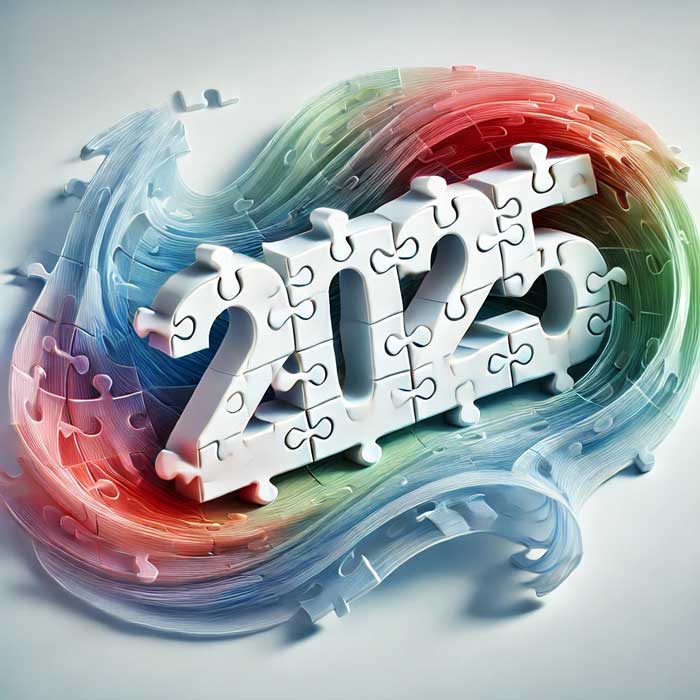
Road Ahead to 2025
The Indian textile industry faced challenges in 2024 with wars, demand contraction, and regulatory changes. Divya Shetty delves into whether 2025 could turn the tide, offering a brighter path for the industry’s future.
2024 was one of the most challenging years for the Indian textile sector as per the industry. Several factors, both domestic and international, contributed to this instability.
Talking about domestic concerns, Gurudas Aras, Independent Director, shares, “Cotton prices in India were 10 to 15 per cent higher than international prices for most of the year. This significantly reduced the competitiveness of the entire value chain, from yarn to fabric to garments. Secondly, in October 2023, the government introduced the Quality Control Order (QCO) for polyester fibres and yarns. While the intention behind the QCO was good, aiming to allow only compliant, high-quality products from abroad, it affected the polyester value chain. The Surat sector, in particular, which depends heavily on polyester yarn imports, especially from China, was severely impacted. As a result, the entire value chain in this sector faced difficulties. ”
Additionally, on-going global conflicts and wars have driven up logistics and shipping costs, further hurting exporters.
Textile chemicals is also one of the most important part of the textile value chain a it contributes approximately 5-10 per cent of the overall manufacturing cost. Umasankar Mahapatra, Managing Director, Pulcra Chemicals, view 2024 as a mixed performance for the chemical industry. He says, “India has a significant advantage in the textile chemical supply chain compared to neighbouring and competing countries. But on the demand side, certain sectors, like denim, have underperformed for the past two to three years, even before and after COVID-19. Capacity utilisation in the denim segment remains low.”
Machinery, which serves as a backbone of the industry, had certain segments that performed well while others did not. According to Ashok Juneja, Director – Sales & Services, Saurer Textile Solutions, “Spinning industries are operating at less than 75 per cent of their capacity. Similarly, the textile machinery sector is also struggling, running at approximately 50 per cent capacity in some regions of India. This trend may vary across segments, but the spinning industry is in particularly poor shape. In contrast, the weaving and processing segments seem to be performing relatively better. Segment-wise, weaving and processing show more stability compared to spinning. However, even the garment sector is not thriving due to a lack of new greenfield projects and reduced order intake, with industries operating at just 50-60 per cent of their capacity. This underutilisation, coupled with rising costs of raw materials and production, posed significant challenge last year.”
The spinning sector has suffered the most. The industry has faced overcapacity, with utilisation at around 70 to 75 per cent. Fluctuating cotton prices have also negatively affected yarn prices, leading to a subdued yarn market.
Gurudas Aras, Independent Director
Raja Shanmugham, MD, Warsaw International, however hints at brighter prospects for the industry looking at the delivery of past few months. He says, “2024 has been quite challenging compared to previous years. However, in the past few months, we have started seeing a ray of hope due to various reasons, though the situation is still not as promising as in 2022. The industry is just beginning to recover.”
Despite having abundant raw materials and a large population, India is struggling to establish itself as a global leader in textiles. Avinash Mayekar, Managing Director, Suvin, encourages the industry to observe and learn from truly inspirational countries and clusters in order to stay ahead. He tells, “Tiruppur has done remarkably well without much help from either the state or central government. The cluster has created the roadmap, built the infrastructure, and designed everything through cooperative efforts. However, it’s essential to remind the government that this is their responsibility. Policymakers must take on this work and support the industry.” He further adds, “When I visited China, I noticed two significant points regarding labour efficiency. First, in Chinese apparel parks, workers remain focused on their tasks throughout the day. In contrast, in India, factory visits often reveal a lack of focus, with workers distracted by the arrival of visitors. In China, the apparel industry is their bread and butter, which drives their discipline. Second, the infrastructure in China is created proactively by the government. Industrial parks are developed first, and then manufacturers establish their facilities there.”
The roadblocks of 2024
India’s textile and apparel (T&A) sector targets $350 billion in annual revenue by 2030, but recent challenges have raised concerns about achieving this goal. First, let’s discuss about the global uncertainty. As per Aras, wars are detrimental to businesses and industries. He explains, “This war has significantly increased energy prices. Europe, a major importer of Indian textiles, has seen energy costs rise exponentially—reportedly five to six times higher during the peak of the crisis. When households face skyrocketing electricity bills, textiles naturally fall to the bottom of their purchasing priorities. Consequently, textile consumption in Europe and other EU countries has declined over the past one or two years, impacting Indian exports, as Europe and the US together account for approximately 75–78 per cent of India’s textile exports. The US market has also witnessed a significant drop in textile consumption due to higher inflation.”
Panipat is benefiting from the growth in home textiles, particularly microfibre bedsheets, which are gaining traction in both domestic and export markets.
Umasankar Mahapatra, Managing Director, Pulcra Chemicals
Global conflicts have disrupted businesses across nations, leading to a sharp rise in shipping costs and container shortages. Longer shipping routes have increased transit times, further straining the efficiency of Indian manufacturers. India’s turnaround time for goods is already higher than competitors like Bangladesh and Vietnam, who are more efficient in meeting delivery timelines. As a result, India has lost a portion of its market share to these countries, despite having the entire value chain and raw materials within the country.
Shanmugham adds, “We have a strong foundation in both cotton raw materials and man-made fibres. However, we are significantly costlier compared to other countries when it comes to man-made fibre-related products. This requires re-evaluation by both manufacturers and policymakers to create a level playing field for the growth of this segment within our manufacturing activities.”
Juneja states that imports must be reduced, and there is a need for self-reliance as he states, “We have an approximately Rs 250 billon machinery market in India, and out of that, Rs 150 billion is imported. About 60 per cent of the machines are imported. There are two concerns as to why we could not manufacture these machines locally. The first is technology, and the second is pricing. Whatever we manufacture, we are not able to keep the prices under control. Ultimately, we are all from the same industry. The price-to-product performance ratio has to work. The price must be reasonable, and the product has to perform.
The profit margins in the spinning market are very thin. After Covid, the industry experienced some improvement, but the margins remain narrow. Only those who are highly competitive can survive.
Ashok Juneja, Director – Sales & Services, Saurer Textile Solutions
When asked about the new machinery safety rules act which will be implemented from August 2025, Juneja says, “A lot of non-standard machines have been entering India, and this needs to be addressed. Initially, these regulations will apply only to embroidery and weaving. At the moment, there are no embroidery machinery manufacturers in India, but weaving machinery manufacturers do exist. By August 2025, these manufacturers will need to comply and register. The intention of the government is commendable—all machines should adhere to standard norms. However, the primary concern is implementation. The execution of these regulations will be key, and we need to see how effectively they are enforced.”
While the textile chemical industry is self-reliant India, Mahapatra feels that we lack in raw materials. He mentions, “Although we are manufacturing most of our auxiliaries, specialty chemicals, dyes, and pigments in the country, there is still some import dependency for key raw materials, such as basic silicone oils, oleochemicals, and palm oil derivatives, which come from Southeast Asia. While the final formulations are done locally, these specific raw materials are still imported. The advantage of local manufacturing lies in close collaboration with mills and end-users. This collaboration is crucial because the requirements in this industry change rapidly. Unlike capital investments that remain static for 10-15 years, in the chemical space, there are constant changes every season or month. These include new finishes, substrate variations, product mixes, and colour trends. Technical service plays an essential role alongside supply, as manufacturers need to work closely with users to meet their evolving demands.”
Government policymakers need to act decisively to support the industry and seize a greater share of the global market. In an open-market situation, we must strengthen our position, but unfortunately, we are being outperformed by smaller nations like Bangladesh, Vietnam, and Cambodia.
Raja Shanmugham, MD, Warsaw International
India is largely compliant with environmental norms, especially for premium European and US brands. However, compliance requirements are becoming more stringent. For instance, the CBMA (Carbon Border Mechanism Adjustment) is being implemented soon, initially focusing on energy-intensive sectors like cement, steel, iron, and aluminium. While consumer goods are not yet covered under CBMA, new regulations such as the Eco Design for Sustainable Products Regulation (ESPR) have been introduced, covering textiles.
The ESPR regulation focuses on not only product certification but also the impact at the user and consumer levels. It examines whether products are repairable, contain recycled content, and meet other sustainability criteria. Previously, certifications primarily assessed toxicity, banned substances, and manufacturing environments. Now, end-of-life treatment and consumer-level impacts are also being addressed.
While companies are now striving to comply with sustainability standards and obtain certifications, smaller businesses are finding it challenging to meet these requirements. Shanmugham adds, “This industry is dominated by micro and small industries. Adhering to all these certification processes is a challenging task because everything needs to be certified by a third party. These third parties charge exorbitant fees, and goods are only accepted in the markets based on certification. This creates a very challenging situation for the survival of these micro and small industries. Everyone must equip themselves, but if the government truly wants to support these industries, they need to devise an exclusive policy, at least for the next two to three years, to help them adapt to the standards demanded by the western or global markets.”
The budget we’re hoping for
According to the industry, last year’s budget was seen as a missed opportunity for the textile sector, as it failed to address a list of expectations. Aras opines, regarding textile and garment exports, the government extended the Remission of Duties and Taxes on Exported Goods (RoDTEP), which has really helped exporters cover some of the costs that are unnecessarily added due to state levies and other factors. I believe the government should extend this further for at least one to one and a half years until our exports become competitive, otherwise we will become uncompetitive.”
He further adds, “In Europe and the USA, sustainable manufacturing is a demand for the next few years. However, those investing in green manufacturing are not being rewarded. I would suggest that some form of incentivisation for investments in sustainable manufacturing practices would motivate people to invest in these initiatives. Thirdly, as I have been repeatedly saying, majority of our industry is in MSMEs (Micro, Small, and Medium Enterprises). Therefore, there needs to be a policy that helps MSMEs become cost-competitive and make their goods exportable.”
Additionally, the industry expects a wider reach of the PLI scheme. Last year the PLI scheme was restricted only to man-made fibres and technical textiles. This limited scope led to fewer takers for the scheme, meaning it hasn’t been very successful.
Technical textile industry is indeed on a growth path. However, the biggest challenge it faces is the non-availability of performance fibres or technical fibres, as they are not produced in India, and there are high import duties on them. Even for active wear, sportswear, and some specialised fibres, if these could be imported under concessional duties, it would open up a significant opportunity for high value addition, and India could compete globally.
Juneja suggests, “The textile machinery market in India is worth Rs 250 billion, while we are importing machinery worth Rs 500 billion. This means there is definitely a big scope for substituting imported machines. Handholding from the authorities is required here. For example, last time they gave some grants to develop shuttle less looms, and machinery has definitely come in. For such initiatives, an initial push from the government is needed to develop substitutes for imported machinery so that they can be used for these purposes. There is definitely scope in the machinery market for indigenous products and substitutes for imported machines. However, the machines that come in should be of high technology, not just of low standards or something like that.”
A policy supporting this industry would be beneficial. The government should consider setting up a centre of excellence for textile chemicals. There is a lot of innovation that can happen in this field. Unlike other sectors, the textile industry should also have centre of excellence across the country for various product categories and applications, also a centre for specialty textile chemicals will be helpful to boost this sector.
Mahapatra adds, “Water is a significant input, and we are all talking about pollution. Can we really modernise STPs and CETPs and invite more private players into this domain so that we have proper functioning of the CETPs? It should not just be about having a CETP but ensuring it operates in its true spirit. I think STPs can help by providing treated water to the industry, so we don’t use any blue water. This will improve the overall environmental score for both the country and the industry. The treated water from the CETPs should be used properly so that there is no need for JDL, which is highly energy-intensive and costly. Every cubic meter of treatment adds a significant cost, making many industries unviable.”
In India, even though there are MIDCs and state industrial corporations, infrastructure is only developed after industries show interest, leading to delays.
Avinash Mayekar, Managing Director, Suvin
Charting the course for 2025
It is believed that India missed the bus with China Plus One policy. However, the industry is quite hopeful about Bangladesh Plus One. Aras says, “First and foremost, you should not rely on someone else’s weaknesses to grow. I believe we need to build our own strengths; only then can growth be sustained in the long term. Personally, I believe the Indian industry is at an inflection point. Bangladesh presents one opportunity, but apart from that, if you observe the US market, there is a clear normalisation of apparel and textile inventories from China. Recent data from the past two to three months shows an increase in consumer spending.”
Trump’s victory has also fuelled optimism in the minds of the textile professionals as the U.S. plans to replace 70 per cent of its Chinese textile imports with goods from Bangladesh, Vietnam, India, and Cambodia. How India positions itself is entirely in our hands. Vietnam has reached its capacity limits. India, on the other hand, is steadily progressing in man-made fibres and blends. Thanks to PLI (Production Linked Incentives) that we are gradually expanding our capacities in garment manufacturing, setting the stage for long-term growth.
Mayekar highlights that the technical textile sector has the potential to enhance the prestige of the Indian textile industry and help it emerge as a global leader. He says, “The technical textile sector is growing in double digits. When it comes to a developing country like ours, we will be consuming more technical textiles. You can see their consumption almost everywhere in India in various forms and applications. So, it will be one of the major contributors to the consumption of technical textiles. This growth will significantly increase the consumption of fibres as well as various technological fabrics that will be produced here.”
Apart from the growth in manufacturing and exports, many European manufacturers have expressed interest in starting manufacturing operations in India. Several have already established joint ventures in the country over the past two to three years. This trend is expected to continue, as manufacturing typically shifts to consumption markets. With rising costs in Europe, many ventures are likely to relocate to India. The technical textile sector is projected to grow at a much faster rate than the commodity textile industry.
Additionally, the automotive industry has already established a significant presence in India, with most automotive parts now being manufactured domestically. This has become one of the major industries driving growth in the sector.
Another significant opportunity this year is the Free Trade Agreement (FTA) with the UK. The news indicates that discussions have resumed following the formation of the new UK government. It’s been reported that the UK importers have started requesting samples in anticipation of the FTA.
To capitalize on these opportunities, the industry must address several key issues. The first priority is to build capacities, as there is currently a notable deficiency in this area. Additionally, developing infrastructure and enhancing cost competitiveness, which continues to be a significant challenge, are essential. Lastly, addressing sustainability concerns is critical, as buyers are increasingly sensitive to issues such as human rights violations, child labour, and environmental abuses. Several industry leaders have already taken proactive steps to overcome these challenges. Meeting these critical requirements could turn 2025 into a defining moment, positioning Indian textiles for unprecedented growth and global dominance.