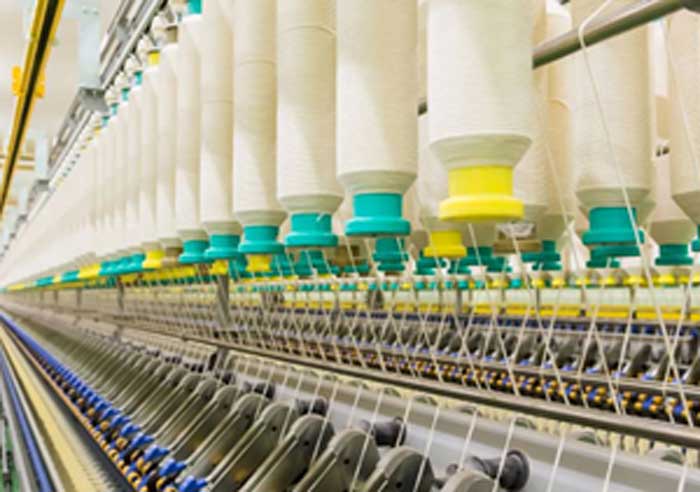
Spin to Win
Spinners operating in this dynamic environment have limited control over profit margins, informs Sarathy TG.
The global textile industry is witnessing a dynamic transformation fuelled by shifts in fibre demand, cost factors, and regional competitiveness. As polyester continues to outpace cotton in growth, manufacturers face challenges in maintaining profitability amidst fluctuating raw material prices, labor costs, and operational efficiencies. Below is an insightful snapshot of the trends and competitive landscape shaping the future of textile production.
Global fibre demand trends
The global fibre demand scenario underscores a significant shift in textile dynamics, with fibre consumption estimated at 100 million tonne in 2021, advancing at a Compound Annual Growth Rate (CAGR) of 3 per cent. Polyester has overtaken cotton as the largest and fastest-growing fibre category, reflecting its versatility and widespread applications across industries. Filament yarn (PFY) is expected to outpace polyester staple fibre (PSF) in growth, attributed to its increasing usage in high-demand sectors. The steady increase in polyester consumption marks a pivotal transformation in global fibre preferences, positioning it as a keystone material in the textile sector’s evolution.
The chart below visualises the steady rise in polyester consumption compared to other fibers from 2014 to 2030, reflecting market shifts. Polyester’s growth curve highlights its increasing relevance, while cotton sees slower growth, indicating market adjustments.
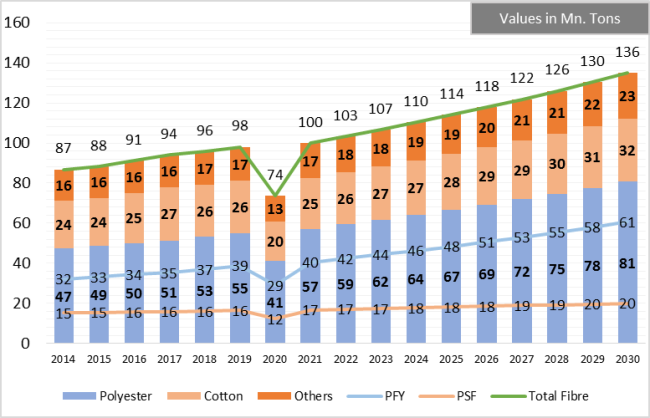
CAGR 2014-19 — 3.1% 1.7% 1.7% 3.8% 1.5% 2.5%
CAGR 2019-30 — 3.5% 1.8% 2.6% 4.2% 1.8% 2.9%
Fibre price trend: Cotton

The chart illustrates the cotton fibre price trends from March 2018 to June 2024 across three major regions: Australia (SM), the United States (CA SM), and India (Shankar-6). Notably, cotton prices experienced substantial fluctuations, with India’s cotton price peaking above that of Australia and the U.S. in early 2022, reaching a maximum around 3.52 $/kg. This surge in Indian cotton prices marked a temporary deviation from historical trends, where India typically maintained lower prices compared to its counterparts. By mid-2023, however, prices realigned, and India’s cotton costs declined below those of Australia and the US, stabilising in the range of approximately 1.88 to 1.91 USD/kg by June 2024. This trend signifies the volatile nature of the global cotton market, influenced by regional supply-demand dynamics, geopolitical factors, and climatic impacts.
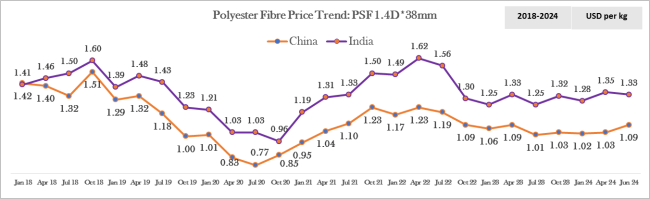
Fibre price trend: Polyester and viscose
The fibre price trends for polyester (PSF 1.4D38mm) and viscose (VSF 1.5D38mm) between 2018 and 2024 reveal distinct pricing dynamics in China and India. In the polyester segment, India’s prices have shown a steady increase, reaching highs of $1.62 per kg in April 2022, while China’s prices have remained comparatively stable, often below those in India, creating a widening price gap. This divergence indicates that India has experienced a more rapid escalation in polyester costs relative to China. Conversely, the viscose fiber prices show a decreasing disparity, with India’s prices exhibiting more stability and proximity to China’s, which highlights India’s improved competitiveness in recent months. This convergence in viscose prices underscores the shifting landscape in fibre trade economics, where India’s strategic positioning appears to be bolstering its role as a competitive player in the global textile market.
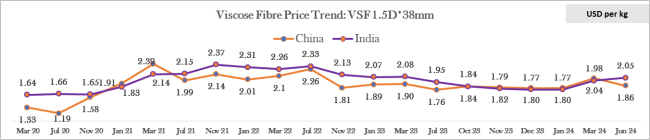
Installed capacity – spindles
The global landscape of installed spindle capacity across major textile-producing nations, it’s clear that significant shifts are underway. China continues to dominate, with a staggering 70 times higher than the lowest country in 2022, inching up slightly to 70.1 times higher than the lowest country in 2023. India follows as the second-largest player, with its capacity growing from 46.5 to 48 times higher than the lowest country within the same period. Other key players like Bangladesh and Pakistan hold steady, each at around 11 to 12 times higher than the lowest country, while countries such as Indonesia, Vietnam, and Turkey contribute at more moderate levels. However, it’s Egypt that stands out with an extraordinary 74 per cent growth rate in spindle capacity since 2022, marking its emergence as a rising force in the textile industry. This data reflects not only the continued dominance of traditional leaders but also the dynamic shifts that are shaping the future of textile manufacturing, as emerging markets accelerate their capabilities to vie for global market share.
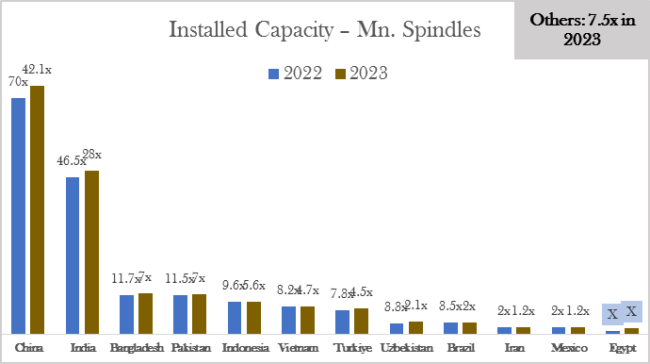
Indicates the lowest value among the group
Installed capacity – rotors
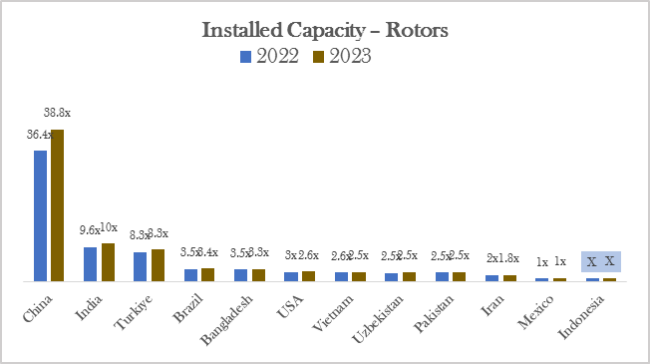
Indicates the lowest value among the group
The global landscape of installed rotor capacity, China’s overwhelming lead, with its numbers rising from 36.4 times higher than the lowest country in 2022 to 38.8 times higher than the lowest country in 2023. India follows, though at a distant second, with its capacity growing from 9.6 to 10 times higher than the lowest country, and Turkey ranks next with around 8.3 times higher than the lowest country. The gap between China and the other nations is vast, but what’s truly remarkable is China’s 17 per cent growth rate in rotor capacity since 2022—a clear testament to its commitment to dominating the global textile sector. Meanwhile, countries like Brazil, Bangladesh, and the United States maintain more modest rotor capacities, reflecting a steady dedication to rotor-based production. This significant expansion in China’s rotor capacity underscores its strategic focus on fortifying its textile manufacturing infrastructure, cementing its position as a powerhouse in this capital-intensive sector.
Cost factors for spinning
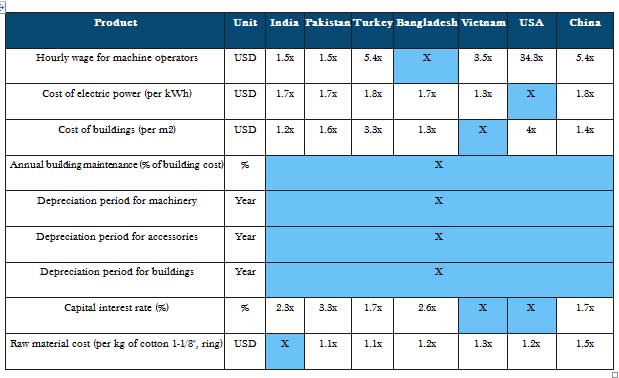
Indicates the lowest value among the group
The table presents a comparative analysis of cost factors in the spinning industry across various countries, including India, Pakistan, Turkey, Bangladesh, Vietnam, the USA, and China. Key cost determinants, such as hourly wages for machine operators, electricity rates, building costs, maintenance expenses, and raw material costs, highlight significant disparities. For example, the USA exhibits the highest labor costs at 34.3 times the baseline, while Vietnam shows a competitive edge with low electricity costs (1.3x) and moderate building expenses. Bangladesh, marked by the lowest figures across various metrics, including labor and raw material costs, showcases its cost-efficiency in spinning production. Such comparative data emphasises the strategic advantages each country holds, shaping competitive dynamics within the global textile sector.
Comparison of cost factors for spinning
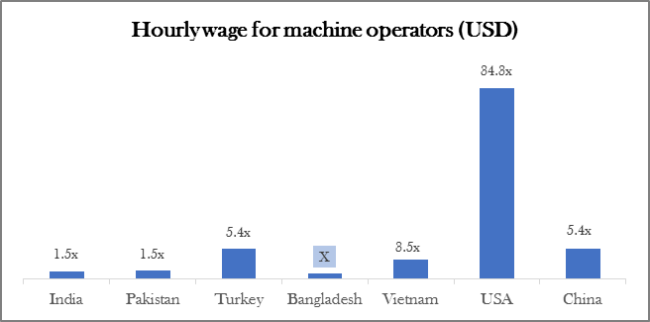
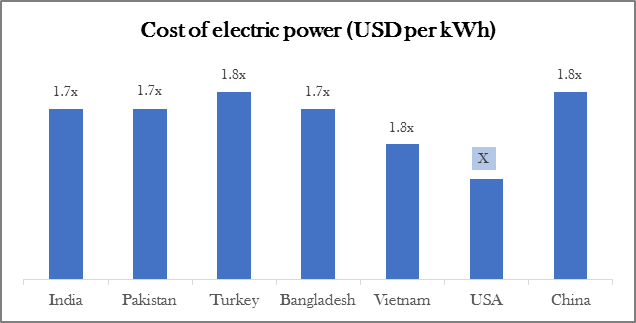
Indicates the lowest value among the group
The chart presents a comparative analysis of cost factors affecting spinning operations across several countries, including India, Pakistan, Turkey, Bangladesh, Vietnam, the USA, and China. Key metrics highlighted are hourly wages for machine operators, and the cost of electric power. Notably, the USA stands out with significantly higher labor costs (34.3 times the lowest country), while Bangladesh generally offers the lowest costs in hourly. The cost of electric power in the USA is lower compared to other countries. This data underscores the substantial cost variances in textile production, influencing competitive positioning across regions.
Total cost: Spinning ring/Ne30
In comparing the total costs of spinning operations across major textile-producing countries, I find India to hold a distinct advantage. India’s lower raw material costs, coupled with efficient manufacturing expenses, position it as the most cost-effective option in the spinning sector. Countries like Bangladesh and Vietnam show competitive manufacturing costs; however, their higher raw material expenses push up the total yarn cost. In contrast, the United States and China face significantly higher costs, particularly in labour and power, which place them at a competitive disadvantage.
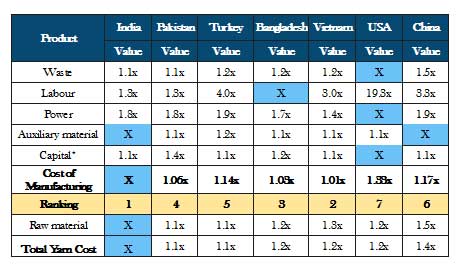
Indicates the lowest value among the group
This cost analysis underscores a clear competitive edge for India in the global textile market, thanks to its ability to maintain lower input costs. It’s evident that strategic cost management is essential in maintaining a stronghold in the international textile landscape, especially as production costs vary widely by region. This disparity highlights how each country’s unique cost structure impacts its position and potential profitability within the industry.
Total cost: Spinning rotor/Ne20
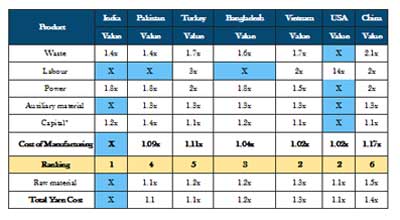
Indicates the lowest value among the group
In examining the cost dynamics for spinning rotor operations (Ne20) across key textile-producing nations, it’s clear that India emerges as the most cost-efficient, ranking first in overall manufacturing expenses. This advantage is largely due to India’s low labor and auxiliary material costs, which significantly reduce the total manufacturing expenditure. Bangladesh and Vietnam, while also showing competitive labor costs, are impacted by higher raw material prices, elevating their total yarn costs. Meanwhile, the USA benefits from competitive capital and power costs but is disadvantaged by substantially higher labor expenses, causing it to lag India and other Asian counterparts in cost-effectiveness. This comparative analysis highlights India’s strong position in the spinning rotor sector, emphasising the country’s strategic advantage in low-cost production inputs and its potential as a preferred destination for cost-conscious textile manufacturing.
Labour cost
In global manufacturing, labor costs play a critical role, especially in sectors like textiles, where workforce expenses heavily impact operational viability. Comparative data reveals that Bangladesh, India, and Pakistan offer the most cost-effective labor, making them attractive for global textile manufacturers seeking cost optimisation. Bangladesh leads with the lowest labor cost per kilogram, strengthening its position in the industry.
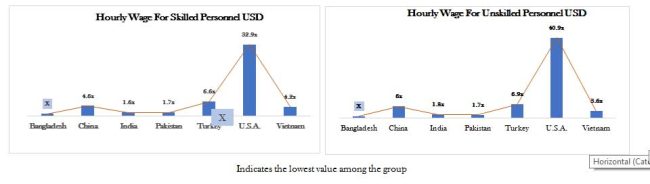
Conversely, the United States reports some of the highest wage rates, with skilled and unskilled labour costing up to 32.9 and 40.9 times the baseline rate, respectively. This high wage structure has contributed to the decline of the US textile industry, as many mills struggle to compete with lower-cost regions. This data underscores the financial dynamics shaping global supply chains, as emerging economies like Bangladesh, India, and Pakistan continue to draw manufacturers with their affordable labour. The trend highlights a geographic shift in textile manufacturing, with significant implications for both economies and workforces worldwide.
Power cost
The power cost landscape for yarn production varies across key manufacturing nations. India, Pakistan, Turkey, Bangladesh and China exhibit relatively similar costs, while Bangladesh offers a competitive edge. Vietnam emerges as a standout with notably lower power costs, potentially influencing yarn production decisions. The USA, though possessing lower power costs, faces obstacles in yarn manufacturing, likely stemming from factors beyond energy costs.
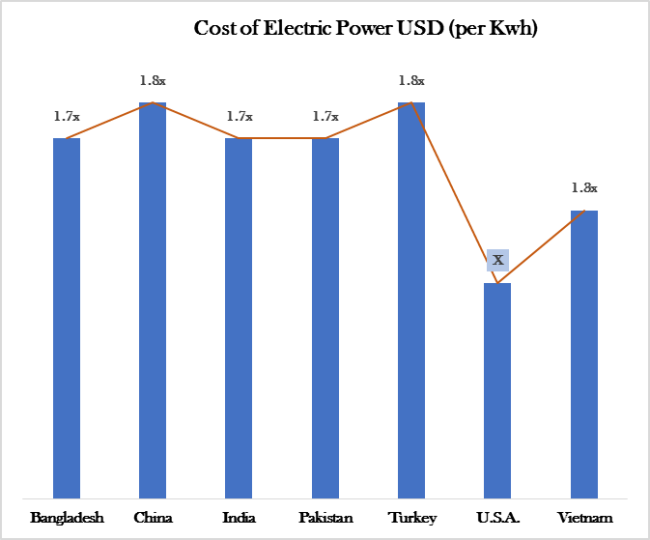
Indicates the lowest value among the group
Capital depreciation & interest cost
The global textile industry relies heavily on capital costs and interest rates, which significantly impact competitiveness. These factors vary widely among leading textile-producing nations.

Indicates the lowest value among the group
In Pakistan, high capital costs and interest rates, driven by economic instability, challenge local manufacturers. Conversely, the USA benefits from the lowest interest rate, potentially attracting textile investment due to reduced financial risks.
India and Bangladesh exhibit similar capital cost structures, creating a level field within this group. However, slight interest rate differences still affect overall costs and competitive positioning.
Textile businesses must strategically evaluate these economic factors to optimise sourcing and production, ultimately strengthening profitability through informed regional choices.
Auxiliary materials cost
A comparative analysis of auxiliary material costs and building construction costs across several key textile manufacturing nations. Notably, India emerges as a highly competitive destination for initial construction expenses due to its significantly lower building cost per square meter.

Indicates the lowest value among the group
The regional disparities in textile costs are evident in the provided data. While India, Vietnam, Bangladesh, and China offer cost-effective solutions, the USA stands out as a significantly more expensive market for both auxiliary materials and building construction. These findings underscore the importance of considering regional factors when making strategic decisions related to sourcing, investment, and supply chain optimisation in the textile industry.
Raw material cost
The textile industry, a cornerstone of global manufacturing, is grappling with rising raw material costs, particularly in key Asian nations. A recent analysis reveals significant variations across countries, with China emerging as the most expensive source for raw materials. This trend is poised to impact the competitiveness of textile manufacturers worldwide.
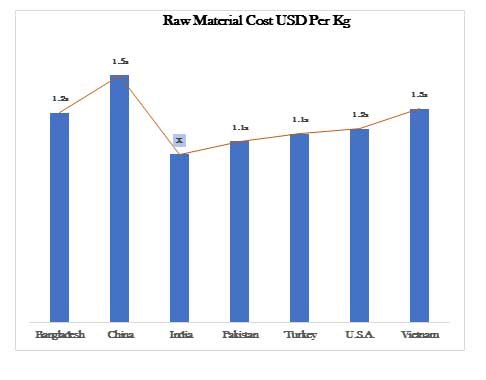
Indicates the lowest value among the group
India, while possessing the lowest manufacturing costs, faces challenges due to escalating cotton prices and import duties. This puts it at a competitive disadvantage compared to nations like Pakistan and Turkey. The infographic reveals that India’s raw material costs, particularly cotton, have surged, making it less attractive for manufacturers.
In contrast, countries like Bangladesh, Vietnam, and the USA exhibit a more moderate range of raw material costs. However, the overall trend indicates a tightening supply chain and increasing costs, which could impact the industry’s profitability and competitiveness.
To address these challenges, industry stakeholders must explore innovative solutions, such as diversifying sourcing options, investing in technology to improve efficiency, and advocating for favourable trade policies. By proactively addressing these issues, the textile industry can navigate the current landscape and ensure its long-term sustainability.
Cost impact on ring spinning
Ring spinning, a crucial textile manufacturing process, involves converting raw materials into yarn. A deep dive into its cost structure reveals key insights for optimising operations and enhancing profitability.
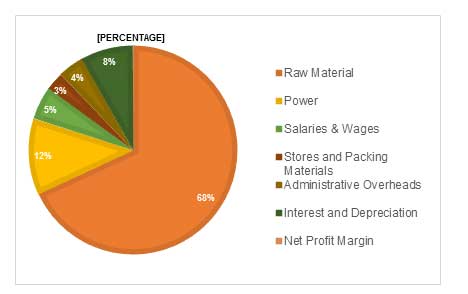
The pie chart illustrates that raw materials dominate the cost structure, representing a substantial 68 per cent of total expenses, underscoring the critical need for efficient sourcing and utilisation. Power consumption, at 12 per cent, also plays a significant role, emphasising the value of energy-efficient solutions.
Salaries, wages, and administrative costs together account for 9 per cent, reinforcing the importance of effective labor and resource management.
Key takeaways
The global textile industry is a complex interplay of factors, where cost competitiveness and operational efficiency are paramount. Countries like India, Bangladesh, and Vietnam have emerged as manufacturing hubs due to their lower costs. However, the fluctuating prices of raw materials like cotton significantly impact yarn prices, influencing the overall profitability of spinners.
While the USA offers lower power and interest costs, its high labour wages and maintenance expenses can hinder its competitive edge. Spinners operating in this dynamic environment have limited control over profit margins. To optimise their operations and maintain competitiveness, they must focus on:
- Minimising manufacturing costs: Implementing operational excellence principles, conducting periodic diagnostic studies to improve key performance indicators (KPIs), and adhering to strict quality control standards.
- Optimising yarn realisation: Employing sound yarn engineering principles to select raw materials based on specific yarn end-use, and ensuring efficient spinning and reeling processes.
- Maintaining asset health: Adhering to specified maintenance schedules for consumables and spare parts, and investing in energy-efficient technologies to reduce operational costs.
- Timely modernisation: Upgrading machinery and technology to enhance productivity, reduce maintenance costs, and improve product quality.
By strategically addressing these key areas, spinners can navigate the complexities of the textile industry and ensure long-term sustainability.
Conclusion
The evolving dynamics of the global textile industry emphasise the need for strategic adaptability. As polyester continues to dominate fibre consumption, manufacturers must align operations to meet shifting market demands while managing the pressures of rising raw material, labour, and energy costs. Countries like India, Bangladesh, and Vietnam have a competitive edge due to lower production costs, but maintaining profitability will require continuous investments in operational efficiency, sustainability, and modernisation. Embracing best practices, from energy conservation to diagnostic studies, will be critical for companies aiming to thrive in this competitive landscape. In an industry marked by rapid change, those who anticipate trends and innovate sustainably will be best positioned to lead the market.
Acknowledgment
- Data courtesy of Wazir Advisors
- Data courtesy of Emerging Textiles
- Data courtesy of International Textile Machinery Shipment Statistics, ITMF 2023
- Data courtesy of International Production Cost Comparison, ITMF 2021
About the author
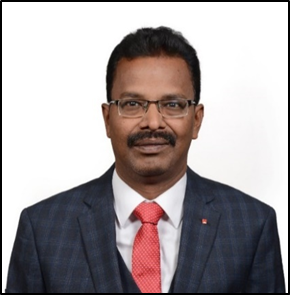
Sarathy TG, who is a Director – Regional Operations (India), Texcoms Textile Solutions, has a 37 years’ of experience in operations, project planning and execution, systems formulation and implementation. He is a specialist in coarse, superfine, compact and fancy yarns. He has worked with leading spinning mills up to director level in India and Thailand. He has planned, implemented, operated and transferred 200,000 spindles from a modern mill in Andhra Pradesh, India and lead the NSL group as Head of Technical. Planned, built, and operated large textile plants. Led operations and turnaround of textile plants.