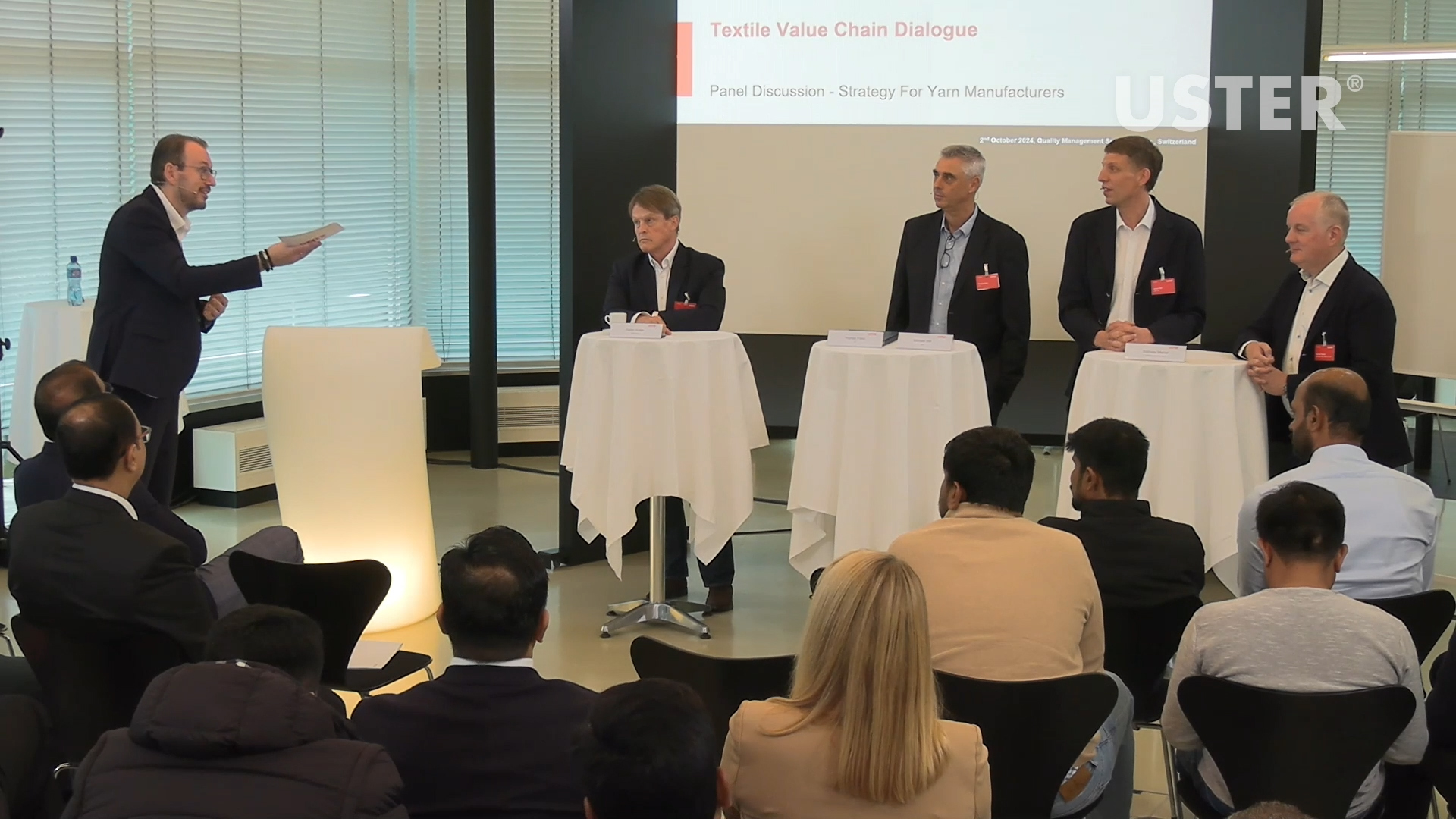
Uster discusses complexities of yarn manufacturing from recycled fibres
Experts from Rieter, Säntis Textiles, Otto Yarns, and TVU commented on the current situation and looked into the future of spinning in a panel discussion organised at Uster headquarters.
What does it take to spin quality yarn from recycled fibres? Uster Technologies brought textile industry leaders together to discuss the role of technology, data and automation – as well as the current challenges in using recycled raw material. Experts from Rieter, Säntis Textiles, Otto Yarns, and TVU commented on the current situation and looked into the future of spinning in a panel discussion organised at Uster headquarters.
It’s more than just machinery – it’s about rethinking processes, embracing AI, data and machine automation as well as building industry-wide collaboration. As spinners navigate the multiple demands of circularity, customer satisfaction, and profitable business, one thing is clear: the future of recycled textiles must be individually engineered, comprehensively tested, and connected like never before.
Standards and individuality: Engineering for reliability and diversity
Advanced machinery is a critical component in enabling engineering teams to optimize processes and drive innovation. Machines from leading manufacturers offer reliability but don’t make an inimitable product. “With the goal of being different and unique, we create our own path by developing our own final machines,” says Andreas Merkel, CEO at Otto Yarns. Otto engineers customize the machines for specialized applications. A notable example is the Spin-Knit system, which integrates spinning and knitting into one continuous operation. Originally configured for cotton, the machine was re-engineered to process technical fibres, by removing the standard top section and implementing a proprietary drafting system.
The production of recycled yarns brings technical requirements that are significantly different from those with virgin fibres. According to Stefan Hutter, owner of Säntis Textiles, there is a clear need for the development of new industry standards tailored specifically for recycled materials, and he advocates for Uster Technologies to take a leading role in this effort. Ultimately, the successful integration of advanced production machinery, newly-defined quality standards, and precise quality control systems will require close industry collaboration. This is the only way that confidence in recycled yarns can be established – ensuring that customers not only trust the product’s performance and consistency but are also willing to invest in its value.
Adapting spinning processes for recycled yarns
Recycled yarn production can be achieved with existing spinning technologies, either by adapting current systems or by integrating additional processing steps. “Spinners must go back to the basic task and again learn how to spin, starting from scratch and going through the whole line of spinning,” says Michael Will, Head Textile Technology & Process Analytics at Rieter. This re-learning process is essential due to the variable nature of recycled fibres, and it demands extensive testing and data collection – measuring key parameters, validating process changes, and ensuring consistency through iterative quality control.
Growing customer demand for more automation presents a dual challenge: matching the need for maximum flexibility with the rigid configurations typical with interconnected automated systems. In conventional spinning mills, linking multiple machines can limit process adaptability. However, machine-level automation offers potential for enhanced flexibility, particularly when processing smaller lot sizes. For instance, features such as automated adjustment of comber nip distances can streamline setups.
The role of data and AI
In the recycling process, sorting, separating, and cleaning are advanced operations in which artificial intelligence plays a critical role in pattern recognition and optimization. In this way, AI enables optimization of material recovery at the right quality, to improve process efficiency. Another key area is traceability, which ensures product reliability and builds trust throughout the supply chain. “For downstream processes such as dyeing, it must be possible to trust certificates,” says Thomas Franz, Sales and Purchasing Manager at TVU.
Data analysis is fundamental to these efforts, but it becomes truly effective only when integrating comprehensive data streams. This means connecting spinning machinery and testing instruments – ideally across different brands – to enable holistic process monitoring and control. For spinners, seamless working between equipment and systems is crucial to unlocking maximum operational benefits and ensuring consistent quality in recycled yarn production.
Enabling the future would start with technology partners meeting, discussing and working together. This is a common belief of the experts participating at the panel discussion – and the Uster event has been one step in this direction.