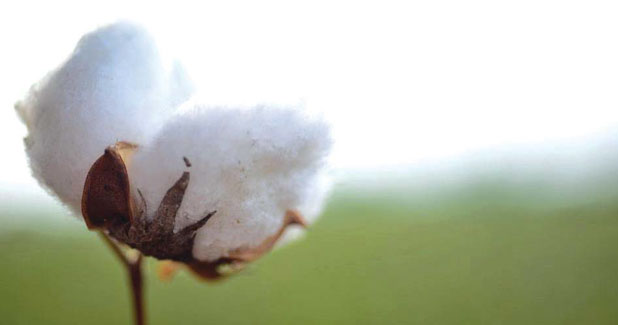
Stickiness in cotton
Stickiness in cotton is one of the major trouble shooting problems in the mills and ginning units. Stickiness leads to choke ups in ginning and loss in production is up to 10-15 per cent.
Stickiness leads to choke-ups in ginning and loss in production is up to 10-15 per cent, reveals N Balasubramanian..
Stickiness in cotton is one of the major trouble shooting problems in the mills and ginning units. Stickiness leads to choke ups in ginning and loss in production is up to 10-15 per cent. Stickiness results in web falling in carding, cylinder loading, scraper blade accumulations, partial or complete roller lapping at draw frame, speed frame and ring frame leads to considerable loss in production, uneven quality and rejections. It also results in increased maintenance by way of frequent cot buffing, application of antilap solution, acid treatment, berkolisation and cot replacement and increased idle spindles leading to lower production is also encountered.
There are several factors contributing to stickiness.
Major ones are:
- Honey dew contamination
- High sugar content from plant nectaries
- Low maturity
- High wax content
- Oily contaminants
Honey dew contamination: Honey dew contamination comes from sugar containing sap secreted by insects like aphid and white fly during growth. Secreted material finds its way to boll. However, Bourley opined that sugar associated with stickiness is melicitose and even a field free from aphid and white fly can produce sticky cottons. Miller et al; found that type of sugar also affects degree of stickiness. Sucrose, melezitose and trehalulose cause more stickiness than turanose, palatinose, and sucrose. Melezitose, raffinose, glucose or fructose contamination. Fibre contaminated with trehalulose is stickier than fibre with an equivalent amount of melezitose. Mixture of sugars which occur in honey dew is more stickier than single sugars. Localised concentrated sugars as in honey dew cause more stickiness than evenly dispersed sugars. Gamble found concentrations of melezitose and trehalulose on the surface of the cotton infected with honeydew decrease exponentially as a result of thermo chemical reactions. The concentration of trehaluose on cotton surface can be reduced substantially by controlled heat and time. Sampling is very important in estimating contamination. Large within sampling variation is found as contamination by insect is in localised portion.
Preventive measures in cultivation: Honey dew contamination is more in frost free conditions with lot of sunshine warm temperature and low humidity. Reducing insect production problem is one of those helpful to prevent contamination. Limiting cotton cultivation to single fruit cycle, harvesting on time and destruction of crops infested with honey dew are some useful measures. Application of selective insecticides may also help to reduce honey dew but there is risk of insecticides becoming resistant to such insecticides on frequent application. Use of mature cotton seeds will reduce sugar. Use of boll opening chemicals will help if immature bolls are high in number. Rainfall will help to wash out the sugars. Spraying enzymes on the plant will reduce sugar as microorganisms eat up sugar. Overhead and in- canopy irrigation have been tried at some places to reduce sugar. Covering cultivation area with film with ultraviolet radiation filters reduces contamination with insects like white fly. Bushiness large leaf area increases stickiness. Optimum planting density, irrigation, open canopy, optimum fertilisers will also help.
Testing for honey dew: Potassium ferricyanide test also known as Perkins test is one of the common methods originally proposed for determining sugar content. Perkins test determines the amount of reducing material in the water extract of cotton by comparing the reducing ability of these extracts with that of glucose used as standard. About 5 grams of purified cotton is immersed in distilled water with addition of sufficient potassium ferricyanide. The solution is boiled for three minutes and colour of solution assessed from which presence of reducing sugars is estimated. This method can be used primarily for screening cottons having sticky sugars and those free from it. Around 0.2 per cent sugar is considered non sticky >0.3 per cent is regarded as highly sticky. But it is not efficient to detect finer differences in sticky sugars in cotton. It is also insensitive to sucrose and melezitose, which also contribute to stickiness as this test determines only reducing sugars and not non reducing sugars. The latter also contribute to stickiness. Brushwood suggested that some of the non reducing sugars can be converted to reducing sugars by adding a mild 0.2 per cent M sulphuric acid before potassium ferricyanide test. Correlation between sugar content by this test and sticky cotton thermo detector test improved by 20 per cent in the case cottons infested with aphid honey dew.
Benedicts test: One gram of opened cotton is wetted with 40 litre of boiled water in a test tube. After heating for 15 minutes, 1 millilitres of Benedicts solution (made up of 100 gram of anhydrous sodium carbonate, 173 gram of sodium citrate and 17.3 gram of copper (II) sulphate pentahydrate is added to 15 millilitres of this solution. The colour taken by the solution indicates extent of honey dew.
Ultraviolet test: Honey dew contaminated cotton gives reddish fluorescence of low intensity when examined under ultraviolet light. The test is not conclusive as similar fluresence by cotton seed hulls, leaf particles and insects is seen in cotton.
High performance liquid chromatography (HPCL): The sugar is extracted from cotton by water. Through the use of an eluant the sugar is separated on the basis of molecular weight and steric arrangement. The individual sugars are indicated by HPCL profile. The main advantage of this method is it can measure both reducing and non-reducing sugars and also source of contamination (white fly or aphid or plant). The test however is time consuming, expensive and does not provide information on distribution of infecting sugar deposits on cotton. Refined gas chromatography test for the water-surfactant soluble components and or natural contaminants on cotton have been developed. This makes test more quantitative. The studies with this method showed that stickiness is directly related to reducing sugar concentration. Field weathering and bacterial and fungal attack lower malic acid content and result in significant amount of arabitol and mannitol.
High resolution near infrared spectroscopy: High resolution NR Infrared spectroscopy can be used to determine the intensity of stickiness. About 15 gram of cotton is placed and pressure applied on it, Spectra are taken. Tests are taken three to four times rearranging samples and average spectra taken. Barton et al found 4 cm-1 resolution gives best results for stickiness. A large number of samples have to be tested to get accurate results. A model has been developed which distinguishes cottons by Barton et al; for checking stickiness intensity.
Ghosh and Roy developed a 4 wavelength regression model with near infra spectroscopy for correlating the results with sugar content.
Abidi and Hequet found a good correlation between FTIR spectra of rotor yarn defects from cottons contaminated with whitefly honey dew and the spectra of white fly contaminated cotton. However no such correlation is found in the case aphid contaminated honeydew cotton. Water absorption of trehalulose sugar has a marginal effect on on the intensities of vibration mode of trehalulose. The results indicate that amongst sugars trehalulose sugar is the main cause for yarn defects.
Sticky Cotton Termodetector: This is a hand-held device developed by CIRAD for assessing stickiness in cotton by thermo detection. Heat and pressure applied on cotton web placed between aluminium foils and sticky points are counted. The results are subjective. CIRAD has developed an improved machine capable of measuring stickiness far more rapidly than the SCT thermodetector, recommended by the international textile manufacturers or ITMF. This is the H2SD (high speed stickiness detector, manufactured in partnership with SYDEL SA, Montpellier (France).
A sample of cotton is opened by rotor to form a sheet. The sheet is them pressed by 2 aluminium foils successfully at four places at a temperature of 540 Centigrade in one of the plates. and number of sticky points is determined by Image analyser. Four samples are tested and average taken. The test is rapid and takes only 30 seconds. Operator involvement is limited to preparing the wad of cotton. The plates are automatically cleaned after each sample. Time taken for a sample is only 30 seconds correlation found between SCT and hot press method is not good. However some cottons give stickiness at elevated temperature but have no stickiness at 270 C leading to false results.
Sticky deposits from aluminium foil trehalulose is the main cause for stickiness with cottons contaminated with white fly. Unidentified compounds are responsible for stickiness in cottons contaminated with aphid. In correlation between thermodevices like SCT, Fixotest, iron, hot press are not good.
Hequet and Abidi have developed a method where cotton is tested at 2 temp viz; 240 and 540 C. Trehalulose deposits are determined at lower temp and non trehalulose-rich honeydew droplets and physiological sugars are determined at higher temp.
Mini card test: The number of sticky points in the stainless steel calendar roller or delivery roller as web passes through them in a mini card (such as one used in Shirley Miniature Plant) is used to estimate stickiness. Other factors taken into consideration while grading cotton for stickiness are time taken for stickiness, number of disturbances in passage of web and intensity of stickiness. Grading is done as no stickiness, light stickiness, moderate stickiness and high stickiness. The processing is done at 55 per cent RH. Water content has a strong positive effect on stickiness while temperature has a negative effect. The effect of relative humidity on stickiness is greater with cottons having high sticking tendency. This is a highly subjective method, accuracy affected by frequency of cleaning of calendar rollers and can be used only for broadly screening cottons as sticky and non sticky. Cottons with plant sugar evenly distributed in the cotton may not produce sticky points in this test. Further the test is slow and its reproducibility is not good.
Fibre Contamination Tester (FCT): Web prepared from Minicard is passed through a pair of crush rollers. The crush rollers are getting heated because of brushes rubbing against them and this causes honeydew to stick. Sticky points are counted by laser beam and computer software. Limitation of this method is it gets contaminated soon and requires frequent cleaning. Out of the various test methods FCT and H2SD have potential for estimating stickiness with reasonable accuracy, if adequate number of samples are tested. Within sample variability is higher and operational efficiency is lower with FCT.
International Committee on cotton testing methods has taken an imitative to standardise test method for testing cotton stickiness. The first step is to create a method for preparing a homogenous samples of sticky cottons. The second step is to conduct stickiness tests on this cotton with various mechanical instruments in different laboratories…The third step is to determine the agreement between results on the same instrument by different laboratories. Also the correlation between different instruments will be studied. Based on this the instrument that gives most reproducible results will be found.
Colorimetric method: Shams-Nateri and Mohajerani16 proposed a method for estimating honey dew. It consists of caramelising cotton by heating which changes the colour of honey dew from pale/colourless to yellow and brown. The yellow index of cotton by Nickerson Hunter colorimeter is used to quantify honeydew. The cotton is divided into two parts. One part is washed to remove honey dew and heated to 1500 in Owen. The second part is not washed but heated to 1500. Yellow index of both samples were determined from which stickiness index was estimated.
Infra Red based Moisture tester: Infra Red based moisture tester was developed at US Cotton Ginning Laboratory at Stoneville, Mississippi. It consists of Infra red based moisture tester, resistance based moisture tester, compression system and a computer with special soft ware. The infra red based moisture measures insect sugar and normal sugar while resistance based moisture tester is only slightly affected by insect sugars. The system predicts accurately stickiness in 75 per cent cases and takes only 5 seconds. The system can also be used online to measure stickiness as cotton is being processed. If the difference between infrared based moisture and resistance based moisture is 0.8 per cent or more cotton is usually sticky. .If the difference between oven based moisture and infrared based moisture is 0.6 per cent and if the difference between infrared based moisture and resistance based moisture is 0.8 per cent or more then the cotton is not sticky though it contains high sugar content.
Accelerated Roller lapping test: Roller lapping on cots in ring frame is highly correlated with stickiness in cotton. So an accelerated roller lapping test can be used to predict stickiness levels. The test is best carried out on a miniature spinning plant like Shirley. Only about 50 to 100 grams of cotton are required and the test takes about 2-3 hours. The ends are broken and time taken for roller lapping to occur is noted for each spindle. The test is repeated 10 times and average time taken for roller lapping to occur is estimated. Time taken for roller lapping is highly correlated with sticking tendency and the test can be used to identify stickiness level in cotton at the time of purchase. The test has the merit that t simulates conditions actually present in mills.
Gamble examined if thermochemical production of volatile compounds produced by heating contaminated cottons can be used to assess stickiness. Heating of contaminated cotton led to degradation and produced 5-hydroxymethyl-2-furaldehyde (HMF) which is volatile. HMF was quantified by gas chromatography. Level of HMF production was found to be correlated with stickiness.
Immaturity: Immature fibres contain a good amount of sugars like glucose, fructose, sucrose and other sugars. These are plant based sugars. Mature cottons are fully dried and contain only traces of sugar. Immature cottons contain a good amount of sugar some of which is sticky.
Crushed seeds and fragments: Crushed seeds and seed fragments ooze oil in ginning and this leads to stickiness. Immature and small seed get caught between knife and roller or ribs in saws result in seed fragments, Improper gin settings and worn out knife and saw also result in seed coat fragments Ginning should be improved to minimise seed coat fragments.
Eltahir et al; employed Taguchi method for analysing the impact of mixing sticky cotton with non stcky cotton. They found optimum amount of sticky cottons to be mixed with non sticky cotton is 25 per cent. CV% of roving and quality of yarn are adversely affected by stickiness of cotton. Rotor yarn quality is not much affected by stickiness in cotton. This is in contradiction with te results of Abidi and Hequet who found rotor yarn defects are caused by sugar from white fly.
Oily contaminants: Contaminants like oil grease, stamp colour and tar among the contaminants found in cotton bale that result in stickiness. Grease and oil come from harvesting machinery and stamp colour from bale stamping.
Measures to overcome processing problems with sticky cottons
Microbial activity is helpful in consuming the sugars. Use of ammonium compounds at a certain moisture to the cotton containing sugars led to marked reduction in stickiness of cotton21 .Standard bale of cotton was opened and sprayed with 0.5 to 1 per cent of Ammonium hydroxide or 1 to 2 per cent Ammonium nitrite and water was sprayed to obtain a moisture content of 10 per cent. The bale was repacked and stored for 120 days. Sugar content was found to reduce from .39 to .09 per cent with ammonium hydroxide and from .68 to .1 per cent with Ammonium nitrite.
Afzal has discussed in detail the causes of stickiness and remedial measures. Multiple pickings reduce the time for insects to enter the plant and help reduce stickiness.
Several additives for spraying on cotton to reduce stickiness are given by Hector and Hodkinson. Use of chemical additives prior to ginning helps to reduce sugar by forming a coating over the fibres. Blending sticky cottons of small amounts with normal cotton may mitigate the problem to some extent. Hequet, Abidi and Ethridge mixed sticky and non sticky cottons in various proportions and spun them into yarn. At low levels of contamination stickiness does not affect end breakages in spinning. Cottons with less than 12 H2SD spots do not have much influence on end breakages in ring and rotor spinning. Even small amounts of trehalulose contaminate the equipment in course of time. Cumulative negative impact is felt as a result on quality and productivity.
Perkins found that tandem carding helps to reduce stickiness. Application of hydrocarbon with surfactant at the opening stage reduces stickiness problems at various stages of spinning. Spraying sticky cottons with Beijerinckia mobilis, a free living nitrogen-fixing bacterium reduces stickiness. CIRCOT suggest spraying of microbial culture recovered from lint reduces stickiness without affecting strength. Other advantage claimed is that it can be applied to seed cotton prior to ginning. Storage of new crop for about 3-6 months will also reduce stickiness
Studies with cotton having high moisture content showed that increase of moisture up to 15 per cent reduces stickiness without affecting quality. Both sugar content and stickiness are reduced with water up to 30 per cent with urea or ammonia. This is contradictory to the findings of Perkins and others that lower humidity in processing helps to reduce stickiness.
Chueng et al analysed trimethylsilyl derivatives of the water-surfactant-soluble components of cotton fibers by gas chromatography and found substantial amounts of sucrose and turanose. The sugars come from honeydew and cause stickiness.
As pointed by Miller, Trehalulose turanose palatonmose and sucrose are very sticky. Melazitose, ruffinose, glucose and fructose are less sticky. Biological methods to control stickiness should concentrate on sticky sugar components and stickiness potential of Individual Insect Honeydew Carbohydrates on Cotton Lint.
References
- J, Bourley, Contribution to the study of sugars in cotton plants (in French) Cot. Fib. Trop., 1980, 35, 189-208.
- W.B. Miller, E. Peralta, D. R. Ellis, H. H. Perkins, JR Stickiness Potential of Individual Insect Honeydew Carbohydrates on Cotton Lint, Textile Research J,1994, 64, p344
- D. E. Brushwood, H. H. Perkins, Cotton sugar and stickiness test methods, Can. Text. J., 110(1993), 54- 62.
- G. Gamble The thermo chemical degradation of melezitose and trehalulose as related to cotton stickiness, Textile. Research. J., 72(2002), p174-
- E. Hequet, T.J. Henneberry, and R.L. Nichols, Sticky Cotton: Causes, Effects, and Prevention, United States Department of Agriculture, Agricultural Research Service, Technical Bulletin Number 1915 June 2007
- M. Shimoda and Ken-ichiro Honda, Insect reactions to light and its applications to pest management, Applied Entomology and Zoology November 2013, Volume 48, Issue 4, pp 413–421
- Ajay K. Sood, Management of insect-pests in protected environment, http://agropedia.iitk.ac.in/content/management-insect-pests-protected-environment
- Donald E. Brushwood, Modification of the Potassium Ferricyanide Reducing Sugar Test for Sugars from Extracts of Cotton Fiber, The Journal of Cotton Science 4:202-209 (2000) http://journal.cotton.org, © The Cotton Foundation 2000
- C.W. Roberts, P.S.R. Cheung, H.H. Perkins, JR Implications of Monosaccharides in Sticky-Cotton Processing Part II: Effects of Growing Conditions on Fiber Contaminants, Textile Research J, 1078, 48, p91
- F. E. Barton J. D. Bargeron iii, G. R. Gamble, D. L. Mcalister, and E Hequet, Analysis of Sticky Cotton by Near-Infrared Spectroscopy, 2005 Society for Applied Spectroscopy, 2005, 59,p 1388
- S. Ghosh & R. B. Roy Quantitative Near-infra-red Analysis of Reducing Sugar from the Surface of Cotton
- J. of Textile Institute 2008,Pages 504-510
- N. ABIDI AND E. HEQUETFourier Transform Infrared Analysis of Trehalulose and Sticky Cotton Yarn Defects Using ZnSe-Diamond Universal Attenuated Total Reflectance, Textle Research J, 2005, 75, p645
- W. Frydrych, T. WI CH, J. Andrysiak, A Walawska, Comparative analysis of the stickiness assessment methods Institute of Textile Architecture, 276 Piotrkowska Str., 90-950 ód, Poland
- E. F. Hequet N. Abidi, Cotton stickiness evaluation by means of multi-temperature testing, Google Patent US20020083764A1
- Gutknecht, J. , Fournier, J.Frydrych, R.
- Influence of water content and air temperature on cotton stickiness with a l aboratory minicard [1986],: INTERNATIONAL INFORMATION SYSTEM FOR THE AGRICULTURAL SCIENCE AND TECHNOLOGY, 1986
- A. Shams-Nateri1 and M. Mohajerani Evaluation of Cotton Fibers Stickiness by Colorimetric Method, Prog. Color Colorants Coat. 6(2013), 9-15
- W. Stanley Anthony, On line Assessment of Cotton Stickiness, https://www.icac.org/icac/Projects/CommonFund/Stickiness/final_report/proceed/anthony.pdf
- G.R. Gamble, Evaluation of Cotton Stickiness via the Thermochemical Production of Volatile Compounds,, The Journal of Cotton Science 7,45–50 (2003)
- H. A. Eltahir, H. Abderahman.,Salah Abdelateef, Salah Aldeen and M.. Elarabi, Taguchi approach for analyzing the impact of varying degrees of cotton stickiness on ring-spun yarn quality, J Of Textile Institute, 2017,108, p 408.
- Hafiz A. Eltahir, H. Abderahman,Salah Abdelateef &Salah Aldeen M. Elarabi, Taguchi approach for analyzing the impact of varying degrees of cotton stickiness on ring-spun yarn quality, Part II: effect on rotor-spun yarn quality J Of Textile Institute, 2017,108,p 665
- Bruria Heuer, Z. Plaut, A New Approach to Reduce Sugar Content of Cotton Fibers and Its Consequence for Fiber Stickiness, Textile Research J, 1985, 55, p263.
- M. I. Afzal m Cotton stickiness – A marketing and processing problem MIAN IFTKHAR AFZAL M, Proceedings of the seminar, July 4-7, 2001, Lille, France
- Hector, H.J. and Ian D. Hodkinson (1989) STICKINESS IN COTTON ICAC Review Articles on Cotton Production Research No 2
- Eric F. Hequet Noureddine Abidi Dean Ethridge, Processing Sticky Cotton: Effect of Stickiness on Yarn Quality, Trxtile Research J, 2004, 75, p 402
- H.H. PERKINS, Identification and Processing of Honeydew- Contaminated Cottons , Textile Research j, 1983, Aug, p 508
- CIRCOT, Reducing the stickiness in cotton = CIRCOT approach, CIRCOT Leaflet No 4
- David T.W. Chun Donald Brushwood High Moisture Storage Effects on Cotton Stickiness, Textile Research
- P. S. R. CHEUNG AND C. W. ROBERTS. AND H. H. PERKINS, J, Implications of Disaccharides in Sticky-Cotton Processing : Honeydew Contamination, Textile Research J, 1980. Jan, p 55.
- O. Fonteneau-Tamime AND R. Frydrych and J.Y. Drean, Carded Spinning of Sticky Cotton Part I: Stickiness Effects on Productivity, Textile Research J, 2001.71 P 10
- O. F.Tamime AND J.-P. GourlO, Carded Spinning of Sticky Cotton Part 11: Stickiness Effects on Quality, Textile Research J, 2001, 71 p1046
N Balasubramanian is Retired Joint Director with BTRA and a consultant. He can be contacted on: 9869716298