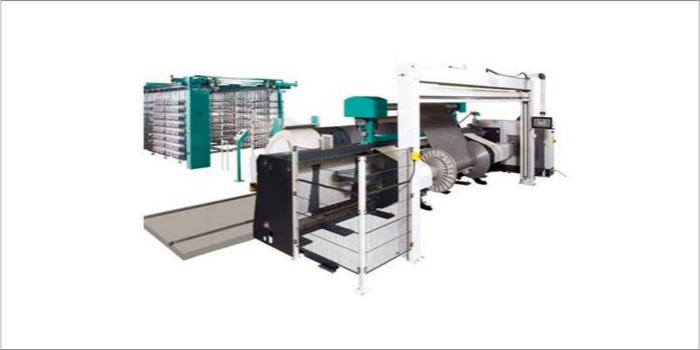
Karl Mayer’s PROWARP & MULTI-MATIC 32 impress
PROWARP sectional warping machine offers utmost flexibility, precision and efficiency, and can be equipped with the latest communication, measuring and control technology. MULTI-MATIC 32 is a highly productive warping machine for the production of sample and production warps with short running length.
With the PROWARP and MULTI-MATIC 32, Karl Mayer presented innovative series machines for weaving preparation at ITMA 2019. With their special performance profiles, they are generating a great deal of interest on the market. The PROWARP sectional warping machine offers utmost flexibility, precision and efficiency, and can be equipped with the latest communication, measuring and control technology. The MULTI-MATIC 32 is a highly productive warping machine for the production of sample and production warps with short running length, which is particularly well received by manufacturers in the high-quality fashion sector. Both machine types have already been sold several times worldwide.
PROWARP
The selectable, innovative solutions offered by the PROWARP configuration include PROACTIVE warping, a system for optimising warp beam quality that will be cloudbased in future. The new development comprises a total of three levels and the amount of information increases with each one. Level 1 provides protocols with data on warping or beaming quality, which are supplemented in level 2 by active quality management with a customer-defined star rating. This extension level also offers the possibility of integrating a modern high-resolution camera system. The innovative solution records measurements including the band width and band set-up – i.e. the distance from band to band or to the cone.
In addition, level 3 offers evaluations and diagrams for the single thread tensions of the optional MULTIGUARD yarn stop motion. In levels 2 and 3, the data is also exchanged with the KM.ON cloud via the KM.ON device k.ey. Using cloud networking, a real-time machine dashboard can be created and, in future, it can be synchronised with new start parameters via an algorithm. If deviations occur, production data can be optimised and adopted for repeat orders if desired. This allows the beam quality to be improved, regardless of the operating personnel.
Further systems for ensuring high product quality relate to regulating the layer thickness during the sectional warping process. To do so, either the yarn tension at the creel exit or, if available, the speed of the yarn feeding elements is adjusted. Fine adjustment is triggered by measured values taken from the layer thickness of the individual sections, which are continuously recorded by laser in a contactless manner and compared with the values of a master section. PROWARP ensures a high degree of quality reproducibility with well-thought-out solutions to manage orders and production data.
Flexible use, best performance values
In addition to product quality, the PROWARP is also efficient. An innovative order management system not only enables weaving mills to be up to 5 per cent more efficient and performance to be increased by up to 30 per cent in weaving preparation compared to standard market counterparts, but yarn waste is also reduced. A high degree of application flexibility completes the PROWARP performance package.
The new high-performance sectional warping machine is suitable for all material types and combinations, and guarantees a constant winding build-up over the entire yarn spectrum. It manufactures production warps that are used in technical and standard applications. It has a special configuration to produce warp beams for technical woven fabrics, determined by the suffix “HT”. For the apparel and home textiles sector, PROWARP offers warp beams for creating detailed patterns and designs of different colours. To meet the wide range of applications, the PROWARP is designed for pulling forces of up to 40,000 N and has a working width of up to 5.6 m. It reaches a maximum speed of 1,000 m/min for warping and 500 m/min for beaming.
Model change by 2021
Since its launch as a series model at ITMA 2019, the PROWARP has been ordered by around ten manufacturers. Orders predominantly came from the technical sector and mostly from Europe; their market distribution will also see a slight model change. Karl Mayer’s Warp Preparation Business Unit plans to merge the ERGOTEC and OPT-O-MATIC product lines and gradually replace them with PROWARP. “We plan to complete the model changeover next year,” said Development Manager Martin Fuhr. Exceptions will, of course, be possible.
MULTI-MATIC 32
The MULTI-MATIC 32 particularly stands out thanks to it excellent price-performance ratio. With the benefit of eight pattern threads, the single-end warp sampling machine offers a third more performance compared to the previous model, but without costing more. It is most efficient at run lengths of 200 to 400 m. When equipped with KAMCOS 2, the MULTI-MATIC 32 can be digitally networked via an integrated OPC-UA interface, which means operating data can be gathered in real time. In addition, the reduced number of bobbins allows for a smaller creel, which can be equipped with rollers and arranged differently depending on the yarn quality.
The innovative MULTI-MATIC 32 was designed to replace the GOM-24. It processes bobbins with greater yarn volume and thus with longer change intervals than the model in the GIR-O-MATIC series, which cuts handling effort and yarn storage costs. Overall, the priceperformance ratio of the MULTI-MATIC 32 is up to 30 per cent better than that of the GOM-24. The MULTI-MATIC 32 also stands out when compared with the sectional warping machine, another adjacent model in Karl Mayer’s product portfolio: the low number of bobbins means that there is no need to split them up by rewinding them onto several bobbins.
Development work on JERSEY EVOLUTION continues
At Interfilière in Paris in January 2020, Karl Mayer launched its first series of warp knitted jersey articles, garnering great interest, especially among international lingerie brands. These supple, next-to-skin fabrics are called JERSEY EVOLUTION. They were produced on the high-performance tricot machine HKS 2-S, which was used with a high machine gauge to create a sophisticated lapping design. This results in highly elastic fabrics. It is possible to stretch the fabric by up to 245 per cent, while still retaining a high rebound force. The elastane threads were specially incorporated to create cut-resistant edges.
In addition, JERSEY EVOLUTION fabrics offer a soft, smooth surface and a flowing drape, just like their circular knitted counterparts. Unlike these, however, knitted jersey goods can be produced highly efficiently: a high-performance tricot machine can replace up to 2.5 circular knitting machines. Warp knitting running costs are also lower since the needle units must be replaced less frequently. Compared to circular knitting machines, these key components can be used around six times longer, thus halving the cost per set. Following the successful launch, Karl Mayer created a second JERSEY EVOLUTION series. As part of recent development work, the lapping and yarn use have been modified to achieve different fabric weights and stretch values. With regard to the lapping, variants and patterns were chosen which are commonly used by Karl Mayer’s customers and which had already proved to be highly effective in the first series.
One bodysuit for every occasion
As can be seen with the strapless eye-catcher on this page, Karl Mayer has developed a garment that can be worn universally and is also extremely efficient to produce. Half bodysuit, half swimsuit, the chic one-piece cuts a good figure both when sunbathing and when strolling around town. The fabric for this street & beachwear is produced on an ML 41 in E 28. For this purpose, the multibar raschel machine produces fabric lines of seamlessly lined up transparent and opaque striped areas, from which – following a 90 degree turn – the back and front of the bodysuit can be separated easily and without much waste.
The pattern guide bars allow for incorporation of the necessary cutting marks, as well as effective designs. Multibar technology opens the door to interesting possibilities in terms of design. In particular transparent striped sections on the base of sporty Powernet within a closed ground construction can be adorned with a feminine lace touch to great effect. The width of the transparent and opaque areas can be changed at will thanks to the threading on the ML 41. The 134-inch machine produces up to three such pre-made-up fabric lines simultaneously and incorporates draw threads between them for easy separation by hand. All that needs to be done to finish the garment, is to stitch the side seams at the front and back together. There is no need for hems at the leg openings because the technology used for warp knitted textiles offers high edge stability. The production process could hardly be more efficient!