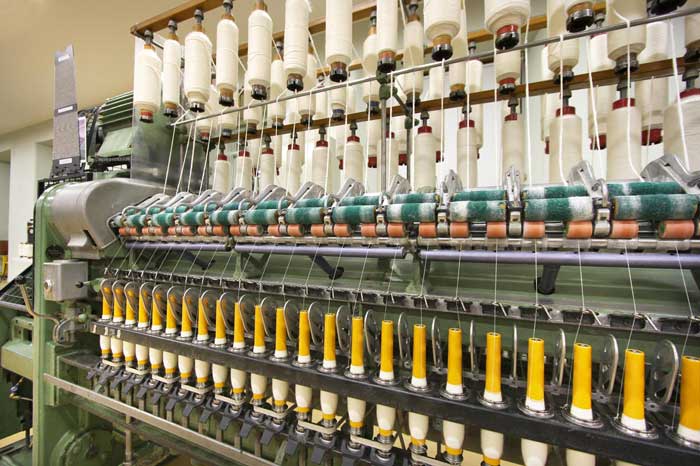
Improving yarn imperfections by optimisation of roller space settings in ring frame
This is to improve yarn Imperfections and CVm of 40 Ne yarn by changing the distance of top roller space settings in ring frame machine.
In spinning industries, the contribution of raw material cost accounts for 50 to 60 per cent of the total manufacturing cost. The spinners, in general, are particularly concentrate in manufacturing quality products at lower manufacturing cost, best yarn quality and also at affordable manufacturing cost. Nevertheless, the yarn quality is decided by many factors which have close inter relationship with other. For example, the fibre properties and the running performance on the machineries, speeds, settings etc. In the manufacturing of 100% carded cotton yarns, apart from the fibre properties, machinery maintenance and processing conditions influence the quality of the yarns produced. The contribution of the blow room and card is the major ones which accounts for 70 per cent of the carded yarn quality. The remaining 30 per cent is contributed by other processes such as draw frame, roving and ring frames.
⦁ Materials and methods
Materials
The fibre materials used in the study is 100 per cent cotton of medium staple variety. A judicious selection of setting based on the fibre material processed has to be taken in to consideration.The cotton fibre properties tested in Uster HVI 1000 is given in Table 1.
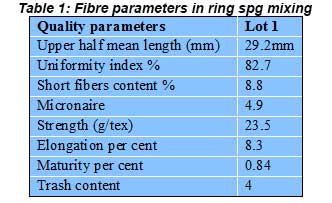
Methods
The cotton samples were tested for their fibres charachterstics in HVI 1000 testing instrument. The cotton material was processed through blow room, carding, drawing, roving and spinning to produce Ne 40 100 per cent carded cotton. For both the samples, the carding and breaker drowframe sliver count maintained was 0.105 Ne. The finisher drow frame and roving count was maintained as 0.11 and 1 Ne respectively. The delivery speed of the ring machine is 10000 rpm and the actual yarn twist (T/M) is 1144. The trials were conducted at the ring machine by changing the top arm settings. Comparative studies on yarn quality were conducted in a controlled manner before and after the setting change. The roll space settings in Ring frame is given in Table 2. The yarn samples collected were evaluated for their yarn quality in evenness tester.
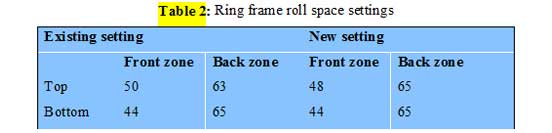
The top roll settings were changed keeping the bottom roller settings constant. The existing and new top roll settings in ring frame is shown in Figures 1 & 2.
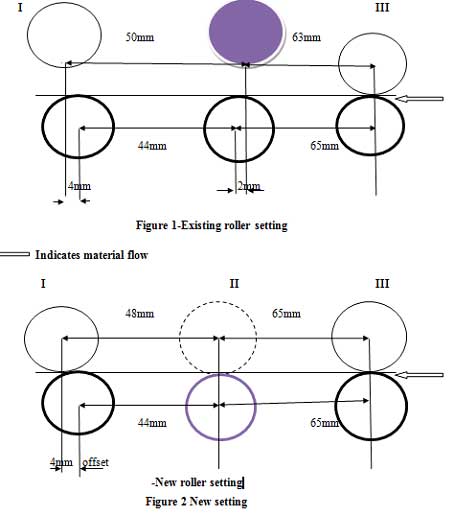
The yarn samples collected for both the trials were tested for their yarn quality attributes such as cofiecient variation of mass, unevenness, imperfections and hairiness index in Uster Tester. The experimental samples were conditioned in a standard atmosphere of 65 ± 2 per cent RH and 20 º C ± 2 º C temperature for 24 h. Each sample was subjected for 20 tests to determine the average value of U per cent, CVm, imperfectionss and hairiness index.
2.0. Results and discussions
The existing setting front and back zone 50/63 and the new setting 48/65 were compared for their yarn quality improvements is given in Table 3. It is observed that the thick places in the yarn has got reduced from 1271/km to 1032/km and neps from 1822 /km to 1600/km. It means there is an inprovement of 18 per cent & 12 per cent in thick places and neps. However, there is no change in thin places between these two trials. There is an overall improvement in total yarn imperfections/km by around 14 per cent, Hariness by 1.6 per cent and U per cent by 2.75 per cent respectively. A graphical representation of the yarn quality is shown in Figure 3.
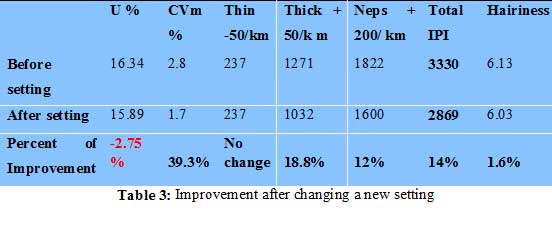
Figure 3: Percent of improvement yarn parameter
The improvement in yarn imperfection with the new setting may be attributed to the fact that the space setting between the top rollers front drafting zone were shifted by 2mm and similarly the space setting btween the top back zone rollers were increased initially by 2mm. Due to this, the floating fibres were controlled between the rollers due to higher fibre-to-fibre cohesion, which leads to better control on short fibre motion while drafting. The improvement in the yarn appearence before and after the top roll space settings in ring frame is shown in Figure 4.
3.0. Conclusions
This study was conducted to improve yarn Imperfections and CVm of 40 Ne yarn by changing the distance of top roller space settings in ring frame machine. A small change in settings has yielded a significant improvement in all the yarn quality parameters. However, many other variables such as break draft, spacer and top arm loading conditions have to be tried for their influence on yarn quality. Based on the fibre properties such as fibre length, other setting trials can also be conducted for the overall improvement in yarn quality and running performance like end breakages.
References
- https://textilevaluechain.in/in-depth-analysis/articles/textile-articles/spinning-geometry-of-ring-spinning-machine/
- Rotor and Compact Comparing Quality Parameters of Yarn Produced by Ring Spinning System. Zahidul Islam, MDAssistant Professor, Department of Yarn Engineering, Bangladesh ,University of Textiles, Dhaka, Bangladesh
- Uster, Uster Statistics, Uster, Uster, Switzerland, 2018.
- Study on the Influence of Fiber Properties on Yarn Imperfections in Ring Spun Yarns⦁ J. Ochola, ⦁ J. Kisato, ⦁ L. Kinuthia, ⦁ J. Mwasiagi and ⦁ A. Waithaka
- Analysis on the Defects in Yarn Manufacturing Process & its Prevention in Textile Industry Neha Gupta Department of Mechanical Engineering, Integral University, Lucknow, India
- Indian Journal of .Fibre & Textile Research Vol. 36, September 2011, pp. 211-214
- Balasubramanian N, A study of the irregularities added in apron drafting, Text Res J, 39 (1969) 155.
- Indian Journal of Fibre & Textile Research Vol. 41, June 2016, pp. 121-128
- Indian Jornal of textile Research vol.14. December 1989. Pp.147-150