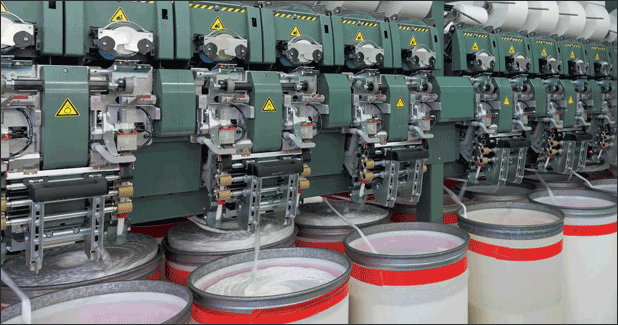
Estimating yarn cost in spinning mills
Wrong estimation of cost is one of the major reasons for the wide difference in yarn cost, says S Mariappan.
Wrong estimation of cost is one of the major reasons for the wide difference in yarn cost, says S Mariappan.
Profit margin in spinning mills is low at about 4 per cent and moreover mills are facing a lot of competition in local/export markets. It was observed that many mills are not using correct method of yarn costing and results in under/over estimation of cost of production of yarn. Thus wrong estimation of yarn cost affects selection of correct product mix of a mill and hence lower profit per month. Some mills follow thumb rule to estimate the conversion cost of yarn and resulting an incorrect estimation of yarn cost. However few mills are estimating department wise costing to estimate yarn cost which involves detailed procedures and calculations. Though it is correct and accurate, the procedures are very cumbersome and take more time for estimation of yarn cost. Hence a quick method is suggested to find out the yarn cost which takes lesser time and at the same time accurate in estimation of yarn cost.
Estimation of yarn cost
First raw material cost or clean cotton cost is calculated. Then conversion cost is estimated and added with raw material cost to give cost of production of yarn or yarn cost.
Yarn cost = raw material cost + conversion cost
All the expenses incurred to manufacture yarns excluding raw material cost is conversion cost. It is nothing but a sum of wages and salaries, power, stores, administrative overheads, interest and depreciation cost.
Raw material cost
Mixing cost per kilogram is the weighted average prices of cotton, if more than one cotton is used. Raw material cost per kilogram of yarn is estimated by using the following formula.
Raw material cost/kg of yarn = (C-W)*100/year Where,
• C – Mixing cost/kg of mixing (Rs) • W – Waste sales realisation per per kilogram of mixing (Rs) • YR – Yarn realisation (%)
Waste sales realisation could be calculated from the price fetched for each category of waste per kilogram and the quantity of waste produced. For different categories of waste, the price realisable would not be significantly different between cottons and hence this difference could be ignored.
Estimation of wages cost
Wages and salaries cost are estimated separately and they are added. Wages cost per 1,000 spindles for a count has been estimated by multiplying number of operatives engaged per 1,000 spindles in that count and average wages cost/operative/shift. The mill has to prepare a spin plan for the number of ring frame spindles allotted for each count.
Number of operatives engaged in each section was calculated based on machine shifts required in each count as given in spin plan and work assignment followed by mills. The common operatives in the departments like material handler, sweeper, etc., are apportioned for various counts based on machine shifts required for each count. Maintenance and non production operatives are apportioned based on spindles allotted for each count. The total number of operatives engaged in each count is estimated by adding operatives engaged in all the sections viz, up to spinning, post spinning, packing, maintenance and non production operatives. From total wage bill and number of man days engaged for the month, average wages/operative/shift for the mill should be estimated. The wages should normally include besides wages, fringe benefits, like P F, ESI, bonus provision, etc. and welfare expenses like canteen subsidy and other benefits to operatives etc., operatives per 1,000 spindle shifts are derived for each count from total number of operatives and spindle shifts allotted. By multiplying the total number of operatives and average wage rate, wages cost per 1,000 spindles is estimated.
Estimation of operatives per 1,000 spindles for each count is an one time exercise for the mill and can be used regularly for calculation. A revision or reworking of the same is required only when there is change in work assignment or drastic change in the machinery or production rate in spinning.
Estimation of salaries cost
The salaries of staff could be estimated by multiplying the number of staff engaged and average salary per month. The number of staff engaged for each count could be estimated by apportioning total number of staffs based on spindle shifts allotted for each count. Average salary could be estimated by dividing total salaries per month by total number of staffs engaged. The salaries should include all fringe benefits such as PF, ESI, leave and holiday wages and all other fringe benefits. Salaries cost per 1,000 spindle shifts could thus be calculated for each count.
Wages and salaries cost
Adding wages and salaries cost, the cost per 1,000 spindles could be estimated. By applying actual average production rate in various counts, wages and salaries cost per kilogram of yarn is estimated.
Power cost
Power cost per kilogram is worked out by multiplying units required per kilogram of yarn (UKG) and average cost per unit. The power cost per unit is estimated based on weighted average of usage of EB, generator, private and wind/solar power. It is ideal to measure the power consumption in each section by using Energy meter for a minimum of three shifts and calculate power consumption per machine shift in each section which can be used in the calculation. The power consumption in common departments like humidification, compressor, lighting, etc., is apportioned to each count based on the spindle shifts allotted. The total units required per 1,000 spindle shifts for each count is worked out and hence count-wise UKG for the mill is estimated.
As like ‘operatives per 1,000 spindles’ in the estimation of wages cost, count-wise UKG is also an one-time assessment and would need revision only when production rate increases substantially or large scale modernisation has taken place. Expected power consumption for the past four months is estimated based on count-wise production achieved and estimated UKG for various counts. It is compared with actual power consumption. The extent of higher or lower consumption is calculated as a correction factor and it is applied to the estimated count wise UKG. Hence thus corrected count wise UKG is estimated.
If energy meter is not available in the mills, the power consumption per machine shift is estimated based on installed motor HP and expected load factor. While estimating ring frame power consumption, account must be taken for the counts run. However in preparatory departments, the difference in power consumption per machine shift is not significant for the counts run and hence it could be taken same for various counts.
The percentage of loading would vary from 60 to 70 per cent in various departments. The power consumption in common departments like humidification, compressor, lighting, etc., is calculated based on the number of hours run and loading. The above power consumption is apportioned to each count based on the count-wise spindle shifts allotted. Thus, count-wise total power consumption per 1,000 spindle shifts and hence count wise UKG is calculated. The expected power consumption is calculated for four months by taking actual count-wise production achieved for the corresponding period and estimated UKG. The expected cumulative total of power consumption for four months is compared with the actual power consumption for the corresponding period. The extent of higher or lower consumption is calculated as a correction factor. The correction factor is applied to the estimated count wise UKG and thus corrected count wise UKG is estimated.
Stores
Stores cost consists of consumable stores and packing material cost. The consumable stores cost includes consumption of items like routine replacement items in various departments, lubricants like oil and grease, machinery spares, electrical spares, generator spares, etc. The consumption of long-life items (more than five years life) like top arms, flyers, spindles, etc., are considered in repair expenses in administrative overhead. Consumable stores cost per 1,000 spindle shifts is calculated based on monthly stores consumption in INR and total spindle shifts allotted for the corresponding month. By taking actual count-wise production rates achieved, consumable cost per kilogram of yarn is obtained.
Standard packing material cost per kilogram of yarn is obtained by cost of items used (packing material) in unit packing and dividing by the package weight. For each count, standard packing material cost per kilogram can be estimated.
Administration cost
Administration cost compromises expenses towards viz. selling expenses, repair expenses and other expenses.
• Selling expenses: This expense comprises of freight, insurance and other selling expenses. The selling expenses will vary depending on market where the yarn is sold for example local/export, local market/upcountry, etc., (only the commission and brokerage expenses incurred can be apportioned to different counts on the basis of actual expense per kilogram and this is subtracted from yarn sale rate per kilogram to get net sale price per kilogram of yarn).
• Repair expenses: This consists of repair expenses incurred for building and machinery (including electrical). Routine replacement items having more than five years life like top arms, spindles, etc. and high-value spare parts required for machinery/generator repair, etc. are included in this category.
• Other expenses: This includes all other office expenses like postage, telegram, conveyance and travelling expenses, Insurance, audit fees, rates and taxes, etc.
All the above expenses are added to get administrative cost and it is apportioned based on the count-wise spindle shifts allotted. Based on the administrative expenses per month and corresponding spindle shifts allotted, cost per 1,000 spindle shifts and cost per kilogram is calculated.
Interest
Interest charges consist of interest for term loan and others and for working capital. The interest cost for term loan (bank loans) and others (fixed deposit, other loans, etc.) is apportioned count wise based on spindle shifts allotted in each count whereas working capital interest is apportioned on the basis of sales turnover. The count wise total interest charges are calculated per 1,000 spindle shifts and thus count wise cost per kilogram is estimated.
Depreciation
Depreciation is the cost allocated for loss of value for wear and tear of the asset due to use over a period of time. Depreciation cost can be allocated to different counts based on spindles allotted. Thus the cost per 1,000 spindle shifts and also per kilogram can be worked out for each count.
Assessment of overall cost and profitability
The mill should compare the actual monthly cost of each head viz., wages, power, stores, administration, etc., with monthly average calculated from last financial year. The deviation, if any, has to be analysed for the reason. After assessing count wise cost of production, the cost sheet has to be prepared to find out the profit margin in each count. Since the production rate varies depending on the count, the profit per kilogram cannot be the basis for deciding the profitable counts. Profitability has to be worked based on 1,000 spindle shifts to help the management to decide the relative profitability in different counts.
The cost sheet is useful for identifying profitable counts. The profit per month could be worked out by multiplying profit per kilogram and yarn production achieved in that count. The profitability so obtained (called costing profit ) has to be compared with the profitability given by Finance department. A suggested Model Cost Sheet Format is given in Table 1.
It is suggested to prepare cost sheet every month and tally profit per month calculated from costing and finance departments.
Wrong methods followed by mills
It was observed that many mills don’t estimate yarn cost correctly. This is one of the reasons for high variation in yarn prices between mills. Many mills have been following incorrect costing methods to estimate conversion cost of yarn and they are given below.
• Method 1: The expense (all expenses other than raw material) for a month is divided by total worked spindle shifts during corresponding period to get average cost per spindle per shift. By using actual average production/spindle/shift for the month, conversion cost per kilogram of yarn in that particular count is calculated. Similarly conversion cost per kilogram in other counts is estimated.
• Method 2: The expense (all expenses other than raw material) for a month is divided by total quantities of yarn produced during that month and average count, to get average cost per kilogram per count. The derived cost per kilogram is multiplied by counts to arrive the conversion cost per kilogram of yarn in that particular count.
• Method 3: Conversion cost is assumed as Rs 1.60 to Rs 2.00 per count per kilogram of yarn for carded yarn and Rs 1.90 to Rs 2.30 per count per kilogram of yarn for combed yarns by the mills depending upon the various factors. The cost varies from mills to mills since it is decided by the management. All the above methods of costing are incorrect and result in wrong estimation of conversion cost.
The mills have to engage operatives depending upon count for example more number of operatives are required per 1,000 spindles for coarser counts compared to finer counts. Similarly power consumption per 1,000 spindles will differ depending upon count and will not be equal in all the counts. Moreover working capital interest would be higher for coarser counts compared to finer counts. Packing material and selling expenses would vary depending upon type of market/packing, etc. However, all the above costs have assumed same for all counts in Method 1 which gives wrong estimation of cost.
In Method 2, production rate in coarser count is higher compared to finer counts. Hence production in kilogram should not be taken for basis of apportioning the cost in Method 2. Since the conversion costs significantly vary with counts. conversion cost is over/under estimated following this method.
The conversion cost would vary from mill to mill depending upon various input costs viz, wages, power, administration expenses, interest, etc. Moreover conversion cost per count per kilogram would vary with the counts even within a mill. Hence it is very vague to estimate the conversion cost based on the rates prevailing in other mills (method 3).
The estimated conversion cost differs widely between above methods and leads to wrong selection of product mix. This affects the profit per month.
Wrong estimation of cost is one of the major reasons for the wide difference in yarn cost. The mill predicts a profit for producing a particular count due to under estimation of conversion cost but actually it is not so. Hence it results in wrong selection of product mix and profit per month is lower. For maximising profit, correct estimation of conversion cost is essential. It is suggested to adopt correct method of costing as suggested in this paper.
The author, S Mariappan, M.Tech,(Textiles), has worked for a few years in spinning mills and has got about 33 years experience in Liaison and Consultancy department in The South India Textile Research Association (SITRA), Coimbatore. He had visited more than 400 mills for consultancy assignments in both India and foreign countries. He has retired from SITRA recently as a Research Associate and is currently a freelance textile consultant.