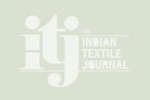
DI-LOOM: Flat needle felts for multiple applications
As the leading specialist DILO offers a complete production range for all needle looms with all working widths, stroke frequencies, needle densities and needling technologies.
As the leading specialist DILO offers a complete production range for all needle looms with all working widths, stroke frequencies, needle densities and needling technologies.
Within the different model series the standard universal needle looms DI-LOOM (DILO needle loom) are the most important ones. These machines are used for manufacturing flat needle felts for various applications such as floor and wall coverings, geotextiles, artificial leather, roofing material, filter media. Felts from all types of fibres can be needled: polypropylene, polyester, polyamide, aramid (eg, Nomex, Kevlar), polyacrylonitrile, cellulose, regenerated fibres, Teflon, carbon fibres, glass and other mineral fibres, metal fibres, wool and cotton, coir fibres, sisal, jute and flax.
The model series DI-LOOM comprises various different types, which meet all technological requirements. All kinds of needling, needling from top, from bottom or from both sides, with one or with two or with four needle boards. The machines are universal because they can be used as pre- as well as finish needlers. The typical pre-needler needles with one board from top in combination with the different batt feeding systems CBF, CBFT, ZBS. Machines with more boards can also be equipped with these feeding systems in such a way that the first needling zone serves as a pre-consolidator and the following one serves for further consolidation.
Thus, there are indeed cases, where double needle looms type OUG with four needle boards are used for pre- and finish consolidation directly after the cross-lapper. To produce felts with minimum draft, a DI-LOOM machine used as a pre-needler has optimised cross-sectional forms of stripper and stitching plates. The stripper plate has outlets in the direction of the material flow through which the fibre fly is able to pass easily to improve de-dusting by making use of the air flow caused by the needle beam. Upon request the needle looms of the DI-LOOM model series may be equipped with a de-dusting device DI-DUST to prolong the cleaning intervals.
As a special accessory the quick release clamping system is available for stripper and stitching plates, to improve accessibility for cleaning of the drillings. For machines with two or more boards the penetration depth and stripper plate gaps may be adjusted individually. The final position is controlled electrically to avoid damage by displacement. Standard working widths range from 1.5 to 8 metres, rising in 0.5 metre increments.
During continuous operation the maximum stroke frequency of the machines of the model series DI-LOOM and DI-LOOM B is 1,200 strokes per minute. Higher stroke frequencies are possible with the DI-LOOM S and SC model series. The machines of the DI-LOOM model series are regarded as the "workhorse" of the needle felting industry and have a machine frame which is highly distortion-free and resistant to bending, ie, "vibration resistant". Feeding system and pair of draw-off rollers are assemblies standing separately, which are fixed to the ground independently from the machine frame.
They carry the safety guards which are closed mechanically and controlled electrically. The safety guards also serve to reduce the sound emission. The pressure rollers on the pair of feeding rollers and the pair of draw-off rollers are controlled pneumatically and can be adjusted precisely to the thickness of the material.
The needle loom itself is mounted on spring elements and vibration is not transmitted to the floor. The machine does not require any foundation and can be put onto the industrial floor. The needle beam is made of a high-strength, bending and torsion resistant aluminium profile. To avoid steps with differences in the penetration depth between parts of the needle board, which would result in tracking marks in the material, the needle beam consists of one piece up to a working width of 8 m.
The pne