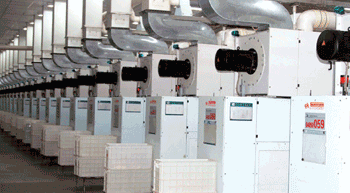
Sanyang: Largest Suessen end-User of EliTe®Compact System in China
February 14, 2015, was an unforgettable day for both Sanyang Textile and Suessen Germany, on which the two companies joined hand-in-hand and signed the great contract about the huge project of conversion of the existing 1,70,000 conventional spindles into EliTe®Compact. Ioannis Spiridopolus on behalf of Suessen, Xu Jianmin, GM on behalf of Sanyang Textile, and Lynn, Suessen Agent, were witnessing the great moment.
February 14, 2015, was an unforgettable day for both Sanyang Textile and Suessen Germany, on which the two companies joined hand-in-hand and signed the great contract about the huge project of conversion of the existing 1,70,000 conventional spindles into EliTe®Compact. Ioannis Spiridopolus on behalf of Suessen, Xu Jianmin, GM on behalf of Sanyang Textile, and Lynn, Suessen Agent, were witnessing the great moment.
Sanyang Textile is one of the targets and ideal customers that Suessen pursued. Sanyang Textile Co, well-known in textile industry worldwide, is located in Lijin county Shandong province PRC, and was established in 2003. With continuous and firm development in the past decade, Sanyang Textile boasts half-million compact spindles, about 400 sets of air-jet looms and 300 sets of two-for-one twisting machines from Germany now.
Sanyang Textile emphasises on pure cotton spinning and weaving, and has a yarn output of 30,000 tons each year, and cotton fabric capacity of 40 mn m per year. In 2015, Sanyang had won the honour of top 20 most competitive enterprises in China textile industry for the seventh consecutive year. In 2013, Sanyang was conferred by China’s State Administration for Commerce and Industry the honorary title of Famous Chinese Trademark.
Xu Jianmin, GM, Sanyang Textile, has expressed that high-quality production starts with the selection of most premium raw material, advanced equipment and latest production technology.
Xu said, “in order to gear up with market expansion and rapidly increasing requirements from our customers on our products, Sanyang must invest money in purchasing new machines and equipments and raw material, this kind of investment will continue in the years to come.â€
The conversion of existing 1,70,000 conventional spindles of Zinser 360 is amongst the ambitious investment plans. Suessen began to approach Sanyang and get the permission to participate in the competition of the conversion project in March 2014. At the beginning of 2014, Sanyang released the plan in textile industry, there were 5 local compact system suppliers participating in this project with trial machine respectively besides Suessen. It is obvious that the competition amongst suppliers of compact system was fierce, and the trial process lasted more than half a year. As mentioned that Sanyang focused on the pure cotton combed yarns ranging from 50s to 200s, the trial included variety of yarns, it is of course a time-consuming competition.
During the competition in that half a year, Suessen system achieved convincing results, which is the foundational condition that Suessen finally won the competition. It is very difficult to convert Zinser 360 from conventional spindles into compact because of the particularity of its structure. Nobody has dared to do this conversion in bulk on this type of machines before, but Sanyang Textile becomes the first in the world to convert 1,70,000 spindles of Zinser 360 in one shot. It really needs so great courage and unique vision to make the decision. The facts show that Sanyang Textile made a wise and right decision. This is the core technology that convinces Sanyang to choose Suessen at last. Xu mentioned that “Sanyang has made a lot of research and trial in several months to compare the different compact systems and yarns produced on them in our own spinning workshop, and then came to a conclusion that Suessen can provide the best technology and solutions for the modification of existing 147 sets of machines, and we Sanyang will definitely benefit from it to the largest extent. Sanyang Textile is the only enterprise in China and even the world to produce pure cotton super-finer yarns for bleaching with average yarn count 80s with all the existing compact spindles. It is also approved by China Cotton Textile Association as the only production base for premium pure cotton super-finer yarns for bleaching with guarantee. Suessen EliTe®Compact System has unique advantages without a parallel in producing super-finer yarns in terms of stability and consistency. All the high quality super-finer yarns produced on the 170,000 compact spindles and all twisted yarns from two-for-one machines are used for yarn-dyed shirts and mercerized T-Shirts with famous brands and for high-end home textiles with famous trademarks, 70 percent of the products are exported. High quality final products request the support with high technology. Therefore, we Sanyang decided to join hands together with Suessen to manufacture premium products to our customers.â€
During the installation, Sanyang and Suessen carried out a one-family working principle, the perfect coordination and cooperation contribute to the smooth accomplishment of the mission. Zhu Bingzheng, the purchasing manager played an important role in putting up platform and bridge for negotiation and installation and taking over the machines after successful conversion.
Chang Yu Hua, Production Manager, and Bao Chuan Jun, Equipment Manager, paid a great deal of help and efforts to this mission from beginning to the end. Frankly speaking, this conversion of 1,70,000 compact spindles is really a huge and challenging project for Sanyang and Suessen, but everything was well organized and under control. This mission has been completed smoothly according to the strictly designed schedule in 2015.