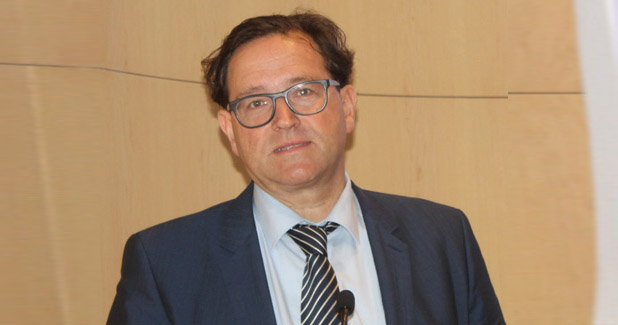
Focus on technical textiles & sustainability: S. Floth of Monforts
Germany-based Monforts, a part of China’s CHTC Fong’s Industries, claims to be ‘Leader in Innovation’ in the field of textile finishing machines. Says Stefan Floth, Managing Director of A. Monforts Textilmaschinen GmbH: “ITMA exhibition is like the Olympics for the textile machinery industry.
“The focus for Monforts Germany is on technical textiles and sustainability,†says Floth.
Added Floth: “The first product is stenter dryer, our flagship product. We are happy to present Montex stenter with the first fully integrated heat recovery and cleaning module. It will help our customers to further reduce their carbon footprint and protect the environment by overall additional reduced energy of 30 per cent as compared to what has been with the state-of-the-art machine before. We are looking from learning from the nature and adopting bionic principals in getting the stenter chamber more leak proof. We are delivering such kind of stenters for special products with drying temperature of up to 320 degree Celsius.â€
Perfect for the treatment of woven and knitted fabrics: The Montex stenter offers the latest technology for the optimum customer benefits. The sophisticated chamber design, the individually controlled air guidance system with maximum temperature precision and temperature distribution or the excellent energy management are just a few of the factors that make the Montex stenter indispensable for high-quality finishing. Furthermore, with stenters you are ideally equipped for the digital transformation of our times. Intuitive touchscreen operation or intelligent monitoring systems and app-based service dialogue tools are just a few of the examples of the ongoing innovations from Monforts.
Speaking further on the innovations for ITMA, Floth said: “The second innovation is in the field of dyeing, wherein we are already for decades. We already have more than 400 continuous dyeing ranges installed in the market. This is completely a new process which we are showing at ITMA.â€
He added: “We are dyeing warp yarn in a continuous way. We are doing that by adopting our Econtrol and Eco Bleach processes for open width dyeing. For this, we have acquired the special know-how over the last decades. This allows the customers to even produce short batches of warp dyed yarn in a very cost-efficient way. This reduces the machine investment cost to our customers as compared to our conventional special dyeing ranges. It reduces energy consumption and uses less chemicals.â€
Econtrol is a pad-dry process employed in Monforts continuous dyeing in which the reactive dyestuff is fixed to the cellulose fibres during drying and the CYD multi-colour yarn dyeing system introduces a number of new concepts based on it, including the unique Eco Bleach process.
“The third innovation is in the denim segment. We are presenting our eco lines for denim treatment, which feature gentle stretching of elastic denims in humid atmosphere, which is crucial to avoid broken lycra of spandex. It requires 30 per cent less energy. For this segment, I would like to refer to special publication of Monforts for aligning our denim competence,†said Floth.
The latest CYD denim processing technology integrates new functions and processes into the weaving preparatory processes – spinning, direct beaming, warping and assembly beaming, followed by sizing and dyeing – in order to increase quality, flexibility, economic viability and productivity.
On other innovations, Floth said, “the fourth innovation is in the technical textiles segment. We have expanded our floating competence. We started with our own texCoat coating unit four years ago. We are in the coating industry for much longer, but we have our own machine so that we can increase in-house in this very important field. We are offering new texCoat machine using carbon fibre reinforced components to allow higher precision in coating. We are using the latest HMI interfaces to enable the very efficient operation of the machine, which is partly remote controlled.â€
“The fifth category is also for the technical textiles sector. We are going into more wide machines dryers. We took some terminology from the garment industry,†he said.
“The sixth category is our package of smart technologies, which is our contribution to the IoT and Industry 4.0. Smart technologies is all about connected data, analysing the data and growing from the data to allow the customers to make better use of the machinery,†he said.
Speaking further on innovations, Floth concluded: “We are also presenting our new online workshop, which allows selling of spare parts. Then we have Monforts Smart Support app, which is also available on app store. Our customers can download this app for free and can enable a better communication with our service and sales.â€
At present with Smart Support, customers can also contact Monforts service via smartphone or tablet, in order to access support on site via a remote visual link. Monforts service specialists can point out individual system parts on the customer’s smartphone and assist them in troubleshooting. Documents such as machine documentation can also be shown in real-time via white-board over a smartphone, tablet or office PC.
CATEGORIES Trade Fair
TAGS Chinas CHTC Fongs IndustriesControlled Air Guidance SystemFloth of MonfortsIntelligent Monitoring SystemsITMAStefan FlöthStenter Dryertechnical textiles segment