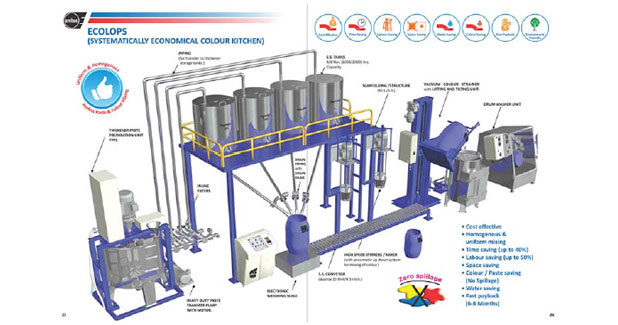
Embee’s systematic colour kitchen
The use of conveyor systems in colour kitchens not only improves efficiency, but also contains the movement of these colour tubs within the designated area. It is generally accepted that colour kitchens associated to the fabrics and yarns dyeing sectors
The use of conveyor systems in colour kitchens not only improves efficiency, but also contains the movement of these colour tubs within the designated area.
It is generally accepted that colour kitchens associated to the fabrics and yarns dyeing sectors have always tended to be better organised than their counterparts in the textile printing companies. In the last decade, the textile printing sector finally awoke to the fact that improving their colour preparation facilities does actually make them more-cost efficient.
However, with regret, on many occasions their attempt to achieve the intended efficiency in the colour kitchens, has tended to confuse their particular needs with the available technology and not taking their employees ability-factor into consideration. Calculating the average costing for the dyestuff used in an average-sized printing company, Embee emphasises average costing due to many variables associated to these costings, i.e. type of fabric, width of fabric, coverage, depth of shade, etc.
The average costing´s calculations are therefore based on the company – printing 30,000 m of 70-inch wide fabric per day.
A basic organised colour kitchen would easily reduce the above costs by 10 per cent ($1,15,200 per year), if only the colourist could spend his time ´preparing the colours´ instead of supervising his labour force doing menial tasks, which could be done better by a machine that does not abscond, err or complain. A colourist´s primary responsibilities must always remain in the preparation of the correct recipes/colour shades, and to avoid clients rejecting the printed fabric (which costs we dare not mention, together with other costs incurred by related loss of reputation).
The textile printing sector must note that developments in colour kitchens are specialised, and are generally divided into two main specific sectors:
1)Colour management instrumentation & software manufacturers
Producing: Storage & pumping system, mixers, filters, various related washing equipment, conveyors, etc.
2)Colour management instrumentation & software manufacturers
Producing: Spectrophotometer and other computer-related colour matching instruments / systems, automatic dispensing systems, etc.
Finally the decision on the equipment necessary, to increase the efficiency in colour kitchen must always be based on the technical ability of the management, the colourist and his labour force. It is important to realise that often, a colour kitchen fitted out like a space ship, without the necessary technically trained labour may actually create more inefficiencies. A colour kitchen basic requirements and the work-flow to improve efficiencies must be first assessed and possibly improved upon, before considering the automation point of view.
Basic requirements in organising a colour kitchen
Thickener/emulsion paste preparation system: Generally based on average production requirement, i.e., 1 kg thickener/emulsion paste per 8 m x 2 m. Wide fabric average time required for preparation of thickener paste, varies slightly from company to company, dependent on the organisation, and the preparation system being used. Following assessment of the average production requirements, the required paste preparation equipment can then be considered.
Storage and dispensing system for thickener/emulsion paste: Storage of the thickener/emulsion paste for more than 48 hours is generally not advisable. Average storage requirements must be considered in assessing the number of storage tanks required, together with the related speed/ production time for paste preparation. The storage tank system, is then required to dispense the paste (via pipe sys