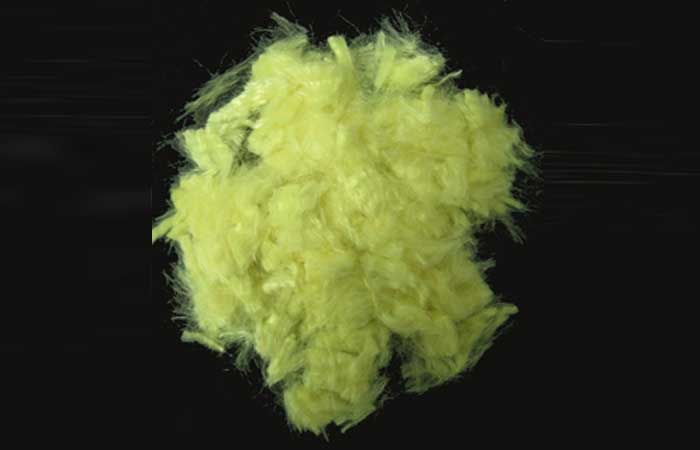
Exploring the potential of para-aramid fibres for multivaried applications
Aramid is used in fibrous form as well as in woven textile and pulp form, as reinforcement in demanding composite applications ranging from protective clothing to automotive and industrial applications.
Para-aramid, poly (p-phenylene terephthalamide), fibres are highly crystalline synthetic fibres with high tensile strength, excellent chemical and abrasion resistance and high melting point. They even outrank carbon fibre in impact and wear resistance while also having higher a strength-to-weight ratio. Aramid is used in fibrous form as well as in woven textile and pulp form, as reinforcement in demanding composite applications ranging from protective clothing (helmets, bulletproof vests, and fire protection) to automotive and industrial applications (gaskets, brake pads, tires, conveyor belts, and hoses).
However, the full use-potential of aramid fibre is hindered due to adhesion issues to matrix materials. To achieve the high strength-to-weight ratio, outstanding mechanical performance and durability characteristic of advanced composite materials, strong adhesion between the reinforcing fibres and the matrix material is critical. The adhesion issues with aramid fibres arise from the surface structure of the fibre, which is very smooth and chemically inert, lacking in reactive side groups. To overcome this phenomenon, surface treatments are used, which traditionally promote either physical or chemical adhesion with the matrix. For example, a plasma treatment increases the surface energy of the fibre by increasing hydrogen bonds at the fibre surface, thus enabling a physical bond to be formed between the fibre and matrix. On the other hand, with a chemical surface treatment, reactive side groups are grafted to the fibre surface, which can react with the matrix material and create a strong covalent bond between the fibre and the matrix. However, these methods are often suitable for only one type of matrix material, may lose their effectiveness rapidly during storage and may drastically reduce the mechanical properties of the fibres. Thus, new approaches are needed, and research is increasingly directed towards utilising mechanical adhesion between fibres and matrix.
Typically, mechanical adhesion is considered a lesser form of adhesion in composites, but it has some major advantages, such as independence of chemical compatibility. With mechanical adhesion or interlocking as the prominent adhesion mechanism, a wider range of material combinations could be used in composite applications, including thermoplastics. Thermoplastic materials are a desirable group of matrix materials for composite applications due to their lower toxicity and easier recyclability when compared to thermosetting materials. However, they are a challenging material group in terms of adhesion. Another benefit of mechanical adhesion at the fibre-matrix interface is that composite production becomes more economical as the same surface treatment can be used with multiple matrix types.
Mechanical adhesion or interlocking can be formed between the fibre and matrix, for example, by adding nanowires, nanoparticles, nanotubes, or nanofibres to the fibre surface. These structures simultaneously increase the surface area and the surface roughness of the fibre. For example, by increasing mechanical adhesion together with chemical interactions, Nasser et al. have been able to increase short beam strength of laser-induced graphene-coated aramid fabric by 70 per cent in epoxy matrix. Lv et al. have achieved similar results with in-situ polymer grafting and carbon nanotubes on aramid in the epoxy matrix, but they concluded the increase in interfacial shear strength (IFSS) to be due to increased polarity rather than topography. However, by purely increasing mechanical adhesion with adsorbed aramid nanofibers, Nasser et al. have been able to increase short beam strength by 26 per cent and IFSS by 70 per cent in epoxy, which shows what the imminent potential mechanical adhesion has in terms of composite applications.
However, to fully benefit from mechanical adhesion, the attached medium (i.e., nanofibers or particles) needs also to be strongly adhered to the fibre surface, as Gonzalez-Chi et al. and Ehlert et al. have demonstrated. Also, the unique skin-core structure of the highly crystalline para-aramid fibre may lower the overall adhesion properties of the fibre even if strong interphase is formed between the fibre and matrix. As force is applied to the interphase, the top layer of the fibre may fibrillate and be sheared off completely. By applying a “new skin” layer of graphene to the fibre, Cheng et al. have been able to reconfigure the phenomenon and change the failure mechanism from fibrillation of the fibre “skin” to clean fracture at the interface, while increasing the IFSS by 75 per cent in epoxy.
In this paper, the effect of mechanical adhesion has been studied as the main adhesion mechanism at the fibre-matrix interface. This is done by adding nanoscale deposits onto aramid fibre surface that increase surface area and topography and thus, enable mechanical adhesion at the fibre-matrix interphase. The concept of nanoscale deposit addition to increase adhesion in macroscale has been proven effective in our previous study. However, the question remained whether the increased adhesion was purely due to mechanical adhesion or a combined effect (i.e., secondary entanglement) and would the result really be effective with other matrix materials as well. In this paper, we aim to address these questions and show that the effect is universal and does work with multiple matrix material types, and that the adhesion increase is purely due to increased mechanical adhesion. Also, we show that the effect is similar across different length scales ranging from micro to macroscale. Both thermoplastic and thermoset matrices were used to evaluate reliably the behaviour of the nano deposit decorated fibre surface in different matrix types, which have significantly different chemical and physical properties. Micromechanical testing is applied so that the failure mode and mechanism of the interphase can be monitored more closely and the effect of secondary artefacts, which may be present in macroscopic bulk material testing, such as fibre entanglement, can be eliminated from the results. For this, a high throughput micro bond test system was used to measure the IFSS of these nano-deposit decorated fibres. This test method was chosen over the more traditional fibre fragmentation test because fibre fragmentation test is unsuitable for aramid fibres due to their high-strain tensile failure mode. Also, the micro bond test method can be applied more easily to both thermoplastic and thermoset matrix materials. In order to focus on the effect of mechanical adhesion, polypropylene (PP) was chosen as the thermoplastic matrix material. PP has very limited hydrogen bonding interactions with the fibre surface, thus making it ideal for this type of investigation. Epoxy (EP) was used as the thermoset matrix because of its availability and wide use in polymer composites across the field. Fourier transform infrared spectroscopy (FTIR), scanning electron microscopy (SEM), and atomic force microscopy (AFM) were used to characterise the nanostructures, study the fibre-matrix interphase and identify the failure mechanism. Further, it was also investigated how well the widely debated micro bond methodology represents macroscale properties of the composite by comparison to the previous results. Also, the influence of aging during storage is studied, and what effect it has on the effectiveness of the surface treatment.
Technical considerations
2.1. Aramid Surface Modification
2.2. Interfacial Shear Strength
2.3. Microscopy
2.4. FTIR Spectroscopy
The fibre surface after the microwave irradiation treatment revealed an abundance of nanostructures covering the surface. As seen in Figure 1, the nanostructures are of irregular shape and that the topography of the fibres has changed due to the surface treatment significantly, but no visible voids are generated on the fibre surface. This is in line with our previous findings stating that the treatment has no negative effect on the mechanical properties of the fibres and highlights the repeatability of the surface treatment method.
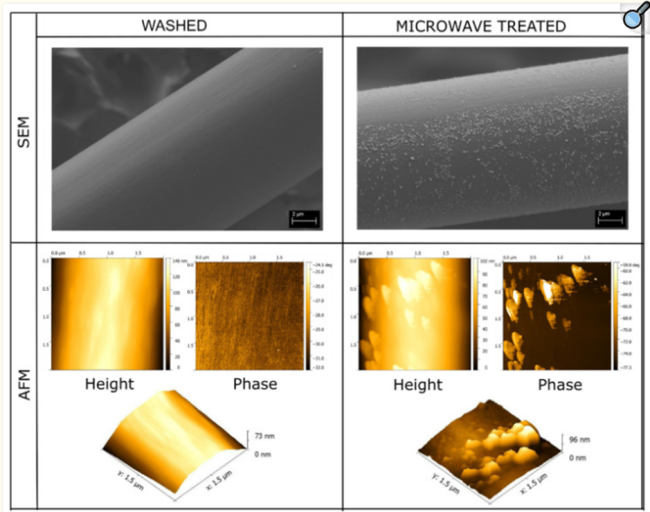
Figure 1: SEM images and corresponding AFM images of the aramid fibres before and after the microwave surface treatment
The AFM studies supported the SEM findings depicting clearly defined protrusions on the fibre surface. The phase contrast image highlights the structural and chemical difference between the bulk fibre and the nanostructures. As the colour gradient in AFM phase contrast image is a combination of topographical details as well as changes in mechanical and adhesive properties, a contrast in colour is created when the chemical and physical properties change in the imaged area. As the nanostructures appear brighter than the fibre surface, it can be deduced that they are not the same material as the fibre surface. Additionally, when using an Energy selective Backscattered (EsB) detector with SEM, the nanostructures also appear lighter than the bulk fibre itself, as seen in Figure 2. The EsB detector reduces edge contrast in the image and thus, the apparent colour difference between the bulk fibre and the nanostructures is due to increased Z-contrast between the two. This, together with the AFM findings, means that the nanostructures are of different material and added to the surface during the microwave surface treatment rather than coming from the bulk fibre itself due to wrinkling or surface degradation.
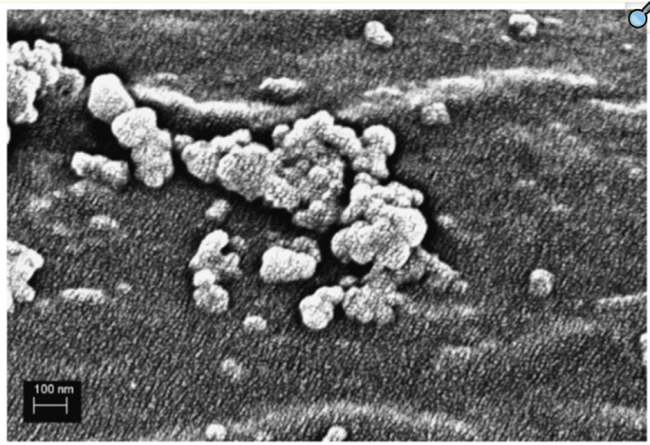
Figure 2: SEM EsB image of the microwave treated fibre surface highlighting the Z-contrast between the fibre surface and nanostructures.
The increased Z-contrast also implies that the nanostructures are mostly carbon-based compounds with traces of iron from ferrocene used in the microwave treatment. As a heavier element, iron would show up lighter in the EsB image. The iron molecule in ferrocene acts as a nucleation site for the carbon atoms as it is heated up during the treatment process and thus can accumulate into the nanostructures. As seen from the figures, the irregular shape and varying size of the nanostructures increases the surface area of the fibre efficiently. This increases frictional forces at the fibre-matrix interface as well as adhesion through mechanical interlocking.
The FTIR spectrum of the washed aramid fibres reveals characteristic peaks for para-aramid at 3312 cm−1 (–NH, hydrogen bond association states), 1637 cm−1 (C=O stretching vibration band of amide), 1537 cm−1 (N–H curved vibration), and 1305 cm−1 (N–H bending vibration). Compared to the FTIR spectrum of W-fibres, the hydrogen band peak of MW-fibres has broadened and moved to a lower wavenumber of 3305 cm−1 indicating increased hydrogen bonding at the surface and weakened hydrogen bonding in the polymer chains of the aramid fibre skin layer. This means that the intense heat during the surface treatment causes some damage to the fibre surface but not to a degree that would affect the tensile properties of the fibres, as shown previously, or be visible in SEM. Also, a new peak is present at 2870 cm−1, indicating CH2/CH groups at the fibre surface. The same peak is also present in ferrocene and graphite. This confirms that the nanostructures are decomposition products of ferrocene and graphite, formed during the microwave irradiation treatment.
IFSS was calculated with linear regression using the slope of load versus embedded area (Aemb) for each tested fibre separately. The IFSS for each sample type was then taken by calculating the average of the IFSS values of the separate fibres of that sample type. From the data obtained, it can be seen that the load required to debond a droplet is higher with samples that are covered with nanostructures than with those that are not, even though the effective embedded area is similar. This implies that protrusions as small as nanoscale, can significantly alter the properties of the fibre-matrix interface in a way that can be detected with a microscale method. This same trend can be seen with both EP and PP matrix. As the behaviour is similar in both thermoset and thermoplastic matrix, it emphasises the importance of mechanical adhesion as a major adhesion mechanism that is independent of chemical compatibility. By increasing mechanical adhesion with the nanostructures, the maximum load increased by 56 and 395 per cent in MW_EP and MW_PP, respectively. Although, the scattering of data appears to increase due to the surface treatment in MW_PP as compared to W_PP, this is not the case. Relative standard deviation (RSD) in both data sets is similar (~14 per cent), which means that the data is highly comparable. Also, the R2 value for all measured samples ranged between 0.82–0.98, meaning high compatibility with the linear fit and thus, highly reliable measurement results.
The average IFSS results are presented for W_EP, MW_EP, W_PP, and MW_PP together with macroscopic fibre bundle pull-out test results for the same surface treatment in rubber. It is evident that the IFSS increases alongside with the increased surface topography of the fibres. Moreover, the increase in IFSS follows a similar trend with the bundle pull-out test in rubber. The results show that the IFSS increases in a similar fashion with thermoplastic, thermoset, and elastomeric matrices, even though the potential for chemical interaction of these matrix types is very different. For example, with EP, an increase in interfacial adhesion can be achieved through covalent bonding with the fibre surface during curing or by creating higher frictional force with the cured and cross-linked resin. Mercaptan compounds, Lewis acid, and alkali products can be used to achieve such covalent bonds with EP. However, as none of them are grafted to the fibre surface in this case, what remains, is the increase in friction. This is also the case with PP. The chemical composition of PP provides only limited hydrogen interaction, which could affect favourably to interfacial adhesion with aramid. The main attribute towards the adhesion is mostly compressive forces due to favourable trans crystallisation occurring during the cooling process of the polymer melt. This was noted by Wang et al. They showed that small grooves and protrusions will increase thermal stress due to increased stress concentration during the PP crystallisation when the melt is cooling. This localised stress concentration will further on enhance the nucleation ability of PP and, thus, promote trans crystallisation leading to enhanced interfacial adhesion. The nanostructures created to the aramid fibre surface in this study, will act as such protrusions as described by Wang et al., and thus, lead to increased mechanical adhesion between the fibre surface and PP. In both EP and PP matrix, the nanostructures also increase stress transferability, which in turn, increases the IFSS in a similar fashion in both matrix types. These findings indicate that the primary adhesion mechanism between the fibre and polymer in this case, is indeed mechanical adhesion.
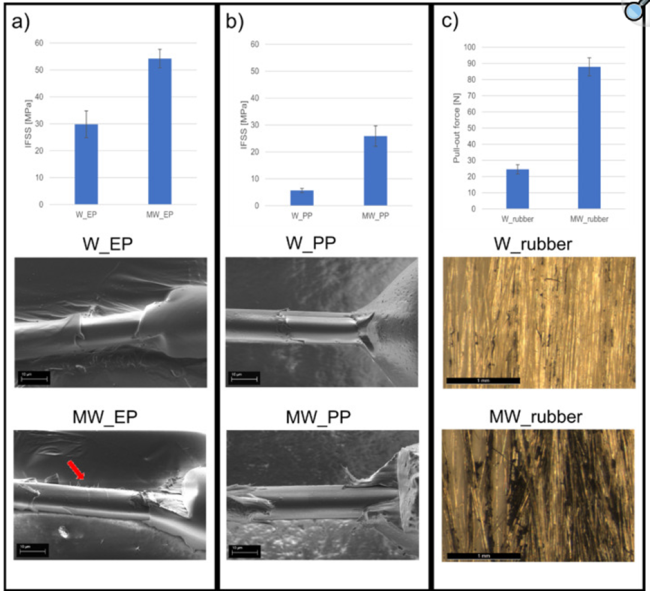
Figure 3: The IFSS results and SEM images of the corresponding fracture surfaces for (a) W_EP and MW_EP, where the arrow indicates fibrillation of the fibre surface, and (b) W_PP and MW_PP. The fibre bundle pull-out force and corresponding optical images are presented in (c) for W_rubber and MW_rubber.
The measured IFSS value for W_PP is 5.7 MPa, which is similar to other studies done with micro droplet test and aramid/PP combination. This shows that the high-throughput microbond method is highly suitable for IFSS evaluation also with thermoplastic matrix. Overall, the IFSS increased from 29.8 to 54.2 MPa (82 per cent increase) and from 5.7 to 25.9 MPa (358 per cent increase), in EP and PP matrix, respectively, due to the surface treatment. This is very significant as it shows that the surface treatment is suitable for both thermoplastic and thermoset materials and that it has a similar effect in them both. Also, it is worthwhile noting that with this straightforward and fast surface treatment process, the IFSS of aramid/EP combination could be brought to the same level as with other more complicated methods reported only recently.
SEM images of the failed fibre-matrix interphase and visual observation during micro bond testing supported the IFSS results. The failure mechanism during testing changed from pure shear at the interphase to a combination of peeling and shear as the surface topography was introduced. With no surface treatment, the fibre surface after de bonding appears smooth and unscathed, with only a minor amount of matrix residue remaining, as seen in Figure 4. This indicates that the fibre-matrix interphase has failed as the matrix droplet is sheared off. Also, the detachment site of the droplet shows a clean break with a small gap between the fibre surface and matrix, indicating a weak interphase. With the surface-treated fibres, the detachment site of the droplet shows no gap and is more uneven, meaning that a stronger fibre-matrix interphase has been created. The debonded surface is rougher even with some fibrillation of the fibre skin structure, which indicates that the failure has shifted from purely occurring at the fibre-matrix interphase to a combination of fibre surface fibrillation and peeling together with interfacial shearing. The change in the appearance of the debonded surface is very clear with the harder EP matrix, as seen in Figure 4a, where red arrows point to sections of fibrillated fibre surface. Whereas with the softer PP, the matrix is rather fibrillating itself and clinging to the nanostructures than cleaving bits off from the fibre surface. The PP strands clinging to the fibre can be seen clearly underneath the fibre. This indicates that the fibre/matrix adhesion is higher than the cohesive strength of the matrix. It also means, that the nanostructures are strongly attached to the fibre surface, as delamination occurs jointly from the skin-core interphase and skin-matrix interphase. As a result, it can be said that the main adhesion mechanism contributing towards the increased interfacial adhesion is mechanical adhesion.
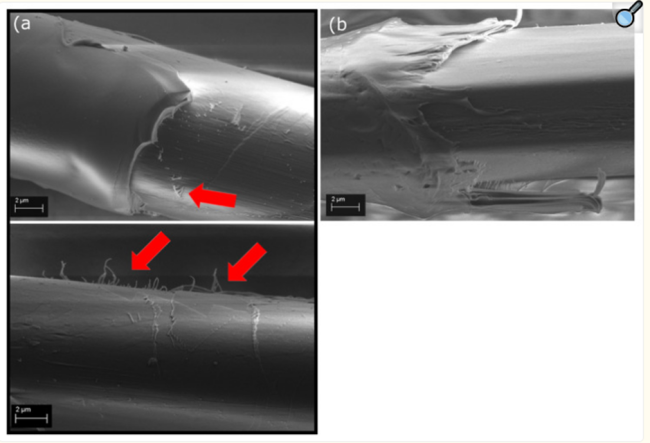
Figure 4: SEM images of the facture surfaces of (a) MW_EP, where red arrows indicate the fibrillation and peeling of the fibre surface, and (b) MW_PP after IFSS testing.
macroscopic fibre bundle pull-out test in rubber. By increasing the amount of nanodeposits on the fibre surface, the adhesion and the strength of the interphase can be increased in both micro and macroscale. This is in line with findings of previous studies, such as the ones made by Beter et al. It also suggests that the high-throughput microbond method produces reliable data, which can indeed be used to evaluate adhesion properties in macroscopic composite structures. This type of composite research and development process can be made more economical and efficient.
Storage properties, and more precisely, aging, of the nanostructure covered fibre surface was also investigated. Some of the surface-treated fibres were taken aside and kept for 48 months at room temperature and protected from light. The IFSS of these fibres was measured with the micro bond procedure in EP, and visual changes in the fibre surface were studied with SEM. The results revealed only minimal decrease in IFSS (~2 per cent), which is well within the deviation range, compared to newly surface-treated fibres. Also, no change in the appearance of the fibre surface was observed. Thus, no significant decrease in the interfacial properties of the fibres has occurred, and the surface treatment can be considered durable enough to withstand storage over long periods of time.
Conclusions
This work explored the effect of nanostructures on the interfacial adhesion of aramid fibre in both a thermoplastic and a thermoset matrix and related the results also to an elastomeric matrix from a previous study. Our findings demonstrated that a significant increase in IFSS can be achieved in both thermoplastic (+358 per cent) and thermoset (+82 per cent) matrix, while maintaining mechanical and storage properties of the fibres. The increase in IFSS was noted to be due to enhanced mechanical adhesion between the fibre surface and matrix material caused by the addition of nanostructures to the fibre surface. The positive effect of the nanostructures on interfacial strength was observed both in micro and macroscale tests. The failure mechanism of the fibre-matrix interphase changes from clean shear to combined shear and peeling, as the level of mechanical adhesion increases, proving that the nanostructures are strongly attached to the fibre surface. These results highlight the significance of mechanical adhesion as the main adhesion mechanism and expand the use-potential of aramid fibres to multiple matrix material types and applications with just one fibre surface treatment.
References
- Karger-Kocsis J., Mahmood H., Pegoretti A. Recent advances in fiber/matrix interphase engineering for polymer composites. Prog. Mater. Sci. 2015;73:1–43.
- Jesson D.A., Watts J.F. The Interface and Interphase in Polymer Matrix Composites: Effect on Mechanical Properties and Methods for Identification. Polym. Rev. 2012;52:321–354.
- Tam T., Bhatnagar A. High-performance ballistic fibers and tapes. In: Bhatnagar A., editor. Lightweight Ballistic Composites. 2nd ed. Woodhead Publishing; Duxford, UK: 2016. pp. 1–39.
- Chang K.K., Fibers A. In: ASM Handbooks. Miracle D.B., Donaldson S.L., editors. Vol. 21. Composites, ASM International; Materials Park, OH, USA: 2001. pp. 41–45.
- Qi G., Zhang B., Du S., Yu Y. Estimation of aramid fiber/epoxy interfacial properties by fiber bundle tests and multiscale modeling considering the fiber skin/core structure. Compos. Struct. 2017;167:1–10. doi: 10.1016/j.compstruct.2017.01.047.
- Luo S., Ooij W.J.V. Surface modification of textile fibers for improvement of adhesion to polymeric matrices: A review. J. Adhes. Sci. Technol. 2002;16:1715–1735.
- Sun J., Yao L., Sun S., Qiu Y. ESR study of atmospheric pressure plasma jet irradiated aramid fibers. Surf. Coat. Technol. 2011;205:5312–5317.
- Wang J., Chen P., Xiong X., Jia C., Yu Q., Ma K. Interface characteristic of aramid fiber reinforced poly(phthalazinone ether sulfone ketone) composite. Surf. Interface Anal. 2017;49:788–793. doi: 10.1002/sia.6224.
- Tie-Min L., Yuan-Suo Z., Jie H. Surface modification of Aramid fibers with new chemical method for improving interfacial bonding strength with epoxy resin. J. Appl. Polym. Sci. 2010;118:2541–2552.
- Gao B., Zhang R., Gao F., He M., Wang C., Liu L., Zhao L., Cui H. Interfacial Microstructure and Enhanced Mechanical Properties of Carbon Fiber Composites Caused by Growing Generation 1–4 Dendritic Poly(amidoamine) on a Fiber Surface. Langmuir. 2016;32:8339–8349. doi: 10.1021/acs.langmuir.6b01485.
About the authors:
- S Karthikeyan is from the Department of Petrochemical Engineering, SSM College of Engineering, Komarapalayam, Tamil Nadu.
- Dr U Ratna is from the Department of Textiles and Clothing, Avinashilingam Institute of Home Science and Higher Education for Women, Coimbatore, Tamil Nadu.
- J Lavanya is from the Department of Fashion Design, SRM Institute of Science and Technology, Chennai, Tamil Nadu.
- V Sathya is from the Department of Fashion Design, SRM Institute of Science and Technology, Chennai, Tamil Nadu.
- Dr N Gokarneshan is from the Department of Textile Chemistry, SSM College of Engineering, Komarapalayam, Tamil Nadu.