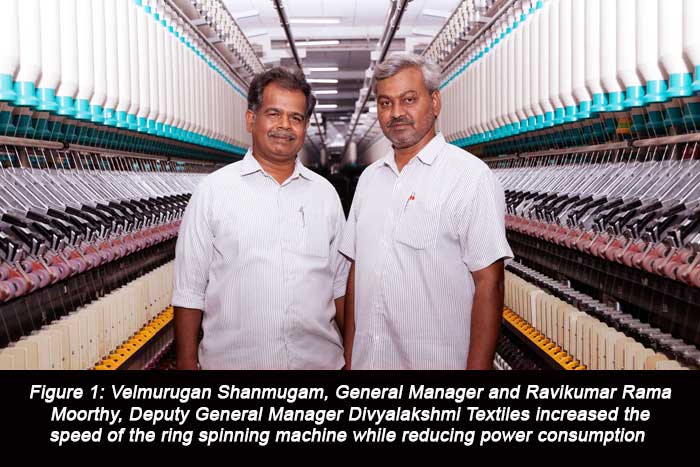
Leading Spinning Mills in India Trust in Novibra’s LENA Spindles
LENA spindles deliver fast speeds and high productivity while consuming as little energy as possible. On top of this, spinning mills also report that Novibra’s modern spindle type reduces noise levels
The ability to save energy and increase production levels are crucial factors for spinning mills to remain competitive. For years, Novibra has been addressing these needs by developing highly performing, energy-saving spindles. The launch of LENA marked a revolution in spindle technology, with energy savings of up to 6 per cent and speeds of up to 30 000 rpm. Such achievements were only possible through innovative optimisations. The smaller wharve diameter allows the machine to operate at lower speed while keeping the same spindle speed and thus, the desired yarn count and twist.
An innovative technical solution was essential for this lower energy consumption. The footstep bearing unit consists of a radial and an axial part. The radial bearing was redesigned as a hydrodynamic plain bearing with an internal diameter of three millimeters, which directly affects power consumption. The small diameter of the shaft’s tip allows additional energy savings.
Reduced noise and extended lifetime
Nowadays, a ring spinning machine runs with at least 1 200 spindles, the latest models even feature up to 1 824 spindles. The noise level of ten machines with 18 240 spindles can therefore have an adverse impact on the wellbeing of the operators. For efficient noise reduction, LENA features a second damping system. This unique and well proven Noise Absorbing System Assembly – known from Novibra NASA spindles – not only reduces the noise level but also provides additional protection to the spindle bearings, ensuring minimum neck bearing load. Thanks to lifetime grease filled in the damping chamber, micro vibrations are absorbed. At the highest speeds, the damping system plays a decisive role, it significantly increases the service life.
Leading spinning mills trust in LENA spindles
Customers in India have been enjoying the benefits of LENA including Divyalakshmi Mills, Sri Jayajothi and Company or Sportking Group.
Divyalakshmi counts a total of 12 000 LENA spindles. The company successfully managed to increase the speed of their 15-year-old machines without changing the motors and drive to 24 000 rpm for Ne 80 combed cotton compact yarn. Besides the production increase, Divyalakshmi was able to reduce energy consumption by up to 12 percent. “With Novibra’s LENA spindles with CROCOdoff we were able to achieve our goal of increasing the speed of the ring frame while reducing the power consumption by one unit per kg of yarn produced. Thanks to CROCOdoff we managed to significantly reduce the restarting yarn breaks after doffing while simultaneously reducing the underwinding waste,” said Velmurugan Shanmugam, General Manager, Divyalakshmi Mills (Figure 1).
Sri Jayajothi has been running their LENA spindles at 26 400 rpm for four years already. As a result, they increased their productivity of 100 per cent combed compact yarn Ne 60 while saving 7 per cent of their energy consumption. “Our positive experience with LENA spindles on the existing spinning machine with respect to speed increase and energy saving made LENA a must for our future spindle acquisitions,” confirmed Venkadesan Duriasamy, General Manager, Sri Jayajothi and Company (Figure 2).
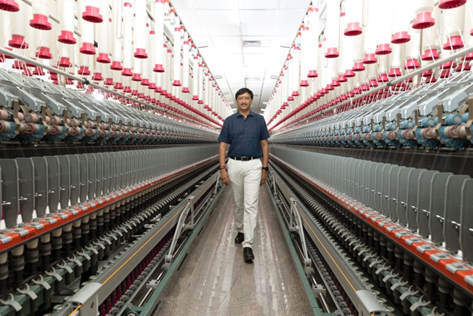
Figure 2: For Venkadesan Duriasamy, General Manager, Sri Jayajothi and Company LENA is a must for future acquisitions.
Sportking Group runs almost 30 000 LENA spindles. The company managed to increase the spindle speed by 5 per cent in their two main production lines – 100 per cent combed cotton yarn count Ne 40 and polyester/cotton blends Ne 40. “We were able to achieve about 8 per cent reduction in power consumption, reduced restarting breaks after doffing, eliminated the issue of low twist per inch in polyester cotton processing and a reduction in the noise level of the ring frame,” shared Shiv Kumar Sharma, President of Sportking Group (Figure 3).
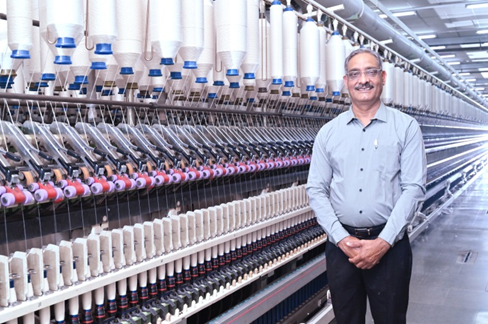
Figure 3: Shiv Kumar Sharma, President, Sportking Group confirmed about 8 per cent reduction in power consumption.
Spindles provide the best results when selected for their intended use. Yarn count, speed, lifetime, maintenance, or energy consumption requirements must be considered in the selection process. Novibra sales teams assist customers in choosing the right spindle to achieve the optimum performance.
About Rieter
Rieter is the world’s leading supplier of systems for manufacturing yarn from staple fibers in spinning mills. Based in Winterthur (Switzerland), the company develops and manufactures machinery, systems and components used to convert natural and
man-made fibers and their blends into yarns in the most cost-efficient manner. Cutting-edge spinning technology from Rieter contributes to sustainability in the textile value chain by minimising the use of resources. Rieter has been in business for more than 225 years, has 18 production locations in ten countries and employs a global workforce of around 5 100, about 16 per cent of whom are based in Switzerland.
About Novibra
Novibra, the world’s leading supplier of high-speed spindles, is a subsidiary of the Rieter Group. The company, based in Boskovice (Czech Republic), creates customer value through system expertise, innovative solutions, after sales excellence and global presence. The leading position of Novibra spindles is based on patented design of spindle insert and the highest quality of the production. Almost all renowned manufacturers of ring spinning machines specify Novibra spindles for high performance.