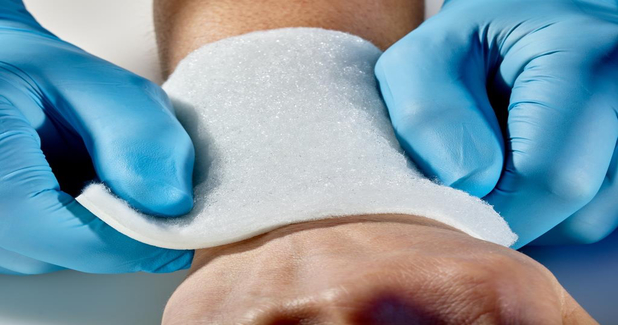
Freudenberg presents innovative direct coating with silicone adhesives
Freudenberg Performance Materials presented a number of innovative solutions at the European Wound Management Association Conference (EWMA) from June 5-7 in Gothenburg, Sweden.
Freudenberg Performance Materials presented a number of innovative solutions at the European Wound Management Association Conference (EWMA) from June 5-7 in Gothenburg, Sweden. These included foams with an innovative direct coating of silicone adhesives, multilayer foam-fleece components with superabsorbent nonwovens, and more efficient PU foams.
The components for wound dressings consist of polyurethane foam with a directly applied layer of silicone, which prevents the dressing from sticking to the wound. They continuously adapt to ensure optimal contact with the wound bed, reduce the complexity of the production process for the customer and have less impact on the environment. The adhesive properties of the silicone facilitate the application of the foam and, at the same time, do not stick to the wound when changing dressings. The Freudenberg solution works without additional layers of film or other liners with acrylic adhesive, which is required as a silicone carrier in conventional products.
The Freudenberg solution with a directly applied silicone layer has a number of concrete advantages:?
The wound dressings consist of an innovative PU foam and constantly adapt optimally to the wound bed; because they can expand evenly in all directions during the absorption of exudate, they provide greater flexibility.
Freudenberg supplies the foam and the silicone components for easy removal from wounds directly to customers as a single product. This brings two clear advantages: one production step is eliminated entirely and the customer’s procurement process is optimized because they no longer need to purchase individual components from different suppliers.
Because Freudenberg develops and produces the foams entirely in-house, top quality is guaranteed at all times. By integrating all process steps under one roof, the individual material properties can be optimally harmonised to achieve the highest possible performance. As a result of eliminating the need for film components, raw material use, energy consumption and waste are all reduced.
CATEGORIES Industry Update