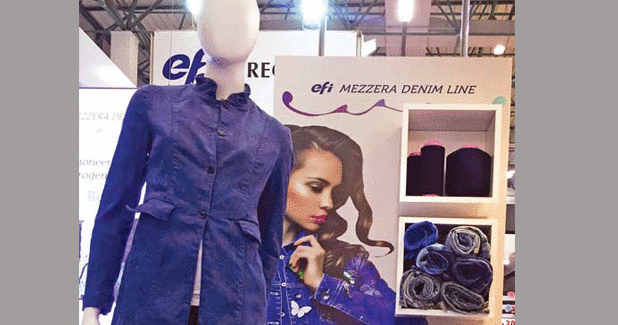
Sustainable fibres for textiles and apparels
In ecology, sustainability (from sustain and ability) is the property of biological systems to remain diverse and productive indefinitely. Long-lived and healthy wetlands and forests are examples of sustainable biological systems.
Cotton is the most common natural fibre used to make clothing, accounting for about 33% of all fibres found in textiles, say Rajanna L Gotipamul, Vaghela Sneha Ishwar and Vivek Chilveri.
In ecology, sustainability (from sustain and ability) is the property of biological systems to remain diverse and productive indefinitely. Long-lived and healthy wetlands and forests are examples of sustainable biological systems. In more general terms, sustainability is the endurance of systems and processes. The organising principle for sustainability is sustainable development, which includes the four interconnected domains: ecology, economics, politics and culture. Sustainability science is the study of sustainable development and environmental science.
The principle of the three pillars of sustainability says that for complete sustainability problem to be solved all three pillars of sustainability must be sustainable. The three pillars are social, environmental, and economic sustainability. Sustainability is the ability to continue a defined behavior indefinitely. For more practical detail the behavior you wish to continue indefinitely must be defined. For example:
- Environmental sustainability is the ability to maintain rates of renewable resource harvest, pollution creation, and non-renewable resource depletion that can be continued indefinitely.
- Economic sustainability is the ability to support a defined level of economic production indefinitely.
- Social sustainability is the ability of a social system, such as a country, to function at a defined level of social well being indefinitely.
Sustainability can also be defined as a socio-ecological process characterised by the pursuit of a common ideal. An ideal is by definition unattainable in a given time and space. However, by persistently and dynamically approaching it, the process results in a sustainable system. Healthy ecosystems and environments are necessary to the survival of humans and other organisms. Ways of reducing negative human impact are environmentally-friendly chemical engineering, environmental resources management and environmental protection. Information is gained from green computing, green chemistry, earth science, environmental science and conservation biology. Ecological economics studies the fields of academic research that aim to address human economies and natural ecosystems.
Moving towards sustainability is also a social challenge that entails international and national law, urban planning and transport, local and individual lifestyles and ethical consumerism. Ways of living more sustainably can take many forms from re-organising living conditions (e.g., eco-villages, eco-municipalities and sustainable cities), reappraising economic sectors (permaculture, green building, sustainable agriculture), or work practices (sustainable architecture), using science to develop new technologies (green technologies, renewable energy and sustainable fission and fusion power), or designing systems in a flexible and reversible manner, and adjusting individual lifestyles that conserve natural resources.
The term sustainability should be viewed as humanity?s target goal of human-ecosystem equilibrium (homeostasis), while sustainable development refers to the holistic approach and temporal processes that lead us to the end point of sustainability. Despite the increased popularity of the use of the term sustainability, the possibility that human societies will achieve environmental sustainability has been, and continues to be, questioned?in light of environmental degradation, climate change, overconsumption, population growth and societies? pursuit of unlimited economic growth in a closed system.
Increased production and consumption
Fast fashion uses innovative production and distribution models to dramatically shorten fashion cycles, sometimes getting a garment from the designer to the customer in a matter of a week instead of months. The number of fashion seasons has increased from two a year ? spring/summer and fall/winter ? to as many as 50-100 micro seasons. Fast-changing trends and low prices have allowed people to consume more. The average consumer is now purchasing 60 per cent more items of clothing compared to 2000, but each garment is kept half as long.
Water stress and pollution
Cotton is the most common natural fibre used to make clothing, accounting for about 33 per cent of all fibres found in textiles. Cotton is also a very thirsty crop, requiring 2,700 liters of water ? what one person drinks in two-and-a-half years ? to make one cotton shirt. In areas already facing water stress, cotton production can be particularly damaging. In Central Asia, for instance, the Aral Sea has nearly disappeared because cotton farmers draw excessively from the Amu Darya and Syr Darya rivers. Cotton farming is also responsible for 24 per cent of insecticides and 11 per cent of pesticides despite using about 3 percent of the world?s arable land. Water use and pollution also take place during clothing production. About 20 per cent of industrial water pollution is due to garment manufacturing, while the world uses 5 trillion liters of water each year for fabric dyeing alone, enough to fill two million Olympic-sized swimming pools.
Climate change
The carbon footprint of a garment largely depends on the material. While synthetic fibres like polyester have less impact on water and land than grown materials like cotton, they emit more greenhouse gasses per kilogram. A polyester shirt has more than double the carbon footprint of a cotton shirt (5.5 kg vs. 2.1 kg, or 12.1 pounds vs 4.6 pounds). Polyester production for textiles released about 706 billion kg (1.5 trillion pounds) of greenhouse gases in 2015, the equivalent of 185 coal-fired power plants? annual emissions.
What?s apparel?s future?
Apparel spending is projected to grow tremendously. This is particularly true in Asia, as hundreds of millions of people in China and India enter the global middle class. By 2030, there will be 5.4 billion people in the global middle class, up from 3 billion in 2015. We can expect increased demand for clothes and other goods that define middle-income lifestyles. If consumption continues at its current rate, we?ll need three times as many natural resources by the year 2050 compared to what we used in 2000. Assuming infinite resources in a finite world is not a sustainable business model. Beyond environmental concerns, unchecked consumption will undermine the world?s economic and social goals. Some apparel companies will ignore those signals and continue with traditional take-make-waste business models. Others will embrace innovative new models that work within planetary boundaries and are a better fit for tomorrow?s markets.
What to do?
Apparel is just one sector competing for natural resources, but it?s important that clothing makers start transforming their business models now given the industry?s strong growth trajectory. Many companies are aware of the environmental risks and are ready to act. The first step is for companies to measure their environmental impacts and understand areas where they can improve. The Sustainable Apparel Coalition?s Higg Index lets companies measure the environmental, social and labor impacts of their products and services, and work is being done on Science Based Targets guidance for the apparel industry.
Sustainability in textiles
Sustainable fashion, also called eco fashion, is a part of the growing design philosophy and trend of sustainability, the goal of which is to create a system which can be supported indefinitely in terms of human impact on the environment and social responsibility.
Sustainable clothing refers to fabrics derived from eco-friendly resources, such as sustainably grown fibre crops or recycled materials. It also refers to how these fabrics are made. Historically, being environmentally conscious towards clothing meant buying clothes from thrift stores or any shops that sell second-hand clothing, or donating used clothes to shops previously mentioned, for reuse or resale. In modern times, with a prominent trend towards sustainability and being ?green?, sustainable clothing has expanded towards reducing the amount of clothing discarded to landfills, and decreasing the environmental impact of agro-chemicals in producing conventional fibre crops (e.g. cotton).
Under the accordance of sustainability, recycled clothing upholds the principle of the Three R?s of the environment: reduce, recycle and reuse, as well as the Three Legs of Sustainability: Economics, Ecology and Social Equity.
Through the utilisation of recycled material for the manufacturing of clothing, this provides an additional realm of economic world profit. Sustainable clothing will provide a new market for additional job opportunities, continuous net flow of money in the economy, and the reduction of raw materials and virgin resources. Source reduction or reducing the use of raw materials and virgin resources can ultimately reduce carbon emissions during the manufacturing process as well as the resources and carbon emissions that are related to the transportation process. This also prevents the unsustainable usage of extracting materials from the Earth by making use of what has already been used (i.e. recycling).
Recycled clothing: In addition to promoting a sounder environment by producing newer clothing made with sustainable, innovative materials, clothing can also be donated to charities, sold into consignment shops, or recycled into other materials. These methods reduce the amount of landfill space occupied by discarded clothes. According to the United States Environmental Protection Agency?s 2008 Report on Municipal Solid Waste (MSW), Generation, Recycling, and Disposal in the United States defines clothing as non-durable ? generally lasts less than three years ? textiles. In 2008, approximately 8.78 millions of tons of textiles were generated, 1.45 millions of tonnes were recovered and saved from landfills resulting in a rate of almost 17 per cent. The EPA report also states that the amount of MSW being ?Discarded? is 54 per cent, ?Recovered? is 33 per cent, and ?Combusted with Energy recovery? is 13 per cent. Approximately two-thirds of clothing materials are sent to landfills, making it the fastest growing component of waste in the household waste stream. Within the last five years, textiles disposed of in landfill sites have risen from 7 per cent to 30 per cent.
According to an ABC News report, charities keep approximately 10 per cent of all the donated clothing received. These clothes tend to be good quality, fashionable, and high valued fabrics that can easily be sold in charities? thrift shops. Charities sell the other 90 per cent of the clothing donations to textile recycling firms.
Textile recycling firms process about 70 per cent of the donated clothing into industrial items such as rags or cleaning cloths. However, 20 to 25 per cent of the second-hand clothing is sold into an international market. Used jeans collected from America, for example, were sold to low-income customers in Africa for modest prices.
3D seamless knitting: 3D seamless knitting is a technology that allows an entire garment to be knit with no seams.
This production method is considered a sustainable practice due to its reduction in waste and labor. By only using the necessary materials, the producers will be more efficient in their manufacturing process. This production method is similar to seamless knitting, although traditional seamless knitting requires stitching to complete the garment while 3D seamless knitting creates the entire garment, eliminating additional work. The garments are designed using 3D software unlike traditional flat patterns. Shima Seiki and Stoll are currently the two primary manufacturers of the technology. The technology is produced through the use of solar energy and they are selling to brands like Max Mara.
Zero waste: Zero-waste design is a concept that, although has been prevalent for many years, is increasingly being integrated into production. Zero-waste design is can be used through multiple industries but is very applicable in developing patterns for garments. The concept of zero-waste pattern making is designing the pattern for a garment so that when the textile is cut, there is no extra fabric going to waste. This means the pattern pieces for a garment fit together like puzzle pieces in order to use the entire amount of fabric provided, creating no waste in this step of production.
Dyeing: Traditional methods of dyeing textiles are incredibly harmful towards the earth?s water supply, creating toxic chemicals that effect entire communities. An alternative to traditional water dyeing is scCO2 dyeing (super critical carbon dioxide). This process creates no waste by using 100 per cent of the dyes, reducing energy by 60 per cent with no auxiliary chemicals, and leaving a quarter of the physical footprint of traditional dyeing. Different names for this process are Drydye and colourdry. Another company called colourep has patented Airdye, a similar process that they claim uses 95 per cent less water and up to 86 per cent less energy than traditional dyeing methods.
Sustainable fibres
Alpaca wool: Alpaca wool is made from the fleece of the South American alpaca, although often softer than sheep?s wool and also hypoallergenic. Alpaca require no pesticides or antibiotic treatment when raised for wool, making their lustrous and durable fleece naturally organic.
Bamboo: Bamboo is a type of grass originating from eastern Asia that requires no fertilizers or pesticides and very little water for its rapid growth. The fabric made from bamboo fibre is silky in texture, has moisture wicking properties, and is very durable. Although current bamboo fabric manufacturing processes involve toxic chemicals, developments for harmless and environmentally-sound processes are underway.
Banana fibre (Abaca): The stalks of the banana plant contain long fibres that can be spun into silky threads most often used in rugs and other interior textiles. Banana fibre has been used in Asian cultures for centuries, where hand extracted, processed and spun banana yarn and fabric can still be found today in the form of tablecloths, curtains and kimonos.
Bysuss: Also known as sea silk, byssus cloth is made from the long micro-filaments secreted by a certain type of mollusk that at one time was widespread in the Mediterranean sea. The mollusk can grow up to 3 feet long and excretes a very fine fibre from one end. Although the production of byssus silk has mostly vanished, artisans on the Italian island of Sardinia are keeping the age-old art alive.
Cotton: Also known as vegetable wool, is a major source of apparel fibre. Celebrated for its excellent absorbency, durability, and intrinsic softness, cotton accounts for over 50 per cent of all clothing produced worldwide. This makes cotton the most widely used clothing fibre. However, growing and processing this particular fibre crop is largely unsustainable. For every pound of cotton harvested, a farmer uses up 1/3 lb of chemical, synthetic fertilizer. As a whole, the US cotton production makes up 25 per cent of all pesticides deployed in the United States. Worldwide, cotton takes up 2.4 per cent of all arable lands yet requires 16 per cent of the world?s pesticides.
Furthermore, the cotton hulls contain the most potent insecticide residues. They are often used as cattle feed, which means that consumers are purchasing meat containing a concentration of pesticides. The processing of cotton into usable fibres also adds to the burden on the environment. Manufacturers prefer cotton to be white so that cotton can easily be synthetically dyed to any shade of colour. Natural cotton is actual beige brown, and so during processing, manufacturers would add bleach and various other chemicals and heavy metal dyes to make cotton pure white. Formaldehyde resins would be added in as well to form easy care cotton fabric.
Bt cotton: To reduce the use of pesticides and other harmful chemicals, companies have produced genetically modified (GMO) cottons plants that are resistant to pest infestations. Among the GMO are cotton crops inserted with the Bt (Bacillus thuringiensis) gene. Bt cotton crops do not require insecticide applications. Bt cotton crops yield 5 per cent more cotton on average compared to traditional cotton crops. Bt crops also lower the price of cotton by 0.8 cents per pound. However, there are concerns regarding Bt technology, mainly that insects will eventually develop resistance to the Bt strain.
Cotton (organic): Organic cotton is grown without the use of any genetically modification to the crops, without the use of any fertilizers, pesticides, and other synthetic agro-chemicals harmful to the land. All cotton marketed as organic in the US is required to fulfill strict federal regulations regarding how the cotton is grown.
Coloured cotton (Naturally): Cotton is naturally grown in varieties of colours. Typically, cotton colour can come as mauve, red, yellow, and orange hues. The use of naturally coloured cotton has long been historically suppressed, mainly due to the industrial revolution. Back then, it was much cheaper to have uniformly white cotton as a raw source for mass-producing cloth and fabric items. Currently, modern markets have revived a trend in using naturally coloured cotton for its noted relevance in reducing harmful environmental impacts. On an additional note, naturally coloured cotton is already coloured, and thus do not require synthetic dyes during process. Furthermore, the colour of fabrics made from naturally coloured cotton does not become worn and fade away compared to synthetically dyed cotton fabrics.
Camel (Wool): Camel hair for the production of fabric is obtained from the Bactrian camel, which reside in the steppes of Central and Eastern Asia. Camel hair is harvested by hand, then graded according to the colour and fineness of the fibre, with about 30 per cent making up the finest, apparel grade fibre. Usually light tan in colour, (explaining the term for shade we call ?camel?) it is typically blended with other fibres for an extremely supple material with excellent drape and temperature regulating properties.
Cashmere: Cashmere is made from the soft hairs that grow on the belly of a Kashmir goat, which is native to the Himalayas. The scarcity and arduous harvesting process of this fibre makes it a luxury material, as do its extremely soft, well-insulating, lightweight and durable properties as a fabric.
Chitin fibre: Chitin fabrics are most often made of a blend of viscose and chitin, which is a substance found in the shells of crabs and other crustaceans. The use of chitin, which is biodegradable, creates an anti-bacterial and hypoallergenic fabric. Chitin for fabric production is most often obtained as a by-product of the food industry, meaning that the shellfish are not harmed solely for the purpose of fabric production.
Coir (Coconut fibre): Coir is obtained from the husk of a coconut, and is most often found in the form of floor mats, doormats, brushes, brooms and as furniture filling. The fibre is also used as a sturdy material for weaving baskets, bags and indoor or outdoor decorations.
Cork: Cork fibre is harvested from the cork oak tree and is currently made into a soft-shell active wear fabric that keeps the wearer warm and is extremely breathable and supple. Raw cork is harvested from FSC (Forest Stewardship Council) certified forests through a process that doesn?t actually involve cutting down any trees. The thick and rugged bark grows back naturally after harvest, causing no harm to the tree.
Corn fibre / Ingeo: A fibre processing company called Nature Works has developed corn fibre based plastics and textile materials under the product name Ingeo. The material is said to use 20-50 per cent less petroleum based resources than polyester, is compostable and can be grown and processed annually to yield high amounts of fibre. However, nearly 85 per cent of the corn fabric produced is made from GM corn, so looking for organic corn options is important.
Fish skin leather: Fish skin leather is produced from the waste of the food industry from the skins of non-endangered fish such as cod, salmon, carp, sturgeon, catfish, wolf fish and perch. Similar in strength to tough cowhide with the appearance of reptile skin, fish skin leather can be used for anything from handbags, belts, clothing, small accessories and shoes, to furniture and interior decoration.
Hemp: Hemp fabric is made from the inner fibres of the stalk of the hemp plant, which belongs to the bast fibre group. Hemp does not require any pesticides or toxic chemicals when cultivated, produces 2-3 times more fibre per acre than cotton, and the plant even fixes nutrients back into the soil. Hemp fabric is breathable, warm, moisture-wicking, anti-bacterial and easily blended with other natural fibres such as cotton and wool for a soft, durable textile.
In-vitro leather: In-vitro or test tube leather is made by manipulating an animal hide cell through a bioreactor, then 3D bio-printing a cell formation, and placing it once again in a bioreactor to create finished leather. In-vitro leather has no hair or tough outer skin, decreasing the amount of time, chemicals, and water required for tanning. An inherent difference when compared to making conventional leather is the complete lack of animal slaughter.
Jute: Jute is a bast fibre plant native to India that contains coarse fibres most often used for products such as coffee sacks , rope, mats and on the soles of shoes like espadrilles. Finer jute fibres are often woven with cotton to create a strong material used in apparel and home textiles.
Kapok: Kapok fibre is found inside the seedpods of the kapok tree in the form of silky fluff that surrounds the kapok seeds. Since kapok fibres are rather short and not very strong, they are difficult to spin on modern machines, but make a plush and light filling for home textiles, bedding, furniture and even flotation devices.
Kenaf: Kenaf is another bast fibre that was used by the Ancient Egyptian and Asians. Related to both hibiscus and cotton, kenaf can be grown in several places including the U.S., converting CO2, improving soil structure, fixing nutrients into the soil and requiring minimal amounts of water and no fertilizers. Kenaf is a superior option for garments, as its extremely long fibres make for very fine yarn when spun, after which it is often blended with cotton.
Linen (flax fibre): Linen is made from flax, another plant in the bast fibre group, and has been used as a textile since Ancient Mesopotamian times. Growing linen requires far less water than growing cotton, no chemical fertilizers, and it is one of the strongest plant fibres. The material takes dyes well, is highly absorbent and keeps the wearer cool, making it ideal for a range of textile uses from apparel to home textiles and canvas bags.
Lotus flower fabric: Lotus flower fabric is a material created from the stems of the Asian lotus flower through arduous processing and weaving by hand. The finished fabric is a cross between silk and linen in texture, and was historically used to make robes for high-ranking Buddhist monks. The unique and soft material is breathable, wrinkle-free, naturally stain-resistant, and waterproof due to its aquatic origin.
Merino wool: Merino wool is made from the fleece of Merino sheep, which are originally from Spain but now mainly bred in New Zealand and Australia. Merino wool is very soft, lightweight and regulates body temperature well, explaining its popularity in sportswear and performance base layers.
Milk fabric/QMilch: Fabric made from milk protein fibres is extracted from commercial milk that doesn?t meet hygiene standards. Produced entirely without chemicals, this fabric contains 18 beneficial amino acids are antibacterial, anti-ageing and are able to regulate blood circulation and body temperature.
Modal: Modal is a fabric made from the cellulose found in beech tree fibre. The production process of Modal involves very few chemicals and recycles most of the water and solvents used. The fabric dyes well, resists shrinkage and fading and is extremely soft.
Mohair: Mohair is made from the hair of the Angora goat, which has a lustrous and soft coat. Mohair goats are typically shorn twice a year, with no harm done to the animal. The finished material is very durable, takes dyes well, is very warm and has excellent insulating properties. Mohair is often blended with other fibres to add strength and warmth to a particular fabric.
Nettle fabric: Nettle fabric is made from the fibrous stem of stinging nettle plants, which produce a soft and lustrous fibre that was very popular in medieval times. Cultivating nettles for textiles is a much more sustainable alternative to cotton, as it is low-maintenance, requires minimal amounts of water and no pesticides, attracts copious amounts of wildlife and thrives even in the poorest of soil unsuitable for other crops, also fixing nutrients back into the soil it grows in.
Peacock feather fabric: Peacock feather fabric is made from the side strands of the tail or ?eye? feathers, which only the male peacocks have. Rural villagers in Western India gather the tail feathers, hand pluck the side strands, which are then twisted and knotted by hand to form a continuous thread. This process is followed by weaving silk, rayon and the peacock feathers into an iridescent material, taking 1 month to complete a standard nine yard roll of fabric. Time-consuming, laborious and requiring ample handcrafting skills, peacock feather fabric is rather costly and production is extremely limited.
Pineapple silk (Pina): Pineapple silk is made from the fibres of pineapple leaves, which are processed and woven entirely by hand. The resultant fabric is a glossy but slightly stiff, ivory-coloured material that is diaphanous, breathable, softer than hemp, better in quality than raw silk and has excellent cooling properties. The fibre takes natural dyes very well, and the glossy surface of the material eliminates the need for toxic treating agents since it acts as a protective layer for the fabric.
PLA fabric: PLA stands for polylactic acid fibre, which is derived from a plant sugar called dextrose obtained mostly from corn as well as sugar beets, wheat or sugar cane. Ingeo corn fibres are essentially PLA fibres, and so considered part of the plant-based synthetics fabric group.
Qiviut: Qiviut is the Inuit word for musk ox, whose warm and strong inner coat hairs are used to spin a silky and soft yarn. Qiviut is much warmer than wool and even softer than cashmere, but extremely rare since the oxen are never shorn, but rather their undercoat is gathered from objects the animals have brushed against each spring.
Ramie: Ramie is an age-old bast fibre plant used by the Ancient Egyptians to make cloth for wrapping mummies. Though very similar to linen, ramie produces a lustrous, silk-like material that is soft to the touch, eight times stronger than cotton, and even strengthens when wet. Industrially processed ramie is chemically intensive, but hand processed ramie is environmentally friendly.
Sisal fabric: Sisal is a type of agave plant that grows in the Caribbean, Africa and Asia. Sisal fibre is obtained from the leaves of the plant, and was traditionally spun and woven into ropes and twines. Finer sisal fibres are spun into yarn used mostly by the carpet industry, but also used for other home textiles.
Soy: Soy fabrics are derived from the hulls of soybeans?a manufacturing byproduct. Soy fabrics can be blended (i.e. 30 per cent) or made entirely out of soy fibres. Soy clothing is largely biodegradable, so it has a minimal impact on environment and landfills.
Although not as durable as cotton or hemp fabrics, soy clothing has a soft, elastic feel. Soy clothing is known as the vegetable cashmere for its light and silky sensation. Soy fabrics are moisture absorbent, anti-bacterial, and UV resistant. However, soy fabrics fell out of public knowledge during World War II, when rayon, nylon, and cotton sales rose sharply.
Spider silk: Spider silk is made from the silk spun by golden orb spiders and only one piece of cloth made from this fibre exists in the world today. However, scientists are developing methods for replicating spider silk, which is lustrous in appearance, soft, extremely elastic and has incredible tensile strength.
Seacell: Seacell is a cellulose-based material that is made up of the fibre from eucalyptus trees blended with sushi grade, USDA certified organic, ?knotted wrack? seaweed. With a fibre structure that facilitates active exchange of nutrients between the skin and fabric, Seacell releases nutrients such as calcium, magnesium, iron and vitamin E (which is extremely beneficial for repairing stretched or damaged skin) onto the wearer. The fabric is very soft, breathes well and is produced through mostly sustainable processes.
Silk: Silk is made from the cocoons of silkworms, which are often killed in order to obtain the silk of their cocoon. This ancient method of fibre production began in China more than 3,500 years ago, and renders a fabric that is lustrous, manages moisture and is completely natural.
Wild / peace silk: Raw silk is different from conventional silk since the silkworm is allowed to live out its full life cycle. The moths are allowed to emerge from their cocoon before the cocoon is harvested for silk production, which requires gathering cocoons from the wild that moths have naturally left behind. The resulting fabric is not inferior to conventional silk, but the lives of the silkworms are spared.
Tencel / Lyocell: Tencell is a biosynthetic fibre made from the cellulose-rich pulp of rapid