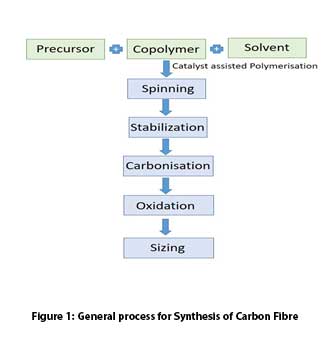
Carbon fibre: Boon or bane
While consumption of carbon fibre is expected to grow rapidly (because of its super capabilities), it is going to pose an environmental threat owing to its non-biodegradability, according to Dr Ashok Athalye and Subhashree Pradhan.
Carbon is a widely distributed natural chemical element and a basic component of natural as well as man-made fibres. However, a textile fibre that is made of only carbon is a novelty and owing to its unique characteristic features and benefits it is considered a new landmark in the textile industrial revolution.
This ultra-modern fibre is composed of carbon atoms as building blocks which are suitably interconnected to form a long chain of typically 5-10 μm in diameter. It is extremely lightweight and has exceptional stiffness, tensile strength, thermal stability, and chemical resistance.
Carbon fibres (CF) are classified based on their precursor material. The initial attempts were made using cellulosic fibre as a starting point, but the resultant fibre did not meet the expected outcome as it contained only about 20 % carbon. Then, polyacrylonitrile (PAN) was used as a precursor which improved the carbon content to as high as 99%. Almost 90% of CF is manufactured from PAN, while the rest is based on the derivatives of various phenolic resins, rayon, hydrocarbon pitch, polyamides, polyesters, Poly(1,1-dichloroethene), etc. It is synthesized either from a single or a blend of organic polymers of varying concentrations along with organic liquids to achieve a specific effect.
In the first step, the precursor is polymerised with other copolymers in a suitable solvent medium in presence of a catalyst. Then the filament is spun and stretched up to the required radii so that molecules are aligned within the fibre. The stretched fibre is cured at 190-2800C in the presence of atmospheric oxygen for 2 hours. During the thermal exposure, rearrangement of atoms within the molecule occurs in a simultaneous multistep process. The rearrangement of atoms leads to the strong bond formation and subsequent stabilisation of the fibre. Some practices include the use of heated gas to expedite stabilisation. In this stage of thermal treatment, a suitable stabilisation method is adopted in order to avoid undesirable self-fusing of precursor.
In the next step, stabilized fibre is exposed to a thermal temperature range of 999-12500C in an isolated system away from air containing oxygen. Fibre tends to lose elements other than carbon atoms like hydrogen, nitrogen etc as oxides at this higher temperature. Carbon atoms in the molecule form a strong bond with each other. At the final stage, CF is allowed to undergo selective oxidation at some specific points to chemically bind with other compounds like epoxies. This method is frequently designated as “graphitising” in which mechanical properties of CF are improved.
Figure 1: General process for Synthesis of Carbon Fibre
To understand the mechanistic approach of carbon fibre, let us assume the most common precursor PAN. PAN consist of a basic long (-CH2-CH-) n chain having cyanide (-CN) as a functional group. The high polarity of cyanide in the PAN induces strong intermolecular forces. There is a change in the molecular structure upon oxidation at higher thermal temperatures. During the process of oxidation, oxygen is introduced along with cyclisation of the polar nitrile group in which polymer reshapes into a single-layered hexagonal like ladder structure. During this process, unwanted molecules like oxides of Hydrogen, Carbon, cyanides etc get formed which need to be effectively removed by chemical and thermal treatment.
The structure of any CF depends on many factors and can be synthesized by having a particular arrangement or directional orientation.
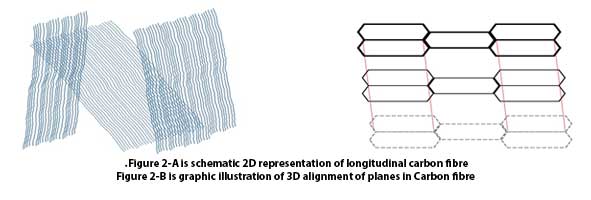
The extremely high strength to weight ratio, electrical conductance, corrosion resistance, rigidity, chemical inertness, and high thermal stability are the unique characteristics of this novel fibre. Therefore, it finds wide applications in various speciality technical textile sectors like ballistic protective vests, automobiles, sports accessories, aerospace, nuclear science, etc. Thus, considering the novelty, uniqueness and exceptional properties, the production and consumption of CF are exponentially growing globally.
However, owing to its extremely high thermal, photolytic and biological stability, it is virtually a non-biodegradable forever chemical component and thus poses threat to the environment. It cannot be reused or recycled, so once made we are stuck with it, and we cannot leave it but must live with it.
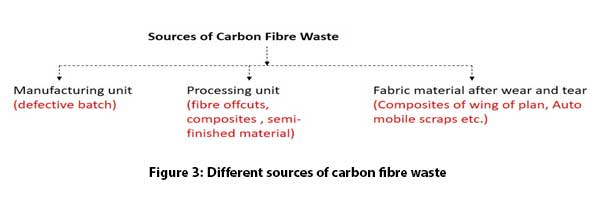
As the dependency on CF is growing globally, it raises concern about increased waste generation post its service life. CF waste is generated from the point of production to the end-use application. The manufacturing process is energy extensive and emits hazardous gases like cyanide, oxides of carbon, oxides of Nitrogen etc.
During the process of manufacturing, a small alteration like temperature or power failure leads to the scrapping of the whole batch. Moreover, a lot of CF offcuts, composites, and semi-finished material are left as waste at the processing units. Finally, these end up as waste which has very limited scope in terms of reusability.
Landfilling is the simplest method in terms of economy but has the cost of environmental pollution. Also, incineration though extremely difficult due to the high thermal stability of CF will lead to the release of toxic fumes which can cause serious air pollution. Thus, suitable reuse for different applications is the widely accepted sustainable alternative to reduce the menace of CF on the environment.
Another way is the use of a specialised recycling method in which CF is recovered from the polymer matrix to manufacture useful products. Thermoplastic based CF composite can be purified by thermal melting and can be used with virgin nano CF for making new products. In contrast, the recycling of thermoset CF composite is complex and costly due to the heterogeneous nature of the fabric.
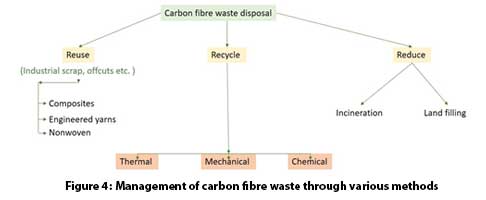
CF is a versatile material and has numerous applications and its consumption is expected to grow rapidly because of its super capabilities. However, such fast growth and high usage are going to pose an environmental threat owing to its non-biodegradability. Thus, managing CF waste is going to be a major challenge. Future research and innovation are expected to be in finding out feasible and effective disposal of such technical textile components.
References:
- Esfandiar P, Sima K, Russell V and Xungai W, (2020) Recent progress in recycling carbon fibre reinforced composites and dry carbon fibre waste
- Verma S, Bhuvaneshwari B, Gupta R (2018), Recycling, Reclamation and Re-manufacturing of Carbon Fibres
- Robert A, Witik A, Remy T, (2013) Carbon fibre reinforced composite waste: An environmental assessment of recycling, energy recovery and landfilling
About the authors
Dr Ashok Athalye is the Professor of Textile Chemistry and Vice President of Technological Association at Institute of Chemical Technology (ICT), Mumbai
Subhashree Pradhan is pursuing MTech in Fibres and Textile Processing Technology at ICT, Mumbai