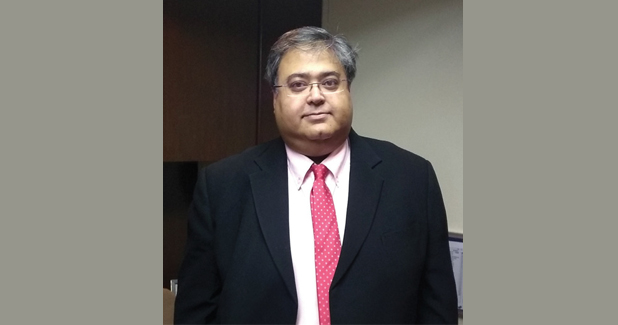
Constant R&D is our forte: Diven Dembla of Precitex
Precision Rubber Industries, owners of the renowned Precitex, a name synonymous with high-quality brands of aprons and cots, was the first Indian company to participate in ITMA that was held in the year 1975.
Precision Rubber Industries, owners of the renowned Precitex, a name synonymous with high-quality brands of aprons and cots, was the first Indian company to participate in ITMA that was held in the year 1975. Since then, they have never missed a single edition of the flagship event for the textile machinery industry. This year too, the company will be participating at ITMA and will be launching new range of cots and aprons to the global market. Says the Managing Director of the company, Diven Dembla, “ITMA is the exhibition we look forward too wherein we can showcase our new products. We do a lot of R&D to develop new products. We will be launching four new products for the market.â€
“Precitex is a market leader in India and are exporting to more than 40 countries. We have a good market share for cots and aprons. Last year, as per exports, we had a fairly good year. We did a growth of nearly 18 per cent. Our exports are increasing all the time,†he added.
The new products that will be launched at ITMA include: “SP†Series apron: This apron is manufactured using specialised polymer. The key features are:
- This will be available for top apron, bottom apron and perforated apron applications.
- This will offer low-efficient of friction to have free movement of apron over the knurled roller and also free and uniform feed of fibres to front roller nip
- Due to light design, the torque required to drive the knurled roller is reduced to a great extent giving big advantage to long frame.
- Substantial improvement in life due to improvement in wear and tear resistance.
“CC 63†cot: This cot is designed to have better fibre handling properties and higher wear and tear resistance, which leads to enhanced grinding cycle.
“XP G 83†cot: This cot is designed for high speed draw frame having speeds above 500 m/min. The key features are:
- The bonding strength is improved to 25 per cent to 30 per cent and after ageing strength is improved by 20 per cent to 30 per cent
- This cot will offer higher grinding cycle and lapping tendency will be minimum.
“CD 6080†cot: This cot is for comber detaching roller application. It is a two core construction having soft inner layer and taper at bot the ends to avoid damage during working. This cot will offer higher grinding cycle up to six months and will offer completely trouble-free operation.
The company’s products are used by all quality conscious spinners across the globe. Some of the major export destinations are Indonesia, Bangladesh, Pakistan, Vietnam, Turkey, Middle East countries, Latin American countries and countries in Africa.
On plans for ITMA, Dembla said, “For us, it will be more of a networking ground. Ours is a consumable product, it’s not like machinery wherein we have to find a new buyer. We plan to tap a lot of export customers. We would also look to get in some agents for the respected countries. There are some countries where there is good growth happening like Vietnam. We are looking to add more agents. In India, we have around 25 distributors. The advantage of adding local agents is that they know the language and the mindset of the people.â€
Precitex has recently expanded their capacity to manufacture 80 million pieces of aprons and cots from their two plants situated in Madhya Pradesh and Gujarat States. Manufacturing process in both the plants are having ISO 9001:2005 accreditation. In fact, Precitex has been winning award for best export performance from various bodies like ITAMMA, AIRIA, CAPEXIL, to name a few.
On R&D, Dembla had this to say: “We have a R&D centre at Thane, outskirts of Mumbai. There we have a full-fledged rubber testing technology, wherein we do testing of all types of synthetic rubbers and chemicals. We always try to innovate with our new products. Today, spinning industry is changing and the speeds are getting faster, and because of this, the wear and tear is faster.
In compact spinning, the travel is much less so the wear-out is faster. Customers expectations are increasing. We even do trials at large-scale level. Right now, we are launching a new product after at least three to four years of trial. A lot of R&D goes into making these products.â€
“The basic raw materials in our products are synthetic nitrate rubbers. There are many types of synthetic rubbers. This petroleum-based product is made by polymerisation process. Unlike natural rubbers, these synthetic rubbers have many applications. We are importing this product from France, and we have another supplier in Germany.
A lot of other raw materials are also imported. Some are sourced from multinational companies, who have a base in India. You can say that about 70-80 per cent of the raw materials are imported. We have a long and tedious manufacturing process. For a small piece of apron, there is at least 20 different processes.â€
On distributorship and sales network, Dembla says, “We have around 25 distributors in India alone. Out of that, 12 are in South India, because around 45 per cent of spinning installations happen in South India. Our distributors even look after the technical aspect and aftersales. Their job includes conducting trials or recommending the right product for the right application. We have different products for different applications. The sales persons job is to educate the customers and give them some suggestions and conduct trials. As you now, the lifecycle of our machine is only two years, so we have to go every two months to monitor the performance.â€
He adds further, “If the customer complaints, we help the end users by giving them the technical knowledge. We conduct buffing audits, and training programmes on proper installations. A customer, nowadays, wants from more value additions.â€