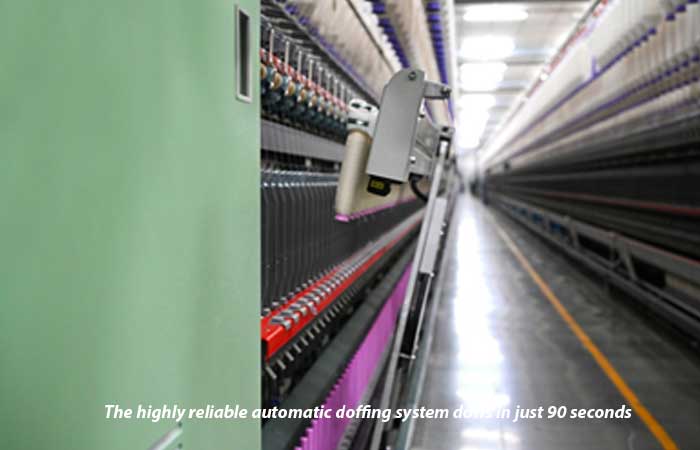
The new generation Rieter Ring Spinning Machine G 38 redefines boundaries
Maximum production in ring and compact spinning not only means offering the highest spindle speeds. Noticeable production benefits can be achieved by significantly reducing machine downtimes. And this is where the new version of the ring spinning machine G 38 leads the way.
The market for ring yarns is large and highly competitive. To succeed in this fiercely competitive market, spinning mills must be highly efficient. The latest ring spinning machine G 38 offers maximum production based on new technical solutions and upholds its reputation for efficiency by minimising its energy consumption.
The highlights of the latest generation ring spinning machine G 38 are: the new doffing system with a doffing cycle time of just 90 seconds, the 12 per cent faster cop transport with SERVOdisc and the new short-balloon setting for balanced yarn tension peaks to reduce the ends down rate. Combined with the highest spindle speed of 28 000 rpm, the G 38 ensures maximum competitiveness in the production of ring and compact yarns in all yarn count ranges.
Doffing in 90 seconds leads to production gain
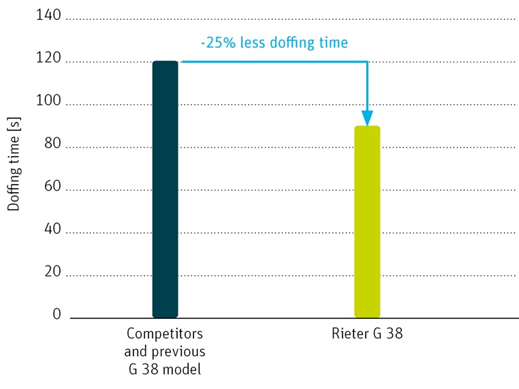
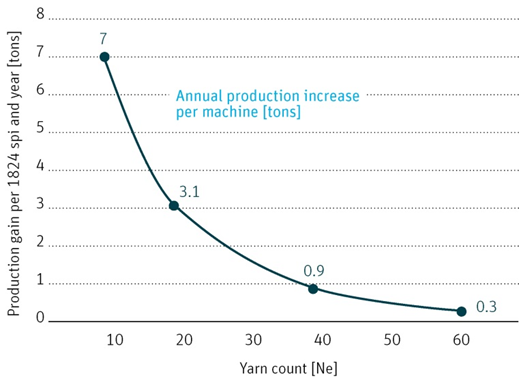
Figure 2: 25% faster doffing leads to a remarkable production gain
The latest and highly reliable automatic doffing system of the G 38 (Figure 1) is equipped with a perfect alignment of grippers, tubes, and cop trays and thus enables a fast sequence of all doffing process steps. The redesigned doffing system completes its cycle in just 90 seconds (Figure 2), which means 25 per cent less time compared to the prior version of the G 38 and all known competitors. The advantage is particularly evident with coarse yarn counts. With a yarn count of Ne 10 the annual production gain is seven tonne and for Ne 20 it is 3.1 tonne for a machine with 1 824 spindles.
12% faster cop transport
The new cop transport system SERVOdisc for the link system with the winding machine Autoconer X6 is 12 per cent faster than the previous solution. It forwards up to 45 cops per minute directly to the winding machine. This open rail system is fast enough to remove all cops on time before the next doffing cycle is due. This is important for long machines with short spinning cycles because of very coarse yarn counts. The optimised SERVOdisc is even more reliable and needs less maintenance. Intelligent cop trays, called Smarttray, with an integrated RFID chip are available with the link system to the Rieter winding machine Autoconer X6.
Production increases of up to 2%
The limiting factors in ring yarn production are yarn tension peaks and the interaction with the ring and traveller. One of the most important tasks therefore is to balance the tension peaks during cop build-up. A short-balloon setting optimises these ratios and brings clear advantages in terms of less ends down and longer traveler lifetime.
Alternatively, the short-balloon setting allows to increase spindle speed by up to 2 per cent while keeping the ends down rate constant.
New G 38 generation: Today’s offering for flexible yarn production
The new G 38 is available either as a machine with a fully electronic system or with a semi-electronic system. In both cases, the spindle speed, the yarn twist, and the yarn twisting direction, Z or S, can be changed electronically and without additional mechanical adjustment. The yarn count can be changed electronically via the panel on the fully electronic machine.
The Individual Spindle Monitoring (ISM)-system premium is now standard on every ring spinning machine and for all applications. This is a great advantage for efficient operator guidance and easy detection of spindles which are not running correctly. ISM premium is the precondition for the fully automated piecing robot ROBOspin to produce high-quality yarn while mitigating labor related challenges.
With a million units installed, customers clearly recognize the benefits of the add-on compacting devices COMPACTdrum and COMPACTapron in terms of yarn quality and performance. The flexible conversion into compact, slub or core yarn production, is a major advantage of the ring spinning machine G 38.
About Rieter
Rieter is the world’s leading supplier of systems for manufacturing yarn from staple fibres in spinning mills. Based in Winterthur (Switzerland), the company develops and manufactures machinery, systems and components used to convert natural and
man-made fibres and their blends into yarns in the most cost-efficient manner. Cutting-edge spinning technology from Rieter contributes to sustainability in the textile value chain by minimising the use of resources. Rieter has been in business for more than 225 years, has 18 production locations in ten countries and employs a global workforce of around 5 100, about 16 per cent of whom are based in Switzerland.