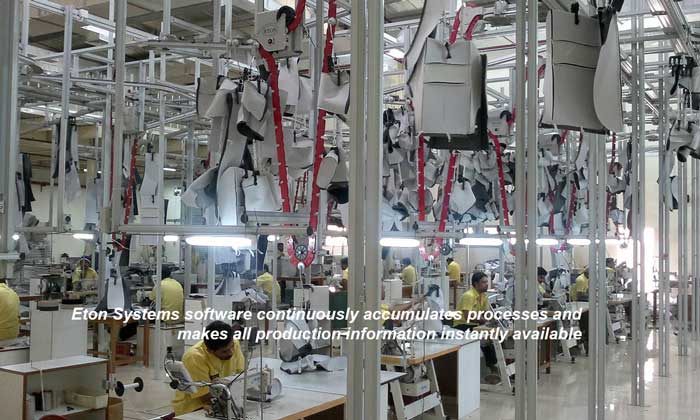
Swedish digitised solutions at Techtextil and Texprocess 24
TMAS will display technologies completely in alignment with the major digitalisation theme.
Members of TMAS – the Swedish textile machinery association – will display technologies completely in alignment with the major digitalisation theme of the forthcoming Techtextil and Texprocess 2024 exhibitions taking place in Frankfurt from April 23-26.
“Textile manufacturers who don’t embrace the new possibilities of digitalisation – in addition to continuing to make sustainable gains – will very soon face obstacles to their progress,” says Therese Premler-Andersson, Secretary General, TMAS.
Automatic handling
The fully automated and digitised handling solutions for finished garments, home textiles and furniture of Eton Systems, for example, will be demonstrated at Texprocess, at stand F31 in Hall 8 in Frankfurt.
Designed to increase value-added time in production by eliminating manual transportation and minimising handling, the individually addressable product carriers are fully managed and controlled by the latest ETONingenious software. This web based real-time data collection and information system continuously accumulates, processes and makes all production information instantly available to supervisors, quality control personnel and management.
Caption for the image: Eton Systems software continuously accumulates processes and makes all production information instantly available.
“Our latest software enables full transparency at all stages of making up and assemby,” says Jerker Krabbe, CEO, Eton. “Over the years we have accumulated significant knowledge of production requirements, customer demand and challenges within the working environment and we are always listening to our customers in many diverse sectors in order to help them further improve and fine tune their individual software platforms. ETONingenious is equipped with an immensely powerful web based graphical user interface fully adapted to the production environment.”
Bespoke seams
Also in Hall 8 at Texprocess, at stand D49, Svegea will demonstrate its EC 300-XS colarette technology which is used by garment manufacturers around the world for the production of tubular apparel components such as cuff and neck tapes and other seam reinforcements.
“Our latest software enables full transparency at all stages of making up and assemby,” says Jerker Krabbe, CEO, Eton. “Over the years we have accumulated significant knowledge of production requirements, customer demand and challenges within the working environment and we are always listening to our customers in many diverse sectors in order to help them further improve and fine tune their individual software platforms. ETONingenious is equipped with an immensely powerful web based graphical user interface fully adapted to the production environment.”
Bespoke seams
Also in Hall 8 at Texprocess, at stand D49, Svegea will demonstrate its EC 300-XS colarette technology which is used by garment manufacturers around the world for the production of tubular apparel components such as cuff and neck tapes and other seam reinforcements.
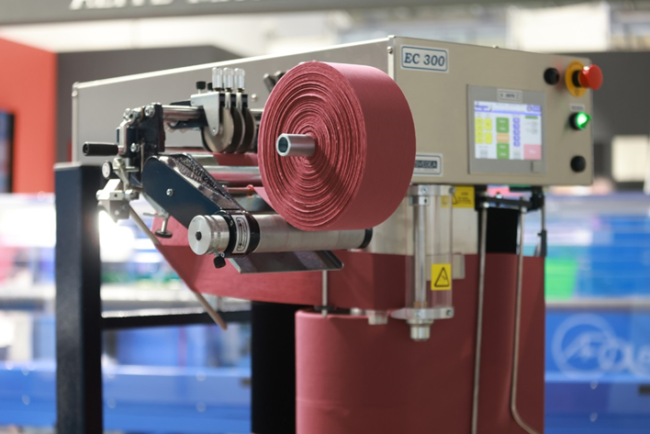
Advances in automation are making the specialised, bespoke machines engineered by Swegea ever more efficient.
“Advances in automation are only making the specialised, bespoke machines we engineer ever more efficient,” says Svegea Managing Director Håkan Steene. “At the moment we’re seeing a lot of interest in the reshoring of operations by our customers, to bring final-stage manufacturing closer to the key European and US markets.”
The EC 300-XS collarette cutter on show in Frankfurt is equipped with the latest E-Drive II system providing the operator with a very user-friendly touchscreen, providing full control of the cutting process. An accompanying FA 350 fully automatic roll slitting machine will also be demonstrated.
“A key function is the ability to ensure perfect synchronization of the tubular fabric between the machine’s turntable platform and its upper cutting body,” Steene explains. “We supply a wide range of automatic collarette band cutting machines with capacities to match the needs of our customers.”
Digital finishing
At Techtextil meanwhile, Baldwin Technology Co will provide full details of how its highly digitised TexCoat G4 non-contact spray technology for textile finishing and remoistening not only reduces water, chemicals and energy consumption, but also provides the flexibility to adapt to customer requirements in terms of single and double-sided finishing applications.
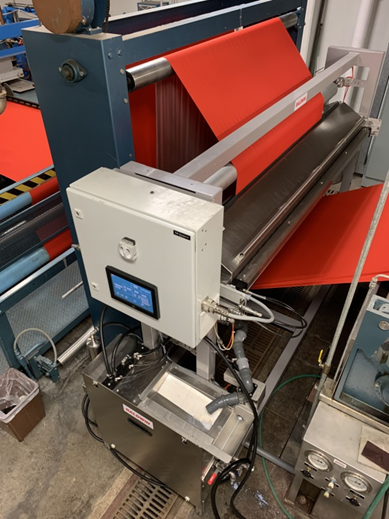
Baldwin TexCoat G4 key reference system at North Carolina State University.
TexCoat G4 can reduce water consumption and chemical usage by as much as 50% compared to traditional padding application processes.
Baldwin now has more than 100 systems installed globally, with key reference systems in place for the TexCoat G4 at North Carolina State University and Graniteville Specialty Fabrics in the USA, as well as at Pincroft in the UK. Most recently, the company has announced the commissioning of a major line at Fakhruddin Textile Mills in Bangladesh.
“Since its introduction, global textile finishers have embraced TexCoat and are now reaping the benefits,” says vice-president of global business development Rick Stanford. “They have been able to increase profitability, cut energy use and reduce their carbon footprint in addition to exercising precision control with our patented precision spray technology.”
Baldwin will be at stand D63 in Hall 12 at Techtextil.
Yarn tension
Assisting in the automated precision of the latest high speed weaving systems is the domain of two further TMAS companies exhibiting at Techtextil.
Celebrating its 60th anniversary this year, Eltex will display the latest Eltex EyETM system for the continuous monitoring of yarn tension on warp beams stand C53 in Hall 12.
The Eltex EyETM eliminates problems when warping, and also in subsequent weaving or tufting processes, monitoring the yarn tension on all positions in real-time and enabling a minimum and maximum allowable tension value it be set. If any yarn’s tension falls outside these values the operator can be warned or the machine stopped.
The Eltex ACT and ACT-R units meanwhile go beyond yarn tension monitoring to actually control yarn tension. This extends the application range greatly. The plug and play system automatically compensates for any differences in yarn tension that arise, for example from irregularities in yarn packages.
“In today’s highly optimised textile production environments, yarn tension has become an important parameter in eliminating faults and ensuring premium quality at all times,” says Brian Hicks, CEO, Eltex.
Accumulated know-how
Vandewiele Sweden AB (stand D20, Hall 12) benefits from all of the synergies and accumulated know-how of the market-leading Vandewiele Group, supplying weft yarn feeding and tension control units for weaving looms to the majority of weaving machine manufacturers. It also retrofits its latest technologies to working mills to enable instant benefits in terms of productivity and control.
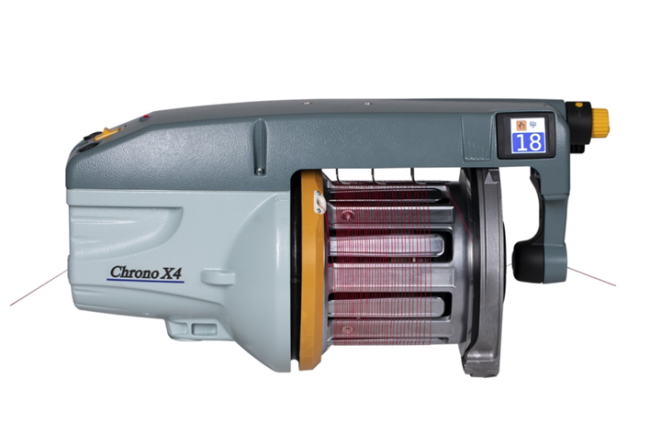
Vandewiele Sweden’s latest X4 yarn feeders provide instant benefits in terms of productivity and control. The company will present its latest X4 yarn feeders
The company will present its latest X4 yarn feeders with integrated accessory displays (TED) as a new standard, as well as launching its own e-commerce platform – iroonline.com.
The TED function enables weft tension settings to be transferred from one machine to another, enabling a fast start-up the next time the same article is woven. The position of the S-Flex Tensioner is constantly monitored by an internal sensor – even if adjustment is made during power off.
X4 feeders are also available with integrated active tension control (ATC-W) as an option. With the ATC-W active tension control, the required tension is easily set and monitored on the integrated display. Once set, the system constantly regulates itself, ensuring consistent yarn tension during the weaving process which is constantly and accurately measured by the ATC sensor unit, sending a signal to the ATC operator unit resulting in consistently stable yarn tension at the required level.
Supply chain infrastructure
“It is now essential for companies at all stages of the manufacturing supply chain to improve their infrastructures since upcoming legal regulations – such as the EU strategy for sustainable and circular textiles and the associated digital product passport – will require a corresponding level of digitalisation,” says Premler-Andersson in conclusion. “At the same time, digitalisation is helping manufacturers to meet the sustainability requirements of customers and partners by, for example, improving supply chain transparency and resource calculation. We look forward to discussing the digital solutions offered by TMAS members at the Techtextil and Texprocess shows.”