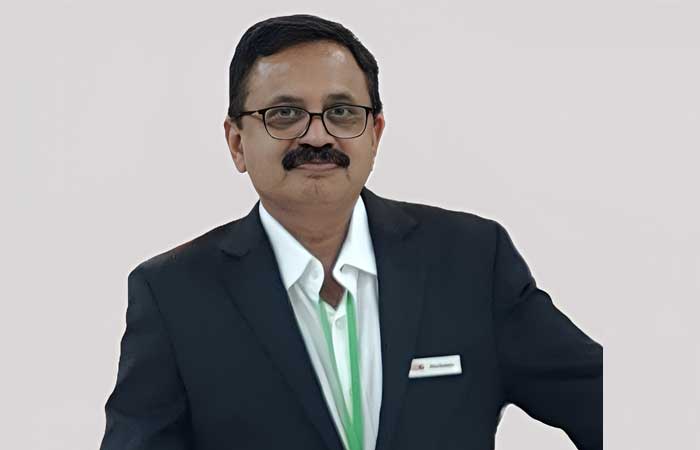
Vikas V Banduke: The benefit of automation is not always immediate, though in the long term, it always pays off
Established in 1939, A.T.E. has evolved into a multifaceted engineering group offering world-class products and solutions spanning several segments. A.T.E.’s businesses encompass manufacturing, industrial sales, distribution, and service and have gained expertise in handling turnkey projects.A.T.E. is respected for its values-based operations and builds deep relationships with all its stakeholders. The group is also deeply committed to societal wellbeing and has been working on achieving social goals through its businesses. Vikas V Banduke, Vice President – Automation, A.T.E. Enterprises, in this interview with Divya Shetty, shares how integrating automation in the manufacturing process can mitigate the challenges in the longer run.
Given the current uncertainty of the Indian textile industry and global industry in general, how can automation help mitigate this challenge?
Automation is primarily implemented to achieve several key objectives. Firstly, it reduces manpower as machines handle all controls, including production and machine parameters. Secondly, it minimises human errors since automation takes over machine control, eliminating the chances of mistakes. Thirdly, automation enhances production efficiency through fast and accurate control, and it also reduces breakdown time by enabling self-diagnosis. Additionally, automation optimises energy use and improves quality by providing online and accurate control of process parameters. It also facilitates the interconnection of machines and a centralised monitoring system, offering an accurate picture of manufacturing without human manipulation. Furthermore, automation is a key component of Industry 4.0 and enables visual interactions between machines and operators through graphical representations on systems like SCADA.
How does automation helps in increasing the productivity and reducing the losses? How is your company benefitting with the automation?
As stated above automation helps in fast and accurate control of machines and all process parameters which helps in producing the product efficiently and without faults.
A.T.E. Enterprises is a leader in textile engineering with 80 years’ experience and deep domain knowledge in textile processes. We have the expertise to successfully undertake automation and upgradation of older textile machines using modern controls and the latest software, if these machines are in good mechanical condition. This results in a significant improvement in the performance of older machines – in terms of productivity, quality, and reduction of operating cost.
A.T.E. also offers stand-alone products to upgrade mill productivity and quality: pre-reduced indigo dosing systems for denim manufacturing (bulk as well as portable); and dye and chemical dosing systems for the processing range like CDR, CBR, etc.
What challenges exist in integrating automation into textile manufacturing? Do challenges such as a shortage of skilled labour, MSMS’s limited expenditure, and rising plant maintenance costs contribute to the challenges?
Integrating automation into textile manufacturing comes with several challenges, and the issues you mentioned—shortage of skilled labour, MSMEs’ limited expenditure, and rising plant maintenance costs—play a significant role. Here’s a breakdown of the key challenges:
Shortage of skilled labours: As part of advanced automation, the programming of PLC, SCADA, and Drives requires specialised skills that are not easily available in the market. Additionally, many workers in textile factories lack exposure to automation, making training programs essential, which in turn adds to costs and time. Moreover, employees who are accustomed to manual processes may be reluctant to transition to automated systems.
MSMS’s limited expenditure: High initial investment poses a challenge for small and medium-sized manufacturers (MSMEs), as they often struggle with capital constraints, making it difficult to invest in automation technologies like robotic looms, automated inspection systems, or AI-driven fabric analysis. Additionally, concerns about return on investment (ROI) further discourage smaller companies from adopting automation, as the benefits are not always immediate, though in the long term, it always pays off.
Rising plant maintenance costs: Many textile plants operate older machines that are not compatible with modern automation systems, leading to increased maintenance costs. Upgrading legacy equipment to work with automation requires additional investment in retrofitting and system integration, further adding to the financial burden. Additionally, the transition phase can result in production stoppages, affecting both output and revenue.
Industry-specific challenges: Unlike industries with standardised materials, textiles involve diverse fabric types that require flexible automation solutions that can suit and work with all varieties. Additionally, automated defect detection systems need high accuracy to ensure precision and quality control, which can be costly to implement. Furthermore, the demand for customisation in textile products makes it challenging to standardise fully automated processes.
Though above challenges are there the automation and upgradation of machineries is surely a solution against large investments on new machine purchase.
How is Industry 4.0 (like AI, IOT networks, robotics, etc.) changing the landscape of textile manufacturing?
Smart automation and robotics: Robotics-driven systems enhance precision, reduce defects, and speed up production. Additionally, Automated Guided Vehicles (AGVs) and collaborative robots (Cobots) streamline material handling and reduce manual labour.
AI and data analytics for quality control: Computer vision systems identify fabric defects in real-time, reducing wastage. Additionally, AI predicts machine failures before they occur by using historical data, thereby reducing downtime.
IOT and real time monitoring: IoT-enabled sensors monitor production parameters such as temperature, humidity, and tension to optimise fabric quality. Additionally, factory managers can track machine performance and receive alerts for maintenance, ensuring efficient operations.
Digital simulation and visual prototyping: Digital simulation production environments help to test and optimise processes. Additionally, visual prototyping reduces the need for physical samples, saving both time and costs.
Sustainable & smart manufacturing: AI-driven systems dynamically adjust power usage, reducing energy consumption. Additionally, AI optimises dyeing and finishing processes, minimising water and chemical waste.
Smart manufacturing and wearable technology: Fabrics embedded with sensors monitor body temperature, heart rate, and movement, making them useful in sportswear and healthcare. Some materials can repair minor damage or change properties based on environmental conditions. Additionally, smart fabrics that change colour based on temperature or light are being developed for fashion and military applications.
Supply chain and warehousing: Blockchain for transparency ensures ethical sourcing and traceability of raw materials. Additionally, automated inventory management powered by AI predicts demand and reduces excess stock or shortages.
Lastly, what are the future trends in automation in textile industry?
The future of textile automation is driven by AI, IOT, robotics, smart fabrics, and sustainable manufacturing. Key trends include AI-powered defect detection, smart factories, automated sewing, energy-harvesting textiles, 3D-printed fabrics, and block chain-enabled supply chains. These advancements will enhance efficiency, reduce waste, enable mass customisation, and promote eco-friendly production, making the industry smarter, faster, and more innovative.