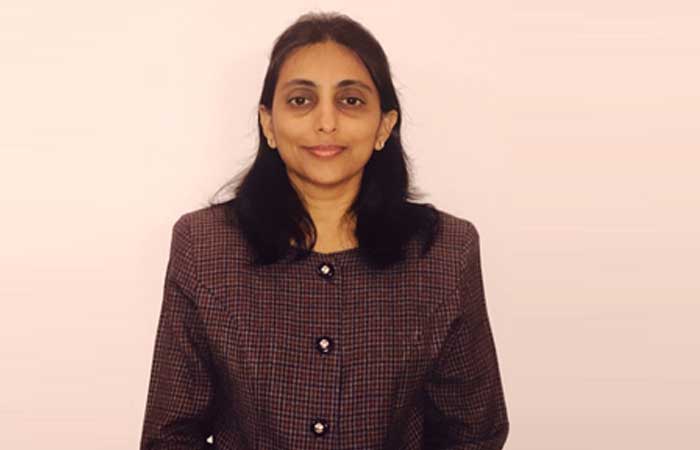
Developing international quality weaving machines can boost domestic weaving
Prashant Gamatex is a leading supplier of high speed sectional warping machine, warping creel, single end sizing machine initiated under technical collaboration with Gamatex, Italy. Amoli Shah, Director, Prashant Group of Companies, in this conversation with Divya Shetty
How would you assess the current state of the Indian weaving industry in terms of its growth, innovation, and global competitiveness?
Indian weaving industry is currently showing quite sustained activities. Especially in filament application, we foresee very good growth in coming years as many players are diverting their product lines from spun to filament looking at the price advantages as well as the new technologies improving feel and handle of filament fabrics.
Initiatives like establishing Textile parks, PLI scheme etc. at central level and development of clusters in remote / backward area with respective state government schemes / policies providing subsidies will definitely boost textiles activities across India and of course, weaving industry will get benefitted out of it. Moreover, looking at the current scenario of Bangladesh, we anticipate some of our Industry players will shift their base in India for making weaving and garmenting units in India.
As a growth aspect for any industry, Innovations and development is a continuous process. In weaving industry, we have seen various weaving machines offering new features optimising the machine speed, performance of shedding motion controls and thereby productivity with Industry 4.0, data matrix etc. facilitating the industry. As a weaving preparatory machinery manufacturer, we have focussed on innovation and R&D as a part of our vision and journey so far. With innovative launch of Lasertronic Sectional warper way back in 2008 and then after Asia’s first Robotic Sectional warping mc MB3 in 2011-12 followed by an advanced model PB 9 , high end Techtronic Sectional warping mc up to 60 KN beaming tension in 2014-15 and onward launch of Indigo Slasher range with Nitrogen Technology way back in 2017 offering substantial savings in water and dyes and chemicals, patented EMT tensioner for Denim and filament application and then after during COVID, successfully introduction of filament Sizing mc and Assembly line respectively for Polyester and Viscose and Direct warper and Sizing for Jute.
Such developments help us to maintain our leadership in preparatory sector not only in the Domestic market but also among our overseas customers who have entrusted us with repeat orders. Our well-equipped manufacturing facility together with design studio and an experienced team is geared up to meet upcoming challenges.
Can you highlight any recent innovations introduced by Prashant Group that are shaping the future of the weaving industry?
During the recent past, we have introduced series of tensioners ranging from 20 cN to 500 cN (with precision tension controls) for different applications launched in the Industry. Our TT tensioners capable to offer 500 cN tensions to take care of processing up to 20000 Denier warp. Magnetic tensioner series MHTD can offer yarn tension up to 250 cN to meet demand of heavy article for Technical textiles. Similarly, MLTD series tensioner can offer tension up to 20 cN with control within 2 cN, for fibre glass application. Such developments help us to meet growth and challenges in Technical textiles sector. Unrolling creel for Polybeamer can provide smooth movement of polypropylene tapes with minimum friction to facilitate beaming with lowest possible tension. Direct warpers with V creel and Sizing for spun yarn application are also enhanced with features for meeting highest requirement for high speed airjet weaving machines. Latest introduction of Fibre glass Sizing mc as an extension to well proven direct warper and Assembly line will make a turnaround in global weaving industry.
In your opinion, what strategic steps should India take to establish itself as a global leader in the weaving sector?
Taking into consideration the global textile market and positioning of India, if Indian textile industry focuses more on R&D for developing new technology that can improve productivity and cater wider application of fabric base in cost effective manner. As a player in weaving preparation mcs, Prashant Group has successfully catered the needs of the Indian Weaving Industry. However, we are still lagging in weaving MCs and have to rely upon European or Japanese weaving machines. Developing international quality of airjet and rapier weaving machines can boost domestic weaving sector a lot.
What are the key challenges currently confronting the Indian weaving industry, and how can they is effectively addressed?
Indian Weaving Industry is facing major challenge with respect to availability of skilled workforce, and experienced technical personnel. Moreover, dependence on manpower from the other states is also a factor.
For filament weaving industry, we have to rely upon imported yarn especially for yarns meant for Technical textiles etc.
Development of skilled manpower with integrity is also quite necessary to achieve such objectives. Industry, together with government institutions can take a lead for same. Government should also focus on producing yarn like Kevlar or Fibreglass etc within India.
Could you elaborate on Prashant Group’s short-term and long-term goals, and how these align with the evolving demands of the weaving market?
Prashant Group has always considered offering highest technology in a cost effective manner.
We have different solutions to cater the demand of small and decentralised customer base as well as highly demanding corporate customers and the overseas customers. Satisfying the need of our existing customers is somewhat short term goal whereas taking global weaving Industry as a whole, Prashant rely on long term goals of meeting customer requirement for most challenging requirements such as optimising performance of Robotics Sectional Warping mc or continuously updating our Spun and Filament preparation MCs including fibreglass sizing and Techtronic Sectional Warping mc.
How does Prashant Group integrate sustainability into its operations, and what role do sustainable practices play in the future of the weaving industry?
We believe in सर्वे जना : सुखीनो भवन्तु : I To encourage ecology and sustainability. Apart from having installed a solar plant of 500 kw in our current setup, our group company PPI, during year 2023, has moved into a new administrative premises as well as workshop, which are complete green building. All our upcoming expansion / new building will be a green one only. Existing shop floors are also equipped with prefabricated structure with sizable insulation and jumbo cealing fans saving a considerable energy as compared with the conventional pedestal fan.
As a part of our efforts to provide sustainable solutions to the industry, Prashant Group provides a unique solution for the Denim Industry which requires a huge quantum of water on 24*7*365 basis. PWP Slasher Indigo dyeing range, equipped with an advanced Nitro technology can offer tremendous saving up to 50 per cent in water, 15-20% in dyes and chemicals and significant saving in space requirement as compared with the conventional Slasher dyeing technology. It offers sizable reduction in ETP requirement as well. Our overseas customers of PWP Nitro dyeing range are highly satisfied with its performance.
Moreover, our high end machines are equipped with Servo motors. Apart from better accuracy and higher torque, it also offers energy saving as against the usual Induction motor apart from better accuracy and higher torque.
What role do advanced technologies such as automation and AI play in transforming the weaving landscape, and how is Prashant Group leveraging these advancements?
Automation with Industry 4.0 is the need of the hour. It helps the industry to integrate the features like production, quality, cost just-in-time production and digital integrated production etc. for various applications. It offers advantages like streamed line production efficiency, customisation, sustainable work practice and waste reduction, textiles recycling planning, design and innovation, fabric defect identification and analysis CAD software process, colour matching, fabric inspection and supply chain management and customer behaviour and market trend etc.
Prashant Group has equipped our products with AI tools for guiding the end user about production schedules, monitoring the health of the equipment and reduction in downtime with preventive maintenance. Thereby, one can achieve increased productivity and reduction in operational costs.