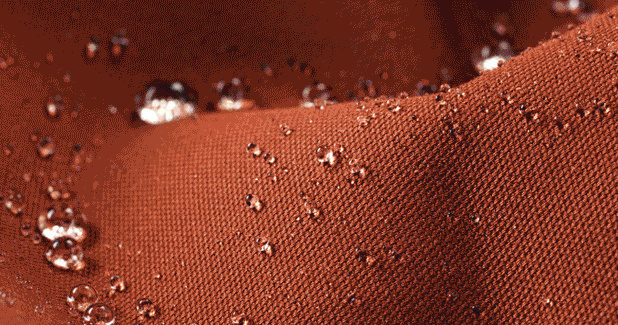
Smart Weaves Making Waves!
Innovation in textiles has reached new heights covering various aspects including care, comfort, hygiene and functional values. An ITJ Exclusive takes a peep into this new world. “Wear Your Sunscreenâ€, drums up an advertisement, promoting a dress with a textile material that can repel UV rays! Ever left the house and immediately regretted your choice of pastel shirt?
Innovation in textiles has reached new heights covering various aspects including care, comfort, hygiene and functional values. An ITJ Exclusive takes a peep into this new world.
“Wear Your Sunscreenâ€, drums up an advertisement, promoting a dress with a textile material that can repel UV rays! Ever left the house and immediately regretted your choice of pastel shirt? Well, a new colour-changing thread developed by researchers in the US could soon make that feeling a thing of the past!
Today’s textiles are more than just textiles! Stain-resistance, odour-control, anti-microbial and many such functions are injected into the textiles, making them smart and dynamic and gel with the aspirations of the present-day needs and modern generations! There has been virtually a flooding of expertise and technologies in colour, care, comfort and functional values of textiles.
“A long time back no one would have considered clothes that would provide medicinal properties like secreting vitamins, aloevera, aromatherapy and anti-allergy properties, but today smart textiles have made this possible by using microencapsulation technology,†says Avinash Mayekar, MD of Suvin Advisors.
Textiles primarily protect body. But today, function and fashion have added a new dimension to the simple protection, with comfort factor throwing its weight among other aspects. The rise of sports, leisure, hygiene and health have also given a new direction for the growth of smart textiles, the scope of which has gone beyond one’s imagination.Applications in the sports and fitness sector expected to lead the smart textiles market during the forecast period.
According to a new market research report of MarketsAndMarkets on “Smart Textiles Market – Global Forecast to 2020â€, the market is expected to reach $4.72 billion by 2020, at a CAGR of 33.58 per cent between 2015 and 2020. The driving factors for the growth of this market include the uptrend in wearable electronics industry, increasing demand for sophisticated gadgets, miniaturisation of electronic components, and a rapid growth of low-cost smart wireless sensor networks. However, the slow rate of adoption and the lack of exhaustive standards and regulations are the major restraining factors for the growth of the smart textiles market.
The application in the sports and fitness sector is expected to exhibit high growth during the forecast period. The demand for smart textiles in sports and fitness is expected to lead, growing at the highest CAGR during the forecast period. So far, the major sector for applications of smart textiles has been military and defense. From smart shirts that record heart rates to intelligent bands that track physical activities, smart textiles in the form of fitness monitoring devices have a lot of demand from health-conscious people. There is also a considerable demand for the smart textile market in architecture. Non-wearable smart textiles can be found in the architecture and design sector. Textile sensors form a huge and significant sub-segment of smart textiles. This is because sensing ability is the most essential characteristic of any smart textile product. Smart textiles have applications in medical, sports, personal protective equipment, geo-protection, military, and aerospace sectors, where sensing and monitoring are already used and would only be made more efficient if integrated with textiles. Thus, sensing functions have grown rapidly in the smart textile market and the same trend is expected to continue during the forecast period. Technology has also kept abreast of the winds of change sweeping across the textile scenario. In fashion, new weaves have set new trends. For instance, warp knitting has captured the imagination and wonders of fashion. Says sources from Karl Mayer, a leader in warp knitting technology for fashion as well as function, “Karl Mayer can provide the Indian companies with both inspiration and high-tech machines. Especially for the production of traditional Indian saris but also of upbeat fashion styles, this innovative textile machinery specialist can offer its RASCHELTRONIC® machine.
What can be done with this equipment shows a collection of sophisticated clothing fabrics made by Karl Mayer’s own product developers.â€
A South India-based maritime services company has launched environmentally friendly and biodegradable nonwoven oil sorbents. There has been a recent incident of oil spill on the shores of Bay of Bengal in India at Ennore port affecting the marine life and the pristine beaches of Marina, in Chennai, India. In the early morning hours of January 28th, an LNG tanker ship and a petroleum tanker collided at Ennore port resulting in spill. Reports indicate that this may have affected the marine life, resulting in dead turtles and oil-laden hatchlings washed ashore.
To aid the clean-up activities, government agencies and NGOs are working diligently.
A Chennai based maritime company; NAVTEK has come-up with a timely solution and has used its environmentally friendly absorbent nonwoven mats at the spill site. NAVTEK has been in the works for some months now to refine their technology and has launched its product, which is much environmentally friendlier than synthetic polypropylene mats. They have 100 per cent biodegradable nonwoven mats and oil sorbents in their product basket.
NAVTEK tested its product at Ennore port.T S Rangarajan, Vice President-Technical of NAVTEK said, he personally evaluated the product on the oil spill site. “Our mats absorbed the oil instantaneously.†According to Rangarajan, the mat was able to absorb minimum 10 times its weight of oil in first shot of soaking. This ties in well with their earlier tests, which were carried out according to international standard by a third party accredited laboratory.
Lenzing achieved another milestone in its innovation heritage in the textile industry by developing a new fibre based on cotton scraps and wood. Refibra is the first cellulose fibre featuring recycled material on a commercial scale and was launched today at Premier Vision textile fair in Paris. The fibre is produced in the Tencel production process. Tencel, already a market success as an eco-friendly fibre, is now achieving another key milestone by creating from natural resources what is likely the most sustainable fibre. Refibra from cotton scraps and wood will further build Lenzing’s reputation as a leader in the field of environmental fiber technology and will push new solutions in the textile industry towards circular economy by recycling production waste.
The new Tencel generation Refibra stands for “Reduce, Reuse and Recycleâ€. The brand name Refibra and the claim ‘Reborn Tencel fibre’ illustrate immediately that this new kind of fibre is made of recycled materials promising reduced reliance on natural raw materials. Because Refibra is based on the Tencel fibre, which has been internationally recognised for its environmentally responsible closed loop production process, Refibra offers a deep sustainability profile that clearly contributes to circular economy.
The Swiss textile technology innovator HeiQ recently launched HeiQ Bug Guard at this year’s ISPO Munich. HeiQ Bug Guard is a reliable and highly effective technology for durable mosquito and insect protection. Wearing apparel empowered by HeiQ Bug Guard reduces the risk of mosquito and bug bites and consequently decreases the likelihood of infection with life-threatening diseases such as Zika, Malaria and Dengue. HeiQ Bug Guard provides prolonged contact protection against mosquitoes but also repels ticks, dust mites, bed bugs and carpet beetles. The Swiss Tropical and Public Health Institute (TPH) has tested and proven its exceptional efficiency and durability up to 100 washings. As a full service partner, HeiQ offers two industry standard test methods for efficacy: the exposure test (TL 830 50331) and the High-Performance Liquid Chromatography (HPLC) test, which determines the permethrin level. Permethrin, the bioactive ingredient of HeiQ Bug Guard, is the only pesticide approved by the US EPA for use in clothing and gear, and is also permitted by bluesign for non-skin contact articles.HeiQ Bug Guard is applicable to all textile fibre types (except for 100 per cent polypropylene) and complies with Oekotex Standard 100.
DuPont’s latest new Nomex Nanoflex barrier material allows to protect Firefighter against toxic particles. Other latest firefighting protective gear from DuPont include: the light weight NFPA Concept Gear; the Nomex 360, the strongest lightweight outer shell; the Nomex Nano & Nanoflex, a thin thermal layer offering improved moisture management and comfort and Glide Ice with Nomex.
Freudenberg Performance Materials is set to present a new dimension in thermal insulation: comfortemp fiberball padding. This first ever padding made from fiberballs combines the advantages of loose down fillings and padding in a quality that has not previously been achieved. For example, thermal insulation is as much as 80 percent higher than conventional padding while the new material is as light and soft as down. Being focused on product innovation for solutions that improve others’ lives, lifestyle brand Napapijri will launch the Superlight Parka for the 2017 Fall/Winter season utilising their owned THERMO-FIBRE technology powered by comfortemp fiberball padding. The thermal insulation of comfortemp fiberball padding is 50 to 80 per cent higher than conventional padding. The material consists of many small fiberballs, between which are many small air pockets. These generate the high thermal insulation.
Materials from international technology company and industrial partner ContiTech ensure safety and security in a wide range of operating environments.For example, a chemical protection suit – manufactured using ContiTech’s innovative “Next Generation†fabric – is now certified to American fire safety standard NFPA. The flame-retardant material guarantees a high degree of safety in working environments where gases are generated and there is a fire hazard. It is therefore a reliable aid for firefighters, in industry and in shipbuilding.
Protective suits for which ContiTech supplies innovative materials are also available for work in extreme temperatures. They are absolutely ideal for preventing direct contact with a heat source. They provide brief protection even at 850°C.These protective suits are also designed for use at extremely low temperatures, offering protection even at -196°C briefly. All ContiTech fabrics are based on the Conti Barrier System, which uses high-performance elastomer coatings. Depending on the finish, this offers secure protection against chemicals, flames, heat or cold.
Schoeller Textil AG is setting new standards in the multinorm fabric sector with the introduction of its brand new pyroshell flame protection technology. Reliable protection from heat and flames on synthetic fabrics ensures outstanding safety and visibility in all EN ISO 20471 colours. Applications on light, elastic fabrics – if desired, combined with membranes and/or other technologies such as the highly abrasion-resistant ceraspace – introduce even more freedom of movement and function into everyday working life.
With its new pyroshell technology, Schoeller Textil AG has succeeded in uniting permanent flame protection with light polyamide or polyester fabrics. For example, pyroshell flame protection can be combined with the highly abrasion-resistant ceraspace technology. Flame protection has become mandatory for personal protective equipment for many postitions, including security staff, railways workers, police officers, staff in power stations and workers in the oil and gas industry, so that they are ideally protected when they come into contact with fire and sparks.
The pyroshell technology is produced in accordance with the bluesign system and permits permanent flame protection on a purely physical basis. Every use of environmentally-harmful flame retardants or additives such as halogens and phosphor has been eliminated. Further Schoeller finishing technologies such as NanoSphere, 3XDRY or coldblack can be applied without affecting the flame protection, thus expanding the spectrum of protective functions and wearability. The ecological, fluorocarbon-free ecorepel Bio and 3XDRY Bio impregnations have also recently become available.
STINGbye S.L. it is a textile company with more than 20 years of experience in the sector. Their goal is to work on tissue efficiency to prevent that vectors are attacking us. Vectors in the medical field is everything that can transmit a disease by itching. STINGbye clothes protect of the tiger mosquito or common, lice, bedbugs and ticks. As an effect the fabrics act as a barrier against diseases like dengue fever, yellow fever or Zika.
STINGbye items are suitable for people of all ages and are perfect clothes to enjoy outdoor activities or trips to areas exposed to mosquitoes and other vectors in complete safety.
SILVERSHIELD is the most advanced silver-based odour control technology on the market, offering highly effective, durable and long-lasting odor control for today’s consumers. SILVERSHIELD was developed as a result of Microban’s years of expertise in creating innovative, sustainably-focused and highly-effective odour control solutions for textiles that eliminate odors before they start.
Effective in various applications such as activewear, apparel, towels and bedding SILVERSHIELD combines the antimicrobial power of silver with Duralink, an innovative bonding system that increases treatment durability and product lifespan. While many silver treatments are applied to fabric, only SILVERSHIELD is chemically bonded to the fabric, ensuring longer- lasting effectiveness.
STORM COTTON technology is a water-repellent finish for cotton that offers protection from rain and snow, while maintaining the natural comfort of cotton. The STORM COTTON™ finish offers improved performance over typical durable water-repellent treatments by maintaining excellent repellency performance throughout the life of the garment and does not inhibit cotton’s natural ability to breathe.
Many water-repellent treatments inhibit a fabric’s ability to breathe and transfer moisture vapor effectively. STORM COTTON technology does not affect the natural ability of cotton fabrics to breathe and keep you cool. Although it repels liquids, the finish still allows moisture vapor to pass through the fabric where it can dissipate into the environment, naturally keeping you more comfortable.
STORM DENIM technology is a water-repellent finish for cotton that offers protection from rain and snow, while maintaining the natural comfort of cotton.
The STORM DENIM finish offers improved performance over typical durable water-repellent treatments by maintaining excellent repellency performance throughout the life of the garment and does not inhibit cotton’s natural ability to breathe.
Many water-repellent treatments inhibit a fabric’s ability to breathe and transfer moisture vapor effectively. STORM DENIM technology does not affect the natural ability of cotton fabrics to breathe and keep you cool. Although it repels liquids, the finish still allows moisture vapor to pass through the fabric where it can dissipate into the environment, naturally keeping you more comfortable.
Unlike water-repellent coatings typically applied to fabric, the STORM DENIM finish is applied in garment form. This allows for greater flexibility to apply various garment finishing techniques to achieve the desired styling and appearance of the finished product. The finish is applied through garment dipping or by metered spray application in a garment machine. The finish must then be cured at the correct time and temperature to ensure durability and permanence over the life of the garment.
What’s next in textiles?
Textiles sector has played a vital role in the industrial revolution. Particularly in India, the establishment of jute mills in Bengal and cotton mills in Mumbai area during pre-independence era is the witness to the importance of textiles. Textiles is not merely spinning cotton yarns or knitting jersey fabrics, textiles are in aerospace, defense vehicles, on the body, in the body, used for hygiene purposes, etc. Non-commodity textiles that are functionalized and have high performance capabilities are the next wave in textiles.
Functionalization in textiles can achieved in many different ways. Chemicals that offer hydrophilic, hydrophobic, flame retardant characteristics can be incorporated into and on to the textiles using organic and green chemistry principles. One early pioneer in this field has been Professor Dave Worley of US-based Auburn University. His work lead to the halamine based free chlorine release antimicrobial textiles. Nano particles were incorporated onto textiles that resulted in super hydrophobicity in textiles. One commercially successful technology in this field has been the Nanotex products. Nano titanium dioxide particles and nano clay particles are being evaluated to incorporate self-detoxification and flame repellency to textiles.
These developments, towards functionalization of textiles is very young field and traces its beginnings in the 1990s. Application of nanoscience to textiles began with the experimentation of spinning nanofibers. Researchers at the University of Akron in the United States re-invented the field of electrospinning of fibers to create nano level fibers. Since that time, this field has exploded with the development of different commercially viable production technologies such as spindle less electrospinning, centrifugal spinning, etc. Around 1990s, Professor Sundaresan Jayaraman of Atlanta-based Georgia Institute of Technology created the ‘Smart Shirt,†which was an early entrant in the field of wearable textiles. In fact, at that time, a separate field of wearable textiles within the textiles was nonexistent. Early on, functionalised textiles such as nano coated textiles and electronic textiles were deemed appropriate for single use applications. This field has caught the attention of mainstream consumers just a few years back. With this, pressure is on to the textile scientists and R&D organisations to make wearable and functionalised textiles practically suitable for consumers. In other words, durability, cost and wash characteristics are surfacing, which need greater attention.
India, so far has focused on multiple forms of nonwoven technologies and products from those. Predominantly these fit well with hygiene and medical textiles. There needs to be collaborative efforts among different Centers of Excellence to develop products from nonwoven technologies that can be available at retailer levels. While such an effort is needed, parallel effort has to be undertaken to initiate knowledge and pilot studies on the development of functional textiles such as wearable textiles. The power houses in basic sciences and engineering such as IISC, Indian Institutes of Technology and UICT-Mumbai have to be enticed to work with Textile Research Associations to focus on developing the next-phase of Indian textiles.
By: Seshadri Ramkumar, Texas Tech University