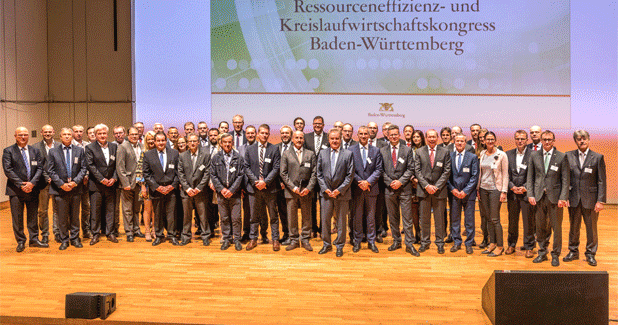
Mayer & Cie.’s Relanit: 30 years on, still going strong
Relanit line’s current flagship is the Relanit 3.2 HS, which is one of the most productive single jersey machines in the market, both for open width as well as tubular. Relanit’s anniversary year started on October 13, 2017. Relanit is one of Mayer & Cie.’s (MCT) most important and most successful machine types. Relanit uses relative technology, the circular knitting machine manufacturer’s proprietary development, launched at ITMA in 1987, when the trade fair opened on 13 October in Paris. In its current version the Relanit 3.2 HS is one of the most productive single jersey machines on the market. At the same time, its energy consumption is 30 per cent below that of a conventional knitting machine. Relanit is also part of Mayer & Cie.’s latest innovation, its spinitsystems technology. Thanks to relative technology a fragile fibre bundle can become a fluffy single jersey fabric.
Relanit line’s current flagship is the Relanit 3.2 HS, which is one of the most productive single jersey machines in the market, both for open width as well as tubular.
Relanit’s anniversary year started on October 13, 2017. Relanit is one of Mayer & Cie.’s (MCT) most important and most successful machine types. Relanit uses relative technology, the circular knitting machine manufacturer’s proprietary development, launched at ITMA in 1987, when the trade fair opened on 13 October in Paris. In its current version the Relanit 3.2 HS is one of the most productive single jersey machines on the market. At the same time, its energy consumption is 30 per cent below that of a conventional knitting machine. Relanit is also part of Mayer & Cie.’s latest innovation, its spinitsystems technology. Thanks to relative technology a fragile fibre bundle can become a fluffy single jersey fabric.
“Relative technology is still the shape of things to come, 30 years after the start of series production,†says Marcus Mayer, Managing Director Mayer & Cie. in charge of technical development. “It exemplifies what we stand for, for our values and our aspiration to always be one step ahead.â€
Conventional knitting machines usually work with horizontal sinkers. That means the needle moves up and down while the sinker works horizontally. With relative technology, the sinker too moves up and down. Relatively speaking, it shifts towards the needle. In this movement lies relative technology’s biggest advantage: In comparison to conventional technology, the yarn only has to travel half the number of deflection points to form a stitch. Each deflection means less stress on the yarn. That is why Relanit can process difficult yarn or inferior qualities without a hitch. Not only to form a fabric of a certain quality but also without making amends in terms of production speed or machine downtimes. Both would be the case if inferior quality yarn were to be processed on a conventional machine. Because yarn is the key cost factor in knitting, Relanit can help the knitter to save a lot of money – and that means to make a profit.
“When we unveiled Relanit at the Paris ITMA 30 years ago, it was unmatched in production, speed, yarn care and energy efficiency,†Marcus Mayer says. “And it still is. We are not aware of any company that has succeeded in replicating the technology. As our patent expired years ago, that would be possible. And nobody has developed a better technology that combines all these benefits either, by the way.â€
While relative technology in itself has remained unchanged, it has grown to keep pace with technological development. The line’s current flagship is the Relanit 3.2 HS. It is one of the most productive single jersey machines in the market, both for open width as well as tubular. At 50 rpm it works with elastomeric yarns just as well as with cotton, the machine’s traditional speciality. Furthermore, the Relanit 3.2 HS uses up to a third less energy than a conventional circular knitting machine.
In addition to the Relanit 3.2 HS, the current Mayer & Cie. portfolio comprises a further eight Relanit machines, with striping machines, electronic and mechanical types among them. Every year, around 300 Relanit machines find their way to clients all around the globe. The specialists in cotton yarn are most popular in Turkey, followed by Brazil and China. Overall, Mayer & Cie. has sold 10,000 units, delivered to about 90 countries worldwide. That means about a quarter of all machines sold in the past 30 years belong to the Relanit family.
spinitsystems is the company’s latest innovation and it would not be possible without relative technology. The spinning and knitting machine Spinit 3.0 E combines formerly strictly separated processes – spinning, cleaning and knitting. The raw material it works with is a not a regular cotton yarn but a roving which easily dissolves when rubbing or tearing it. This is exactly the material that Spinit 3.0 processes. Relative technology deserves much of the credit for it succeeding in doing so. The fibre bundle travels a much shorter distance and is subject to less tension than would be the case with conventional knitting technology. In short, it is thanks to relative technology that a fragile roving can be transformed into fluffy single jersey on Spinit 3.0 E.
No spinitsystems without relative technology: The Relanit’s gentle processing of the yarn makes spinning and knitting possible. This is how a Relanit looked 30 years ago: Relanit 4, one of the machines presented on ITMA in 1987, works with four needle tracks. And this is Relanit today: In the Relanit 3.2 HS relative technology ensures extraordinary productivity, reliability and a large variety of yarn qualities that can be processed.
Circular knitting machine manufacturer Mayer & Cie. has received an award from Baden-Württemberg for the energy-related renovation of its building services. Franz Untersteller, Minister for the Environment, Climate Protection and the Energy Sector, named Mayer & Cie. one of the state’s 100 Resource Efficient Companies. He presented the award at the Resource Efficiency and Recycling Congress held in Stuttgart on October 18 and 19, 2017.
“We are delighted that the state of Baden-Württemberg has chosen to honour our work in this area as exemplary,†says Marcus Mayer, Managing Director of Mayer & Cie. “For us as an owner-managed family firm sustainability is a ‘must’ in every respect. That is why it is just as much a matter of course for us that our knitting machines work resource-efficiently as that we manufacture them efficiently. And optimised energy costs for cooling, heating and electricity make an important contribution to resource efficiency.â€
Since Mayer & Cie. moved to its corporate headquarters on the outskirts of Albstadt-Tailfingen in the 1950s the buildings on the site have repeatedly been extended, including many local and separate energy centres. This led to a disproportionately high use of energy. That was why, in 2014, Mayer & Cie. began to renovate its cold-water network. As a result, a third of the existing cooling plant became superfluous to requirements. Today’s cooling management now harnesses the Swabian Alb region’s bracing climate and switches off more cooling machinery during the five cold winter months. In 2015 Mayer & Cie. went on to upgrade its water pipes and renovate two heating plants. Last year, new compressors helped generate compressed air. This year the company was able to connect all consumers and install load profile management. Plans for the combined heat, power and cooling concept were also completed and a cooperation agreement was concluded with the Neckar-Alb Virtual Power Station, a pilot project undertaken in collaboration with the University of Reutlingen. “These measures have enabled us to reduce our ancillary costs considerably,†Marcus Mayer concludes. “That could especially be a competitive advantage if the economic situation were to become less favourable than it is today.â€
Heiko Hämmerle, Mayer & Cie.’s head of plant technology, who has been in charge of the project for over four years, adds: “We are also forearmed for further energy market developments. It could well be that we will as a result enjoy a major advantage with modes of energy supply that may be available in the future.†Hämmerle will take the project further forward in 2018. Implementation of the heat, power and cooling concept will then be on the agenda, including the installation of a combined heat and power unit and many other lines.