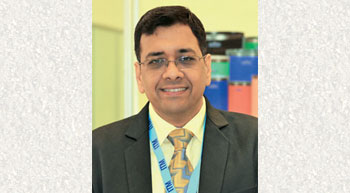
Spincan makes a mark in card & spinning cans
Spin cans and all the components are designed, materials selected and manufactured in all sizes and diameters following ISO specifications. For over 50 years, Kolkata-based Spincan and its associates have been manufacturing card and spinning cans for the jute and textile industries. The invaluable experience and expertise built over this period have kept Spincan abreast of current technology and enabled it to provide state-of-the-art cans and accessories.
Spin cans and all the components are designed, materials selected and manufactured in all sizes and diameters following ISO specifications.
For over 50 years, Kolkata-based Spincan and its associates have been manufacturing card and spinning cans for the jute and textile industries. The invaluable experience and expertise built over this period have kept Spincan abreast of current technology and enabled it to provide state-of-the-art cans and accessories.
In all functional areas—from design to construction and dynamics of spinning—spin cans are the products of innovative technology, their quality assured by rigorous control at every stage of manufacture. The company has a number of patents to its credit. These products have found wide acceptance, not just in India, but also in countries the world over. Spin cans and all the components are designed, materials selected and manufactured in all sizes and diameters following ISO specifications. Castor Wheels of fluff-proof design patented by the company are the integral parts of its state-of-the-art cans. The can body is made of a special blend of polymers – HDPE with plasticised polymer blend for making the butt weld perfect and stress free. The butt welding is performed in a numerically controlled welding machine specially designed and also the weld area is ironed out to ensure the inter lattice diffusion at the joint. Thus, a seamless barrel is made and joints are tested for impact resistance. The side seams of its cans have never failed at the joint even after several years of intensive use in spinning.
Springs are the heart of spinning cans. It is made of high carbon spring steel wire manufactured by a renowned steel company with ISO 9002 certification.
They are heat treated to ensure fatigue-free performance, uniform collapsibility and release; these are the quality springs of spincan for fitment in modern spinning machines. Plastic bottom covers are so designed that they allow clustering of coils of the spring within themselves. This allows additional capacity for the sliver to fill in. Springs for higher load and diameter of laid-on-slivers, are fitted with Pantograph. A triangular bottom is required for the free movement of the Pantograph, so that the spring collapses uniformly. The bottom of the Pantograph is especially designed to accommodate the collapsed convolutes which ensures uniform movement of sliver, not allowing any tilting of the top plate. These bottom plates are made from deep drawing quality GI sheets which are equidistantly embossed to enhance the overall strength and to avoid any deformation.
Spincan offers castor wheels of different sizes. Apart from ones with trapeze base, rectangular base, it offers castor wheels with ball bearing, bush bearing, needle bearing, etc. ‘Dynamic’ Castor Wheels are manufactured inhouse with needle bearings, ball bearing, bush bearing, and ball bearing spin castor. Tyres are in-situ injection moulded with RPU polymer, nylon and polypropelene. A number of patents have been awarded for Spican’s innovative fluff-proof designs of castor wheels.
(For further information, visit: www.spincan.net)