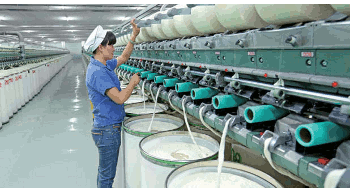
The economic R 35 offers flexibility for applications
Thanks to the new S 35 spin box and improved technology, the semi-automated R 35 rotor spinning machine is able to process a wider range of raw materials. With 500 spinning positions, it achieves maximum production rates, explain Karel Bonek and Jagadish Gujar. The R 35 semi-automated rotor spinning machine is the economical alternative to produce quality yarns Ne 2 to Ne 40 using state-of-the art technology.
Thanks to the new S 35 spin box and improved technology, the semi-automated R 35 rotor spinning machine is able to process a wider range of raw materials. With 500 spinning positions, it achieves maximum production rates, explain Karel Bonek and Jagadish Gujar.
The R 35 semi-automated rotor spinning machine is the economical alternative to produce quality yarns Ne 2 to Ne 40 using state-of-the art technology. With up to 500 spinning positions, it stands for good quality, high production performance and, thanks to the improved AMIspin technology, for excellent piecer quality with fast machine start-up (Fig 1).
Highest productivity
The S 35 spin box with improved and sensitive fibre opening leads to high fibre utilisation. The benefits are good yarn quality and high spinning stability, even at rotor speeds of 120 000 min-1 (Fig 2). The R 35 with the new box, in combination with the new electronic yarn traverse, achieves competely new production output rates at delivery speeds of up to 200 m/min and full machine length.
Technology for high efficiency
The productivity with the S 35 spin box is complemented by a further development of the AMIspin piecing technology. The simplified piecing operation leads to higher machine efficiency.
The R 35 with totally independent machine sides is equipped with two separate package conveyor belts. This guarantees maximum protection against package mix-ups. Lot changes or maintenance can be performed with minimally reduced production loss on one half of the machine while production continues on the other side.
The new individual motor for sliver feeding ensures that only undamaged fibres are used for piecings. The technical solution is based on Rieter’s know-how of automatic piecing. The supplied fibre quantity is adapted in such a way that an optimal appearance of the piecing with consistently high quality is ensured.
The R 35 can be optionally equipped with the new Q 10 generation of yarn clearer. All settings are adjustable on the machine panel. The Q 10 guarantees a 100 per cent quality check of yarn and piecings.
The new function Fast Spinning-In (FSI) assists the operator for a high level of machine efficiency (Fig 3). After a clearer cut, searching for the yarn end is unnecessary as it is clearly visible and accessible for the operator. Fast Spinning-In not only shortens the spinning interruption but also increases the probability that the operator eliminates the fault from the yarn package.
Increased raw material utilisation thanks to optimised opening area and opening housing. Raw material costs represent more than half of the yarn manufacturing costs. Practical experiences with the R 35 show, in comparison to other machines, that the loss of good fibres is reduced without influencing yarn values like yarn strength and imperfections.
For spinning of waste and regenerated fibres on semi-automated rotor spinning machines it is decisive to have best spinning stability and to ensure an easy and fast piecing operation (Fig 4) in order to handle higher ends down rates. In this connection, the optimised opening roller housing is the result of specific developments for this area of application.
Secured winding quality
The semi-automated Rieter rotor spinning machines are renowned for their outstanding piecing and winding quality at high delivery speeds. This is a prerequisite for the processing of viscose fibres. Viscose yarn packages have a high density. This requires an effective damping and high stability of the winding system. The winding system of the R 35 uses similar components as the automated R 60 rotor spinning machine. This is the most accepted winding mechanism for viscose yarns.
Optimised spinning geometry
In order to extend the economical rotor spinning process to more applications, Rieter has continued to work with specially treated and regenerated wool fibres.
In recent years, customers have also started processing wool and its blends on semi-automated rotor spinning machines. Extensive in-mill evaluations by a wool spinner show that the R 35 has advantages in wool processing, as there is a possibility to optimise trash extraction on the S 35 spin box.
Quality Spinning-In (QSI)
Continuous development of the modern drive and control concept of the R 35 is made together with the other Rieter rotor spinning machines. New advantages are created for customers. The QSI process has been introduced especially for the start-up of the machine after a planned or unplanned machine stop. Quality Spinning-In stands for a rapid start-up after power failure (Fig 5) with 100 per cent AMIspin piecing quality.
The system works irrespective of the application with minimum operator requirement. The preparations can be already started during the machine stop. Once the power is back, spinning start-up is completed very fast. All spinning positions of the R 35 are automatically started in a few minutes. Piecings are created with the renowned high AMIspin quality.
Karel Bonek and Jagadish Gujar are from from Product Management – Rotor at Rieter. They can be contacted at: karel.bonek@rieter.com and jagadish.gujar@rieter.com.