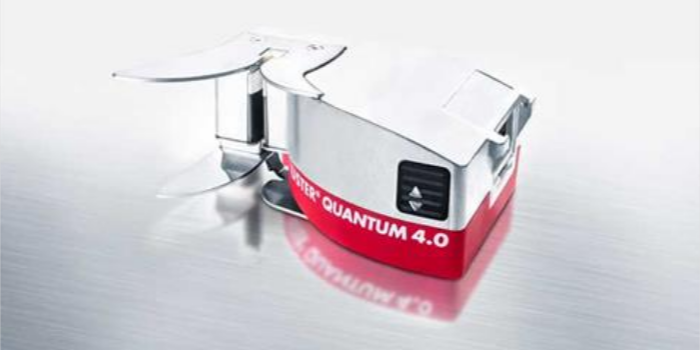
Clear choice: Security, prevention and flexibility
New Uster Quantum 4.0 yarn clearer offers spinners the best of both worlds
Which
yarn clearing technology should spinners choose? Now there’s only one answer,
as Uster launches the new Quantum 4.0 clearer generation. This world-beating
innovation combines both capacitive and optical sensors in one – delivering
comprehensive security, prevention and flexibility.
The
Smart Duo system offers the best of both worlds for intelligent yarn quality
control and optimized profitability. It means mills can now focus on meeting
the fast-moving market challenges, instead of pondering technical options.
Security and reliability: the basis
of yarn quality
Quantum
4.0 is like a dream come true for the industry. For years, spinners have wished
for a way to bring the best of different technologies together, for secure
quality and maximum flexibility.
Spinners
can now access full security in quality control, ensuring the best clearing
mode is applied. The Quantum 4.0 enables this through a simple
Capacitive/Optical switch. This allows greater flexibility in the types of yarn
which can be produced, while also dealing with factors such as humidity
variations.
Intelligent sensors in tandem
The
capacitive and optical sensors work intelligently in tandem through an
innovation known as Cross Clearing. This locates and eliminates hidden defects
by means of a double check, in which the main sensor’s signal is supported by
the assistance sensor. This deals with issues such as unnoticed fluff events,
which might otherwise cause breaks downstream.
Today’s
market trends show strong demand for compact yarns. Here, spinners can trust
Quantum 4.0 to tap this potential and deal with any quality issues. The density
feature, for example, protects mills from substandard cops caused by ring
spinning malfunctions such as blocked compacting zones, or twist problems. The
Smart Duo has the advantage of monitoring yarn density continuously and after
every splice. “No matter where density variations originate, be it compacting,
different twist levels due to slip spindles or otherwise, Uster Quantum 4.0
takes care of it – and this is a real technical innovation,†said Katrin Hofer,
Product Manager at Uster Technologies.
No more material mix-ups
A
further valuable innovation with Quantum 4.0 is the Blend Mix-up option, which
now enables mills to identify mix-ups of different types of raw materials. This
long-awaited market request detects any wrong raw material in greige and white
yarns, combating the infamous, but serious, barré effect in fabrics. Cop
mix-ups can happen in mills, since differences are hardly visible to the human
eye. But Quantum 4.0 stops the problem before it becomes an issue, thanks to
significantly improved hardware and software – all underpinned by the Smart
Duo.
The
higher processing power of the new sensors brings additional benefits such as
the enhanced Continuous Core Yarn option, which detects both missing and
off-center core continuously.
Innovations
in Quantum 4.0 also focus on contamination, with deeper analysis of
polypropylene and foreign matter. A new PP classification gives users the
overview of polypropylene content, while the Advanced FD classification now
shows extra classes below the 5 per cent lines. Both these features add to the
value of the contamination function, together with Total Contamination Control
(TCC).
Quantum
4.0 gives spinners the ultimate confidence through the intelligent interaction
of capacitive and optical sensor technology. It achieves ‘one of a kind’
security levels in basic clearing, while also cutting only what’s necessary.
Prevention pays off
As
well as identifying defects at winding, preventing defects at source is also in
focus with the clearer’s new Expert System. The new Quantum Expert is now
included in the product offering. Thanks to many added intelligent analytical
features, the Uster Quantum Expert enhances process control and prevention of
defects, through Total Contamination Control, Ring Spinning Optimization and
the RSO 3D Value Module.
Latest
innovations in the new clearer protect spinners from claims and waste – but
enabling business success is the real purpose of Quantum 4.0. Latest clearing
technologies work with Uster’s unique data analysis to enable flexible
data-based decisions using Application Intelligence. “Failure prevention is the
key to success and tackling issues at source is the way to do it. Uster Quantum
4.0 plays an important role in this, offering options to strengthen it,†said
Hofer.
Secure and user-friendly
The
secret of true innovation is how well it is designed through to the point of
user interaction. No matter how much data – in terms of quantity and different
parameters – is collected for analysis, Uster Quantum Expert manages the
complexity, while staying as intuitive as ever.
With
Quantum 4.0, a new central Smart-Limit button enhances flexibility, since
operators can adjust all available smart limits with a single tap, based on the
unique Yarn Body concept. Each individual limit can be simply fine-tuned as
preferred.
Users
enjoy the established Quantum workflows and embrace the new customer-centered
user interface with a 16:9 touchscreen on the 7th generation control units`.
Nothing
gets in the way of success with this prevention strategy. Uster recognises that
today’s challenges are tough, can be overcome with prevention, security and
flexibility on your side – and Quantum 4.0 on your winding machine.