yarn realisation and productivity at the time of study through taken various actions and those mill improve raw materials utilisation of 58884.39 Kg per year which is totally will be changed to yarn. In buying cotton or raw material, the price includes the non-lint material and has to be considered in valuing the material.
The main parameters that affect raw material cost per kg of yarn are raw material (lint cotton) cost, waste selling price, yarn realisation and invisible loss. The first two (lint cotton cost and waste selling price) are not directly controlled by the spinning mill while the other two (yarn realisation and invisible loss) are can be controlled. So, as yarn realisation increases, the amount of waste extracted goes down leading to a minimum gain of money out of those small amounts of waste. But ultimately, by increasing the yarn realisation, the eventual gain will increase as selling price of yarn is much more than selling price of waste extracted. In the case of this study, the raw material cost per kilogram of yarn and waste cost per kilogram of mixing (P) affected by yarn realisation as shown on the Table 1.2.
Raw material cost per kilogram of yarn and price realised from waste can be calculated by:
per kilogram of yarn and selling price realised from waste per kg of cotton decrease. As the yarn realisation increases price realised from the waste has decreased because when yarn realisation improved, the amount of waste extracted goes down leading to a minimum gain of money out of this small amount of waste and low selling price. But ultimately, by increasing the yarn realisation, the high amount gain will increase due to the effect of raw material cost to produce one kilogram of yarn is reduced more compared to waste selling price. Waste material gain reduced and raw material gain improved through increasing materials utilisation or yarn realisation improvement. Raw material cost per kg of yarn in birr as indicated in the Table 1.2 indicate significant reduction from 181.66 to 178.36, 185.03 to 182.74, 188.37 to 186.00 and 185.69 to 183.28 with difference 3.30, 2.29, 2.37 and 2.41 birr after yarn realisation in Kombolcha Textile Share Company, Adama development plc, MNS Manufacturing plc and Edget yarn and sewing thread Share Company respectively.
Due to improved utilisation of raw materials the factories gain from materials or cotton which changed to yarn 8,749,038.63 birr per year rather than gain of 280,548.61 birr per year from waste selling price.
5.0 Conclusions
In manufacturing industry costs are incurred by the producer and the price is asked upon selling the product. Under globally competitive conditions, price is determined by availability of the product already in the market and the quality of the product being offered for sale. The difference between price and cost is profit (or loss). The cost of a yarn are the summation cost of more than half is from the cost of fibre, part represents sales costs, and the rest comes from costs associated with the conversion of fibre to yarn. Generally, in buying cotton the price includes the non-lint material or waste, so in order to survive the huge competition it is absolutely essential that waste incurred during the yarn manufacturing processes should be kept control. The more quantity of yarn produced or even a one percent improvement utilisation from a given weight of raw materials is a matter of paramount importance in the production economics of a spinning mill.
References
⦁ D.K.T.E. Society’s Textile and Engineering Institute, Ichalkaranji. Yarn realisation & control of waste in spinning. Jun 24, 2016.
⦁ Woodhead Publishing India Pvt. Ltd. Control of wastes in spinning. 2016
⦁ G. Thilagavathi and T. Karthik, Woodhead Publishing India Pvt. Ltd. Process control and yarn quality in spinning. 2016
⦁ R. Senthil Kumar, Taylor & Francis Group, LLC, Process Management in Spinning, 2015.
⦁ Peter R. Lord. Woodhead Publishing Limited in association with The Textile Institute, Technology, science and economics, Hand book of yarn production, 2003.
⦁ Shri T.V. Ratnam et.el. SITRA norms for spinning mills. 2010
About the author:
Wondwossen Mamuye, Department, Spinning Industry Research and Development Desk, Textile and Garment Industry Research and Development Centre (TGIRDC), Ethiopia.