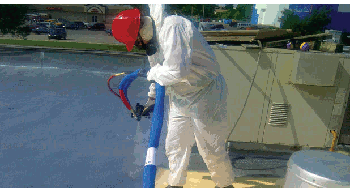
Pros & cons of polyurethane coating
Polyurethane has been used in coating for their compressive nature, thermal behaviour, complex structure designing and many other aspects, say Laga SK and Vignesh Dhanabalan, who provide a view of end applications of coated material in market use and also the advantages and disadvantages of foam coating.
Polyurethane has been used in coating for their compressive nature, thermal behaviour, complex structure designing and many other aspects, say Laga SK and Vignesh Dhanabalan, who provide a view of end applications of coated material in market use and also the advantages and disadvantages of foam coating.
Coatings of textile substrate are finishing process designed to add or improve functional properties to materials and to create specific properties. Coatings have become an important aspect of manufacturing/designing of advance featured substrates imparting improved properties of material like heat and chemical hazard, medical based properties, better adhesion between substrate, wet-ability, corrosion resistance, wear and tear and many other properties. Coating is a process of applying of single or multilayer of material deposition onto the substrate.
Initially coatings were made from naturally available materials like tree gum, oils, smoke soot for producing water proof coating then with want of improvement in medical field substrates with inherent medical behaviour were used medical based coatings were used to increase their behaviour. In 1823 modern methods of coatings came into patterned usage with high demands which lead to the synthesis of man-made plasticisers and their application[1-3]. Polyurethane coating has become one of the highly preferred plasticisers as coating material due to its enormous use in metal, wood, plastic, glass and textile coating. They are widely used in ship paints, and about one in four cars produced worldwide today is coated with a polyurethane clear coat. Plastic scratches of the poly- urethane coating are substantially reversible self-healing, (initiated by the recovery forces of these bonds, above the glass transition temperature (Tg)).
Polyurethane coating helps bringing about dramatic reduction in production time, fabrication that takes days together using polyester fibre glass can be reduced to hours using spray polyurethane coating for foam.
The two-component polyurethane automobile clear coats have improved scratch resistance[4]. Aromatic two-component polyurethane systems are mainly used in wood finishes, in corrosion-protection applications and for floor coatings in the construction area.
Coatings based on aliphatic polyisocyanate are used as aircraft paints particularly for their fast curing at ambient temperature with excellent light stability to finish even to high-UV radiation.
Polyurethanes are also widespread in construction applications, such as floor and balcony coatings and pipeline coatings, polyurethane surface coatings are applied to wood, concrete, and automobile and machine parts. They also have marine applications where they are rapidly increasing in importance too.
Polyurethane synthesis
Polyurethane foam system is prepared by reaction of short chain polyol (an alcohol with more than two reactive hydroxyl groups per molecule) with a long concentration urethane linkage of diisocyanate or a polymeric isocyanate in the presence of suitable catalysts, surfactants, blowing agents and additives.
The dispersing of gas (component A) throughout a fluid polymer phase (component B) and stabilising results in the formation of foam. Depending on the type of polyol and isocyanate used the generated foam exhibits different properties.
An alternative soft segment of polyol with weak segment of polyols with weak inter chain interaction is present in coiled form and a hard segment is formed by reaction of diol/diamine and the diisocyanate.
By careful selection of the polyol and isocyanate, foam with varying properties can be generated. It could be soft and flexible with totally open cell structure. Isocyanates and polyols in a 100 per cent solids polyurethane system are reacted normally by around the ratio range of 1:1. It requires that the both components have the same or close viscosity.
This is the most difficult challenge for a coatings chemist in designing 100 per cent solids polyurethane coating system. A 100 per cent solids polyurethane coating system with a mixing ratio higher than 1:1 will have better chance to cause mismetering problems (often called as off-ratio) during its application. The higher ratio is, the higher possibility it will occur.
Polyols
Polyol is a macro molecule of poly hydroxyl alcohols with molecular weights ranging from 200 – 7000 with functionalities ranging between 2 and 8. Monomeric polyols such as glycerin, pentaerythritol, ethylene glycol and sucrose often serve as the starting point for polymeric polyols. Functional polyols are used to obtain by combining with propylene oxide or ethylene oxide. Polyester polyols, Polyether polyols, Fire retardant based polyols are different varieties of polymeric functional alcohols.
Isocyanate
This is the second basic component in manufacturing foam material. Isocyanate is the functional group with the formulae R?N=C=O. Organic compounds that contains an isocyanate group. Isocyanate is electrophiles and is reactive toward nucleophiles including alcohols, amines, and even water. Upon treatment with an alcohol, an isocyanate forms urethane linkage, Isocyanate is extremely reactive and they react with materials containing active hydrogen[5].
Catalyst
Catalyst are substance that increases the rate of a chemical reaction without itself undergoing any permanent chemical change, the tertiary amine catalyst is commonly found in rigid polyurethane foam formulation and are strongly basic and often have higher vapour pressure, it causes skin irritation and precautionary measures are must while handling.
Blowing agent
A blowing agent is a substance which is capable of producing a cellular structure via a foaming process in a variety of materials that undergo hardening or phase transition, CFC are the most preferred though they are low toxic by standards if wrongly dealt it might cause heart related problem. During thermal decomposition of chemical blowing agents nitrogen/carbon dioxide generation takes place these gas phase molecules helps in forming bubbles in the foam material creating the resilience effect[6].
Polyurethane coating
Polyurethane coatings are of two types one component system and two component system.
1. One component system:
This system is low molecular weight prepolymer with terminal isocyanate group. They are dissolved in solution and applied on to the substrate and moisture cure, the water molecule acts as chain extender and cross-linking agent creating urea. Doing the exothermic reaction carbon dioxide is formed through slow diffusion of gas. The curing depends on temperature and humidity. The use of block allows formulation one-component system at room temperature.
2. Two component system:
Isocyanate-terminated prepolymer (or) polyfunctional isocyanate is reacted with polyhydroxy compounds containing urethane groups, curing of this solution occur due to formation of urethane linkages. The resulting coating depends on polyol and molecular weight, temperature, concentration of polar group and cross linking density. Additives are used in two component systems mainly they are generally silica fillers, these are generally polar in nature and should be handled carefully not to form blisters.
Theory behind coating
Coating material may be in liquid, melt powder, solid layer (film, foam and web) during application and they are brought to the convenient phase for usage during application, the wetting and spreading of coating material on substrate is a major characteristic to be analysed, it affects the interfacial bonding between the coating material and the substrate material.
During application the liquid spreads over the solid phase substrate displacing the original fluid (mostly gas phase) making a contact angle ?q? between the solid and the liquid interface. During the phase change of material case is there where the interfacial bond between the substrate and the coating material gets disturbed so finishing treatment like binders are used to catch hold of them. The rapid and exothermic chemical reaction between the isocyanate component and polyol component also plays a role in the selection, application, and inspec- tion of 100 per cent solids polyurethane coatings.
Factors responsible for results of coated material
-
Cohesive nature between the substrate and material
This property largely influences the characteristic feature of the coated material. If the cohesive nature of the coating material/substrate is not as per the requirement then the possibility of peeling/patch like formation on the surface is sure to occur creating a hindrance to the desired output of the material.
-
Chemical cross linkage
The appropriate usage of raw material for the syn-thesis of coating material based on end product is a must. In case of wrong selection the cohesive nature of the material gets affected.
-
Curing temperature and pressure
The post care treatment of the coating is a must to have better durability of the imparted feature and this curing should be done keeping factors like end use, chemical nature, thermal behaviour and other features as primary concern.
-
Thickness of the coated substrate
Thickness of coating influences properties like rigidity, tensile strength, bending modulus etc.
-
Chemical behaviour of the coated material
Influence of external environment (UV degradation, heat, humidity, acidic nature?etc) hinders the output result.
Application methods of coating on substrate
- Foam coating
The coating or finishing material is converted into foam from solution or emulsion and applied on the fabric knife as roll; the penetration of foam is low but gives much better handle and drape. This is used for open type cell construction.
The foam coated substrate is passed through a stenter for finishing process, care should be taken such that high heat is not supplied and neither lowers than the finishing temperature. With 5-10 per cent of moisture content the fabric is passed through steel rollers crushing the foam and curing at 160-70°C. The foam collapses on drying leaving a thin film on the surface.
-
Spray coating
Spray foam is long lasting, durability and lightweight. Instead of replacing your entire system because one area of the surface is an issue, spray foam coating is a more cost effective solution.
It is sprayed onto the surface to fill small cracks and crevices; it then expands approximately 30 times its original liquid volume to form a hard, closed cell roof surface. The foam dries almost instantly and self adhere to the surface. Not only is the foam coating is an expensive solution to protect your roof, but it insulate the building exterior which will lower the utility cost. This method involves use of single coating material or multiple materials to spray. The main drawback of this method is the non-homogeneity and expensive cost for manufacturing but this can be used for specialised narrow web bonding for design complicated structures.
-
Rod Mayer coating technique
The Mayer rod is a stainless steel rod that is wound tightly with stainless steel wire of varying diameter. The rod is used to doctor of the excess coating solution and control the coating weigh.
The wet thickness after doctoring is controlled by the diameter of the wire used to wind the roll and is approximately 0.1 times the wire diameter. Lower setup cost and precise thickness control (control the web coating thickness in 0.1-0.2 mil increments) are features that make the process favourable over the other methods, but low viscosity liquids (viscosity parameter) and coating capacity of only 1000 ft/min are found to be the limitations.
Other coating methods
The general coating methods are mentioned below. These methods are used to prepare prepegs coatings with one component and the other components are added to during product formation.
-
Knife coating
The substrate is pulled by rollers and the excess amount of coating material is fed and the application is controlled by the doctor knife. The coating thickness is calculated based on the gap between the knife and the substrate excess coating material is removed by the knife.
-
Immersion/dip coating
Simplest and most commonly used coating technique used. The substrate is dipped into the solution bath contai- ning coating substrate and taken out, the direction of gravity determines the geometry of application the excess coating material on the substrate is removed using doctor blade.
-
Transfer coating
The coating material is applied to an external material with required value then it is transferred to the substrate by application of heat and pressure using hot rollers.
- Roll coating
This method is also called as kiss roll coating and has procedure similar to that of immersion coating, N numbers of rollers are used with textured patterns to achieve desired results this also uses heat and pressure to fix the coating material, the thickness of the coating is determined by the texture pattern and the pressured involved.
-
Screen coating
The surface of the screens has mesh structure with minute pores allowing the coating material to flow through them. The amount of coating is determined by the screen mesh number; squeeze pressure, angle between the squeeze blade and the screen, the viscosity of the coating substrate. This method helps in producing very fine and delicate film coating onto the surface having no external pressure or heat to seal the coating material binders (fixing agents) are used.
-
Powder coating
Powder coating is one of the methods that involve use of solid phase coating material. In this method pre-prepared coating powder in solid foam is deposited directly onto the substrate, since no water is used drying of material is not required and wastage of energy is also reduced. The scattering of solid powder is comparatively uniform with rotating scatter roller.
Evaluation of coated fabrics
Coated fabrics have wide range of application. The coating material on substrate should not hinder the base properties of the material and impact the properties of coated substrate like interfacial bonding, chemical beha- viour of material, dimensional stability and many more. Characterisation involves testing of adhesion, peel strength, abrasion resistance, fabric handle and drape under standards based on ASTM and BS.
Coated fabric mechanical properties (by NMR) are dependent on the molecular mobility of components within the coating.
Molecular mobility can change with curing conditions or plasticiser concentrations. NMR is not only able to characterise this mobility for a bulk sample, but can also measure maps, representing the curing homogeneity and plasticiser concentration within a sample.
-
Tensile strength test
Tensile strength of the base material (substrate) varies, usually strength increases as the coating is applied. Unless the coating material has corrosive effect on the surface of the material there is no retardation in tensile property. The adhesion between the coating material and the substrate determines the total strength with thickness of the coating.
Li.W.Y and Li.C.J, studied the effect of annealing treatment on the micro structure and properties of cold-sprayed Cu coating and stated that the deposition of particles takes place through the intensive plastic deformation upon impact in solid state at a temperature well below the melting point of spray materials[6].
-
Shear behaviour
The shear behaviour of architectural coated-fabrics is an important issue in structural engineering. In tensioned fabric structures, the shear deformations allow flat fabric patterns to be developed into complex forms. Shear stiffness has also been taken into account for the design of these structures under load as, it can significantly affect the values of stress concentrations predicted by numerical analyses[7].
The coating penetration and thickness can affect shear behaviour of coated fabrics, primarily through restriction of yarn rotation and mobility in shear and tear, as well as through contribution to load carrying capability.
-
Peel strength
The bonding strength of coating-substrate interface is significantly influenced by the hardness of substrate. On the other hand, the higher gas temperature is beneficial to the impact velocity and temperature of particles, consequently improving the bonding strength of particle-substrate and particle-particle.
-
Dimensional stability and cell structure analysis
Dimensional stability remains a major factor in designing of product and is expected to remain the same throughout the usage because it is expected to give the specified result in that structure, deformation in the shape leads to property loss of the material so even the coated material is also expected to maintain the stability of the substrate even after application and prolonged usage.
The fabric structures are analysed using X-ray spectroscopy or SEM image analysis and deformation by 3D image scanning. The 3D image scanning is a non-contacting method, the fabric is viewed using a high resolution digital charged coupled device (CCD) cameras. Using principles of photogrammetry the centre of each facet is defined as a measurement point and is tracked through each digital image.
Different microscopy methods are used to categorise fabric structure to determine adhesive level, thickness and penetration of coating material. Coating penetration can be done by using SEM and even X-ray spectroscopy for energy dispersion.
-
Thermal transmission
The coating material helps/retards the flow of heat to external bodies by the name of conduction, convection and insulation. The thermal behaviour is based on the type of coating applied used on the substrate. To characterising the thermal behaviour of the mentioned coated fabrics the thermogravimetry (TG), the derivative thermogravi- metry (DTG) and the differential thermal analyse (DTA) can be utilised.
DTA is a dynamic technique that permits to record the temperature difference between the sample and the reference substance depending on time or temperature. The same substances are placed in the same enclosure and in programmed heating conditions.
TG permits the mass measurement of a heating or cooling sample depending on time or temperature. The complex processes are took place in successive serial stages.
DTG is the technique with that it is possible to deduce the differential of a thermo gravimetrical curve depending on time or temperature, giving information about the kinetics of the thermal decomposition processes.
-
Creep behaviour
Jia Y et al, studied the creep behaviour of polyurethane coated material and stated that creep strain curve increased with temperature. When temperature was increased from 35 to 80°C, it apparently should that the creep strain increased from 0.12 to 0.18 (by 45 per cent approximately) maintain at time frame for 30 minutes. This indicates that the creep property is closely related with intrinsic viscoelastic properties of the materials[8].
Applications of polymeric coating
-
Polyurethane coatings for metal
Polyurethane coating on metal provides a thin film, high gloss finish with exceptional weathering performance characteristics. This coating is used in virtually all indus- trial markets to provide a smooth durable finish that has superior resistance to corrosion, abrasion, and chemical exposure. Polyurethanes are normally used to topcoat high build epoxy and inorganic zinc.
-
Polyurethane coatings for wood laminates
They have high level of quality and give perfect fit with the natural properties of wood. They combine to provide outstanding resistance to solvents and chemicals with unique toughness and flexibility. Because of their good pigment wetting properties – pigmented coatings yield high-gloss, high-bodied films with excellent flow properties. The films have outstanding mechanical properties and provide the ideal balance of hardness and flexibility, even at low temperatures.
Good scratch resistance is also a feature of polyurethane coatings[9].
-
Coating concrete surfaces
Concrete surface is not homogeneous like steel which makes the coating of concrete somewhat different from coating steel. Non-homogenous concrete surfaces may contain irregularities such as bug-holes, fins, tie rod holes, and form joints. Concrete prepared with the same raw materials may vary from one pour to the next due to variations in cement, sand and gravel, non-uniform mixing, the degree of vibration, and weather conditions.
Spray Equipment & Process is used, fast setting of 100 per cent Solids Polyurethanes comprising of two components, the Resin (Polyol/Polyamine/Blend) and the Activator (Isocyanate). Proportions the two liquids in the designed ratio by volume (3:1/2:1/1:1) and develops a pressure of 2000 – 3000 Psi.
-
Polyurethane coating for colour enhancement
Polyurethane coatings provide additional functional properties like, colouring of glass and imparting of special properties can be done using polyurethane coating.
The polyurethane coating can perform functional tasks like the protection from mechanical and chemical stress. It increases scratch resistance it also adds shatter protection and makes it more dishwasher proof.
-
Polyurethane adhesives and sealants
Polyurethane-based adhesives and sealants contribute new solutions for assembly, joining and sealing in the construction industry. Polyurethane adhesives can be formulated to withstand high stresses, they are tough and at the same time they stay elastic, so they follow any ?natural? movement of materials with a high coefficient of expansion without damaging the adhesive joint.
-
Polyurethane for sport field designing
The polyurethane sports coating has a thickness of 4 to 8 mm full PU resins applied in site, paved on to either reinforced concrete or asphalt substrate. The System is cushioned court with excellent playing characteristics of good traction and uniform medium-fast bounce, an all-weather for year round play, and relatively low maintenance. This is apt for multiple-use indoor and outdoor sports surfaces.
-
Antibacterial composite coatings
Graft from polymerisation was using nano-titania/polyurethane (nTiO(2)/polyurethane) composite coatings made from nTiO(2) that is chemically attached to the backbone of the polyurethane polymer matrix with a bifunctional monomer, 2,2-bis(hydroxymethyl) propionic acid (DMPA). This bifunctional monomer can coordinate to nTiO(2) through an available -COOH group, with two available hydroxyl groups reacts with diisocyanate terminated pre-polyurethane through step-growth polymerisation. After step-growth polymerisation, the functionalised nTiO(2)-polyurethane composite coatings exhibits excellent antibacterial activity against gram-negative bacteria Escherichia coli[10].
Advantages of PU coating
- In coated fabrics drape effect and smooth appearance are better to conventional material.
- Custom made shape such as spiral, radial and corrugate surface profiles can be easily designed.
- Dry cleaning is best suited.
- Low temperature flexibility.
- Low additives.
- Are 100 per cent solids, having zero or near zero VOC?s.
- Are non flammable, solvent free and as safe as house paint.
- Can be applied in a single multi-pass coat to any dry film thickness.
- Can be put into service within hours.
- Non-dangerous goods for transportation.
- Requires no post curing.
- Pot life ranges from a few seconds to several minutes making it suitable for different end application.
- Resistance to gouging and abrasion and disbandment forces.
- Resistance to chemical attack.
Limitations of polyurethane coating
- Penetration of the foam material into the textile substrate is comparatively low.
- Rapid drying results in the formation of skin substrate on the surface.
- In case of heavy drying the foam material springs back and in case of low drying pock marked appearance are formed.
- It is cost involved.
- Evolution of CO2 gas during synthesis of polyol and isocyanate creates suffocation for the workers[11].
Conclusion
Coating and lamination has always been a substitute for imparting additional characteristics to the material. Based on the end application, the type of coating and technique involved varies with usage. Day by day inno- vative application of coatings is bought into use for better end product. Coatings are not only used for imparting functional property to the fabric but also are being used as function improviser as well as resin that could create interface in composite structures.
Acknowledgement
The author wishes to express their thanks to DKTE TIFAC CORE in Technical Textiles for their timely help and support.
References
- Sen Kumar A: Coated Textiles Principle and Application, Second Edition CRC Press, ISBN 978-1-4200-5345-6, 2007.
- Smith William C: Smart Textile Coating and Laminates: Woodhead Publications, ISBN 978-1-84569-379-4, 2010.
- Chapman and Hall: Surface Coating and Raw Material, Vol 1, 1993.
- Maria-Carmen Loghin, Irina Ionescu, Pulferia Nicolaiov, Ionu Dulgheriu: Thermal Characterisation of Coated Fabrics, Unpublished Work.
- https://en.wikipedia.org/wiki/Isocyanate (data retrieved on 5th July 2013).
- W-y li and C-j li: Effect of Annealing Treatment on the Microstructure and Properties of Cold-sprayed CU Coating, Thermal Spray, Internal Thermal Spray Conference 2005.
- Galliot C, Luchsinger R H: The Shear Ramp: A New Test Method for the Investigation of Coated Fabric Shear Behaviour, Empa – Swiss Federal Laboratories for Materials Science and Technology, Centre for Synergestic Structures, Ueberlandstrasse 129, CH-8600 Duebendorf, Switzerland.
- Jia Y, Jiang M Z, Gong X L, Zhang Z: Creep of Thermo- plastic Polyurethane Reinforced with Ozone Functionalised Carbon Nanotubes, Express Polymer Letters, Vol 6, No 9 (2012), 750-758.
http://www.bayercoatings.de/BMS/DB-RSC/BMS_RSC_CAS.nsf/id/COEN Wood. (data retrieved on 2nd Sept 2013) - Charpentier PA, Burgess K, Wang L, Chowdhury RR, Lotus AF, Moula G: Nano-TiO2/Polyurethane Composites for Antibacterial and Self-cleaning Coatings, Nanotech- nology, Vol (42), pp 23, 26th Oct 2012.
- http://www.indiamart.com/acesports/sports-surfaces.html. (data retrieved on 2nd Sept 2013)
The authors are with the DKTES Textile & Engineering Institute, Ichalkaranji, Maharashtra-416 115. Email: swapan.laga@gmail.com vigneshdhanabalan@hotmail.com.