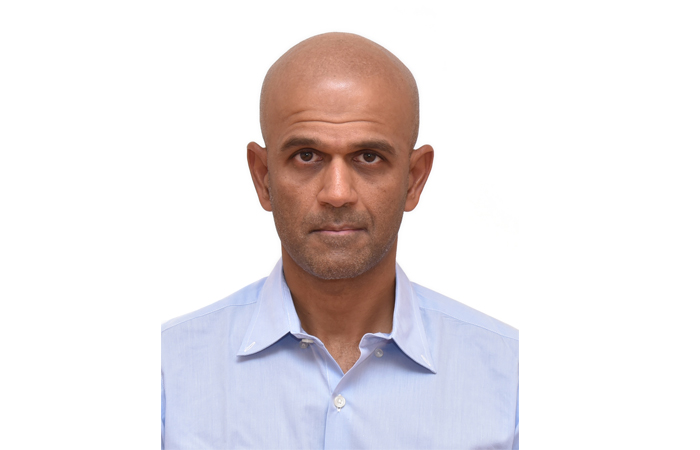
R&D is central to everything that LCC does: S Harishankar
In this interview with Rakesh Rao, S Harishankar, Joint Managing Director, Lakshmi Card Clothing, highlights industry trends and LCC’s future growth plans.
Card clothing plays a vital role in the carding of textile fibres, a crucial step in the spinning process that ultimately enables the production of yarn across an endless range of fibre types. Lakshmi Card Clothing Mfg Co Pvt Ltd (LCC) has emerged as the leader in this sector by providing top-tier solutions. In the conversation with Rakesh Rao, S Harishankar, Joint Managing Director, Lakshmi Card Clothing, highlights on the industry trends and LCC’s future growth plans.
How has Lakshmi Card Clothing evolved over the years?
Lakshmi Card Clothing, established in 1960 in collaboration with a Swiss card clothing manufacturer, has grown steadily over the past six decades. The company’s early years were marked by the transfer of international know-how and technology, which laid a strong foundation. As we matured, we developed our own in-house R&D capabilities and began manufacturing independently. Today, we are proud to be a key player in the Indian market, with more than 50 per cent of the yarn produced in the country being processed using card clothing and accessories supplied by us. This demonstrates not only our technological excellence but also our widespread market acceptance.
Our journey is one of transformation—from a collaborator to a self-sustaining manufacturer and now a leader in precision textile engineering. Our facilities have been upgraded periodically to accommodate newer technologies and meet the evolving demands of modern carding systems. Our focus on consistent quality, product innovation, and customer satisfaction has enabled us to emerge as a preferred supplier for both domestic and international markets.
Can you highlight some of the key milestones achieved?
Initially, we focused on producing flexible card clothing, which was widely used in earlier generations of carding machines. However, as the industry evolved—with carding machines becoming faster and wider—the demand shifted towards metallic card clothing. Our ability to adapt quickly to these market changes was a significant milestone.
Today’s modern spinning mills operate high-speed 60-inch wide carding machine, compared to the earlier 40-inch models. This leap has required enhanced metallurgical solutions, automation, and upgraded manufacturing infrastructure. Our commitment to staying ahead of the curve has led to the successful development of our patented CENTURA3F SERIES (Fiber Friendly Finish). This new generation of cylinder wires, doffer wires, stationary flat tops, and revolving flat tops is designed to deliver optimal performance, efficiency, and precision. It is a product of our dedicated R&D efforts and has been widely adopted in the market. Our 3F SERIES is a market leader, thanks to its proprietary design and patent status.
How crucial is R&D to your success and the Indian industry at large?
R&D is the backbone of any precision engineering company, and in our case, it is central to everything we do. The demands placed on card clothing components are extremely specific—they need to perform under high-speed conditions with microscopic tolerances. Continuous improvement and product customisation are only possible with a robust R&D foundation.
We believe that risk-taking is inherent in any successful R&D programme. While not every experiment may yield immediate results, the long-term benefits of a well-funded R&D initiative are substantial. In comparison to our global counterparts, Indian companies still invest relatively less in research and innovation. Increasing R&D spend is not just a competitive requirement but a strategic necessity for Indian manufacturers to remain relevant on the global stage.
The government is promoting manmade fibres (MMF). How do you view this opportunity?
Our customer-centric philosophy ensures that we are constantly evolving in line with market requirements. In recent years, we’ve seen significant volatility in cotton prices, prompting many of our clients to shift toward manmade and regenerated fibres. This trend is not just a domestic shift but is also reflective of global consumption patterns, especially in fashion and fast fashion sectors.
Regions like Panipat, for instance, are becoming hubs for recycled and regenerated fibres derived from used garments. This movement is part of a larger global sustainability push, especially among younger consumers who increasingly demand products made from environmentally responsible sources. Manmade fibres and blends are gaining traction, particularly in export-driven markets where sustainability credentials play a critical role in procurement decisions.
Recognising this shift, we have introduced card clothing and accessories specifically engineered for MMF and regenerated fibre applications. These innovations ensure high performance and durability, even with the varying physical properties of alternative fibres.
What is the contribution of exports to your business, and how do you plan to expand it?
Currently, exports account for around 20–25 per cent of our total turnover. While our manufacturing capacity can support higher volumes, global market demand, especially in spinning, has been somewhat affected by economic slowdowns in key regions such as Bangladesh and Indonesia. Despite these challenges, we see signs of stability returning in markets like Vietnam, and we remain optimistic about recovery.
To boost our exports further, we are exploring partnerships in newer geographies and working to establish a more direct presence in high-potential regions. Our goal is to strengthen brand visibility and create local support systems to serve international clients more effectively.
How has Coimbatore’s evolution contributed to India’s textile industry?
Coimbatore, along with Erode and Tiruppur, has built a world-class textile ecosystem. The region is home to over 5 million spindles, making it a critical spinning hub. Tiruppur, in particular, accounts for nearly 40 per cent of India’s knitted garment exports.
Beyond manufacturing, Coimbatore also boasts a strong engineering base, including companies like LMW, Lakshmi Ring Travellers, and ourselves. The synergy between textile production and textile machinery manufacturing has created a self-reinforcing ecosystem. This region continues to produce skilled graduates who contribute to the textile industry not only in India but across global markets.
How do you see Coimbatore growing from here?
While Coimbatore retains its leadership position, certain challenges must be addressed. Raw material costs are relatively higher in this region, and the availability of skilled labour is becoming increasingly limited. Moreover, today’s youth are more inclined toward careers in IT rather than traditional manufacturing.
To adapt to these trends, we are expanding our technical service network across major textile hubs such as Panipat, Ludhiana, Madurai, and Rajkot. These centres offer value-added services and technical support to mills, which are otherwise struggling to find skilled manpower.
Additionally, the region is witnessing a gradual shift toward fibre blends and regenerated materials, a change driven largely by export market demands. This evolution will play a critical role in Coimbatore’s future growth trajectory.
Are technical textiles gaining traction in the industry?
Yes, technical textiles are seeing a steady rise, especially post-COVID. The pandemic highlighted the need for application-based textiles in areas such as healthcare, filtration, automotive, and geotextiles. While this segment remains underdeveloped in India, it offers immense potential for value addition and import substitution.
For companies like ours, which already operate at the intersection of material science and mechanical engineering, the rise of technical textiles presents an exciting frontier. By investing in specialised R&D and engaging with end-user industries, we aim to contribute meaningfully to this emerging space.
What are your plans for LCC’s next phase of growth?
While we continue to lead in the carding segment, diversification is a key component of our growth strategy. One of our most promising initiatives is our entry into combing machine accessories, including top combs and circular combs. These products are currently in the final stages of field trials and are scheduled for a full-scale launch at ITMA Asia 2025 in Singapore.
In addition, we are exploring other high-precision engineering applications. A prime example is our Radio Frequency (RF) drying machines, which were initially developed for textile applications. With India’s food processing sector experiencing exponential growth, we have started customising these RF machines for food-grade drying and disinfestation processes. This pivot reflects our long-term strategy to broaden our market base while leveraging our core engineering competencies.
Do you have any specific growth targets?
While the card clothing market is mature and currently experiencing a response to the global economic recession, we managed to achieve a 4–5 per cent growth rate last fiscal year. This is a commendable performance given the market conditions and underscores our commitment to innovation and market responsiveness.
Going forward, our focus will remain on expanding into adjacent segments like combing machine accessories and RF drying systems. These areas offer higher growth potential and can help balance the cyclical nature of our core business.