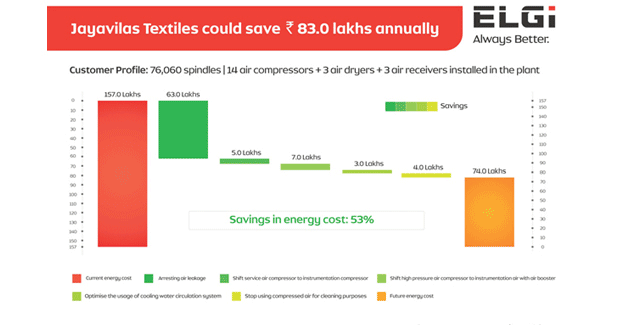
Material handling in spinning mill
In a spinning mill, there are many departments that involve handling of raw material, intermediate products, wastes, finished goods, stores and maintenance tool equipment, explains R Senthil Kumar.
In a spinning mill, there are many departments that involve handling of raw material, intermediate products, wastes, finished goods, stores and maintenance tool equipment, explains R Senthil Kumar.
Material handling can be defined as: “art and science of conveying, elevating, positioning, transporting, packaging and storing of materialsâ€. Material handling plays a vital role in any manufacturing industry by easily transporting the material from one place to another place. A material may be handled even 50 times or more before it conversion to finished product. It has been estimated that average material handling cost is roughly 10-30 per cent of the total production cost depending upon product to process. The cost of the production can be reduced considerably by saving the material handling cost. Material handling involves the movement of materials, manually or mechanically in batches or one item at a time within the plant. The movement may be horizontal, vertical or the combination of these two. Material movement adds to the cost but not to the product value. The ideal manufacturing plant would have an absolute minimum of materials handling and more use of mechanical material handling equipment. The multiple benefits associated with effective material handling in a manufacturing industry are listed in table 1.1.
Principles of material handling
- Reduce the unnecessary movements (manual and mechanical) involved in a production process.
- Adopt possible shortest routes for transporting materials.
- Employ mechanical trolleys and fork lifts wherever essential instead of manual labour for material handling in order to accelerate the material movements.
- Adopt principle of containerization or palletization to transport bulk number of materials in single unit (bobbins, cones).
- Overloading of material in the material handling equipment should be avoided in order to prevent any material quality deterioration.
- Appropriate, standard, efficient, effective, flexible, safe and proper sized material handling equipments should be selected.
- Utilize gravity for assisting material movements wherever possible.
- Design trolleys, containers in such a way that material transported should not get damage during handling.
- Design material handling equipment in such a way that it economizes the material handling process.
- The movement of material handling equipments should not interfere with neighboring machine operations.
- The maintenance of material handling equipment is vital in preventing any interruption in handling. Factors governing selection of material handling equipment
- Dimensions and parameters of materials being transported: The dimensions of the material being transported such as length, width diameter and material parameters such as weight, surface characteristics, delicacy and its chances of getting damaged during handling etc. should be considered.
- Layout of department: The path of material transportation, door dimensions, equality in floor levels between departments, height of the ceiling, strength of floor and walls, columns and pillars influence to a great extent the choice of a material handling equipments.
- Machine production: The machines may have different production rate per unit time. The material handling equipment should be able to handle the maximum output.
- Type of material flow pattern: A horizontal flow pattern may need trucks, overheads bridge cranes, conveyors etc, whereas a vertical flow pattern will require elevators, conveyors, pipes etc…
- Production type: The selection of the material handling equipments depends on type of production such as mass production and batch production. Conveyors are more suitable for mass production on fixed routes and powered trucks and trolleys for batch production.
- Other factors: Some other factors also considered during selection of material handling cost such as cost of material handling equipment, handling costs, life of the equipment and amount of care and maintenance required for the equipment.
The article is authored by R Senthilkumar, Yarn R&D, Super Sales India Ltd – Textile Division, 34A, Kamaraj Road, Coimbatore – 641018 Tamil Nadu. He can be contacted on: Mobile: 9677468590
Material handling equipment in spinning mills
In spinning mill, there are many departments that involve handling of raw material, intermediate products, wastes, finished goods, stores and maintenance tool equipment. During fibre to yarn conversion, materials (raw material, laps, sliver, roving, yarn, and wastes) are stored at different places and transported between departments. The selection of appropriate production machinery and proper layout of spinning mill eliminate as far as possible the need of material handling. In a spinning mill, the chute feed system, and automatic material transportation (ribbon lap, roving bobbin, ring bobbin, cone) reduces the material handling activities to a greater extent, which significantly contributes to productivity enhancement. The selection of appropriate material handling equipment for performing a particular task is crucial in terms of cost minimisation. The various material handling equipment used in departments of spinning mill are summarised in table 1.2.
Bale godown: Spinning mills receive cotton fibres in the form of bales in lorries or trucks. Cotton bales usually weigh around 170 kg in conventional mills, bales are transported with the help of 2, 3 or 4-wheeled industrial trolleys for storing in bale godown one by one which consumes time and requires more workers. Modern mills normally handling large number of bales can use forklifts exclusively for unloading bales from lorry and transporting them to the godown and stackers can be used to stack the bales.
Mixing and blow room department: In a conventional blowroom line, cotton from the mixing to the mixing bale opener is transported by means of a mixing trolley. Use of lift-able spring type pedal operated mixing trolley eliminates spilling of the fibre tufts on the floor leading to poor housekeeping and more waste. This type of trolley can transport up to 30 kg of material at a time. In a conventional blowroom line, blowroom laps are transported manually by the workers keeping one lap at a time on the shoulder. Some modern mills having lap feed system are using lap trolley that can transport 4 to 6 laps at a time. The vertical stacking of laps closer together in the lap trolley may lead to damage the lap surface. Lap produced from blow room must be covered with synthetic cover cloth in order to correct the above problem.
Trolleys used in carding, drawing and comber: Sliver cans (full and empty) are to be transported between cards, draw frames, comber preparatory machines, combers and fly frames. The cans in which sliver get deposited are of various diameter such as 14-inch, 16-inch, 42-inch and 48-inch that are provided with or without castor wheels. Cans that are transported manually by dragging them on the floor would not only spoil the floor but also damage the can and result in wastage of sliver. To overcome the above problem, the sliver can is normally transported by means of can trolley.
Roving bobbins trolley: The doffed roving bobbins are normally placed on the top arm frames and the doffers then carry 8-10 bobbins by hand to the storage place. This practice affects the package quality and sometime may also cause injury to the worker. Roving bobbin trolley can be moved in between fly frames and up to 60 bobbins (30 on each side) can be stacked easily. After doffing, roving bobbins are usually kept in racks and transported to the ring frame by open type trolley or automatic roving bobbin transporting system.
In another model of roving bobbin trolley, the spring-loaded bottom keeps the bobbins at an almost constant height and thus avoids physical strain on the workers and protects the yarn when loading and unloading the trolley.
Ring bobbin trolley: In conventional mills, doffed cops are transferred to baskets or big containers and they are transported to post spinning departments in trolleys. This practice results damage to some cops and entanglements leading to yarn waste. Today, the ring bobbin trolley is used which has two compartments such as one for carrying empty cops and another for keeping doffed cops. Plastic crates can be fitted in the compartments. Each doffer must be given one trolley. Modern mills are equipped with automatic doffing and ring bobbin transportation which drastically reduces yarn waste and labour requirements and improves yarn and package quality.
Winding and packing: Cone/cheese trolleys are used to transport the cone from winding machine to packing section. Packed cone bags or cartons are transported to cone bag godown by carrying them manually. This reduces the capacity of material handling and some time it may cause yarn damage. Platform truck can be used to overcome the above problem.
Automation in roving bobbin transportation
Automation is about improving quality, because frequent contact with the bobbins, which damages the material and impairs quality, is avoided, and many working processes can be simplified and designed to be less labor-intensive. The bobbin transport system provides economic advantage to package handling in ring spinning. It ensures the protection of roving wound around the bobbin, which is highly liable to damage during manual transportation.The train of bobbins is automatically transported from speed frame to the storage area and respective ring frame by selecting the appropriate program in the PLC. Empty bobbins in the ring frame are manually interchanged with full bobbins.
Automation in ring bobbin transportation
The maximum level of automation on the winding process is achieved by a direct link of the ring spinning frames to the winder. The advantage is continuous automatic transfer of the ring bobbins from one machine to the other.The main advantages are:
Yarn quality of the wound package is preserved as bobbins are prepared and automatically doffed on the ringframes, without any operator handling or loading into separate boxes.
Higher efficiency on winder.
Production output flow consistency and timed as a single machine
Minimisation of winding room personnel.
Table 1.1: Benefits associated with effective material handling
- Improving productivity
- Increasing the handling capacity
- Reducing man-power
- Increasing the speed of material movement
- Reducing materials wastage
- Promoting easier and cleaner handling
- Eliminating idle time of machines, equipment and workers
- Reducing fatigue incurred by the workers
- Increasing safety and minimizing accidents
- Locating and stocking material better and in less space
- Minimising production cost, etc.
Arshad FLUXOMATIC plasma treater
Arshad Electronics Pvt Ltd was established in the year 1971, and ever since has been innovative in producing the latest technology and the most advanced systems of Corona treaters and induction cap sealers in India. Built on solid fundamentals of the late AG Moolji, Arshad Electronics carries his legacy of precision and quality with a success streak with over 40 years. The company’s main focus is to deliver the best product at the best price with timely service. To ensure customer satisfaction, the company has established an after-sales service backup in major cities in India as well as other countries. Arshad Electronics aims to achieve perfection and the complete satisfaction of its clients by providing solutions and quick service. With over 300 installations around the world, the company brings forth its range of Corona discharge treaters with latest technology, full functionality and high performance.
Plasma is a partially ionised gas, composed of highly excited atomic, molecular, ionic and radical species of free electrons and photons. Plasma technology is highly innovative in the field of superficial treatment of the materials based on a DBD electric discharge (dielectric barrier discharge). The modifications applied to the surface are on nanometer scale at room temperature. The process involves cleaning, activation grafting and deposition.
Arshad FLUXOMATIC plasma treater
The treater is based on DBD discharge; operates under atmospheric pressure with air or inert gas and several gas mixtures; produces plasma between two or more electrodes in which the fabric runs; speeds up to 20 mI min; treatment on single or double side; fabric width up to 2,000 mm; high tension/ frequency electric generator, with automatic control power, PLC controlled.
Its advantages include:
- lt generates innovative materials and new surface properties.
- lt does not modify the bulk property ofthe material.
- Negligible quantity of chemicals.
- Dry process, which does not require solvents or chemicals dangerous for the environment.
Technology are:
- lt operates at atmospheric pressure
- Continuous Production processes.
- Reduced Process time
- All disadvantages due to the preparation of vacuum plants are avoided.
- It is not necessary to use seal devices.
Applications include: increase of wettability, increase of hydrophilicity, water-repellent and oil-repellent surfaces achieved, biocompatibility (Antibacterial properties of adhesion; affinity to proteins and other bio molecules), dyeable (increase of dyeing speed), print (increase of absorbed calor quantity by textile fibres),
and adhesion (increase of spreading adhesion with specific compounds).
Fabrics: It is applied to fabrics and yarns of natural and artificial fibres without modifying their bulk properties. The organoleptic properties and the transpiration are unchanged. Fabrics with multifunctional properties can be obtained. They can be applied to all textiles working phase from fibre until fibre finishing process. They can be easily introduced into the productive processes.
Substrates: Polypropylene, polyethylene polyester, nylon, natural textile fibres, etc. Fabrics for clothing, fabrics for furnishings, and technical fabrics (filtration, medical and pharmaceutical) and nonwoven fabrics.
For further information:
305 Hammersmith Industrial Estate,
Off Sitladevi Temple Road,Mahim,
Mumbai – 400 016.
Maharashtra, INDIA.
Tel:+91 22 24451709124462628124460383
Email: amoolji@arshadelectronics.com
Web: www.arshade1ectronics.com