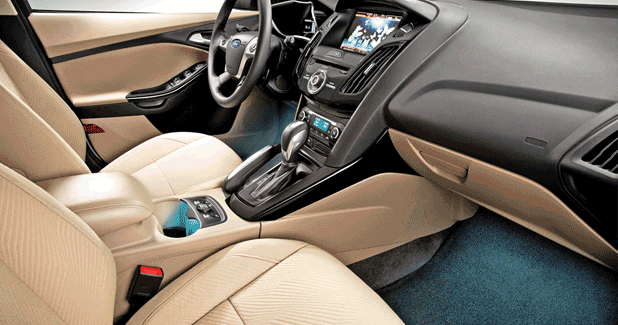
Versatile seating fabrics for automobiles
Textile fibres can be used in the transportation sector on a regular basis due to their broader versatile fibre characteristics, explain Kunal Singha and Subhankar Maity.
Textile fibres can be used in the transportation sector on a regular basis due to their broader versatile fibre characteristics, explain Kunal Singha and Subhankar Maity.
Transportation is the largest user of technical textiles. Textiles in transportation are classified as technical because of the very high performance specifications and special properties required. Seat coverings are not easily removable for cleaning and indeed in automobiles they are fixed in place and must last the lifetime of the car without ever being put in a washing machine.
In trains, aircraft and passenger vessels they are exposed to much more rigourous use than domestic furniture. In addition they have to withstand much higher exposure to daylight and damaging ultraviolet radiation (UV) and because they are for public use they must satisfy stringent safety requirements such as flame retardant. In more functional applications, textiles are used in articles as diverse as tyres, heater hoses, battery separators, brake and clutch linings, air filters, parts of suspension, gears, drive belts, gaskets and crash helmets. Fibre composites are replacing metallic components and more traditional materials with considerable benefits, especially savings in weight. The most significant growth area in transportation textiles is expected in composites that combines the textile and plastics industries.
Fibre requirements
The fibres mainly used for seat coverings, the main technical requirements are resistance to sunlight (both colour fading and fabric degradation by UV), abrasion resistance and the fabrics need to be resistant to mildew, and strong with high tear strength. The fibres should also contain the soil resistance and easy cleaning ability characteristics. Generally, for public transport vehicles we use those materials, which provide reduced flammability because seats frequently get damp from contact with wet clothing and, in the case of seats in public transport, subject to abuse by vandals and other irresponsible individuals.
Resistance to sunlight and UV degradation: Because glass windows are being placed more at an angle, the temperature within a vehicle can exceed 100°C and during the course of a day relative humidity can vary from 0-100 per cent. These factors, combined with sunlight, contribute to breakdown of seat fabric. Glass filters out a section of the sunlight spectrum including part of the UV area, which is most damaging to most fibres and in particular polyester. Hence polyester exposed behind glass exhibits much better performance compared to polyester exposed directly to sunlight. This factor is a major reason why polyester has emerged as the most used fibre for car upholstery.
Parameters affecting UV degradation: The actual degradation by UV radiation is influenced by the thickness of the yarn, the thicker the better because less radiation will penetrate into the centre and delustred yarn often breaks down the fastest because the titanium dioxide delustrant may photosensitise degradation.
UV degradation will therefore also be influenced by cross-section, the poorest again being those presenting the greater surface area for a given linear density. Moreover, significant improvements in UV resistance can be obtained by addition of certain chemicals that are UV absorbers and these are used extensively with polyester, nylon and polypropylene for transportation applications. For example, UV absorbers in nylon are usually added to delustred yarns which deactivate the sensitising effects of the titanium dioxide present.
Abrasion resistance: Seating fabric needs to be of the highest standard of abrasion resistance. Only polyester, nylon and polypropylene are generally acceptable, although wool is used in some more expensive vehicles because of its aesthetics and comfort. Fabric abrasion is influenced by yarn thickness, texture, cross-section and whether spun or continuous filament and those factors that result in larger surface area or provide points of frictional stress reduce abrasion resistance because the fabric abrasion resistant property is immensely influence by the fabric construction and weight.
Flammability: Flammability testing has become much more sophisticated as the mechanisms of fire disasters and the causes of fatalities are analysed. It is now important to test for toxicity of smoke generated and its effect on visibility as well as for ignitability and rate of propagation. Heat generated has also been identified as important and tests have been developed to measure this. Testing of whole assemblies such as seats is now carried out in addition to testing of the individual components. ?Fire blocker? materials have been introduced between the face fabric and the foam.
These are textile fabrics made from fibres with a very high level of inherent flame retardancy and heat stability, for example Panox (Lantor Universal Carbon fibres), and aramids. They are being used increasingly on trains, buses and coaches.
Seats
The seat is probably the most important item in the car interior. It is the first thing the customer sees when the car door is opened and he or she will probably instinctively touch it; there is only one opportunity to make the most of this first impression. The seat is also the main interface of man and machine and seat comfort is of paramount importance. Textiles have become by far the most widely used material in seat coverings and are beginning to be used in other areas of the seat in place of polyurethane foam. The move to replace polyurethane foam is mainly driven by recycling, communisation of materials and disposal factors at the end of the car?s life.
Methods of seat construction: The traditional method of seat making involves cutting and sewing of panels of the seat cover laminate (face fabric/foam/scrim) into a cover, which is then pulled over the squab (seat back) and cushion (seat bottom), and then fixed in place using a variety of clips and fastenings.
This process is both time consuming and cumbersome, and because it includes considerable human element, consistency of quality could be better, which is a cause for concern even with skilled operatives. Furthermore, this problem is becoming even more troublesome with modern highly contoured seats.
Foam in place: The ?foam in place? technique (also called ?foam in fabric? or ?pour in foam?), was developed in the late 1980s and achieved considerable initial success, especially with the Ford Fiesta. The method combined two separate processes into one; foam cushion and squab moulding with the fixing of the seat cover in place over the pre-moulded foam. Panels of the seat cover laminate were cut and sewn into a ?bag? and the liquid foam components were poured in. These liquids reacted together to form the solid foam, but to prevent the liquids seeping through the fabric cover laminate before the reaction was complete, it was necessary to include a polyurethane barrier film into the cover laminate beforehand. It was believed that this polyurethane film reduced seat thermal comfort because the water vapour permeability of the films used was too low to allow the passage of human perspiration. For this and other reasons, this novel method of seat making was generally discontinued for large-volume production. However, the basic method is still used for smaller, less critical items such as headrests and armrests. These smaller items do not need polyurethane films to act as liquid foam barriers, because the actual liquid foam pressure in such small items is not as great as in a seat cushion or squab. Laminate foam of higher density or slightly lower porosity, or a non-woven scrim, is generally sufficient to prevent liquid foam strike through.
Direct joining techniques: Several other methods have been developed based on directly joining the cover fabric laminate to the squab and cushion. Direct joining is especially suited to seats with curvaceous contours and it also allows a reduction in the thickness of the laminate foam. There are many variations to the basic principle and both hot-melt adhesive films and solvent spray adhesives are used. Vacuum is applied to hold the components together, and the hot-melt adhesive is activated by steam or hot air. This general method is gaining popularity because it removes some of the human variation factors (the least controllable) and generally produces a more uniform seat appearance. However there are still problems to overcome such as preserving the pile in velvets, and other raised or textured fabrics, and cover laminate thickness has become more important. Certain other quality control tests have become more critical such as cover fabric to laminate foam adhesion, which needs to be generally higher because there are fewer sewings in the new process, to help keep the two materials together. In addition, alternatives may have to be found eventually to replace solvent¬ sprayed adhesives as environmental laws tighten. Changing production to this method requires investment in costly new equipment and specially made tools.
3D knitting of car seat covers: This highly advanced, computer-controlled knitting technique enables several conventional cut and sews panels to be replaced with just a single 3D shaped piece. The objective was to knit garments in one piece, thus eliminating panel cutting and making up together with the associated cutting waste of up to 30 per cent. The potential benefits for car seat covers were soon realised and General Motors became involved. Each needle is individually computer-controlled to enable almost infinite colour combinations and design patterns. Car seat covers can be knitted in just one piece; the single item includes all tubes, flaps and tie downs necessary for direct fitting. The labour intensive stages of panel cutting and sewing of up to 17 individual pieces of fabric are reduced to just one or two with no cutting waste. The 3D technique allows considerable design flexibility and creativity. Computer-assisted design systems facilitate design themes.
Materials for seat making: Non-woven polyesters fabrics ? especially those made from recycled fibres, and novel knitted structure such as spacer fabrics, and Struto have been considered as substitutes for polyurethane foam in the cover laminate. Spacer fabric is essentially a knitting product with threads perpendicular to the plane of the fabric with a knitted layer each side. A novel development from the Czech Republic, Struto non-woven fabric, is produced from layers of fibre vertically lapped. Non-woven materials made from recycled wool and polyester has also been examined and is used commercially and the tests show that they have generally similar compression/strain characteristics to polyurethane foam (fig 1).
Materials based on polyester fibre all lose significant thickness when tested by the compression/strain test, even when the test is done at lower temperatures (table 1).
The ?touch? of these materials is quite different from polyurethane foam however (Table 1), and if this is a problem it is not likely to be overcome easily because of fundamental differences in material behaviour when compressed locally. The foam has an isotropic structure (3D) whilst the nonwoven made from a carded fleece is only two dimensional. The slight ?scrunching? sound when spacer fabrics are compressed or sat upon has also been commented upon.
Alternatives for seat squab and cushion foam: Several alternatives to polyurethane foam used in the squab and cushion have also been developed. DuPont has introduced polyester fibre ?clusters?, which have a coiled and fluffed configuration. The clusters are put into a mould made of perforated metal and hot air is applied which bonds the clusters together. They can be formed into seat cushions and squabs in place of polyurethane foam and the manufacturers claim weight savings of up to 30 to 40 per cent compared to foam. DuPont also claim the seat enable easier disassembly and recycling, and better comfort through increased breathability.
Toyobo has launched a material called BREATH AIR described as random continuous loops of a thermoplastic elastomer; similar claims of comfort and recyclability have been made. Natural materials referred to loosely as ?rubberised horse hair? have also been usec This fibrous matter, believed to include coconut fibre and pig?s hair as well as horse hair, coated with a rubber, provides good body support, has high porosity and breathability and is also claimed to be easily recycled. However it does not provide a smooth surface and the seat cover laminate foam or foam substitute must be relatively thick for a comfortable seat. In addition rubberised horse hair is said to be not a pleasant material with which to work. All of these substitute materials are not as resilient as polyurethane foam especially when tested at higher temperatures and lose significant thickness.
Tunnel tie: It is another new method of securing seat covers over the foam cushion. It features a specially designed sleeve through which a draw cord passes. The sleeve is sewn to the edge of the seat cover, which is then drawn over the foam cushion and the cover is secured by pulling the cord tight also for more complex seat forms the cord is drawn through small apertures in the sleeve and secured to the back of the cushion. Tunnel tie is economical and simple to use without the need for hooks, or plastic clips. It is also easier to disassemble, which could facilitate recycling, and especially suitable for detachable.
Sewing thread: It is an engineered material, which has to withstand considerable forces both during seat cover manufacture and also during use. The actual process of sewing makes very demanding requirements on the thread, which in typical seat covers include sudden accelerations and tensions while being drawn at high speeds through not only fabric, but also light plastics. Typical sewing speeds are around 2000 stitches a minute, or 30 per second and considerable heat can be generated. The yarn threads are spun to a high specification, resin-bonded together to prevent fraying and a carefully formulated lubricant is applied during thread manufacture which reduces needle heat and helps promote easy movement through the goods. These processes are critical to sewing performance; the thread must be round, even and balanced in twist, i.e. it must not curl around itself when allowed to hang loose. All of these properties are specified and monitored, to prevent production problems. The thread must of course last the life of the car without breaking down in any way such as snapping, shrinking or stretching. It must be very strong and have very high abrasion and UV radiation resistance in all conditions encountered in the car, including high temperatures and relative humidity.
Most car seat thread is produced from continuous filament high tenacity nylon 66 in approximately 800 to 1,200 dtex but varies according to specifications set by the Car manufacturers. Nylon is best suited for this application because of its abrasion resistance, elastic recovery and wet strength in addition to the ability to withstand the usual conditions inside a car. In a small number of cases, polyester thread is used.
Man-made leather and suede: Man-made products have the important advantages over natural leather of availability in roll form, light¬ness of weight, uniformity of quality, uniformity of thickness and other physical properties, which allow more efficient production planning, and minimisation of waste. The man-made leather also have better elongation, tear strength, mouldability and high-frequency weldability and are available in variety of colours. At present, the most successful man-made products are entirely Japanese made, and the companies involved have production expansion plans. The base materials are generally non-wovens using micro-fibres in polyester, which constitutes 68 per cent of the weight, the remainder is polyurethane resin. For use as car seat covers, the man¬made suede is polyurethane foam backed with a scrim fabric in the usual way. The best known is Alcantara, made in Italy since 1975 by a Toray/Enichem joint venture (now Toray/Mitsui) and initially used mainly in Italian cars. Over a million sq m are used at present, but this is likely to increase.
Flocked fabrics: Flocked fabrics and other flocked materials (plastics can also be flocked) are finding applications in the elimination of squeaks and rattles. Flocked articles are also useful as seals for example on car windows and they can act as a lubricant for example on the sunroof sliding hatch. Flocked fabrics at competitive prices are claimed to reproduce the appearance and touch of velvet and suede. Virtually any fibre, natural or syn¬thetic can be flocked but materials for automotive use are mainly polyester. The manufacturing process involves applying flock by either mechanical or electrostatic means to an adhesive-coated base fabric. Flock fibre is about 0.5 to 1 mm long, about 1.5 to 3.5 dtex and can be matt, bright or semi-matt yarn in any colour. Recent improvements in flock technology have expanded the scope of flocked fabrics, associated with both Rhone Poulenc and Fiat, have produced material for car seat covers. They have experimental evidence showing improved seat thermal comfort of flock fabrics.
Alternative methods of seat making
Some alternative approaches to seat making replace both seat structure and foam with textile fabric. The main benefits of these methods are reduced weight, space saving by thinner profiles, reduction in the number of components and also reduced assembly costs. Recyclability and ease of dis¬assembly are also important advantages and better thermal comfort has been claimed. The foam can be replaced altogether by inflatable system, which can be adjusted to suit individual requirement by inflating the structure. It was designed mainly for lumbar support but can also be applied to other seat areas. DuPont have publicised the possibility of a 100 per cent polyester seat; cover, cushion and seat frame. It would comprise a polyester face fabric, laminated to a polyester nonwoven fabric, covering a squab and cushion made from DuPont polyester Fibre Cluster material. The seat frame would be made from injection-moulded thermoplastic polyester and compression moulded thermoplastic polyester. The whole assembly would therefore be constructed from all DuPont polyester materials requiring minimum disassembly for recycling and would also weigh less than a conventional seat. Ultra-Flex Corporation using elastomer monofilament fibres developed a lightweight fabric seat suspension system, space¬ saving and requires less foam. Better height control, less noise and greater long-term durability are also claimed.
The use of composites and carbon fibres in seat frames of high volume production cars is a development not likely to appear for several years, but the price of carbon fibres is coming down. This development would not only save weight, it would also provide more space inside the car by allowing seats with thinner profile.
Seat comfort: The car seat must be comfortable in all senses of the word: psychologically, physiologically and thermally.
Psychological comfort: Overall aesthetic appearance; fabric yarn type; colour; seat contours; current fashion; prejudice; and suitability for vehicle. The ergonomics of seat design such as, suitability for drivers of different shapes and sizes ease of reaching controls, visibility, getting into and out of the car etc.
Physiological comfort: Its mainly attributed to some of the properties of the car seat like; softness, abrasion/roughness; smoothness? initial cold/warm feel, not too slippery, fibre shedding, prickle/tickle and allergy sensitisation. Seat thermal comfort: Thermal comfort has been defined, as ?that condition of mind which expresses satisfaction with the thermal environment; the person does not know whether he or she would prefer a warmer or a cooler environment?. A significant proportion of the seated human body is in contact with the car seat cover, which can be regarded as another layer of clothing through which perspiration must pass. Underneath the seat cover, there are the squab and cushion, made from much thicker pieces of polyurethane foam, which are additional barriers to the escape of perspiration.
Deep sew lines in the seat cover, which can act as channels for air circulation, and as an escape route for perspiration would be expected to be beneficial to seat thermal comfort. Polyester face fabric is not ideal for thermal comfort because of its very low moisture absorbency. Application of a hydrophilic finishing agent to the polyester has been shown to have some beneficial effect but finishing agents generally only have a limited life. Wool or wool/polyester blends face fabrics are more costly and more moisture absorbent but will have lower abrasion resistance than 100 per cent polyester. However some manufacturers do use wool or wool blends in seat cover laminates both in face fabric and also in the backing to reduce the stickiness feeling. In one novel development a natural fibre Ramie, is used as a moisture transport medium. Other methods to improve seat thermal comfort have been made by the use of ventilated seats using air driven by electric fans.
Textiles are eminently suitable for sound and vibration insulation and damping and also for eliminating squeaks and rattles. Natural fibres, jute, sisal and kapok, are also being considered for use in seats as alternatives to polyurethane foam. As well as environmental advantages, benefits relating to comfort such as moisture absorbency are claimed. The ability of uses of these alternative materials in dampen vibrations when used in conjunction with or in the absence of ? seat springs, needs to be established.
Conclusion
Textiles are no more limited for use as apparels clothing is just are but not the only purpose of textiles with the rapid changes in the social economic structure of our society. Many efforts are made to some and protect human life. Automotive textiles happens to be the rewarding sector finding extensive use of technical textiles in the product categories viz. interior trims, safety devices like seat belts and airbags, carpets, filters, battery separators, hood liners, hoses and belt reinforcement. Textiles, which constitute approximately 20-25 kg in a car, are not only used for enhanced aesthetic of automotive but also for sensual comfort & safety. Additionally, few textile products found their applications as design solutions to engineering problems in the form of composites, tyre reinforcement, sound insulation & vibration control. Apart from woven and knitted constructions, Nonwovens also find applications in transport textiles due to certain advantages served by them. The use of textiles in automotive applications includes floor coverings; upholstery; belts, tubes and tapes; tyre cord; safety belts; airbags; components; and filters. The global automotive industry has experienced an unprecedented boom in the recent years. From 2007-2015 India will contribute 16 per cent to the global automotive textiles. This is due to the sudden increase in the demand of automotive which is triggered primarily by the factors like increase in income and standard of living of the middle class Indian families and Indian government liberalisation measures. Further, as travel has become the integral part of everyone?s life, issues such as comfort and safety have taken on a right priority. All these factors clearly indicate brilliant prospect for automotive textile industry which lead to increased demand of the technical textiles components used in automobiles. It is expected that India will be the leading car producer (15 per cent) by 2015. Another reason for large growth in the automotive textiles is that India is a low cost manufacturing base.
References
- Viju, Mukhopadhyay S; Automotive filters; Asian-Textile-Journal. 2006; 15(5): 49-55.
- Mukopadayay S K, Partridge JF; Automotive Textiles, Textile progress, 29, No.12, 1997
- www.2.dupont.com/Automotive/en_us; dwld on 21.7.2012
- www.scienceservingsociety.com; dwld on 17.7.2012
- www.howstuffworks.com/airbag; dwld on 29.6.2012
- www.carsafety.com/airbag-wikipedia; the free encyclopedia Bauxton A., Tech. Text. Market, Oct., 1992, 34
- Adnur S; Wellington Sears Handbook of Industrial Textiles, Technomic, Switzerland, 1995, 500-506.
- Mukhopadhyay SK., Patridge JF; Automotive Textiles, Textile Progress, The Textile Institute, 29(1/2), 1997.
- Flung W., Progress in automotive textiles; Tech. Text. Intl., Feb., 1998, 22.
- Dorn M., Automotive textiles review; Text. Month, May, 1997, 19.
- Zukizi G; A short overview on automotive textiles; Man-Made Textiles in India, March 2000, Pg 113-118
- Dorn M., Current market and potential on automotive textiles industry; Melliand International, Vol.6, Sep 2000, Pg 226-228
- Mukhopadhyay SK; A review on automotive textiles II; Asian Textile Journal, Nov-Dec 2003, Pg 61-69
- Dorn M., Textile fibres used in automotive textiles; Technical Textiles, Vol.41, Feb 1998, Pg E4-E8
- Foren M; Eectronic and automotive textiles; Textile Asia, June 2003, Pg 72-73
- Mukhopadhyay SK, Patridge JF; knitwear importance in automotive textiles; Knitting Technique, 14(1992) 2, Pg106-109
- Gibbs E; progress in textile on automotive textiles; The Indian Textile Journal, June 2003, Pg 13-19
- http//:www.fibre2fashion.com; dwld on 25.7.2012
- Brad R, Coman D; Incoming quality testing for textile automotive industry; Textile department, Lucian Blaga, University of Sibiu, Romania.
- www.freepatents.coms ; dwld on 21.7.2012
Kunal Singha is with the National Institute of Fashion Technology, Patna. He can be contacted at: kunal.singha@nift.ac.in
Subhankar Maity is with the National Institute of Technology, Jhalandhar