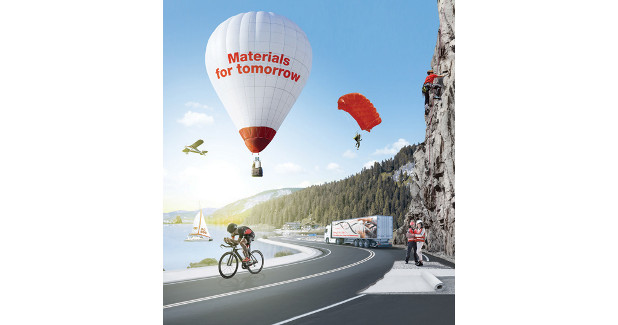
The materials that the future is made of
At home, at work, on the street, in the sky, on the water, even in space, technical textiles and nonwovens are swinging towards ever higher performances in amazing applications.
Hall: 3 | Booth: B06
At home, at work, on the street, in the sky, on the water, even in space, technical textiles and nonwovens are swinging towards ever higher performances in amazing applications. Versatile and light, but sometimes stronger than metal, these materials of the future gain their superpowers from the interaction of precisely coordinated textile systems. At Techtextil in Frankfurt am Main from May 14 to 17, 2019 in Hall 3, B06, Oerlikon will be showing chemical fibre applications made of polyester, polypropylene and Co. and what they can do in these fields. However, these exhibits are only a communicative means to an end, as Oerlikon is primarily interested in placing the associated machinery and plant solutions at the centre of discussions with trade fair visitors.
More than two thirds of all technical innovations are directly or indirectly based on new materials, says the German Research Ministry. One could add: The key to a more advanced world, for technological products with amazing functions, breathtaking performance and greater environmental benefits, is also to improve the properties and processing of materials. This applies first and foremost to textiles. Probably no other fabric is so strong as a “team player†who draws its strength from its cohesion.
A single polyester thread, for example, looks inconspicuous. Processed into a thigh-thick special weave, however, high-strength High Modulus/High Tenacity fibres anchor floating oil platforms in the deepest waters. These kilometer-long “Mooring Ropes†withstand a breaking load of well over 1,000 tons and perform their task better than steel. For decades, Oerlikon Barmag has been offering special solutions for the production of so-called industrial yarns (IDY) that are tailored to customers worldwide. “We will once again be presenting numerous innovations at this trade fair to inspire our customers,†explains Dr.-Ing. Dipl.-Chem. Roy Dolmans, Technology Manager IDY and R&D Filament Processing.
Strong and light fabrics make you mobile
But everyday textile products also meet high demands, as the manufacture of car safety belts shows. Their special fabric construction made of lint-free PET yarn is both stable and stretchable to protect vehicle occupants in the event of a collision, but not to injure them. In the automotive world, chemical fibers have become indispensable: the German Textile Research Board already says that every car drives with around 30 kg of textiles. They are found in airbags, car roofs, upholstery, trim, switches, operating elements, drive belts or hoses.
“The automotive industry is also interested in low costs when it comes to their use. A prime example of the economic production of technical textiles in the automotive sector is the manufacture of tyre cord from HMLS (High Modulus Low Shrinkage) yarns. These precursors made of polyester are extremely tear-resistant, still highly elastic as well as temperature and dimensionally stable,†explains Dolmans. The topic of traceability along the entire textile value chain plays also a major role, especially in the automotive industry. “Thanks to our production and process solutions for our customers and our own DIN ISO certifications, we at Oerlikon can guarantee traceability in the production process at any time,†continues Roy Dolmans.
Twisted into a flat fabric, the industrial yarns lie between several rubber layers and stabilise the car tires on the road. Talking of roadways, technical yarns are also at work underneath. Geotextiles secure and stabilise the soil in road and path construction. The flexible surface structures made of PET fibres, for example, are extremely tough, creep-resistant and can survive underground for decades.
High-tech membranes made from 5th building material
Textiles have long since arrived in the construction sector and are increasingly playing a role as the “fifth building material†alongside steel, concrete, wood and glass. Innovative solutions include high-tech membranes made of specially coated polyester fabrics, already used for roofs of football stadiums in Warsaw and Kiev or the international airport of Bangkok.
Building materials of the future are also nonwovens. The non-woven, textile fabrics can be equipped with a variety of properties on the basis of various manufacturing processes and combination techniques. They are temperature- and shock-resistant, breathable and at the same time resistant to moisture, mold and detachment, and are used for roofing, insulation, insulation and drainage throughout the construction sector. Oerlikon Nonwoven offers the corresponding machine and system solutions. But not only there: In medicine, nonwovens are experiencing a real boom as an inexpensive material for surgical gowns or bandages, because they function as a liquid or bacterial barrier, but remain vapourpermeable and absorbent and do not stick together. The range of applications extends from baby diapers, wipes and napkins to geotextiles and felt carpets. And here, too, Oerlikon Nonwoven is far ahead.
For the large variety of textile floor coverings, special textured continuous filament yarn made of polypropylene or polyester is particularly suitable: Oerlikon Neumag stands for this as the expert for machine and plant solutions for the production of BCF yarns with a wide variety of properties.
Versatile nonwovens & smart textiles
Functional clothing textiles are a playground for innovative applications of technical yarns. The spectrum of new developments ranges from breathable tracksuits with living microbial cells that react to moisture fluctuations to smart clothing that uses electronics and sensors to open up previously unknown functions. Smart textiles can generate heat, light and electricity, measure temperature and vital functions, heal wounds and reduce pain, modernise industries and make cars and construction safer or more comfortable.
Given this future scenario, it is no wonder that technical textiles, the materials of tomorrow, are on the upswing worldwide. Analysts such as the London market researchers of Future Market Insights estimate that the world market volume for technical textiles will climb from around $166 billion in 2016 to a good $260 billion in 2027. This upswing will certainly also drive the market for polyester fibres, which has been growing continuously for many years.
The intelligent processing of such manmade fibres as raw materials is an important foundation for future textile innovations. Market leaders such as the Oerlikon Manmade Fibers segment and its brands Oerlikon Barmag, Oerlikon Neumag and Oerlikon Nonwoven stand for this. Their innovative technologies from melt to yarn, fibres and nonwovens lay the foundation for many of the applications mentioned here – and for ever higher performance, efficiency and quality on the journey to tomorrow’s materials.
Oerlikon develops modern materials, systems and surface technologies and provides specialised services aimed at securing high-performance products and systems with long lifespans for customers. Supported by its technological core competencies and its strong financial footing, the corporation continues its medium-term growth plan by implementing three strategic factors: focusing on attractive growth markets, ensuring structural growth and expanding through targeted M&A activities. Oerlikon is a globally-leading technology and engineering corporation, operating its business in two segments (Surface Solutions and Manmade Fibers) and employing around 10,500 members of staff at 175 sites in 37 countries worldwide. In 2018, Oerlikon generated sales of CHF 2.6 billion and invested around CHF 120 million in R&D.
With its Oerlikon Barmag, Oerlikon Neumag and Oerlikon Nonwoven brands, Oerlikon Manmade Fibers segment is the world market leader for manmade fibre filament spinning systems, texturing machines, BCF systems, staple fibre systems, solutions for the production of nonwovens and – as a service provider – offers engineering solutions for the entire textile value added chain. As a future oriented company, the research and development at this division of the Oerlikon Group is driven by energy-efficiency and sustainable technologies (e-save).
With the supply of continuous polycondensation and extrusion systems and their key components, the company caters to the entire process – from the monomer all the way through to the textured yarn. The product portfolio is rounded off by automation and industry 4.0 solutions. The primary markets for the products of Oerlikon Barmag are in Asia, especially in China, India and Turkey, and – for those of Oerlikon Neumag and Oerlikon Nonwoven – in the USA, Asia, Turkey and Europe. Worldwide, the segment – with just under 3,000 employees – has a presence in 120 countries of production, sales and distribution and service organisations. At the R&D centers in Remscheid, Neumünster (Germany) and Suzhou (China), highly-qualified engineers, technologists and technicians develop innovative and technologically-leading products for tomorrow’s world.