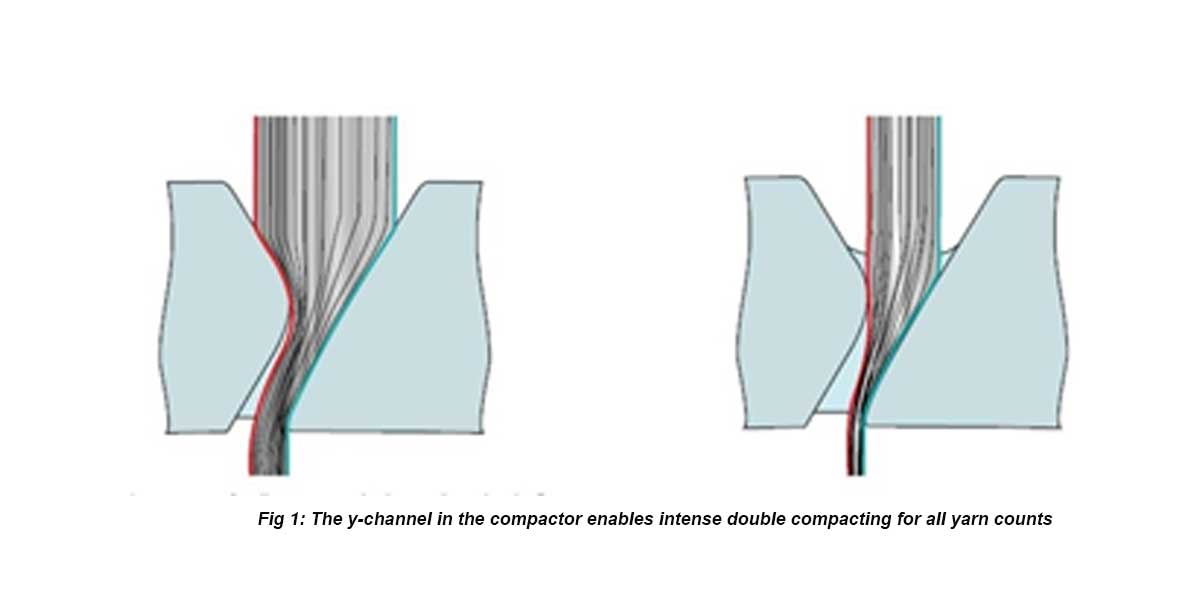
Economical Compact-Spinning Using State-of-the-Art Technology
The COMPACTeasy mechanical compacting system from Suessen addresses the need for higher productivity and cost optimization in compact spinning. The system can spin high-quality yarn from all common raw materials – at a high speed. Low investment cost, less energy consumption and minimal maintenance make COMPACTeasy an attractive alternative to pneumatic systems for spinning mills.
Saving energy and cost are decisive factors for spinning mills today. Most spinning systems require both a high level of initial investment as well as considerable operating cost. While compact spinning is appreciated for its excellent yarn quality and high productivity, it can also be very cost-intensive, especially with pneumatic compacting systems requiring a lot of electricity.
Unmatched compact-spinning quality
Continually striving to push boundaries of innovation, Suessen developed COMPACTeasy, a mechanical compacting solution that offers low investment cost without compromising on quality. It produces yarns with excellent characteristics from a broad range of raw materials, such as cotton and man-made fibres, as well as their blends. With a count range from Ne 20 to Ne 60, COMPACTeasy covers most applications.
The recipe for success
COMPACTeasy guides fibres through the y-channel of the compactor with precision, which results in intensive double compacting (Fig 1) without any additional energy requirements compared to ring spinning.
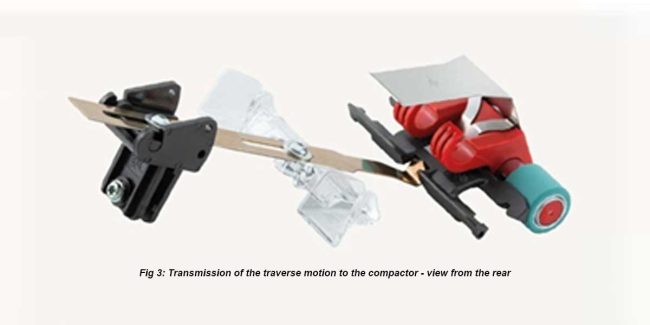
Compared to other mechanical systems, the compacting channel of COMPACTeasy is much wider, so it is less prone to clogging. Thanks to the traverse motion of the compactor (Fig 3), the lifetime of cots is extended resulting in lower maintenance requirements and constant and durable yarn quality. This is a considerable advantage compared to flipping the front top roller, which is what mechanical systems usually require.
Sophisticated technology for less wear and tear
The device consists of a front top-roller retainer and the smaller COMPACTeasy roller (Fig 2). The compactor features the y-channel and the preceding pin and is located between the two top rollers. The compactor spring uses a low spring force to press the compactor against the bottom roller. This causes considerably less wear and tear on the compactor than magnetically loaded compacting elements.
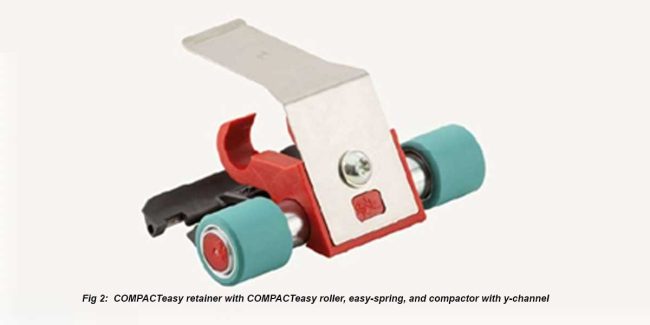
The yarn quality is determined by both the y-channel of the compactor and the integrated pin, which takes effect precisely in the zone of the drafting system where the fibers have the least guidance. This process improves yarn irregularity and increases yarn tenacity. Hairiness is also significantly reduced and often achieves better results than pneumatic compacting systems.
Flexibility and compatibility
COMPACTeasy can be added to the specifications for new ring spinning machines (Fig 4). Furthermore, machines that have already been installed can easily be retrofitted. COMPACTeasy enables production to be switched from ring to compact yarn by simply installing or removing the compacting device on a ring spinning machine.
Suessen customers are not just impressed by COMPACTeasy’s low investment and operating cost, they also appreciate the very high yarn tenacity and consistency, as well as the ability to produce a wide range of fibers and counts.
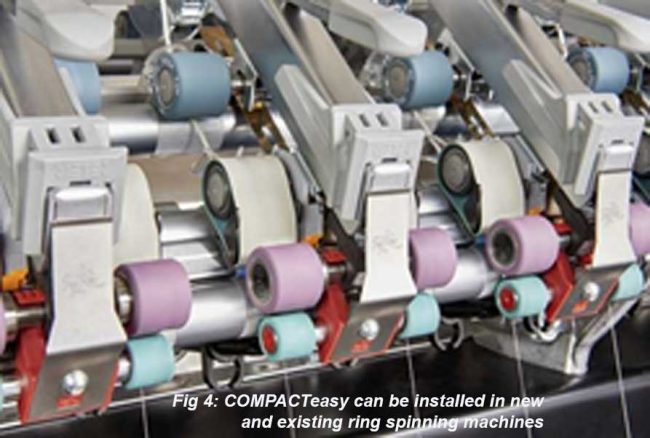
Rieter is the world’s leading supplier of systems for short-staple fiber spinning. Based in Winterthur (Switzerland), the company develops and manufactures machinery, systems and components used to convert natural and man-made fibers and their blends into yarns. Rieter is the only supplier worldwide to cover both spinning preparation processes and all four end-spinning processes currently established on the market. Furthermore, Rieter is a leader in the field of precision winding machines. With 17 manufacturing locations in ten countries, the company employs a global workforce of some 4 900, about 18% of whom are based in Switzerland.
Suessen, the world’s leading manufacturer of spinning systems and components for spinning machines, is a subsidiary of the Rieter Group. The company, based in Suessen (Germany), creates customer value through system expertise, innovative solutions, after-sales excellence and global presence. Considerable investments in R&D ensure further development of technical and technological components in an uncompromising and resolute manner. The company focuses on universal applicability, improved yarn quality, increased service life, reduced maintenance and proven reliability in industrial applications.