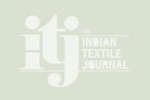
Lipase hydrolysis of poly & poly cotton blends
Enzymatic Hydrolysis on synthetic fibres enhances the hydrophillicity and solves the concerns regarding the environmental issues of Textile Industry, write J Anandha Kumar and Dr M Senthil Kumar.
Enzymatic Hydrolysis on synthetic fibres enhances the hydrophillicity and solves the concerns regarding the environmental issues of Textile Industry, write J Anandha Kumar and Dr M Senthil Kumar.
Polyethylene terephthalate (PET) is one of the most commonly used synthetic fibres. Major advantages of PET are high strength, stretch resistance, washability, wrinkle resistance and abrasion resistance. However, PET has undesirable properties such as pilling, static and lack of dyeability associated with its hydrophobic nature. PET fibre has a low moisture regain about 0.4 per cent. The most conventional and industrially way to modify polyester fabrics is an alkaline treatment. But alkaline treatment affects on strength of polyester fabrics.
A recent alternative is the use of enzymes in surface modification.[8, 10] Studies about enzymatic treatment of polyester have been focused on biodegradation of aliphatic polyester using a lipase, and biological synthesis of polymer with enzymes. Only a few studies have been reported regarding enzymatic modification of PET fabric.Improvement hydrophilicity of polyesters by hydrolysis of ester bonds has been reported.[14] These studies focus that the applicable enzymes are lipases and polyesterases. Lipase is known to hydrolyse water-insoluble esters or triglycerides composed of long chain fatty acids.[15] Thus, the application and studies about lipases in textile processing have been focused on detergent. If enzymes can hydrolyse ester linkage in PET fabrics, polar hydroxyl (-OH) and carboxyl (-COOH) groups will be formed on the surface of PET fabrics. As a result, moisture regains and wettability will improve due to the forming of hydrophilic groups on PET fabrics. Carboxyl and hydroxyl groups on PET fabrics can be evaluated through dyeability of disperse dyes.
Materials and methods
In the present work, 100 per cent polyester fabric is taken to know the effect of enzyme treatment on the structural modifications. The fabric specifications and enzyme specifications are given in the Table I and II. The fabrics are subjected to washing treatment to eliminate the presence of impurities as well as finishes. The fabrics are treated with enzymes with varying concentrations, treatment time as well as temperature. The fabrics selected for the experiments are subjected to alkali treatment as well as lipase treatment with different concentrations namely 5 per cent, 10 per cent, 15 per cent. The fabrics are dyed with disperse dye with a shade level of 5 per cent on weight of the fabric. The treated fabrics are dyed using disperse dye with high temperature high pressure dyeing machine.
The fabric weave is a plain weave and the chemicals used in this work was laboratory grade reagents.
Treatment: Polyester fabrics were treated with an aqueous solution containing different concentrations (5 per cent, 10.0 per cent, 15 per cent o.w.f.) of Lipolase 100L-EX. The reaction was conducted at 40° C at pH 8. The material-to-liquor ratio was 1:30.The fabrics were treated with sodium hydroxide solution for the same concentrations.
Dyeing: Enzyme-treated as well as sodium hydroxide treated polyester fabrics were dyed in an aqueous solution containing 5 per cent (o.w.f.) using disperse dye.
Analytical methods
Weight loss evaluation: The weight loss (WL) is expressed as relative WL according to the equation: WL = 100*(W1– W2)/W1); where W1 and W2 are the weights of the samples before and after treatment respectively. Wicking height measurement: The wicking heights of the treated fabrics are tested as per AATCC Test Method 197 to evaluate the specimens to transport liquid along them. The distance at a given time is measured. Absorbency measurement: The water absorbancy of treated fabrics are tested as per AATCC Test Method 79 to know the time taken by a drop of water placed on the fabric surface to completely absorb.
Scanning Electron Microscope (SEM) analysis: The Enzyme treated polyester and blended samples are analysed through Scanning Electron Microscope (SEM) to know the effect of enzyme treatment on the surface etching. The Fourier Transform Infra Red spectroscopy (FTIR) Analysis: FTIR tests were carried out to reveal the additional functional groups due to alkaline and enzymatic hydrolysis.
Water vapour permeability measurement: The water vapour transmission rate of treated fabrics are tested as per ASTM D6701-16 using water vapour permeability tester.
Colour measurements: Measurement and analysis color measurements: The relative color strength (K/S) of dyed fabrics was measured by the light reflectance technique using Macberth Reflectance type spectrophotometer.
Low stress mechanical properties evaluation:
The Kawabata evaluation system (KESF) tester is used to measure the low stress mechanical properties of treated fabrics.
Results and discussions
It is understood from the Table 3 that the increase in concentration of enzyme causes increase in weight loss in both the cases. The weight loss is very high for alkaline treated whereas the loss in weight of lipase treated is very low for the similar concentrations. It is understood from Table 4 that the increase in temperature increases the weight loss percentages and increase in treatment time increases the weight loss percentages.Effect on absorbency: From the Table 5 it is understood that lipase treated samples are having higher absorbency characteristics compared with the untreated fabrics and alkaline treated fabrics.Effect of lipase treatment on surface characteristics polyester and blended fabrics: The Enzyme treated polyester and blended samples are analysed through Scanning Electron Microscope (SEM) to know the effect of enzyme treatment on the surface etching. The fabric samples are magnified to (5000X).The SEM photographs of the Alkaline treated, lipase treated and the untreated samples are magnified to the extent possible to understand the effect of various treatments respectively. The extent of damage is shown in figure 1.
From the Figures 1 and 2 it is understood that alkali treatment offers more surface itching which causes heavy weight loss where as the lipase treatment offers gentle treatment which hydrolyses the polyester. However lipase enzyme attacks the polymer chain which causes a mild etching noticed in the photographs. It is mainly attributed to the weakening of polyester polymer chain which degrades the fibre due to alkaline treatment. The enzymatic method of treatment offers low weight loss due to surface level etching.
Effect of lipase treatment on moisture regain: The Fourier Transform Infra Red spectroscopy tests reveal the additional functional groups due to alkaline and enzymatic hydrolysis. The addition of hydroxyl groups in polyester is responsible for the hydrophillicity. The following comparative FT-IR spectrum reveals the modification in the functional chains which are responsible for the property changes.
From the Figure 3 it is noted that the following additional groups are present in the treated fabrics. The Table 6 illustrates the presence of various functional groups in the treated. The groups presence are identified as aromatic ring, alkynes, esters, hydrogen bonded and carboxylic acids. The stretching in the region of 3600-3200 is responsible for the hydrophillicity of lipase and alkaline hydrolysed polyester. The stretching is very high in the case of lipase hydrolysed polyester which makes the enzyme treated more hydrophilic. It is also noted the presence of basic functional groups inherent in the polyester materials.
From the Figure 4 it is noted that the following additional groups are present in the treated fabrics. The Table 7 illustrates the presence of various functional groups in the treated groups. The groups’ presences are identified as aromatic ring, alkynes, esters, hydrogen bonded, carboxylic acids, and CH2,. The stretching in the region of 3600-3350 is responsible for the hydrophillicity of lipase and alkaline hydrolysed polyester/cotton blends.. It is also noted the presence of basic functional groups inherent in the polyester cotton materials like aromatic ring and CH2.The presence of carboxylic acids are noted in the stretch of 3000-2500.
Effect of lipase treatment on Water vapour permeability of polyester and blends: The lipase treatment of polyester fabrics enhances the comfort characteristics of the polyester. Since the treated fabrics are more hydrophilic due to the addition of hydroxyl groups in their chain. The untreated polyester and the blended fabric with the treated fabrics are subjected to assess the rate of water vapour transmission.
The vapour permeability tester tests the rate of water vapour transmission in terms of gms/m2/day.From the Table 8 it is understood that the alkaline and lipase treated polyester fabrics are having improved water vapour permeability when compared with the untreated polyester fabrics. It is mainly due to the degradation of chain links and the addition of hydroxyl groups. Similar trend is observed in blends also. The improvements in blends are mainly due to the enhancement of hydrophilic groups in polyester whereas cotton in the blend possesses inherent hydrophillicity.
Effect of enzyme treatment on dye uptake of polyester fabrics: The alkaline treated, lipase treated and dyed fabrics are tested by reflectance type spectrophotometer to know the K/S values. These values help to understand the difference in lustre as well as colour values. The treatment offers better dye uptake which enhances the colour values.
From the Table 9 and Figure 5 it is understood that lipase treated fabrics shows higher reflectance values and lower K/S values. Similar trend is observed in dyed fabrics. This clearly shows that treatment enhances the dye uptake of the polyester fabrics.
From the Table 10 and figure 6 it is understood that lipase treated fabrics shows higher reflectance values and lower K/S values. Similar trend is observed in dyed fabrics. This clearly shows that treatment enhances the dye uptake of the polyester fabrics.
Compression properties: The Kawabata evaluation testes are carried out for lipase treated and untreated fabrics of polyester. Compression and shear properties are evaluated since it reveals the effectiveness of the enzyme treatment.
From Table 11 it is understood that lipase treatment reduces the linearity of compression and compression energy in polyester and the blends. The compression resiliency enhances for polyester fabrics whereas in polyester/cotton blends the effect is not much noticed due to the presence of blend component. The enzyme treatment makes the fabric much softer and it retains its original shape as quickly as possible while applying low stress load.
From Table 12 it is understood that lipase treatment reduces the linearity of compression and compression energy in polyester and the blends. The compression resiliency enhances for blended fabrics. The enzyme treatment makes the fabric much softer and it retains its original shape as quickly as possible while applying low stress load. Shear properties: It is the resistance to rotational movement of the warp and weft threads within the fabric when subjected to low levels of shear deformation. Lower the value of fabric shear rigidity more readily the fabric will conform to three dimensional structures.
From the Table 13 it is possible to infer that lipase treatment makes the polyester fabric with low shear rigidity which indicates that the fabric will conform to three dimensional structures while applying low stress.
From the Table 14 it is possible to infer that lipase treatment makes the polyester blended fabric with low shear rigidity which indicates that the fabric will conform to three dimensional structures while applying low stress. For polyester/cotton blends the dyed sample shows low shear rigidity. The alkaline and lipase treated polyester/cotton blends shows low shear rigidity compared to the untreated fabric
Conclusions
The following conclusions were drawn from this work:
References
Table 1: Fabrics specification
Material | Linear Density | Ends/Inch | Picks/Inch | Thickness (mm) | GSM |
---|---|---|---|---|---|
Polyester (100%) | 75*150 D | 120 | 94 | 0.18 | 82 |
Polyester/ Cotton (67/33) | 108*86 D | 70 | 56 | 0.28 | 60 |
Table 2: Enzyme specification
Name of the Enzyme | Activity |
---|---|
Lipolase 100L-EX | 100,000 U/g |
Table 3: Effect of lipase treatment on weight loss of polyester and blends
Sr. No. | Materials | 5% | 5% | 10% | 10% | 15% | 15% |
---|---|---|---|---|---|---|---|
Polyester | Polyester/cotton | Polyester | Polyester/cotton | Polyester | Polyester/cotton | ||
1. | Alkaline treated weight loss (%) | 7.14% | 5.7% | 12% | 11% | 22% | 14% |
2. | Lipase treated weight loss (%) | 2% | 1.3% | 2.6% | 2% | 4.6% | 3.3% |
Table 4: Weight loss of alkaline treated fabrics at different Treatment time and Temperature
Time (hrs) | Temperature (° c) | Temperature (° c) | Temperature (° c) |
---|---|---|---|
60 | 70 | 80 | |
1 | 2.4 | 3.8 | 6.1 |
2 | 4.2 | 6.3 | 11.6 |
4 | 7.6 | 11.5 | 21.7 |
6 | 11.8 | 14.7 | 33.0 |
8 | 13.4 | 23.5 | 47.2 |
Table 5: Influence of lipase treatment on absorbency of polyester
Sr. No | Fabrics | Wicking Height (Cm) | Wicking Height (Cm) | Drop Test (Sec) | Drop Test (Sec) |
---|---|---|---|---|---|
Polyester | Polyester | Polyester/cotton | Polyester | Polyester/cotton | |
1. | Un treated fabric | 2.5 | 3.0 | 4.8 | 5 |
2. | Alkaline treated fabric | 5.9 | 6.5 | 3.5 | 3 |
3. | Enzyme treated fabric | 6 | 7.5 | 2.8 | 2 |
Table 6: Functional group identification of polyester
Group | Vibration | Type | Range | Inference |
---|---|---|---|---|
Aromatic Ring | Ring Stretch | Symmetric | 1600,1500 stretch | C=C |
Alkynes | Bend | Band | 700-610(b) bend | C-H |
Hydrogen-bonded | Stretch | OH stretch | 3600-3200(b) stretch | O-H |
Esters | Stretch | C=O | 1760-1670(s) stretch | C=O |
Carboxylic acids | Stretch | Anti symmetric | 3000-2500(b) stretch | COOH |
Table 7 Functional Group Identification of Polyester/Cotton Blend
Group | Vibration | Type | Range | Inference |
---|---|---|---|---|
Aromatic Ring | Ring Stretch | Symmetric | 1600,1500 stretch | C=C |
Alkynes | Bend | Band | 700-610(b) bend | C-H |
Hydrogen-bonded | Stretch | OH stretch | 3600-3350(b) stretch | O-H |
Esters | Stretch | C=O | 1760-1670(s) stretch | C=O |
Carboxylic acids | Stretch | Anti symmetric | 3000-2500(b) stretch | COOH |
CH2 | Bend | Scissors | 1455 | CH2 |
Table 8: Water vapour permeability of lipase treated polyester
Treatment type | Water vapour permeability |
---|---|
(gms/m2/day) | |
Untreated Polyester fabric (100%) | 1260 |
Alkaline Treated Polyester Fabric | 1660 |
Lipase Treated Polyester Fabric | 1980 |
Dyed Enzyme Treated Fabric | 2761 |
Untreated Polyester/Cotton fabric (67/33) | 1676 |
Alkaline Treated Polyester/Cotton Fabric(67/33) | 2761 |
Lipase Treated Polyester/Cotton Fabric(67/33) | 3055 |
Dyed Enzyme Treated P/C Fabric | 2942 |
Table 9: Polyester fabric K/S values
Type of Treatment | Wave length(nm)/ K/S Value | Wave length(nm)/ K/S Value | Wave length(nm)/ K/S Value | Wave length(nm)/ K/S Value | Wave length(nm)/ K/S Value | Wave length(nm)/ K/S Value | Wave length(nm)/ K/S Value |
---|---|---|---|---|---|---|---|
400 |