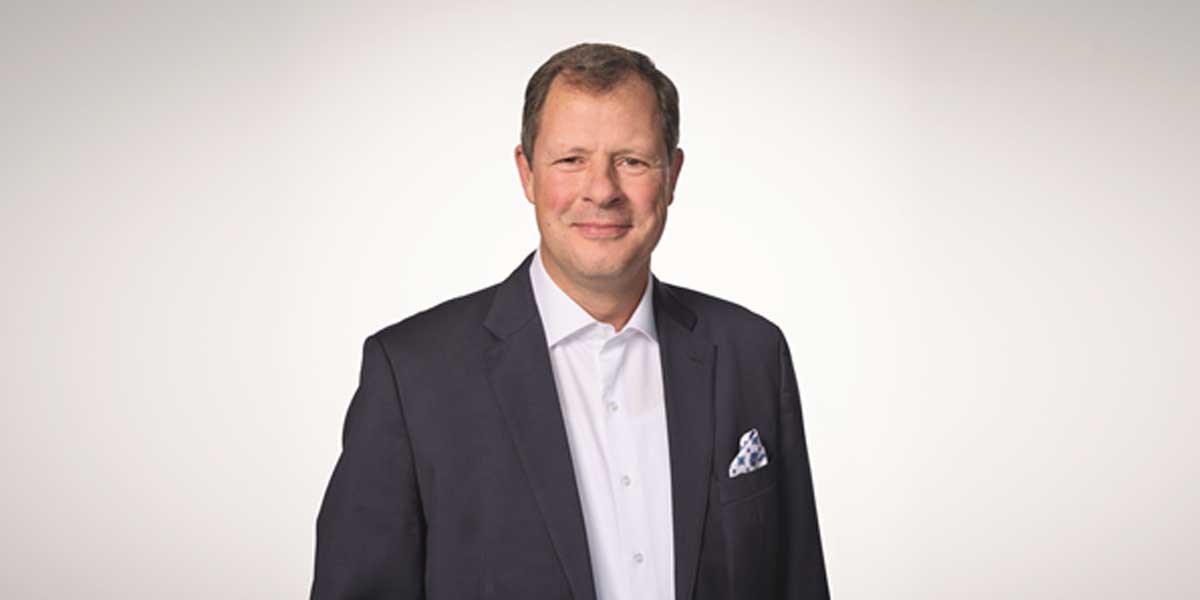
Thomas Oetterli: The future of spinning is automated, digital and smart
Rieter is the world’s leading supplier of systems for manufacturing yarn from staple fibres in spinning mills. Based in Winterthur (Switzerland), the company develops and manufactures machinery, systems and components used to convert natural and man-made fibres and their blends into yarns in the most cost-efficient manner. Thomas Oetterli, CEO, Rieter, sat down with Divya Shetty to deep dive into the company’s latest technology advancements and explore what’s in store for the year ahead.
Switzerland has long been recognised as a global leader in textile machinery. What factors have contributed to its stronghold in this sector?
Switzerland regularly tops country rankings for innovation. At Rieter, we invest around five percent of our sales in research and development for spinning systems as well as digitisation solutions.
How does your company contribute to innovation and technological advancements in textile machinery?
Our Campus headquarters in Winterthur (Switzerland) are home to one of the industry’s most modern innovation and technology centres, where we combine our extensive know-how and longstanding experience in the yarn manufacturing process under one roof. Our R&D focus is on automation, digitisation, artificial intelligence and recycling technologies. The ultimate goal is to enable customers to realise the full potential of their spinning mills under sustainable production conditions.
What are the key strengths of Swiss textile machinery in terms of automation, precision, and sustainability?
In the spinning sector, we are a technology leader and set the pace for innovation. As the only systems provider covering all process steps and all four end-spinning technologies, our expertise in converting fiber to yarn puts us at the forefront of the industry. With Rieter technology, spinning mills are able to maximise resource efficiency and minimise cost conversion, while achieving higher yarn quality.
How significant is the Indian market for your company, and what strategies have you adopted to expand your presence in India?
India is one of our key markets. The country’s middle class is expanding steadily with fiber consumption set to rise accordingly. India is uniquely positioned to benefit from these growth prospects because it has access to an abundant supply of cotton, a deep pool of workers and a strong spinning industry that creates high-quality yarns for downstream processes. This is further underpinned by government initiatives that are helping small and medium sized businesses access affordable technology solutions. To help mills embrace automation, digitisation and recycling technologies so they can seize the growth opportunities ahead, Rieter has strengthened its manufacturing and R&D capabilities in the country.
What are the latest trends and challenges in the global textile industry, and how is Swiss textile machinery addressing them?
Five megatrends are reshaping the textile industry and thus yarn manufacturing. Sustainability is an overarching megatrend as the textile industry is a key contributor to climate change. With fibre consumption rising, recycling and resource-efficient technology like ours will become ever more important.
Manufacturing is facing a major labor shortage that is set to worsen due to aging populations, loss of qualified workers and changing skill requirements. For spinning mills, we offer state-of-the-art automation technologies to help them overcome labour shortages.
Digitisation is transforming production processes in every industry, driven by the
Internet of Things and artificial intelligence. Rieter’s vision is to create smart spinning mills with fully automated production – from fibre delivery to package palletising.
As fiber consumption is projected to rise, the majority of growth will come from man- made fibres. The growth of natural fibres such as cotton and linen is limited. Man- made fibres such as viscose or polyester will help to meet expanding demand for clothing, technical and home textiles.
The decoupling of the global economy is accelerating the trend towards a reshaping of the customer service footprint and a localising of supply chains. Rieter has relocated production and R&D closer to customers, sharpening customer-centricity, accelerating the speed of product development and improving agility.
Sustainability is a key focus in modern textiles. How is your company integrating eco-friendly solutions into its machinery?
Rieter uses its technology expertise to offer a complete recycling spinning system for both ring and rotor spinning lines. This enables customers to spin fibres from used garments and textile waste into yarn, thus helping to close the loop in textiles. Rieter has established a recycling classification system for the typical raw-material quality available on the market. The classification system makes it easier for spinners to estimate what targets can be reached depending on the raw material. Rieter also helps customers develop yarns that use sustainable chemical fiber manufacturing processes.
What are your future plans for growth and innovation in the textile machinery segment, particularly in emerging markets like India?
The future of the spinning industry is automated, digital and smart. As mills struggle to hire and retain workers, automation technology is essential in order to ensure consistent and efficient operations. Rieter has stepped up its R&D activities to fully automate the value stream by 2027 through autonomous transport systems and collaborative robotics. Rieter’s digital spinning suite ESSENTIAL will be the command-and-control center of smart and high-performing mills that lower cost and maximise returns. Customers will be able to fully focus on their yarn business by outsourcing their operations to Rieter technology and expertise.