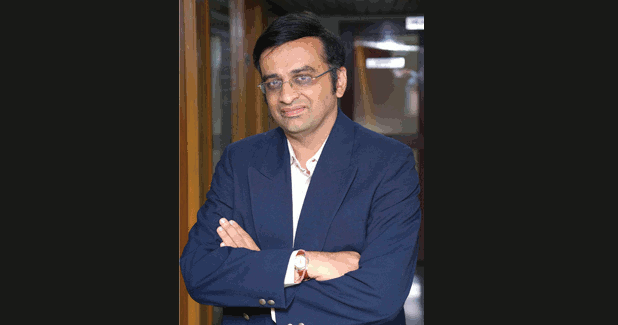
SprintOn makes strides, enters US market: Amol Bhagwati
InspirOn Engineering Private Limited (IEPL) is the world’s largest manufacturer of high performance aluminium flyers having manufactured and sold over 3.5 million of these critical textile components around the world.
InspirOn Engineering Private Limited (IEPL) is the world’s largest manufacturer of high performance aluminium flyers having manufactured and sold over 3.5 million of these critical textile components around the world. Amol Bhagwati, Managing Director of InspirOn Engineering, speaks on various machinery and technologies the company is planning to launch during ITMA.
How many ITMAs has your company attended? Please share your company’s experience in the international markets with reference to participation in other exhibitions too.
We had very good response from the industry and the footfall was more than we expected in last exhibition. We can readily say ITMA 2019 will be a very good exhibition for InspirOn. Inspiron, as the leading technology provider and partner of textile industry, will definitely utilise the platform to present our latest innovative developments and solutions for esteem customer base. Participating in the major event since its inception.
What are the machinery/accessories your company will be displaying during this ITMA Barcelona? What are their unique features and applications?
We have developed our own technology for SprintOn/Motex 15000 Stenter with exclusive features such as:
Higher drying efficiency: Achieving optimum solution for higher throughput of Hot air is the prime objective in order to achieve higher drying efficiency. Series of iteration with CFD software, for nozzle development, finally resulted into development of unique “Uniflow†air flow system by R&D team.
Validation process of the newly-developed nozzle was performed on 100 per cent cotton fabric, considering the inherent properties e.g. cool, comfort, moisture regain and user spectrum; at our R&D centre and further validated by running in an established process house at Ahmedabad. Comparative study between Motex 4560, a machine manufactured by InspirOn with Monforts technology and supplied to above process house in 2012 and new model (a machine developed through our own R&D efforts and Installed in December 2015 in the same process house) was carried out by DKTE Institute, Ichalkaranji.
Drying efficiency of new model (Motex 15000 / SprintOn) Stenter is observed and certified by both DKTE and customer as, significantly higher than the existing model Motex 4560 by 15 per cent; at par or better than the European competitors.
Higher Squeezing Padder 12 ton with Triflex Roller: Considering perception of customers who would like to squeeze the fabric optimally prior to drying and also squeeze out liquor from knit fabrics in a manner whereby the basic structure is not distorted – our R&D team developed new high squeezing Padder with following parameters,
- Robust compact frame structure.
- Optimised trough capacity to reduce drain losses substantially (up to 60 liter).
- Pneumatically controlled sliding and tilting trough with user-friendly operation of lifting, level controlling and cleaning
- Load capacity is increased up to 12 Ton maintaining uniform force of 50 kg/cm throughout fabric width thereby maintaining uniform nip through high squeeze Triflex® rollers
After conducting extensive trials at our R&D ventre on various substrates, we finalised the design, which would work successfully at customer process house. While commissioning the padder at Somany Evergreen Knits Limited it was observed that single jersey GSM-150, Width-180 cm of knitted fabric produced results of squeezing efficiency comparable to the one being observed on padders supplied along with world’s best manufacturer of Stenter.
Further, new design of Padder enabled processors to achieve:
- uniform padding pressure across the fabric width
- short cloth passage
- Extreme low fabric tension ensuring minimum fabric elongation and horizontal fabric guiding through the Padder rollers. This has ensured that knitted fabric is handled with delicate treatment to the web.
- Higher Squeezing capability ensures optimum pick up % for specific processes e.g. wet on wet finish with desired add on % next, resulting in better productivity.
Artificial Intelligence (Process Control & Automation): Our user industry is rapidly moving to adopt Industry 4.0 standards. Considering this development, all our new features shall support besides automation, adoption of Industry 4.0 standard at customer’s end. Features which shall support transformation of modern controls are
- Web App for remote visualisation of HMI screen via smartphone or tablet devices
- Remote access for online diagnosis
- On line process control and monitoring through unified HMI and data analysis on a real-time basis through SCADA system
- Process automation and Control with Pleva sensors
Strengthen mechanical design part: Redesigned topography of chain imparting higher strength however, reducing its weight requiring less energy for its rotation, superior insulation of roof and door panels of chambers etc.
KAPrec HRU units: Air-to-Air Heat recovery Unit makes the new series of InspirOn Stenter, more energy efficient – KAPrec – an unique product, designed by Helge Freiberg, former R&D chief and marketed by Wolfgang Kaphahn former Marketing Director of A. Monforts. InspirOn Engineering is licensee for manufacturing and marketing of KAPrec HRU.
HRU is a compact unit and is mounted on each chamber of our stenter. This high performance device saves energy by heat recovery. It is supplied in completely pre-assembled condition and therefore can be readily installed either on new stenter or can be retro-fitted. It can be easily retrofitted into the existing exhaust ducts – no large scale / expensive re-ducting is required.
About 50 mm thick high density insulation is provided inside to prevent heat loss, Due to unique design of HRU, cleaning frequency is ranging from six months to one year. Other HRUs offered by competitor require very frequent cleaning thereby interrupting production. Production loss with KAPrec HRU will be therefore, minimal. With the rising cost of energy, KAPrec HRU has become a right solution for much needed and sought for energy conservation.
Study was carried out to evaluate the performance of HRU units under controlled (process and machine Parameters) conditions running with specific substrate at one of the reputed customer’s end where seven HRU units have been installed on stenter machine. Observations were made for inputs properties e.g. exhaust air volume, exhaust air temperature, fresh air volume and output properties Delta T, Fresh air inside etc. as ultimately the saving depends on them. Performance evaluation of the HRU for specific processes was done as energy saving in Kcal/ hour.
Energy saving observations as quantitative performance evaluation of “HRU units†for finishing and Heat-setting process was observed at 7,000-9,000 Kcal/hour and around 10,000-13,000 Kcal/hour for each HRU. HRU units are mounted on individual chamber, considering the eight HRUs mounted on a 10F chamber machine at one of the customer’s place, saving is observed around 60000-70000 Kcal /hour. and 80000-100000Kcal /hr. in finishing and heat-setting processes respectively.
Over 125 installations of KAPrec HRU units are currently running successfully in organisations like Vardhman, Arvind, Raymond, etc. and in the process have make our stenter more energy efficient.
The textile processing industry in India facing several issues such as higher cost of energy, paucity of labour and effluent treatment plants and emissions. The thrust is predominantly on the reduction of thermal and electrical energy needs, recovery of energy from exhaust air, elimination of value losses, consistent and reproducible results. Applications where by reduction in errors of operation, efficient and quick diagnostics to reduce downtime etc.
Optimised energy consumption: energy cost / kg of fabric: InspirOn Stenters have performed in corporate customers like Arvind, Raymond and Vardhman where considerable savings in thermal and electrical energy is achieved. Corporate customers have therefore, placed repeat orders and as such we have supplied 13 stenters to Arvind Mills and seven to Raymond.
At several corporate customers, we have been able to run trials on ours as well as European competitors’ stenter, applying similar parameters both in terms of fabric as well as operating parameters. In all such trials, we have found that thermal and electrical energy consumption is less in New Model (SprintOn / Motex 15000) stenter than the imported stenter machine. This is evident from the trial results as mentioned below. This savings shall certainly translate into substantial cost reduction in unit of fabric.
Versatility: SprintOn / Motex 15000, having very sturdy design has very low maintenance cost. It provides complete solution for all kinds of substrates (Woven/knits/technical textiles from 200 gsm to 800 gsm or more).
Further, the utility of InspirOn Stenter (SprintOn / Motex 15000) can be greatly enhanced by inbuilt features or additional features as per the requirement of customer, as mentioned below:
- Cradle and brushing units for denim
- Higher squeezing Padder
- Pin protection flapper
- Cushioning effect for Knits
- High operational speeds up to 150 mpm
SprintOn / Motex 15000 is capable of producing desired finishing effects for shirting and suiting which normally processors feel by hand. Thanks to the mechanical, electrical and electronic features which in combination enables machine to reproduce same process parameters ensuring of achieving desired finish of fabric on repeat runs.
How have your company’s products been doing in the global export markets? In which year did the company make a breakthrough and how has this progressed through the years?
Being known to be continuously on the progressive front, InspirOn engineering has now crossed Indian borders and has entered the USA market with unprecedented success!
The recently installed stenter, branded “SprintOn†– aptly named to match the Hi-speed performance, at Crypton Inc., North Carolina has set the market literally on the move! This dream story began with the flawless shipment followed by installation in a record time, handing over the machine for production within a time frame not even envisaged by the management of Crypton Inc. Every day, Crypton continues to grow stronger. Including green vertically integrated manufacturing facility in Kings Mountain, North Carolina. Today, Crypton is more than 100 dedicated, enthusiastic people. Crypton® sells a wide range of products worldwide that makes life easier and continue to exceed expectations.
The “SprintOn†stenter meets with all the essential safety features which are mandatory in any USA production house. The ten chambers “SprintOn†stenter is an integral part of an intricately designed coating line and the entire synchronization of various components and their drives, was done by InspirOn team.
The performance levels have exceeded those which were committed, so much so that Chip king – manufacturing head of Crypton Inc. conceded that SprintOn has been the best thing that has happened to him in the past 25 years that he has been around in the industry. This is remarkable considering the fact that he has European set-up in his state-of-art processing plant which caters to the hi-demanding furnishing and upholstery industry.
In a heartwarming letter addressed to Prakash Bhagwati, Chairman of InspirOn Engineering, King has complimented for the exemplary execution of SprintOn stenter.
It has been a dream come true for Prakash Bhagwati to be a world leader in supplying best technology to advanced and growing nations. Bhagwati, who was directly involved in the set-up and manufacturing process of European textile technologies in India, is very positive about the market development for ‘SprintOn’.
The installation of ‘SprintOn’ in USA has already generated tremendous enthusiasm in the USA market with several live projects under discussion.
The forthcoming ‘ITMA’ exhibition at Barcelona in June, 2019 should witness many interesting developments for InspirOn engineering in terms of product features and market expansion.
In the recent past, has your company entered new markets, and if so, which are the ones and for which products?
In last year, we have made breakthrough in the USA market – 10 CH stenter was installed at Crypton.
Inspiron, as the leading technology provider and partner of textile industry, will definitely utilise the platform to present our latest innovative developments and solutions for esteem customer base.
We believe in sustained technology development to bring in innovative features, operational economies and user friendliness.
Promoting products/machinery effectively through exhibitions abroad is very important for the industry and the country in these days of globalisation.
Is your company fully or partially dependent on foreign technology or inputs? Or are the products totally indigenously made? Give your comments on your competitive strength.
We believe in sustained technology development to bring in innovative features, operational economies and user friendliness. Our product development is backed by DSIR recognised R&D facility to carry out trials for validation of new features. A team of dedicated design engineers with application technologists are continually working on development project to fulfil the immediate/ forthcoming and implied need of the industry.
With some new countries entering textile production and also a few restoring & revival of textile industries, do you see any rise in demand for your products globally?
There is always demand for good technology, Our product performance itself speak in terms of repeat orders at esteem organizations like Arvind, Vardhman, Raymond, Mafatlals, BVM etc.
What are the future prospects and problems that your company is facing in raising its share for its products/machinery in the global market?
Technology has its own value and we believe in value for money concept. Promoting products/machinery effectively through exhibitions abroad is very important for the industry and the country in these days of globalisation.
Do you have any suggestions/advice for the industry?
Definitely we believe that it is important to explore global perspective. Exhibitions and media are the platform to share the developments and edge. We believe in quality not in numbers. Our product performance at various esteem organisations itself play as a big advertising tool for us.