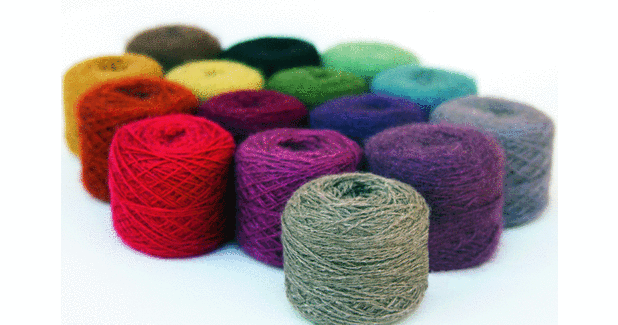
Study of regenerated cellulosic fibres
The need for better quality goods has led to the modification of regenerated viscose fibres. The main focus of this paper is on the development of cotton and cellulosic-based viscose fabrics made from modified viscose yarns such as Excel and Modal with reference to 100 per cent cotton fabrics and their unique, investigated physical and mechanical properties.
The need for better quality goods has led to the modification of regenerated viscose fibres. The main focus of this paper is on the development of cotton and cellulosic-based viscose fabrics made from modified viscose yarns such as Excel and Modal with reference to 100 per cent cotton fabrics and their unique, investigated physical and mechanical properties.
A fibre manufactured by dissolving cellulose and then restoring or regenerating the material through extrusion and precipitation cellulose is commonly regenerated to form rayon. Regenerated nitrocellulose cellulosic fibre was first manufactured by George Audemars in 1855. These fibres are soft and strong but highly flammable. Later Hilairedechandrannet perfected production of nitrocellulose fibre, but manufacturing of these fibres were relatively uneconomical. In 1890, LHD invented the cuprammonium process. Where cuprammonium solution was used to solubilise cellulose, this method is still used today for production of artificial silk. In 1891, it was discovered that treatment of cellulose with alkali and carbon disulfide generated a soluble cellulose derivative known as viscose. Modal is wood pulp-based cellulosic fibre, made out of pure wooden chips from the beech tree, having high tenacity and high wet modulus. Modal was first developed by Austria-based Lenzing AG which trademarked the fibre name. Excel is a third-generation cellulosic fibre, made from highly-refined eco-friendly process developed by the Birla Research Institute. It combines comfort and luxury of a natural fibre with engineered precision of a man-made fibre. Excel comes with a unique set of properties like high strength and dimensional stability.
Tencel is a brand name for a fibre, which is also called Lyocell, manufactured by Lenzing AG. Technically, a fabric must contain at least 30 per cent of these proprietary fibres in order to use the name Tencel, but the term has become more commonly used than Lyocell for similar products from all sources. Apparel made from the regenerated cellulosic fibres is soft and comfortable. It drapes well, which is one of the reasons it is so desirable as an apparel fabrics. Thus these fibres popularly used for making blouses, dresses, saris, sportswear, slacks, sport shirts, etc.
Rayon is the most absorbent of all cellulose fibres, even more so than cotton and linen. Because of this, rayon absorbs perspiration and allows it to evaporate away from the skin, making it an excellent summer fabric which is also used in the production of disposable medical devices as well as fabrication of artificial membranes. It is used for apparel, ladies stocking and better quality fabrics. Rayon can have finer denier resulting in higher pliability and very good draping qualities. It is also a major feedstock in the production of carbon fibre. The rayon manifold hand opened a field of research and application. Further development of these fibre will surely direct to some surprising properties and facts. After more than 100 years of viscose fibre, there is still more room for development.
Manufacturing process of viscose rayon
Steeping: Cellulose pulp is immersed in 17-20 per cent aqueous sodium hydroxide (NaoH) at a temperature in the range of 18 to 25 degree Celsius in order to swell the cellulose fibre and to convert cellulose to alkali cellulose. Pressing: The swollen alkali cellulose mass is pressed to a wet weight equivalent of 2.5 to 3.0 times the original pulp weight to obtain and accurate ratio of alkali to cellulose.
Shredding: The pressed alkali cellulose is shredded mechanically to yield finely divided, fluffy particles called as crumbs. This step provides increased surface area of alkali cellulose, there increasing its ability to react in the steps that follow.
Aging: The alkali cellulose is aged under controlled condition of time temperature, in order to depolymerisation. In this step, average molecular weight of the original pulp is reduced by a factor of two to three reduction of the cellulose is done to get ‘A’ viscose solution of right viscosity and cellulose concentration.
Xanthation: In this step, the aged alkali cellulose crumbs are placed in vats and allowed to react with carbon disulphide under controlled temperature to from cellulose xanthate.
Dissolving: The yellow crumb is dissolved in aqueous caustic solution. The large xanthate substituent on the cellulose forces the chains apart from reducing the inter-chain hydrogen bonds and allowing water molecules to solve and separate the chains leading to solution of the otherwise in soluble cellulose because of the blocks of un-xan that end cellulose in the crystalline regions, the yellow crumbs are not completely soluble at these stage. Because the cellulose xanthate solution has a very high viscosity, it is termed as viscose.
Ripening: The viscose is allowed to stand for a period of time to ripen. Two important processes occur during ripening — Redistribution and loss of xanthine groups. The reversible xhantation reaction allows some of the xanthine groups to revert to cellulosic hydroxyl and free Cs. This free Cs2 can then escape or react with order hydroxyl on other portion of the cellulose chain.
Filtering: The viscose is filtered to remove undissolved materials that might disturb the spinning process or cause defect in the rayon filament.
Degassing: Bubbles of air entrapped in the viscose must be removed prior to extrusion or they would cause voids, or weak spot in the fine rayon filament.
Wet spinning: Production of viscose rayon filament: The viscose solution is metered through a spinneret into a spin bath containing sulphuric acid, sodium sulphate to import a high salt content to the bath which is useful in rapid coagulation of viscose.
Drawing: The rayon filaments are stretched while the cellulose chains are still relatively mobile. This causes the chains to stretch out and orient along the fibre axis. As the chains become more parallel, inter-chain hydrogen bonds form, giving the filaments the properties necessary for use as textile fibre.
Washing: The freshly regenerated rayon contains many salts and other water soluble impurities which need to be removed. Several techniques may be used.
Cutting: If the rayon is to be used as staple the group of filaments (termed low) is passed through a rotary cutter to provide a fire which can be proceed in the same way cotton.
Properties of regenerated cellulosic fibre
Viscose rayon fibres have thickness of 1.7 to 5.0 dtex, and particularly those between 1.7 and 3.3 dtex dominate large scale production. Tenacity ranges between 2.0 to 2.6 g/den when dry and 1.0 to 1.5 g/den when wet. Elongation – at break varies from 10 to 30 per cent dry and 15 to 40 per cent wet. Thermal properties include: Viscose rayon loses strength above 149 degree Celsius. Chemical properties include: Hot dilute acids attack rayon. Whereas bases do not seem to significantly attack rayon.
The tensile strength of Modal fabric both in warp and weft direction and crease recovery angle are very good in comparison with cotton fabric. Whereas the stiffness (warp and weft) and mean drape co-efficient are less in Modal fabrics over that of cotton fabrics. The hairiness of 100 per cent cotton yarn is the lowest, 100 per cent Tencel. The air permeability reduces with the increase of fibre fineness. Therefore air permeability for 100 per cent micro Modal fabric is lower than 100 per cent Modal fabrics. Having the coarse fibre water vapour permeability is the ability of the fabric to transfer the perspiration in the form of moisture vapour. The higher hairiness level of cotton yarn makes air pockets inside the fabric, which decreases the thermal conductivity of these fabric.
Plan of work
Based on the review of various literatures related to regenerated fibres, the foregoing plan of research work was prepared, the details of which are as follows:
Materials: In this project, mainly along with cotton three types yarns of regenerated fibres were used having count range of 40s Ne. i.e., viscose rayon, Modal fibre, Excel fibre.
Method: Produced woven fabrics using 40s Ne cotton as warp and 40s Ne weft of three regenerated cellulosic fibres along with cotton maintaining EPI 52 and PPI 44.
Testing
Single yarn strength: These tests are used to determine the breaking force, elongation and toughness properties of yarn. Breaking tenacity, a ratio of the breaking force to yarn linear density is also a common property for evaluating the strength of a yarn material and for comparison and validation purposes.
Lea strength and CSP: A lea strength tester measures the strength of one lea yarn. One lea means 120 yards. Strength is a measure of the steady force necessary to break a material and is measured in pound. The machine works in constant rate of extension, assuming the specimen to be extensible and an absence of any dynamic effects.
Fabric tensile strength: This instrument works on the pendulum lever principle with constant rate of traverse. In this testing the following values were calculated:
Tearing strength: To estimate the force required to continue a tear in the specimen of fabric. Tear strength test: force required to propagate an existing tear is measured as a part of the preparation of fabric specimen, a cut is in them and the force is required to extend the cut is measured. In this testing is to be calculated. Average warp way tearing strength and weft way tearing strength.
Abrasion tester: Abrasion is just one aspect of wear and is the rubbing away of the component fibres and yarns of the fabric. Principle of abrasion testing is to determine the fabrics properties in regard to wear resistance. Abrasion to the fabric is a tester of the Martindale type.
Stiffness: The principle employed is to measure a particular length of the fabric specimen of specified dimensions which when used as a cantilever bends to a constant angle under its own weight. In this testing, calculating average bending length in both ways, i.e warp way & weft way is measured.
Air permeability: In this testing, air permeability of fabric is found out in Cm3/cm2/sec.
Wicking test: In wicking test, water raised due to capillary action is noted down in both warp way and weft way – in centimeter per unit time.
Results and discussion
The experimentation of this work was conducted as per the plan of work. The regenerated cellulosic fibres were tested for – CSP, tensile strength, single yarn strength, tearing strength, stiffness, abrasion resistance, air permeability and wicking test.
Single yarn strength/tenacity: As per the ASTM D2256-02 standards, single yarn strength/tenacity results were tested. It prescribed a method for determination of breaking load, elongation at break and tenacity of yarn. Pendulum lever principle with constant rate of traverse (CRT) and CRE with tensolab strain gauge principle. The single yarn strength/tenacity of all the three regenerated cellulosic fibre yarns along with the cotton yarn. The Excel yarn has an excellent elongation% compared cotton yarn. Modal yarn has a good elongation% than viscose yarn.
Lea strength and CSP: As per the ASTM D1578-93 IS1671:1977 standards, lea strength and CSP were performed. A lea strength tester measures the strength of one lea yarn. One lea means 120 yards. Strength is a measure of the steady force necessary to break a material, which is measured in pound. This works in constant rate of extension by pendulum lever principle by constant rate of traverse. The lea strength and CSP respectively of all the three regenerated cellulosic fibre yarns along with the cotton yarn. Both lea strength and CSP of Tencel is excellent as compared to the other fibres.
Tear test: As per the ASTM D 2261-96 standards, tearing strength of fabric was performed. A rectangular specimen cut in the centre of a short edged to form a two-tongued specimen, in which one tongue of the specimen is gripped in upper jaw and the other tongue is gripped in the lower jaw of a tensile testing machine. The separation of the jaw is continuously increased to apply force to propagate the tear. At the same time, the force developed is recorded. The force to continuous the is calculated from autographic chart recorders or microprocessors data collection system.
The tear strength of all the three regenerated cellulosic fibre yarns along with the cotton yarn. The tensile strength of excel fabric in weft way direction is more and warp way strength of cotton is more.
Stiffness: As per the ASTM D 1388-96 standards, stiffness test for fabric. A specimen is slid at a specified rate in a direction parallel to its long dimension, until its leading edge projects from the edge of a horizontal surface. The length of the overhanging is measured when the tip of the specimen is depressed under its own mass to the point where the line joining the top to the edge of platforms makes a 0.924 rad (41.5o) angle with the horizontal. from this measured length the bending length and flexural rigidity are calculated.
The stiffness property of all the three regenerated cellulosic fibre yarns along with the cotton yarn from the figure we can see that viscose fabric having is having higher warp way bending length and cotton and excel is having similar weft way bending length.
Tensile strength: As per the ASTM D 1682 standards, tensile strength of fabric. The test process involves placing the test specimen in the testing machine and slowly extending it until it fractures. During this process, the elongation of the gauge section is recorded against the applied force. The data is manipulated so that it is not specific to the geometry of the test sample.
The elongation measurement is used to calculate the engineering strain.The tensile strength of all the three regenerated cellulosic fibre yarns along with the cotton yarn from the figure we can see that viscose, excel and modal with cotton shows maximum extension and tensile strain as compared 100 per cent pure cotton fabric. Abrasion: As per the ASTM D4966-98 standards, abrasion resistance of fabric. Abrasion is just one aspect of wear and is the rubbing away of the component fibres and yarns of the fabric. It is series of repeated applications of stress, there for capacity of absorb punishment is required to the fibres. Inherent fibre properties such as work of rupture may give a high resistance to abrasion.
Air permeability test: As per the ASTM D 737-96 standards, air permeability test of fabric. The rate of air flow passing perpendicularly through a known area of fabric is adjusted to obtain a prescribed air pressure differential between the two fabric surfaces. From this rate of air flow, the air permeability of fabric is determined.
Air permeability modal/cotton fabric is very low air permeable because the number indicates high thickness value of modal/cotton fabric. Excel fabric having more permeability due to their round in cross section. Thus at the fabric stage Excel show more uniform nature and easily air entrap and pass through their gaps. Furthermore, cotton convolutions are ribbonlike twists that characterise cotton.
Wicking test: To perform standard wicking test of a fabric was suspend vertically so that bottom is just touching water surface. Measure the distance travelled by the water during a set period of time. Measuring performance in both warp and weft direction.
The wicking behaviour of yarns for the different time. From the results we can say, that there is an increase in wicking height of viscose yarn because present of highly crystalline region. Thus flow of water more rapidly with less absorbency through its outer surfaces which ultimately causes the increase in capillary pressure.
Conclusion
Tensile properties of yarn: The findings show that the cotton having lower value of tensile strain andtenacity while regenerated cellulosic fibre yarn has higher value. this is due to the regenerated fibre yarn contains a high degree of crystallinity and orientation, as well as a high average molecular mass and the degree of polymerization. Tear test/tensile properties of fabric: The tear strength and tensile properties of Excel fabric in weft way direction is more and warp way strength of cotton is more. Viscose, Excel and Modal are having a maximum extension and tensile strain as compared 100 per cent pure cotton fabric. This is because modified regenerated yarns are having high molecular mass, thus achieving high tenacity and elongation. Also in comparison with Modal and Excel, viscose fibres have highest orientation factor and crystalline region one of the reasons for that being the difference between fibre spinning solution.
Stiffness: From stiffness testing the authors conclude that viscose fabric have higher warp way bending length and cotton and Modals have similar weft way bending length. Excel fibre has a smoother and suppler surface than cotton. This is because cotton has irregular and rough surface.
Abrasion resistance: According to the analysis, there is a significant relationship between the fibre type and the fabric abrasion resistance. It is observed that 100 per cent cotton fabrics have a higher weight loss than other fabrics, which indicates the relationship between weight loss percentage and yarn type. This is due to the highest tensile strength of modified viscose fibre against cotton, which makes it more durable during abrasion test. The modified viscose fibres have merits of smoothness and softness against cotton fibre.
Air permeability: Air permeability of modified cellulosic fabrics. It can be seen that Modal fabric is having very low air permeablility because the number indicates high thickness value of Modal. Excel fabrics have more permeability due to their round in-cross section. Thus at the fabric stage Excel shows more uniform nature and easily air entrap and pass through their gaps. Whereas cotton is having low air permeability because when cotton fibre matures, lumen dries out and collapses which makes secondary wall start to twist. These fibre convolutions besides extra cotton yarn hairiness enhance the air resistance of the cotton fabric.
Kicking test: From the results of wicking test, we can say that there is an increase in wicking height of regenerated cellulosic fibres when compared with cotton because of presence of highly crystalline region. Thus, water flows more rapidly with less absorbency through its outer surfaces, which ultimately cause an increase in capillary pressure.
References
Research Coventry (UK) LenzingerBerichte, June 1985.
The article is authored by Prof Sunil A Pardeshi, Omkar Sadalkar and Rohit Shinde, who are with the Department of Textile Technology, D.K.T.E’s Textile and Engineering Institute, Ichaklkaranji, Maharashtra.