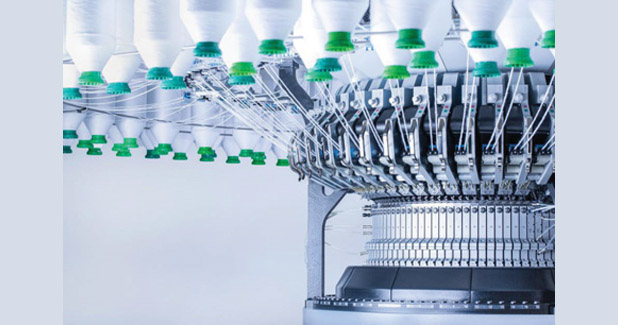
Mayer & Cie. presents advanced Spinit 3.0 E
Mayer & Cie. (MCT) has equipped its Spinit 3.0 E spinning and knitting machine with new functions for the industry’s leading trade fair ITMA. Existing properties of the machine such as fancy patterning possibilities have been developed further.
Since the end of 2018 the Spinit 3.0 E spinning and knitting machine has been in series production and in use by a large number of customers. The manufacturer has taken the multiple award-winner further so that it can now process polyester and thereby create new products. Mayer & Cie. is specifically targeting the athleisure and sportswear sector. The fancy patterning capabilities are interesting for designing fashionable sportswear. Unique patterns can be produced by the Spinit 3.0 E – and by it alone. Spinit fancy jerseys are characterised by soft transitions and switching between opaque and transparent pattern areas, while soft transitions set Spinit designs significantly apart from the transitions that a jacquard machine can produce.
“In discussions with our customers we have discovered that they particularly appreciate our spinning and knitting machine’s fancy patterns. That is why we have worked intensively on this feature. Our customers now benefit from greater flexibility that enables them to create their own USP with the Spinit 3.0 E in keeping with our ITMA slogan ‘Stay a winner: With Mayer & Cie.’,†says Michael Tuschak, head of spinitsystems sales and marketing. That in no way changes the known properties of Spinit jersey fabrics. They are strikingly soft and supple, even, glossy and glamorous. Extraordinary physiological properties such as warmth retention complete this line-up.
The Spinit 3.0 E has also been given an ease-of-use upgrade. “Under the heading ‘Digital Spinit’ the digital improvements that are being taken forward across the company have found their way into spinning and knitting technology,†Michael Tuschak says. “Create, Operate and Control are the three key terms,†he adds, “and we have attractive innovations to offer in each of these areas.†Create describes the process of designing new patterns, starting from the idea and leading to the final knitting programme. Mayer MDS1 makes creating patterns easier. At the operating level, the 10 inch touch display improves ease of use. Thanks to a new interface, Spinit 3.0 E is fit to connect to Knitlink, a platform that optimises the Control function, offering monitoring and remote service.
There has also been a further improvement in the machine’s productivity. Subject to the raw material and the pattern knitted, the Spinit 3.0 E is up to 20 per cent faster. “With this speed upgrade we are responding to our customers’ wishes, and for them an increase in productivity is most important,†Michael Tuschak explains. A new interface for an automated roving bobbin transport system supports this objective, too. Partnerships with market leaders in this field have already been initiated. Thus, Mayer & Cie. can offer its customers tailor-made solutions that help to increase the Spinit 3.0 E’s productivity further.
Because a spinning and knitting machine has much more to offer and is more complex than a conventional circular knitting machine Mayer & Cie. has added a comprehensive customer service programme to provide additional assistance. Fibre-to-Fabric offers both pre-sales and after-sales support. Comprehensive analysis and material tests in the run-up to purchase are as much a matter of course aspect of this support as the professional commissioning process and intensive individual training sessions provided by Mayer & Cie. “This comprehensive customer service concept aims to ensure that our customers achieve long-term success with their Spinit 3.0 E,†Tuschak says.
Successful placement of the Spinit 3.0 E in the market is based on a twin-track approach. For one, Mayer & Cie. addresses customers directly, showing them the wide range of opportunities offered by using Spinit 3.0 E by means of the Fibre to-Fabric programme. For another, Mayer & Cie. Maintains direct contacts with brand and sportswear manufacturers. “They have an especially strong demand for fresh patterns,†says Michael Tuschak. Depending on the area of use, these manufacturers specify certain fabric qualities as standard for the products in question and then order them from their suppliers. “We have already been able to convince manufacturers of our characteristic fabric quality,†says Michael Tuschak, “and only the Spinit 3.0 E delivers itâ€.
Mayer & Cie. exhibits weft knit machine study
Mayer & Cie. (MCT) also exhibited at this year’s ITMA a weft knit machine study that demonstrated a new technique of manufacturing textile fabrics. The long-established German firm is taking a fresh look at a proven procedure, weft knitting, and combining it with circular knitting. Especially in view of the bearded needle technology used the new procedure offers benefits in terms of needle service life and gentle yarn processing. The company sees further potential in the higher working speed that bearded needle technology makes possible.
“Our focus at this year’s ITMA was on sport and thus targets the very latest market requirements,†says Marcus Mayer, managing director in charge of technology at Mayer & Cie. “But our philosophy also involves developing new processes irrespective of shorter-lived trends. Success by Innovation: Traditionally a Step Ahead’ is our company’s motto and we aim to do it justice yet again with our Weftnit 3.2. We last succeeded in doing so with spinitsystems.â€
The most striking difference between a conventional circular knitting machine and the Weftnit 3.2 is the needles it uses. In the past, all Mayer circular knitting machines have used latch needles; the Weftnit 3.2 relies on bearded needles. That has several advantages for the user. As the head of a bearded needle is thinner than that of a latch needle, stitch formation is especially gentle. This effect is enhanced if the stitch forming is based
on the weft knitting principle using only two steps and requiring a lower yarn tension than circular knitting does. Bearded needles can be expected to have a longer service life – an effect that will be reflected in production costs. The same is true of the fact that a machine with bearded needles is easier to use overall. With a conventional circular knitting machine the operator must open the needle latches after sack removal and before knitting on again, which calls for some experience. With the Weftnit 3.2 that is no longer required.
In addition, the Weftnit 3.2, working with four needle tracks, produces all of the popular single jersey structures, such as piqué and double piqué, terry cloth, two-thread fleece and single jersey plated. Due to its distinctively gentle stitch formation the Weftnit 3.2
also scores points for processing critical yarns, as extensive tests by the circular knitting technology
leader have shown.
CATEGORIES Trade Fair
TAGS Circular knittingconventional circular knitting machinejacquard machineMayer and CieMichael tuschakspinning and knitting machineyarns