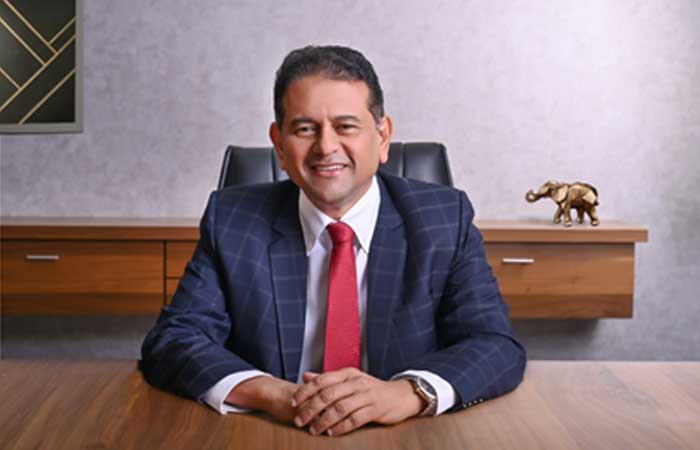
MB Raghunath: Govt needs to study the cost structure of our products with other countries
Mafatlal Industries (MIL) has been a leader in textiles for over 120 years, offering a diverse range of products across various sectors. Their extensive textile portfolio includes yarn-dyed shirting, suiting, voiles, prints, linens, bleached white fabrics, rubia, and complete uniform solutions such as school uniforms, shoes, accessories, and corporate/institutional uniforms. In this interview with Divya Shetty, MB Raghunath, Chief Executive Officer, Mafatlal Industries, discusses the significance of integrating sustainable practices in manufacturing and outlines the company’s future plans.
What according to you is the present state of the Indian textile industry?
Indian textile industry is going under pressure due to lower demand from US and Europe. Domestic demand and growth is also muted. There is a general slowdown across the world due to current political scenarios, wars, credit risk and investment risks in the past years Indian manufactures has increased the weaving and spinning capacities by improved technology. Processing industry has not seen the investments as good as spinning and weaving due to high CAPEX, import duties, delivery and installation delays and local environment policies. Processing industry has huge skilled manpower shortage too.
The Indian textile sector has set an ambitious target of achieving $350 billion in market size by 2030. In your opinion, what are the significant challenges or barriers that could hinder this progress?
It is only possible if the cost structure of our textile products are in par with China and other countries like Indonesia, Egypt, Bangladesh, Vietnam, etc. our cost structure is high due to high domestic raw material cost, land procurement cost and construction cost, power cost, etc. manufacturing companies face high borrowing cost for CAPEX and OPEX compared to the peers worldwide. Textile funding is not preferred by banks and financial institutions due to certain past history of few textile manufacturing companies.
What opportunities do you foresee for the Indian textile industry as we move into 2025?
India is a preferred supplier by brands across US, EU and many other countries, we face challenge on pricing, delivery period due poor capacity build up in the past due to government policies of garment sector. India really needs focus on quality, capacity building and reduction of cost inputs and modernisation of production lines to achieve ambitious targets.
How crucial is sustainability in positioning India as a global leader in the textile industry? Additionally, could you share how your company is integrating sustainable practices into its operations and supply chain?
Sustainability is extremely important for the country and world. India has started off well in developing sustainable fabrics and garments in woven and knit segments. Manufacturing companies from southern part of India is doing lot of activities in this area. Sustainability is going to be a global order and Indian manufacturers need to invest in latest manufacturing technologies to upgrade the quality, efficiency and scale of manufacturing. As a country organising raw material for sustainable yarn is a big challenge currently. Government needs to improve and find efficient ways for collection of scrap to fulfil the industry requirements. In Mafatlal we have started sustainable products across our product lines. We are the first ones to introduce sustainable fabrics and garments in school and corporate uniform segments.
How important is technological modernisation in enhancing our global competitiveness, and what more can be done to accelerate the adoption of cutting-edge technologies in this sector?
Modernisation is extremely important but it needs heavy CAPEX cost. Import Cost of machines, cost of land & buildings are high in India. Cost of borrowing is also high. Textile industry and financial institutions needs to reach a funding model for textile manufacturing industry with the help of government. Few states are doing little bit their own but creating cluster’s in selected areas of the country with required infrastructure from government is a better solution. Textile and garmenting are large job providers for non-skilled and semi-skilled man power.
What measures should the government take to further strengthen the Indian textile and apparel (T&A) segment?
Government needs to study the cost structure of our products in comparison with other countries, especially china and come out with policies to make the industry cost competitive rather than putting up textile parks across the country. Development must be around areas where raw materials and manpower is available. Government must put up centralised Zero discharge plants and charge production units as per use. Power tariff must be streamlined. Our cost and quality of fibre used in spinning is inferior to the fibre used by other manufacturing countries. This variation in quality and cost is impacting our efficiency, product quality, yield and scale of production.
Which emerging areas within the textile industry hold the most potential for growth?
India needs to invest in Technical textiles, fashion textiles and garmenting to achieve the goals. There is a major requirement from engineering companies to scale up textile machines and accessories production to reduce import cost and time. This will also improve maintenance requirements of textile industry. Textile engineering is no more very attractive course in universities hence government and educational institutions must encourage textile related courses to fulfil the requirements of future industrial scaling up of this segments.