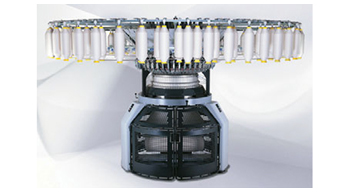
Spinitsystems, a 3-in-1 revolution!
This year?s ITMA set the scene as customers and prospective customers saw for themselves in Milan the market-ready Mayer & Cie. spinning and knitting technology that is better known as spinitsystems®.
This year?s ITMA set the scene as customers and prospective customers saw for themselves in Milan the market-ready Mayer & Cie. spinning and knitting technology that is better known as spinitsystems®. Since a prototype was presented for the first time in Barcelona four years ago, Mayer & Cie. has taken the technology consistently further forward and has gained extensive experience with it. It even already has its own knitwear collection. Mayer & Cie. presented models from this collection at its ITMA stand.
spinitsystems® 3-in-1: Mayer & Cie.?s spinitsystems® combines in an intelligent way what were previously separate processes in textile manufacturing. The technology combines the three process stages spinning, cleaning and knitting. Rewinding ? a step that was previously necessary ? is no longer required.
The Spinit 3.0 E is the first machine to be fitted out with the new technology. On this machine single jersey knitwear is manufactured not from yarn but from roving straight from the spinning mill. This machine?s technology thus kicks in at an entirely different point from conventional circular knitting technology. With spinitsystems® technology the so-called flyer roving is taken from conventional flyer bobbins and fed to an electronically controlled conventional 3-over-3 roller drafting system where it is drawn into a fine fibre bundle. The twin-jet false-twist spinning unit then takes over, feeding the fibre bundle to the knitting unit, where it is resolved on the yarn guide into a composite fibre without a twist. After cleaning the composite fibre is formed into loops by means of a conventional circular knitting process using the tried and trusted relative technology and a textile surface takes shape.
This process provides the users with a whole array of advantages. Where the quality of the knitted goods is concerned, its lack of a skew is especially striking. That is because spinitsystems® processes roving straight into knitwear, knitting the fibres into loops gently and without a twist. Other benefits that struck customers in trials included the voluminous feel of the knitwear. That makes it particularly suitable for use in manufacturing high-quality baby linen and nightwear and quality shirts.
The combination of several processes also leads to lower overall capital investment in machinery. It also brings a space saving of one third because ring spinning and winding machines are no longer required. The Spinit 3.0 E is similar in dimensions to a conventional knitting machine. Viewed across the entire production process that leads to significantly lower production costs. At the same time the Spinit 3.0 E offers the user a gain in flexibility because in some cases different fabric weights can be manufactured from the same flyer roving.
The Spinit 3.0 E fulfils today?s sustainability requirements brilliantly, using a good third less energy to manufacture single jersey knitwear than the conventional manufacturing process would require. That too is due to the combination of processes. The fact the energy-intensive ring spinning and winding are no longer required has a particularly positive effect on the machine?s energy and CO2 balance sheet.
From the prototype in 2011 to market maturity in 2015:
?Since presenting the prototype four years ago in Barcelona we have, of course, continued to work intensively on the machine,? says Michael A. Tuschak, in charge of spinitsystems® marketing and distribution at Mayer & Cie.
Cleaning is one process that underwent further development. The roving sensor reliably identifies and cleans thin and thick sections in the fibre material presented. The machine carries on running because the fully integrated software cuts out the yarn bobbin in question until the faulty yarn segment has been automatically cleaned up. The cleani