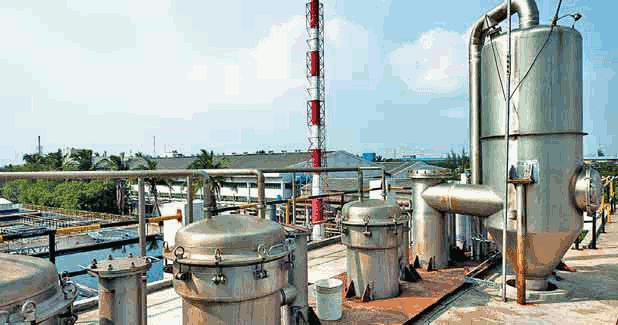
Protecting water quality
On average, an estimated 100 to 150 litres of water is needed to process 1 kg of textile material, with some 28 billion kilos of textiles being dyed annually.
On average, an estimated 100 to 150 litres of water is needed to process 1 kg of textile material, with some 28 billion kilos of textiles being dyed annually. A reliable wastewater treatment is extremely important for the production of textiles, finds an exclusive ITJ cover story.
The textile industry is believed to be one of the biggest consumers of water. In conventional textile dyeing, large amounts of water are used both in terms of intake of fresh water and disposal of wastewater. In India, zero liquid discharge (ZLD) or near ZLD may not be happening in full throttle like in developed economies. A reliable wastewater treatment is extremely important for the production of textiles. When the present Indian government ushered in a draft regulation, which will make ZLD mandatory for textile units having waste water discharge of more than 25 KLD (kiloliters per day), the issue of water pollution came out again. As you know, textile dyeing contributes 20 per cent to industrial pollution and is one of the biggest reasons for the closure of many textile units in Tiruppur (Tamil Nadu) following High Court order a few years ago.
Wastewater is a major environmental impediment for the growth of the textile industry besides the other minor issues like solid waste and resource waste management. This directly and indirectly has an impact on aquatic life, and it may also be lethal to certain forms of marine life due to the occurrence of component metals and chlorine present in the synthetic dyes. So, this textile wastewater must be treated before their discharge. Major ongoing developments aim at a minimization and rationalisation of water consumption and at the development of cost-effective treatment units for advanced wastewater treatment for increasing the degree of water loop closure. Because of lower water quality demands, water is often reused in washing and desizing processes.
Speaking on the importance of ZLD, Ajay Popat, President, Ion Exchange (India), said, “ZLD is very important for the textile industry because it requires huge amount of water to manufacture its products. Waste is generated in large volumes, which need treatment before it is discharged. Since water consumption is very large, it is prudent to do ZLD or near ZLD by which the industry is able to meet the discharge norms. For some companies, this becomes a source of water as municipal corporations give priority to agriculture or consumers. Also the price at which the water is supplied by the municipal corporations to the industry is very high with a regular hike every year. Hence it makes sense to recycle water.â€
Bhushan Zarapkar, Director – Operations, A.T.E. Huber Envirotech (AHET), had this to say: “With India’s freshwater sources depleting fast, we firmly believe that wastewater is our best source of water. Recycling wastewater using modern treatment technologies will go a long way towards alleviating the current scarcity of water. Our comprehensive and cost-effective wastewater treatment and recycling solutions are the result of continuous process development. A.T.E.’s AAA® technology is a proven solution for treatment textile wastewaters that enhances biological treatment efficiency and minimises sludge generation. Contrary to conventional wastewater treatment processes, AAA® reduces both chemical consumption and sludge generation, while maintaining consistency in the treated effluent quality. In addition to AAA®, A.T.E.’s state-of-the-art SUFRO and MEE technologies enable wastewater recycle and ZLD for textile wastewater treatment.â€
Rohan Desai, Director of Enviro Analysts & Engineers, said, “Why ZLD has become so famous? It is because; there is CETP all over Maharashtra which does not cater to all the plants. Imagine the CETPs were made in 1990s with the capacity of 25 MLD. Currently the minimum requirement is almost 100 MLD. Tiruppur became the first textile cluster in India to achieve ZLD in their units. It has not reached that level yet. It will take time.â€
Is complete ZED a reality in India? Desai said, “Of course it is. The biggest issue that comes is the trust factor. A lot of suppliers have become consultants now. We are design consultants who provide turnkey solutions. There are only consultants who does only supply but also provide designs and put the plant there with low cost. That is the biggest issue right now. Cost is also the biggest issue right now.â€
“Textile industry produces huge volume of wastewater containing various chemicals used in dyeing, printing, and various other processes. Discharging of untreated effluent from textile industries is highly harmful to the environment, causing pollution to nearby water and soil. To get rid of this problem, ZLD plants are installed which plays an important role in textile or industries by protecting environment from the harmful effect of wastewater. ZLD greatly minimises the damage done to the environment and also results in benefits for the industry,†said Vinod Kumar Gupta, Managing Director of Dollar Industries.
Avinash Mayekar of Suvin Advisors describes: “ZLD means zero or no discharge of wastewater or any liquid effluent from a factory to outside surroundings. The entire wastewater generated due to processes inside a factory has to be treated and recycled back into the factory! ZLD – it is not a single system but a combination of various treatment processes which may vary from industry to industry. This is due to the fact that the type to technology depends upon the quality of effluent and process water quality requirement.â€
The Zero Discharge of Hazardous Chemicals (ZDHC) is a foundation that puts all its efforts into a mission of life-saving exercise — in eliminating, nay, minimising to a near-zero level the dangers that chemicals pose, right from its source, especially in the production of textiles and apparels.
“There is a misconception in the minds of many. ZLD is not to be confused with ZDHC, which is a holistic set of management. It starts with the input of chemicals and ends with the output of the product. It is a sustainable chemical management and practices. ZDHC is not a certification as many people think so,†says Prasad Pant, South Asia Director of The ZDHC Foundation. Pant who has taken over the directorship of South Asia of the foundation a little more than a year back, explained, with ease and aplomb all the objectives and programmes of ZDHC.
The ZDHC Programme is a continuous set of action, aimed at almost eliminating the hazardous chemicals that go into the manufacture of products including textiles and apparels. “The ZDHC Programme starts with the purchase of chemicals in a factory, storing and handling them, then using them and finally disposing of them. It is concerned with the wet processing side of textile production but the scope just goes beyond just products.â€
Can we achieve zero discharge of hazardous chemicals? Says Pant: “The target is aspirational. Traces of chemicals can never be totally eliminated, but we can achieve near-zero and remove all the toxicity from the textiles. In the second phase of action, the focus shifted to the tier II, to laundries and tanneries where there is a huge discharge of chemicals. For the brands it was a complex process since they have a variety of supply chain and it was difficult to keep tab. Initially, it started with some brands including Nike, Adidas, Puma, CNA and H&M. In 2015, it was decided to have a structured organisation, a legal entity. It was registered in The Netherlands, where the laws for NGOs were strong and reliable and where Green Peace is also registered.â€
Ion Exchange offers products like softeners to reduce hardness from groundwater, which is contaminated with calcium and magnesium. If the total dissolved solid (TDS) is high, we offer reverse osmosis (RO) systems to reduce salinity. The company also offers demelanising plants where the industry requires very high quality water – both for the process as well as boilers. We offer speciality water treatment chemicals that are used in cooling towers to improve its performance and efficiency. We provide the entire package of cooling towers and boiler treatment chemicals.
Said Popat, “Ion Exchange also offers speciality chemicals—coagulants and flocculants—as well as colour removal polyelectrolytes for waste treatment. Apart from these, we also offer certain process chemicals that are used for thickening emulsions. Ion Exchange resins are not only used for softening and demelanisation, but also used for colour removal. These resins compliment colour removal through chemical and biological processes. We supply a range of biological processes – aerobic and anaerobic. Our membrane system—both spiral and distant tube ROs—can be used to enhance maximum recovery.â€
According to Desai of Enviro Analysts & Engineers, “If you have any industry coming up, then we provide environmental engineering solutions – it can be wastewater or it can be even environmental clearance, etc. We have been accredited by MoEF. We do layer studies; we represent them in front of the Ministry. Otherwise, we also provide system solutions to high-rise buildings. It can be rainwater harvesting, solar, etc. Industry-wise, we provide turnkey projects for wastewater treatment. We have a monitoring system and we have a laboratory which do all the analysis related to water and soil.â€
The ZDHC movement is expected to give a push to innovation. Says Pant: “The ultimate aim of ZDHC is innovation because companies will be exploring to identify less harmful alternatives to existing harmful chemicals. Today, there are still a lot of hazardous substances like hydro-sulphides, which cannot be totally eliminated. But they have to be safely handled. Efforts are on to find an alternative. Another product is the oil- and water-repellent finishes, which use PFCs that are harmful. Companies like DuPont and many others have decided to stop any compound containing PFCs by 2020. What is the alternative? There are alternatives but nothing has matched the ones containing PFCs. So, this has kickstarted a move to find alternatives, with many company involving research and development. Another chemical is DMF – Dimethylformamide, which is used in the making of PU soles in shoes. Everyone knows it is a proven carcinogenic material, but there is no alternative. A Chinese company has recently come out with water-based PU, which is totally free of all harmful substances. This is how innovation is happening.â€
After dealing with output, then comes waste water. “For this ZDHC has made guidelines for wastewater discharge and sludge. The factories supplying to the big brands have to test the wastewater discharge, and these will be uploaded on the Gateway, and the brands can monitor the reports.â€
Other services of ZDHC include a training academy, which will educate those joining it to evaluate the dangers of chemicals by testing and finding results. All knowledge on chemicals used in the various processes of textile industry will be imparted to them. We develop the content for the trainees. We outsource for conducting workshops on chemical management. Certificates are issued for the candidates.â€
The specialty chemicals company LANXESS has comprehensively updated its LewaPlus design software for the water industry. The dimensioning of reverse osmosis (RO) and ion exchange systems (IX) is now even more practical and user-friendlier. There is also the option to include ultrafiltration (UF) in the planning. The new UF module will be presented for the first time at Aquatech, which will take place from November 5 to 8, 2019, in the Dutch city of Amsterdam.
Ultrafiltration is used as pretreatment for reverse osmosis – and increasingly for ion exchange resins applications. Around one third of all newly built reverse osmosis systems have upstream ultrafiltration – and the number is rising.
LANXESS is a global distributor of high-quality Gigamem ultrafiltration membranes and systems from French company Polymem, which is based in Toulouse. In order to design complex water treatment systems that also include ultrafiltration technology, LANXESS has now integrated this pretreatment into its software. Ultrafiltration purifies and disinfects water in a single step. It is an alternative to conventional filtration in water purification and produces filtrate with a water quality that is considerably more consistent. Ultrafiltration often also replaces other conventional treatment techniques as well as microfiltration, as it also removes smaller particles and thus significantly reduces deposits in subsequent process steps. This enables a more stable process.
LewaPlus also offers users the option to create their own water library. This is because customers often have only an incomplete water analysis – if they have one at all – when planning their system. With a library, they can then utilise the data that is stored in LewaPlus.
Telangana-based KEP Engineering Services designs and manufactures major industrial equipment with international standards. The company provides turnkey solution for ZLD, which includes the process like primary treatment, secondary treatment, tertiary treatment and evaporators and dryers. Based on the effluent characteristics, KEP will select the process of treatment to recycle 100 per cent water to process.
The elimination of process-water and chemicals would be a real breakthrough for the textile dyeing industry, and it seems this has now come to fruition, with the launch of the world’s first ever industrial dyeing machines that uses super carbon dioxide (CO2) as a replacement for water. The manufacturer behind this system is the Dutch company, DyeCoo Textile Systems BV. Years of extensive research and development has gone into producing the novel, completely water-free dyeing process which has considerable lower operational costs compared to conventional dyeing processes.
When carbon dioxide is heated to above 31°C and pressurised to above 74 bar, it becomes supercritical, a state of matter that can be seen as an expanded liquid, or a heavily compressed gas. In short, above the critical point, carbon dioxide has properties of both a liquid and a gas. In this way supercritical CO2, has liquid-like densities, which is advantageous for dissolving hydrophobic dyes, and gas-like low viscosities and diffusion properties, which can lead to shorter dyeing times compared to water. Compared to water dyeing, the extraction of spinning oils, the dyeing and the removal of excess dye can all be carried out in one plant in the carbon dioxide dyeing process which involves only changing the temperature and pressure conditions; drying is not required because at the end of the process CO2 is released in the gaseous state. The CO2 can be recycled easily, up to 90 per cent after precipitation of the extracted matter in a separator.
“Today, we have nearly one-fifth of the world’s population, with access to only 4 per cent of the world’s water resources. India is set to become the world’s third largest economy by 2030. This necessarily means that we need to invest in wastewater treatment and recycle infrastructure. While the wastewater management issues that India is facing are serious, they are not insurmountable. Achieving water sustainability can be done through a mix of incentives, policy structures, and regulations. This will encourage various stakeholders to recycle and reuse wastewater. One of the silver linings in this scenario is that new wastewater treatment technologies need not be developed. It is simply a matter of accelerating the adoption of proven, high efficiency technologies, which can be done with the right push from the government. Probably appropriate pricing of water, once basic needs are met, especially if drawn from ground water, could be an extremely effective first step,†concluded Zarapkar.