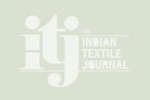
ROTORCRAFT’s futuristic solution
The Rotorcraft presented a revolutionary new ring spinning frame. Named Next Generation Spinning (NGS®), this frame meets all the requirements of a 21st century mill. In order to avoid any human and operating errors that are common with ring frames today, the NGS® frame has no setting screws whatsoever.
The Rotorcraft presented a revolutionary new ring spinning frame. Named Next Generation Spinning (NGS®), this frame meets all the requirements of a 21st century mill. In order to avoid any human and operating errors that are common with ring frames today, the NGS® frame has no setting screws whatsoever.
The setting of the drafting systems is achieved by the use of exchangeable elements in different colours. The distance between the drafting system and the spinning ring remains constant during the entire operation. Bottom aprons are replaceable individually while the frame is running. A low-pressure channel is built in between the working elements of both sides of the frame, rather than above the frame. The channel is large enough to fit the suction tubes as well as the low-pressure elements for pneumatic compact spinning. The two sides of the frame can work completely independently, and all bearings of the working elements are sealed for life.
A large international audience visited the Rotorcraft booth, the common overwhelming feedback from technical experts and mill owners sounds like: “We have seen the future of ring spinningâ€, “NGS is the game changer for the next decade.â€
The next generation of Compact Spinning Systems named Green Compact (pat.pend.) was also on display. The system attains the yarn quality improvements introduced by the first generation of compacting systems, while saving $6-8 in energy cost per spindle per year. It therefore performs considerably more economically and sustainably compared to old generation compacting systems.