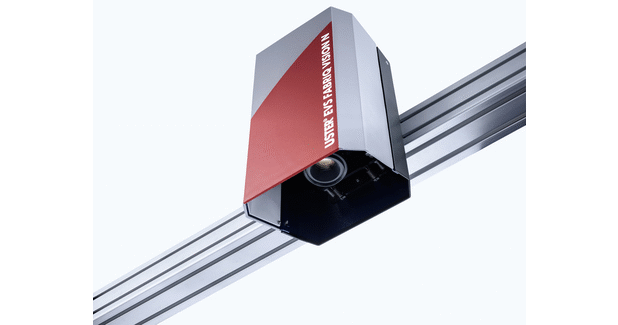
USTER in-process inspection for tightly-spaced production lines
Fabric manufacturers serving critical applications need quality that is both precise and secured. But in the typical nonwovens process line, space is always at a premium, making it tough to fit suitable automated inspection systems which deliver these requirements effectively.
Fabric manufacturers serving critical applications need quality that is both precise and secured. But in the typical nonwovens process line, space is always at a premium, making it tough to fit suitable automated inspection systems which deliver these requirements effectively. The USTER®EVS FABRIQ VISION N inspection technology solves the problem, with customised solutions designed to slot neatly into tightly-spaced production units – at the same time ensuring light conditions allow the best detection results and reliable data for optimal first quality yield.
USTER offers quality solutions suited to nonwovens premium segments. In textile applications from fibre to fabric, USTER expertise is already appreciated worldwide. Now the nonwovens community is recognising what has been acknowledged in the spinning industry for more than 70 years. Expert knowledge in yarn quality – including controlling all kinds of contamination – is now extended to fabric and nonwovens quality assurance. This is based on the know-how of EVS, a world-leading high-technology supplier of automated vision inspection, acquired by USTER in 2018.
USTER®EVS FABRIQ VISION N fabric inspection now represents a second solution for nonwovens – along with USTER®JOSSI fibre cleaning systems – supporting the unique ‘Think Quality’ approach of USTER.
Automated in-process control
Consistently high rates of defect detection, to guarantee reliable quality, are required by fleece manufacturers. USTER®EVS FABRIQ VISION N ensures this, by using automated control during intermediate inspection. USTER®EVS FABRIQ VISION N locates any visible faults objectively and consistently. Defects in every roll are located and recorded, at normal line running speeds.
USTER®EVS FABRIQ VISION N stands for seamless integration of an inspection system into any production process – and ideally into nonwovens manufacturing lines –detecting holes, irregularities, contamination and any other defect. The installation is easy and flexible: a fixture bar bridges the full width of the process line holding as many spectroscopes as required for the application. The sophisticated spectroscopes offering best monitoring conditions for the inspection. To guarantee optimal defect detection in combination with the spectroscopes, various light sources are integrated in the installation – all customised and perfectly suited to mill light conditions.
The system may be slim and compact, but it delivers big-value benefits for the operator. USTER®EVS FABRIQ VISION N provides real-time alerts, showing all defects and automatically creating roll inspection charts. All detected faults are collected in an album review. Here, the operator can quickly mark faults and select which can be deleted. Users can set their own quality standards for different types of nonwovens, increasing the efficiency of the grading process – and finally delight the customers with consistent quality.
Optimised yield for manufacturers
“USTER®EVS FABRIQ VISION N offers manufacturers significantly improved first-quality yield, for all applications,†says John Belew, USTER Vice-President for fabric inspection. The combination of a full map of fabric defects and the cut optimisation module means more first-quality rolls can be produced and bad quality taken out.
USTER®EVS FABRIQ VISION N leads to total fabric quality assurance, and major advantages for production security and profitability. “Our customers aim for confidence in delivering the right quality to strengthen customer relationships. With USTER® fabric inspection systems, they can guarantee quality compliance and protect their business,†says Belew.