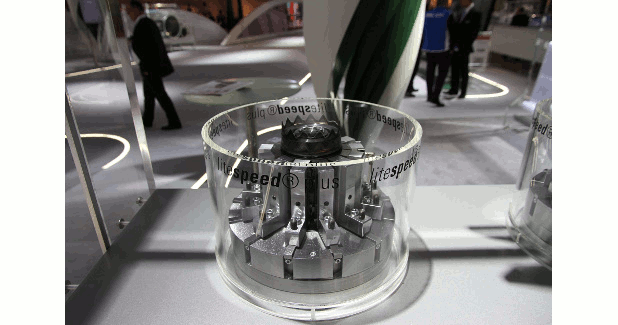
Groz-Beckert’s litespeed plus for increased energy saving
The litespeed needles were specially designed by Groz-Beckert for use in (high-performance) circular knitting machines.
The litespeed needles were specially designed by Groz-Beckert for use in (high-performance) circular knitting machines.
Groz-Beckert a few months back last year presented its various offerings from all six product areas at the ITMA Asia+CITME. The Knitting (knitting and warp knitting) product area presented its portfolio for circular knitting, flat knitting, leg wear and warp knitting. The division placed a particular focus on a system-oriented approach: Thanks to extremely tight production tolerances, needles and system parts from a single source guarantee precisely coordinated tools for smooth interaction.
The litespeed needles were specially designed by Groz-Beckert for use in (high-performance) circular knitting machines. The litespeed plus is a further development of the proven litespeed technology. It reduces energy consumption and the machine temperature even further – by up to 20 or 17 percent, for a noticeable reduction in costs.
The needle geometry makes the difference: In the dimensions relevant for loop formation, the litespeed plus needle corresponds exactly to a conventional needle for circular knitting machines. The difference lies in the optimised shaft geometry: Thanks to a partial reduction of the needle shaft thickness on both sides, the needle can be inserted irrespective of the machine direction. The weight and the friction of the needle in the needle trick is also reduced. Both have a positive impact on the flow characteristics of the needles in the cylinder.
Reduced energy consumption: The reduction of the contact surface through the reduced shaft thickness of the litespeed plus on both sides leads to a lower level of friction between the needle and cylinder. This means that less energy is required for the needle movement, which can help to reduce the energy consumption in the knitting process by up to 20 per cent. This not only reduces the energy consumption, but also helps to achieve a significant reduction in CO2 emissions.
Reduced machine temperature: In practice, extremely high temperatures can be achieved on cylinders and cam parts in modern (high-performance) circular knitting machines. This inevitably leads to problems during the needle and sinker change. In extreme cases, this can even limit the speed performance of the machines. The reduced needle shaft thickness of the litespeed plus reduces the friction between the needle and cylinder and improves the lubrication behavior, which can reduce the temperature at maximum machine speeds by up to 17 per cent.
Reduced oil consumption and optimised lubrication behaviour: The partially reduced needle shaft thickness enables better distribution of the needle oil in the needle trick. For the knitting machine, this means: lower machine temperature, reduced oil consumption and less oil nebulisation.
The advantages of the litespeed plus needle at a glance: energy saving; temperature reduction; more efficient lubrication behaviour: reduced CO2 emissions; reduced energy and oil consumption; no dependence on the running direction; reduced wear on the system components; use of the maximum machine speed; lower maintenance and ancillary costs.
Other product portfolio
At the ITMA Asia, a new acrylic exhibit of a sock machine rounded off the glass insights into the different knitting technologies. The exhibit demonstrated a wide range of Groz-Beckert products in different gauges – with needles and system parts for ten different models from the fields of socks and seamless hosiery.
Whether cleaning, drawing-in, tying or weaving:
As a system provider, Groz-Beckert offers a unique product variety with its Weaving division. Visitors could experience some of these products at ITMA Asia. The high-performance tying machine KnotMaster was presented in the field of weaving preparation. It is characterised by a wide variety of functions, ranging from single and double knots and short knot ends, through to four knotting types and thread breakage monitoring.
Heald frames and healds, as well as warp stop motions, drop wires and the PosiLeno leno system were available for customers to experience in action in the WeavingLoom, a replica weaving machine made from acrylic glass. Four fabric strips were presented, highlighting the different applications, from leno to jacquard fabric. Illustrative hand samples of the weaving accessories harness frames and healds completed the Weaving exhibition.
As a development partner, Groz-Beckert has expanded its range for application advice with is own staple fibre needle punch line in the field of Felting (nonwovens) in the Textile and Development Center (TDC) in Albstadt, Germany. The system is available to customers and partners for tests and joint projects. Many visitors experienced the staple fibre needle punch line live. The 3D-printed model in 1:18 scale impressed with its wealth of detail.
The division also presented its patented GEBECON Felting Needle, which offers improved surface quality and optimal bending resistance. The EcoStar Felting Needle is a real highlight for all applications with the highest demands for surface quality. It is characterised by its special working part cross-section, which has been reduced by 13 per cent compared with the standard needle. The geometry of the EcoStar thus creates a narrower contact angle of the fibres in the barb and thus achieves a higher fibre retention capacity.
For spun-lace customers, Groz-Beckert presented the innovative HyTec jet strip. The significantly higher hardness and the spring-hard properties have a positive impact on all mechanical properties. Customers benefit from the significantly improved handling properties, optimal service life and high scratch resistance to damage when changing jet strips.
As a system provider, Groz-Beckert also offers all tool components – consisting of tufting needles, loopers, reed fingers and tufting knives, in the field of Tufting – all from a single source. The Gauge Part System from Groz-Beckert impresses with its controlled and coordinated selection of materials and adherence to the narrowest tolerances. The precise dimension coordination between all individual tools used forms the basis for a smooth interplay between the various components within the system. The Groz-Beckert gauge part system thus fulfills all requirements of rug and artificial lawn manufacturers for functionality, reliability and durability, delivering a remarkable cost-saving result.
A perfectly coordinated interplay between the clothings in the field of carding achieves an optimal carding result both in the revolving flat card and in the roller card. The use of special clothing geometries in the nonwovens industry, like the worker and doffer wires SiroLock and EvoStep leads to better fibre control and a more even web. The SiroLock card clothing also impresses with increased performance of the roller card, while EvoStep card clothing focuses on saving raw material.
For the spinning industry, Groz-Beckert offers metallic card clothing, flat top and stationary flat clothing, as well as flexible strips. For processing synthetic fibres in particular, the company offers a special card clothing with a curved tooth profile: the synthetic doffer wire D40-30-52C CBF. This achieves a better fibre transfer from the cylinder to the doffer, thus creating an improved yarn quality and higher efficiency of the revolving flat card.
The Sewing product area showed how the different stitch formation types work in detail at ITMA Asia. The individual stitch types differ in the number and geometrical arrangement of the threads and are divided into six basic types (classes 100 to 600). Visitors experienced the stitch type 605 (cover chain stitch) at the trade fair. It consists of three needle threads, one looper thread and a covering thread and is used for sewing bindings and fancy seams onto items of clothing made from knitted fabric. The acrylic replica of a sewing machine and an impressive animation brought the interaction between the machine, needle and threads to life at the Groz-Beckert booth.
In order to establish optimal communication in the Chinese market, the Groz-Beckert WeChat Account went online in 2017. Since then, the needle manufacturer has been providing weekly news on the company, its products and services, as well as the latest topics relating to all aspects of the Chinese textile market. As usual on WeChat, the content is published in Chinese – the Groz-Beckert Account also includes links to content in English.
Groz-Beckert is the world’s leading provider of industrial machine needles, precision parts and fine tools as well as systems and services for the production and joining of textile fabrics. The products and services support the fields of knitting, weaving, felting, tufting, carding and sewing. The family-owned company, founded in 1852, employed more than 8,800 people and generated a turnover of around €740 million in 2017. Groz-Beckert operates with agencies, production and distribution subsidiaries in more than 150 countries around the world.