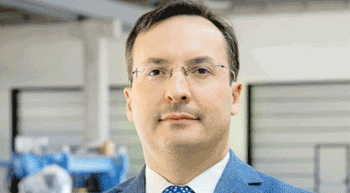
Santex Rimar Group’s weaving solutions
Santex Rimar Group’s weaving division was present in Shanghai with a Terry Jaquard loom under SMIT brand for first rate terry towels productions. Textile finishing division was present with Decofast machine under Sperotto Rimar brand. It was possible to see some fabrics treated by Santasynpact, Sanfor and Compacting process machine under Santex brand.
Santex Rimar Group’s weaving division was present in Shanghai with a Terry Jaquard loom under SMIT brand for first rate terry towels productions.
Textile finishing division was present with Decofast machine under Sperotto Rimar brand. It was possible to see some fabrics treated by Santasynpact, Sanfor and Compacting process machine under Santex brand.
Technical textile division will be present with Cavimelt P+P, the latest solution under Cavitec brand for coating and laminating, while Isotex which is working on a partnership with Covestro on water-based solvent free synthetic leather, was present with a Coating Head.
GS940 F technology—to produce first-rate terry fabrics—is characterised by the patented system of pile formation by slay motion that ensures the gentlest treatment of warp yarns called Dynamic Pile Control. The electronic pile control allows freely programmable pick ratio to create unique pile relief patterns.
The maximum loose pick distance of 24 mm and the freely programmable pile height enable to introduce unique effects such as waveforms. Thanks to GS940 F, customers can leverage on new competitive advantages towards customers. The aim is to find levels of treatment much more efficient than those of the atmospheric decatizing in continuous, up to exceed the results of the traditional back-decatizing machines.
Besides, the introduction of new fivers in the wool fabrics such as the elastomers destined to the informal clothing brought to the definition of new technologies requested by the new millennium and whose features are present in DECOFAST.
CAVIMELT P+P is a compact machine developed with the goals of precision, production and cost effectiveness in Hotmelt coating and lamination using an engraved roller. Integrated within the machine frame are both the un- and re-winder, accepting rolls up to 600 mm in diameter.
Conversion to the alternative tensionless contact unwinding mode is performed simply through removal of the quickly detachable brush expander rollers. All well-known adheseves in thermoplastic and reactive Hotmelts are applicable. Delivered pre-wired, assembled and tested, CAVIMELT P+P stands for Plug+Play because of short installation and commissioning time.
Isotex is a specialised supplier of coating and laminating lines to a great variety of industrial sectors, such as airbags, technical textiles, tarpaulin and medical adhesives, the industrial composites and many others.
With more than 100 years of activity, the Group has the experience to be innovative yet offer reliability, lower cost of production and environment friendly technologies. Santex Rimar Group is present in Italy, Switzerland, China and India and has more than 10,000 customers throughout the world.
Santex Rimar Group is focused on customers
On the occasion of ITMA ASIA 2016, Santex Rimar Group participated with all Group’s brands unified to strengthen the new mission of being the only reference partner for different solutions.
Santex Rimar Group has reached the perfect balance of deep knowledge, design and high quality throughout the production process to build a strong, long lasting and mutually beneficial relationship with customers, together with whom we share visions about developments, processes, productions, materials and fabrics.
“With almost 30,000 machines installed worldwide, we are constantly visiting customers and listening to them. Our goal is to provide custom solutions in terms of quality and sustainability in order to enable them to build stronger relationships also with their customers: our customers’ success is our success,†said Stefano Gallucci, Santex Rimar Group CEO, and concludes: “Santex Rimar Group is flexible, integrated, sustainable and above all, expert on customers.â€
The Group keeps on investing in Qingpu (Shanghai) based production site to fulfil the demand of such an important market like China. Also thanks to the local management, Chinese productions are continuously growing and improving and machines’ level upgraded. The strong commitment to China has been confirmed also with the establishment of New Smit China, under the lead of Rock Luo, to strengthen customers’ support.
As a technology partner for knitted, woven fabrics, nonwovens and green solutions the Group started as different companies that in 2015 have evolved into Santex Rimar Group: Cavitec and Isotex lead the technical textiles machinery market; Santex and Sperotto Rimar produce machines for textile finishing; Solwa provides eco-friendly machinery for water treatment, food dehydration, agribusiness sector and industrial waste management. With the entrance of SMIT, the Group has recently become a solution provider also in the weaving sector.
Simone Rancan is new CEO of SMIT
Established in 1938 and worldwide recognised as a forerunner in weaving technology, SMIT officially joined Santex Rimar Group in April 2016. The brand new SMIT production site is already working in Trissino (Vicenza) where Group’s headquarters is based and new Chief Executive Officer has been nominated: after several years of experience in the textile world, Simone Rancan officially joined Santex Rimar Group and assumed the role of SMIT CEO. “Simone Rancan knows textile business and will move SMIT forward with the speed required to capitalize on opportunities. He has a great ability to connect with employees, partners, customers and global leaders. Rancan’s vision, strategy and execution is exactly what SMIT needs as we enter our next chapter, which I am confident will be even more impactful and exciting than before†said Stefano Gallucci, Santex Rimar Group CEO.
Simone Rancan started his career in Sperotto Rimar, afterwards has worked in important players in the sector of weaving machines and he spent the last four years in spinning machinery with Rieter: “I am honored by the unique chance provided by Santex Rimar Group to lead SMIT on its path forwards. Strong and well known technological foundations, coupled with the unique knowledge of a wide range of textile processes available inside the Group, provide the base for moving ahead in full confidence. New production concepts have been implemented at record speed, spare parts deliveries have already started six months ago and first looms have been delivered this month thanks to the trust of our customers who are the focus of our actions and effortsâ€.
SMIT SMART PLATFORM is a structural architecture concept involving the whole machine project – mechanics, electronics and communication systems – to provide the most advantageous weaving machine configurations to produce high quality fabrics for any sector, widening weaver’s market access.
For further information: Santex Rimar Group, www.santexrimar.com