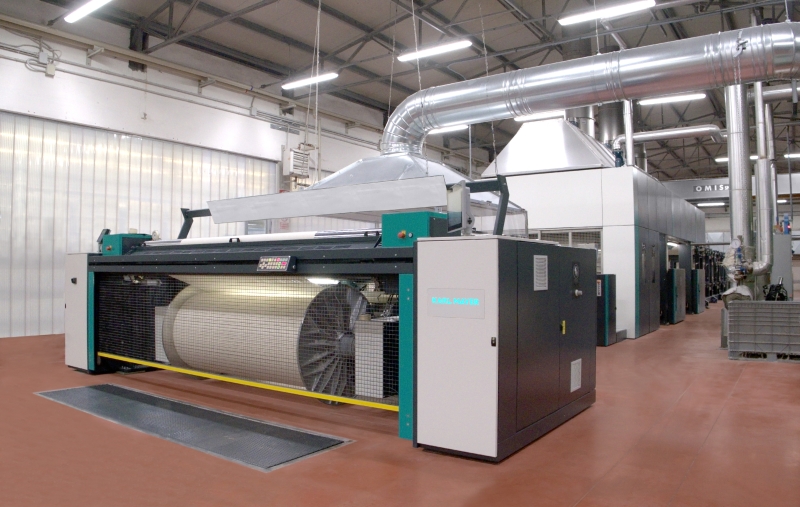
Karl Mayer Group’s Cascade System for Sizing Machines and Dyeing Systems
The customer benefits from significantly lower energy costs and CO2 emissions.
A Karl Mayer Group solution for verifiable inline energy recycling on sizing machines and dyeing systems.
Energy consumption is an important success factor for textile companies. For finishing companies, it can lead to costs of up to 15 per cent of turnover. The industry average for energy expenditure is around 5 per cent.
For both economic and sustainability reasons, manufacturers are increasingly looking for innovative technical solutions. When it comes to the energy-intensive drying processes in warp preparation, the Karl Mayer Group has the answer: The global player has developed a sophisticated system for considerable energy savings when operating the cylinder dryers in its Prosize sizing machines and Bluedye dyeing plant.
Saving costs with inline energy recycling
The innovation is called Cascade and focuses on steam as a heating medium in cylinder dryers. And for good reason: according to the IPCC report by ITMF Zurich, one tonne of steam cost between $ 20 and just under $ 27 internationally in 2021. The new solution relies on reuse to reduce the amount of process energy required.
“Cascade recirculates parts of the process steam in cylinder dryers, enabling genuine, efficient energy recycling within the machine,” explains Karl-Heinz Vaassen, Head of Textile Drying at Karl Mayer.
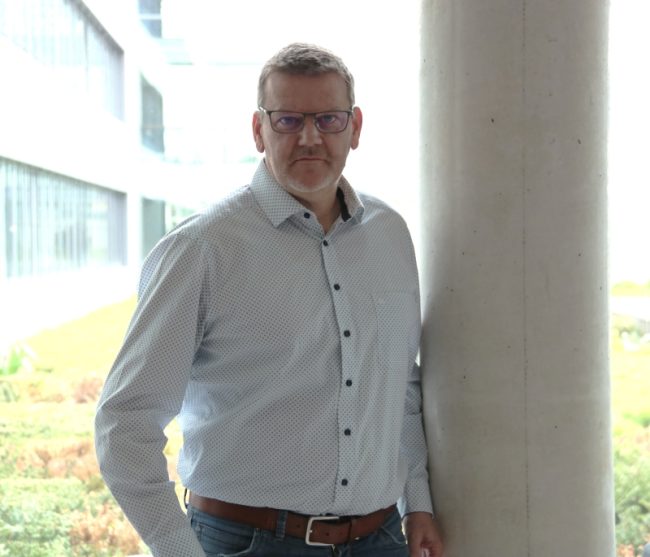
The customer benefits from significantly lower energy costs and CO2 emissions. With a view to the Asian market, a dryer with 14 cylinders and a running time of 7,000 working hours can achieve cost savings of up to $ 17,000 per year.
Precise, real savings values are available when looking at the machine dashboard. A sensor provides real-time data on the amount of steam circulating in the circuit, from which the corresponding reduction in CO2 equivalents can be calculated.
Utilising the pressure drop
Cascade reuses part of the invested process energy and uses the flash-steam in conjunction with the pressure ratios, which – nomen est omen – decrease in cascades in the different zones of the cylinder dryer.
The highest working pressure prevails in the first cylinder section. The heat transfer medium steam emits large amounts of energy for yarn drying and condenses without temperature loss.
The resulting hot condensate is not immediately discharged from the machine, but is instead fed into a flash tank, where vapor exhaust is formed as a result of the pressure reduction. In conventional systems, the carrier medium for gases is only created in the return line towards the boiler house and is eliminated as undesirable. Instead of being utilised in the process, it escapes into the environment. With the Cascade system, this “freshly recycled steam” is used for the heat supply in the second cylinder section, but not without prior treatment.
In the system patented by Karl Mayer, the recycled steam is intelligently mixed with live steam and thus raised to the level of the required process conditions for use in the cylinder section at the end of the dryer. Here, the fabric moisture is reduced to the desired residual value at medium pressure and temperature conditions.
Market launch is underway
Cascade was filed for patent by the Karl Mayer Group. It was published in September 2023.
The innovative solution at no extra charge was presented at ITM 2024 in Istanbul and was a visitor highlight at the Karl Mayer Group stand.
From January 2024, Cascade will be part of the Prosize as standard. The first sizing machine with the upgrade for greater energy efficiency will be delivered in the second quarter of this year. It will go to a manufacturer in Europe. In the next step, Cascade will be integrated into other dryer types and will also be available for the Bluedye.